Добавлен: 08.11.2023
Просмотров: 274
Скачиваний: 4
ВНИМАНИЕ! Если данный файл нарушает Ваши авторские права, то обязательно сообщите нам.
Основной причиной неравномерности износа контура зацепления является провисание автосцепок. При провисании резко уменьшается площадь поверхности контакта сцепленных автосцепок, что ведет к увеличению интенсивности местного износа. Кроме износа, провисание автосцепок увеличивает эксцентриситет сил, действующих на автосцепку, что вызывает местные перенапряжения и появления трещин на ударной стенке зева корпуса 7 и 8, а также в зоне перехода от головы к хвостовику 3.
Износ поверхности упора 9 возникает от взаимодействия с выступающей частью розетки. В нормальных условиях эксплуатации сжимающие усилия, возникающие в поезде или при сцеплении вагонов, должны восприниматься и гаситься в поглощающем аппарате. Однако в связи с ростом весовых норм поездов и недостаточной энергоемкостью поглощающих аппаратов в определенных ситуациях после полного закрытия поглощающего аппарата часть передаваемой кинетической энергии остается непогашенной аппаратом, и она передается непосредственно от упора головы автосцепки на выступ розетки и на раму вагона. Такая передача сил отрицательно влияет на техническое состояние рам вагонов и приводит к смятию и износу упора головы корпуса автосцепки.
Износы 4 поверхностей корпуса автосцепки в зоне перехода от головы к хвостовику образуются от взаимодействия с поверхностями окон в розетке и вертикальном листе концевой балки рамы. Это взаимодействие происходит в случае отклонения оси корпуса автосцепки в вертикальной или горизонтальной плоскости. При проходе вагонов в кривых малого радиуса и особенно при сцеплении вагонов с разной длиной консольной части рамы оси автосцепок отклоняются и на первом этапе подвергаются износу вертикальной стенки хвостовика корпуса автосцепки.
При достижении определенной величины износа прочность стенок становится недостаточной и возможны появление изгиба хвостовика в горизонтальной плоскости и образование трещин 3 .Аналогично происходит процесс изгиба хвостовика в вертикальной плоскости, когда поезд проходит различные переломы профиля пути. Особенно это относится к проходу вагонами горбов сортировочных горок.
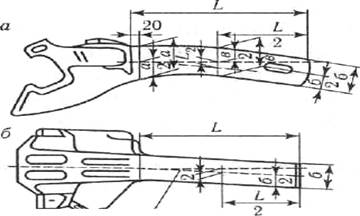
Рис.2.Деформации корпуса автосцепки.
В некатаных случаях, когда имеет место большая разница высот осей двух соседних автосцепок или когда сцеплены два вагона консольной части рамы, при проходе горба сортировочной горки возникает заклинивание автосцепок в контуре зацепления. В результате этого хвостовик автосцепки одного из вагонов упирается через тяговый хомут в верхнее перекрытие хребтовой балки и начинает поднимать вагон. Это также может привести
к изгибу хвостовика или изломам маятниковых подвесок смежной автосцепки.
Износы 4 восстанавливаются наплавкой при глубине износов от 3 до 8 мм, а при износах более 8 мм корпус бракуется, так как надежность восстановления таких тонких стенок становится недостаточной.
Трещины 3 разрешается устранять, если суммарная длина их до 100 мм у корпусов, проработавших более 20 лет, и не свыше 150 мм для остальных корпусов. По разрешению МГТС максимально допустимая длина завариваемых трещин 3 может быть увеличена до 40 % периметра сечения, причем разрешается заваривать и сквозные трещины. Заварка трещин должна выполняться только с полным проваром.
Износы стенок отверстия для клина 5 по ширине и длине образуются за счет износа и смятия стенок от взаимодействия с клином тягового хомута.
Износ упорной поверхности хвостовика автосцепки 6 происходит от взаимодействия с упорной плитой.
Боковые стенки отверстия для клина наплавляются при износе на глубину более 3 мм, но не более 8 мм.
Наплавка износов отверстия для клина в продольном направлении и износа упорной поверхности хвостовика 6 производится при толщине перемычки, измеренной в средней части не менее 40 мм для автосцепки СА-3 и не менее 44 мм для автосцепки СА-ЗМ.
Кроме перечисленных износов и повреждений, как уже сказано выше, корпус автосцепки получает различные деформации хвостовика, представлены на рис.2 и уширение зева корпуса (расстояние от большого до малого зубьев). Уширение зева определяется шаблонами.
2.5 Технологических процесс ремонта автосцепного устройства..
1) Осмотр автосцепного оборудования. (Производит освобожденный бригадир отделения по ремонту автосцепки);
2) снятие автосцепки с вагона и передача на участок по ремонту автосцепки (КПА) для ремонта (производит работник производственного участка по ремонту тележек);
3) очистка корпуса автосцепки (производит слесарь участка по ремонту автосцепки);
4) контрольный осмотр автосцепки и определение объема ремонта (производит освобожденный бригадир участка по ремонту автосцепки);
5) разборка автосцепки, очистка деталей автосцепки (производит слесарь); осмотр и проверка деталей автосцепного устройства шаблонами, дефектация деталей (производит освобожденный бригадир участка по ремонту автосцепки);
6) неразрушающий контроль головной части корпуса автосцепки, хвостовика автосцепки, тягового хомута, поглощающего аппарата;
7) сварочно-наплавочные работы по ремонту корпуса и деталей автосцепки (производит электрогазосварщик участка по ремонту автосцепки);
8) механическая обработка наплавленных поверхностей деталей и корпуса автосцепки до чертежных размеров (производит слесарь участка по ремонту автосцепки);
9) проверка деталей после ремонта, нанесение клейм и окраска в соответствии с инструкцией [14] (производит слесарь отделения по ремонту автосцепки);
10) сборка автосцепки (производит слесарь отделения по ремонту автосцепки);
11) проверка собранной автосцепки, нанесение клейма (производит освобожденный бригадир).
12) покраска в соответствии с инструкцией [14] (производит слесарь);
13) передача отремонтированной автосцепки работникам производственного участка по ремонту тележек для установки её на вагон (слесарь отделения по ремонту автосцепки).
Автосцепки, снятые в вагонов, устанавливают в подвижную кассету конвейера и закрепляют на ней. Под действием привода автосцепка перемещается на позицию очистки. Очищенная автосцепка подается на позицию разборки, на кантователь, где производится разборка автосцепки, ее осмотр, определение объема ремонта деталей. Контроль геометрических параметров корпуса и деталей механизма зацепления автосцепки производится на автоматизированном комплексе для контроля геометрических параметров автосцепки КИТ. В случае неисправности комплекса контроль производится при помощи шаблонов. Если при проверке корпуса автосцепки будет обнаружена какая-либо неисправность, его устанавливают в подвижную кассету и передают на позицию сварочно-наплавочных работ. Обработка наплавленных поверхностей производится на фрезерных станках. После обработки корпус устанавливается в кассету конвейера, комплектуется исправными деталями механизма сцепления, и собранная автосцепка проверяется.
Поглощающие аппараты в комплекте с тяговым хомутом и упорной плитой подаются в контрольный пункт и устанавливаются на стенд, на котором производится разборка, проверка и сборка.
При плановых видах ремонта производится полный осмотр автосцепного устройства.
При полном осмотре съемные узлы и детали автосцепного устройства снимают с подвижного состава не зависимо от состояния и направляют в отделение по ремонту автосцепки, для проверки и ремонта в соответствии с требованиями, изложенными в инструкции [14] и настоящим технологическим процессом.
К несъемным деталям автосцепного устройства относятся: ударная розетка, передние и задние упоры, располагающиеся на хребтовой балке, детали расцепного привода (фиксирующий кронштейн, кронштейн и расцепной рычаг). Проверку несъемных деталей производит освобожденный бригадир отделения по ремонту автосцепки на подвижном составе.
Детали, требующие ремонта, демонтируются работниками производственного участка по ремонту тележек и передаются в КПА. После ремонта детали устанавливаются работниками производственного участка по ремонту тележек на вагон.
Детали автосцепного устройства, снятые с подвижного состава и подлежащие проверке и ремонту, тщательно очищаются от грязи на участке наружной очистки и осматриваются. Участок наружной очистки оборудован следующим оборудованием:
1) Струйно-абразивная камера типа АК-214;
2) Кран-балка (грузоподъемностью 0,5 т);
3) Лупа трехкратного увеличения согласно ГОСТа 25706-83;
4) Переносной фонарь для осмотра кармана автосцепки на предмет видимых трещин.
После очистки автосцепка устанавливается при помощи кран-балки в кантователь для осмотра и разборки автосцепок.
После очистки корпус автосцепки, тяговый хомут, клин тягового хомута, маятниковые подвески центрирующего прибора должны быть подвергнуты неразрушающему контролю. Неразрушающий контроль автосцепки, тягового хомута, клина тягового хомута, маятниковых подвесок и стяжного болта производится на участке по ремонту автосцепки.
Неразрушающий контроль производится в соответствии с комплектом технологической документации на производство неразрушающего контроля.
Неразрушающий контроль производится дефектоскопистом на позиции дефектоскопирования производственного участка по ремонту автосцепного устройства.
Стяжной болт поглощающего аппарата, подвергают неразрушающему контролю только после ремонта сваркой.
На детали, прошедшие дефектоскопирование и проверку шаблонами при их исправности наносят клеймо. Проверку шаблонами и нанесение клейм производит бригадир.
Наплавка и упрочнение автосцепного устройства осуществляется согласно инструкции ЦЛ-201-03 и комплекта технологической документации на производство сварки и наплавки.
Температуры прокалки электродов:
- УОНИ-13/55 К температура прокалки 170-200°С, 60 мин.;
- УОНИ-13/45 температура прокалки 350-400°С, 60-120 мин.;
- УОНИ-13/55 температура прокалки 250-300°С, 60 мин. - 120 мин.;
- УОНИ-13/45АА температура прокалки 380-420°С, 180 мин.;
- АНО-4 температура прокалки 180-200°С, 60 мин.;
Прокаленные электроды необходимо хранить при температуре 80°С.
В целях увеличения межремонтного пробега пассажирских вагонов и сокращения материальных затрат на их ремонт, повышения безопасности движения пассажирских вагонов детали автосцепного оборудования должны упрочняться и восстанавливаться. Упрочнение деталей автосцепного устройства (корпуса автосцепки, замка автосцепки, центрирующей балочки, маятниковой подвески и тягового хомута) производится способом плазменно-порошковой наплавки согласно комплекта технологической документации на производство сварки и наплавки.
Для контроля за обеспечением установленной твердости наплавленных материалов ударно-тяговых поверхностей корпуса автосцепки и замыкающей поверхности замка производить периодические проверки твердости наплавленного металла.
После ремонта производится контрольная проверка шаблонами.
2.6