Добавлен: 08.11.2023
Просмотров: 271
Скачиваний: 4
ВНИМАНИЕ! Если данный файл нарушает Ваши авторские права, то обязательно сообщите нам.
, неисправные разбирают на прессе для разборки и сборки. Затем на стенде производят дефектоскопирование тягового хомута, определение объема его ремонта и, в зависимости от его технического состояния, направляют на участок сварочных работ. После ремонта сваркой тяговый хомут направляют на участок механической обработки.
Упорные плиты, клинья, маятниковые подвески проверяют на верстаке, магнитный контроль производят на стенде. После ремонта и обмера шаблонами
Подготовленные для упрочнения ИМС автосцепку, замок, замкодержатель подают на участок упрочнения ИМС. Упрочненные детали обрабатывают бормашинами. На упрочненные детали ставят клеймо «У»
ЛКЫН ЛАТТЕ
ЫСЫМЫН АШ
2.2 Планировка контрольного пункта автосцепки
ОТКРОЙ СЕЗОН
ОДНОГО ЛАТТЕ!
На ремонтных позициях контрольного пункта автосцепки расположено следующее оборудование [3]:
1. Участок дефектоскопирования, разборки и сборки автосцепки
1) помост для осмотра автосцепки
2) дефектоскоп МД-12ПС,
3) кантователь для обмера корпусов автосцепки,
4. стенд для обмера и ремонта деталей автосцепки,
5. кассета для сборки автосцепки,
6. кассета для складирования замков,
7. заточной станок;
ІІ. Участок сварочно-наплавочных работ
JACOBS
1. сварочный стол,
JACOBS
2. кантователь для наплавки автосцепки,
3. кантователь для наплавки тяговых хомутов,
4. сварочный выпрямитель,
5. сварочный полуавтомат,
11I. Участок механической обработки
1. фрезерный станок УФ5570М,
2. строгальный станок,
3. фрезерный станок 6Н-13П,
Участок ремонта поглощающих аппаратов
1. пресс для разборки и сборки поглощающих аппаратов,
2. дефектоскоп МД-12ПС,
3. верстак для ремонта деталей,
4. площадка для складирования поглощающих аппаратов;
V. Участок упрочнения индукционно-металлургическим способом
1. высокочастотный генератор,
2. кантователь,
3. бак с водой,
4. шкаф для хранения документации.
2.3 Расчет штата контрольного пункта автосцепки
1.2 Конструкция И основные ТИПЫ автосцепного устройства
Назначение и типы автосцепного устройства. Автосцепное устройство относится к ударно-тяговому оборудованию вагона и предназначено для сцепления вагонов между собой и локомотивом, удержания их на определенном расстоянии друг от друга, восприятия, передачи и смягчения воздействия растягивающих и сжимающих усилий, возникающих во время движения.
От исправного состояния этого оборудования во многом зависит безопасность движения поездов.
Это оборудование относится к объединенным устройствам, где совмещаются все функции ударных и тягово-сцепных приборов. До перевода подвижного состава железных дорог бывшего СССР на автосцепку он оборудовался раздельными приборами, когда в качестве ударных приборов устанавливали буферные комплекты, а сцепных — винтовую упряжь.
На каждом вагоне современной конструкции установлено два комплекта автосцепного устройства, размещенных по концам вагонной рамы.
Перевод подвижного состава на автосцепку позволил:
- рационально использовать силу тяги локомотивов,
- увеличить массу поезда и тем самым повысить провозную и пропускную способность железных дорог, устранить тяжелый и опасный труд сцепщика,
- ускорить процесс формирования поездов и оборот вагона,
- уменьшить тару вагонов за счет снятия буферных комплектов, облегчения боковых и концевых балок.
Автоматические сцепки делятся на три типа:
- нежесткие,
- жесткие,
- полужесткие.
Нежесткие автосцепки допускают относительное перемещение сцепленных корпусов в вертикальном направлении.
В случае разницы по высоте продольных осей нежесткие автосцепки располагаются ступенчато, сохраняя горизонтальное положение. Перемещение в горизонтальной плоскости в них обеспечивается сравнительно простыми по конструкции шарнирами на концах корпуса автосцепок.
Жесткие автосцепки исключают относительное перемещение сцепленных корпусов в вертикальной плоскости. Если до сцепления вагонов имелась разность высот продольных осей, то после сцепления они совместятся и займут наклонное положение, располагаясь по одной прямой.
На концах корпуса таких автосцепок имеются сложные шарниры, обеспечивающие относительные вертикальные и горизонтальные угловые перемещения.
Полужесткие автосцепки взаимодействуют друг с другом в процессе работы как нежесткие, однако вертикальные перемещения их относительно друг друга ограничены предохранительными кронштейнами, расположенными на малых зубьях корпусов.
Полужесткие автосцепки применяются в вагонах, имеющих удлиненную консольную часть рамы (восьмиосные и некоторые специализированные вагоны).
Каждая из этих видов автосцепок обладает своими достоинствами и недостатками и поэтому применяется на таких типах вагонов, где это наиболее целесообразное.
К преимуществам жестких автосцепок относятся: простота автоматического соединения воздушной магистрали и электрических линий; более плавный ход вагона вследствие малых зазоров и меньших ударов между сцепляющимися поверхностями; облегчение работы механизма автосцепок в результате меньших перемещений деталей; уменьшение шума при движении вагонов, что важно для создания комфорта пассажирам.
Достоинствам нежестких автосцепок относятся: обеспечение гарантированного сцепления вагонов со значительной разницей продольных осей по высоте, особенно при сцеплении груженого с порожним вагоном; отсутствие сложных концевых шарниров; меньшая масса автосцепки, простота конструкции.
Нежесткие автосцепки применяются в вагонах наземных железных дорог, а жесткие — в вагонах метрополитена.
В зависимости от типа вагонов автосцепные устройства подразделяются на конструкции, предназначенные для четырех-, шести- и восьмиосных грузовых вагонов, а также пассажирских в а гоно выключая электро- и дизель-поезда.
Четырехосные грузовые и пассажирские вагоны оснащены типовой нежесткой автосцепкой СА-3 (советская автосцепка, третий вариант), которая отличается только шириной окна ударной розетки и конструкцией поглощающих аппаратов.
Шести- и восьмиосные вагоны оборудуются нежесткой или полужесткой автосцепкой типа СА-ЗМ (модернизированной).
1.3 Требования, предьявляемые автосцепным устройствам
Все вагоны, выпускаемые в СССР для железных дорог колеи 1520 мм, оборудованы автосцепными устройствами, которые служат для автоматического сцепления вагонов при формировании поезда, передачи продольных сжимающих и растягивающих усилий в поезде, а также ручного расцепления вагонов при маневрах.
В типовое автосцепное устройство (рис. 44) входят автосцепка 1, поглощающий аппарат 4, тяговый хомут 3, центрирующий прибор 5, упорные угольники 2 и расцепной привод 6.
Общие требования к автосцепным устройствам и их установке на вагонах магистральных железных дорог определены Правилами технической эксплуатации железных дорог СССР (ПТЭ), ГОСТ 3475—62 и Нормами для расчетов на прочность и проектирование механической части новых и модернизированных вагонов железных дорог МПС колеи 1520 мм (несамоходных).
Автосцепное устройство вагона согласно ПТЭ и ГОСТ 3475—62 должно быть расположено так, чтобы его высота h над головкой рельса у всех новых вагонов составляла 1040—1080 мм. Для предварительных расчетов вновь проектируемых вагонов эту высоту принимают равной 1060 мм. Автосцепное устройство вагонов должно обеспечивать беспрепятственное прохождение сцепленными вагонами кривых участков пути. Грузовые и пассажирские вагоны общесетевого назначения должны проходить участки сопряжения прямых и кривых радиусами соответственно 80 и 120 м и S-образные кривые радиусами соответственно 120 и 170 м без переходных кривых и прямых вставок. Наибольшее отклонение продольных осей сцепляемых автосцепок в горизонтальной плоскости, при котором обеспечивается автоматическое сцепление вагонов, составляет 175 мм. Конструкция автосцепки при некотором износе ее узлов и деталей должна обеспечивать автоматическое сцепление при вертикальном смещении продольных осей автосцепок до 150 мм. Для гарантии надежности сцепления вагонов в поезде разница по высоте между продольными осями сцепленных автосцепок согласно ПТЭ ограничена до 100 мм.
Детали автосцепного устройства по прочности должны удовлетворять следующим основным требованиям:
наибольшие напряжения в корпусе автосцепки от сжимающей или растягивающей силы 250 тс при разности уровней осей сцепления 50 мм не должны превышать предела текучести материала QТ;
напряжения в упорных плитах, тяговых хомутах и клиньях или валиках тяговых хомутов при наиболее невыгодном приложении продольной сжимающей или растягивающей силы 250 тс не должны превышать 0,75Qт;
напряжения в передних и задних упорах автосцепного устройства при наиболее невыгодном приложении продольной сжимающей или растягивающей силы 250 тс не должны превышать напряжений, допускаемых для расчетного режима I (см. гл. П). Перемычку, соединяющую угольники упора, рассчитывают на действие перерезывающей силы 100 тс.
Под наиболее невыгодным приложением продольной силы понимают случай ее действия с перекосом, когда разность уровней осей сцепления может достигать 100 мм, а на угольники одного упора передаются усилия разной величины.
К поглощающим аппаратам автосцепного устройства помимо требований по прочности предъявляют специальные требования, определяемые назначением этих устройств. Продольная сила между вагонами, возникающая при трогании с места и осаживании однородного поезда весом до 10 тыс. тс, а также при маневровых соударениях одиночных вагонов со скоростью не менее 7,5 км/ч, не должна превышать 200 тс. Силу закрытия аппарата, на действие которой рассчитывают его прочность, принимают равной 250 тс.
Энергоемкость поглощающих аппаратов определяют из расчета на соударение со скоростью не менее 7,5 км/ч полностью загруженных одиночных вагонов данного типа. При этом продольное усилие между вагонами не должно превышать 200 тс. Ориентировочно энергоемкость поглощающего аппарата Э = mv^2/8, где т — масса вагона брутто; v — скорость соударения. Энергоемкость аппарата пассажирских вагонов должна быть не менее 3 тем, а максимальное продольное усилие при их соударении со скоростью до 7,5 км/ч — не более 150 тс.
Отдача поглощающего аппарата грузовых вагонов рекомендована не более 30%, а пассажирских — не более 50%, усилие предварительной затяжки — соответственно не более 20 и 5 тс. При статическом нагружении конечное усилие сопротивления поглощающего аппарата грузового вагона должно быть не менее 100 тс, а пассажирского — не менее 75 тс. Поглощающий аппарат должен обладать достаточно высокой надежностью, износостойкостью, и не допускать ускорений при соударении вагонов, превышающих уровень, определяемый принятыми нормами.
Сложные условия эксплуатации автосцепного устройства обусловливают высокие требования не только к конструкции его узлов и деталей, но и к материалу и качеству изготовления. Материал и качество изготовления литых деталей автосцепных устройств регламентированы соответствующими техническими условиями и стандартами. Корпус автосцепки
Упорные плиты, клинья, маятниковые подвески проверяют на верстаке, магнитный контроль производят на стенде. После ремонта и обмера шаблонами
Подготовленные для упрочнения ИМС автосцепку, замок, замкодержатель подают на участок упрочнения ИМС. Упрочненные детали обрабатывают бормашинами. На упрочненные детали ставят клеймо «У»
ЛКЫН ЛАТТЕ
ЫСЫМЫН АШ
2.2 Планировка контрольного пункта автосцепки
ОТКРОЙ СЕЗОН
ОДНОГО ЛАТТЕ!
На ремонтных позициях контрольного пункта автосцепки расположено следующее оборудование [3]:
1. Участок дефектоскопирования, разборки и сборки автосцепки
1) помост для осмотра автосцепки
2) дефектоскоп МД-12ПС,
3) кантователь для обмера корпусов автосцепки,
4. стенд для обмера и ремонта деталей автосцепки,
5. кассета для сборки автосцепки,
6. кассета для складирования замков,
7. заточной станок;
ІІ. Участок сварочно-наплавочных работ
JACOBS
1. сварочный стол,
JACOBS
2. кантователь для наплавки автосцепки,
3. кантователь для наплавки тяговых хомутов,
4. сварочный выпрямитель,
5. сварочный полуавтомат,
11I. Участок механической обработки
1. фрезерный станок УФ5570М,
2. строгальный станок,
3. фрезерный станок 6Н-13П,
Участок ремонта поглощающих аппаратов
1. пресс для разборки и сборки поглощающих аппаратов,
2. дефектоскоп МД-12ПС,
3. верстак для ремонта деталей,
4. площадка для складирования поглощающих аппаратов;
V. Участок упрочнения индукционно-металлургическим способом
1. высокочастотный генератор,
2. кантователь,
3. бак с водой,
4. шкаф для хранения документации.
2.3 Расчет штата контрольного пункта автосцепки
1.2 Конструкция И основные ТИПЫ автосцепного устройства
Автосцепное устройство
Назначение и типы автосцепного устройства. Автосцепное устройство относится к ударно-тяговому оборудованию вагона и предназначено для сцепления вагонов между собой и локомотивом, удержания их на определенном расстоянии друг от друга, восприятия, передачи и смягчения воздействия растягивающих и сжимающих усилий, возникающих во время движения.
От исправного состояния этого оборудования во многом зависит безопасность движения поездов.
Это оборудование относится к объединенным устройствам, где совмещаются все функции ударных и тягово-сцепных приборов. До перевода подвижного состава железных дорог бывшего СССР на автосцепку он оборудовался раздельными приборами, когда в качестве ударных приборов устанавливали буферные комплекты, а сцепных — винтовую упряжь.
На каждом вагоне современной конструкции установлено два комплекта автосцепного устройства, размещенных по концам вагонной рамы.
Перевод подвижного состава на автосцепку позволил:
- рационально использовать силу тяги локомотивов,
- увеличить массу поезда и тем самым повысить провозную и пропускную способность железных дорог, устранить тяжелый и опасный труд сцепщика,
- ускорить процесс формирования поездов и оборот вагона,
- уменьшить тару вагонов за счет снятия буферных комплектов, облегчения боковых и концевых балок.
Автоматические сцепки делятся на три типа:
- нежесткие,
- жесткие,
- полужесткие.
Нежесткие автосцепки допускают относительное перемещение сцепленных корпусов в вертикальном направлении.
В случае разницы по высоте продольных осей нежесткие автосцепки располагаются ступенчато, сохраняя горизонтальное положение. Перемещение в горизонтальной плоскости в них обеспечивается сравнительно простыми по конструкции шарнирами на концах корпуса автосцепок.
Жесткие автосцепки исключают относительное перемещение сцепленных корпусов в вертикальной плоскости. Если до сцепления вагонов имелась разность высот продольных осей, то после сцепления они совместятся и займут наклонное положение, располагаясь по одной прямой.
На концах корпуса таких автосцепок имеются сложные шарниры, обеспечивающие относительные вертикальные и горизонтальные угловые перемещения.
Полужесткие автосцепки взаимодействуют друг с другом в процессе работы как нежесткие, однако вертикальные перемещения их относительно друг друга ограничены предохранительными кронштейнами, расположенными на малых зубьях корпусов.
Полужесткие автосцепки применяются в вагонах, имеющих удлиненную консольную часть рамы (восьмиосные и некоторые специализированные вагоны).
Каждая из этих видов автосцепок обладает своими достоинствами и недостатками и поэтому применяется на таких типах вагонов, где это наиболее целесообразное.
К преимуществам жестких автосцепок относятся: простота автоматического соединения воздушной магистрали и электрических линий; более плавный ход вагона вследствие малых зазоров и меньших ударов между сцепляющимися поверхностями; облегчение работы механизма автосцепок в результате меньших перемещений деталей; уменьшение шума при движении вагонов, что важно для создания комфорта пассажирам.
Достоинствам нежестких автосцепок относятся: обеспечение гарантированного сцепления вагонов со значительной разницей продольных осей по высоте, особенно при сцеплении груженого с порожним вагоном; отсутствие сложных концевых шарниров; меньшая масса автосцепки, простота конструкции.
Нежесткие автосцепки применяются в вагонах наземных железных дорог, а жесткие — в вагонах метрополитена.
В зависимости от типа вагонов автосцепные устройства подразделяются на конструкции, предназначенные для четырех-, шести- и восьмиосных грузовых вагонов, а также пассажирских в а гоно выключая электро- и дизель-поезда.
Четырехосные грузовые и пассажирские вагоны оснащены типовой нежесткой автосцепкой СА-3 (советская автосцепка, третий вариант), которая отличается только шириной окна ударной розетки и конструкцией поглощающих аппаратов.
Шести- и восьмиосные вагоны оборудуются нежесткой или полужесткой автосцепкой типа СА-ЗМ (модернизированной).
1.3 Требования, предьявляемые автосцепным устройствам
Все вагоны, выпускаемые в СССР для железных дорог колеи 1520 мм, оборудованы автосцепными устройствами, которые служат для автоматического сцепления вагонов при формировании поезда, передачи продольных сжимающих и растягивающих усилий в поезде, а также ручного расцепления вагонов при маневрах.
В типовое автосцепное устройство (рис. 44) входят автосцепка 1, поглощающий аппарат 4, тяговый хомут 3, центрирующий прибор 5, упорные угольники 2 и расцепной привод 6.
Общие требования к автосцепным устройствам и их установке на вагонах магистральных железных дорог определены Правилами технической эксплуатации железных дорог СССР (ПТЭ), ГОСТ 3475—62 и Нормами для расчетов на прочность и проектирование механической части новых и модернизированных вагонов железных дорог МПС колеи 1520 мм (несамоходных).
Автосцепное устройство вагона согласно ПТЭ и ГОСТ 3475—62 должно быть расположено так, чтобы его высота h над головкой рельса у всех новых вагонов составляла 1040—1080 мм. Для предварительных расчетов вновь проектируемых вагонов эту высоту принимают равной 1060 мм. Автосцепное устройство вагонов должно обеспечивать беспрепятственное прохождение сцепленными вагонами кривых участков пути. Грузовые и пассажирские вагоны общесетевого назначения должны проходить участки сопряжения прямых и кривых радиусами соответственно 80 и 120 м и S-образные кривые радиусами соответственно 120 и 170 м без переходных кривых и прямых вставок. Наибольшее отклонение продольных осей сцепляемых автосцепок в горизонтальной плоскости, при котором обеспечивается автоматическое сцепление вагонов, составляет 175 мм. Конструкция автосцепки при некотором износе ее узлов и деталей должна обеспечивать автоматическое сцепление при вертикальном смещении продольных осей автосцепок до 150 мм. Для гарантии надежности сцепления вагонов в поезде разница по высоте между продольными осями сцепленных автосцепок согласно ПТЭ ограничена до 100 мм.
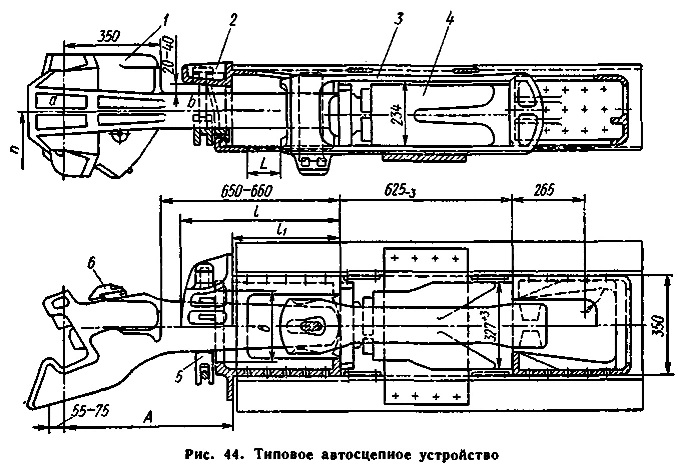
Детали автосцепного устройства по прочности должны удовлетворять следующим основным требованиям:
наибольшие напряжения в корпусе автосцепки от сжимающей или растягивающей силы 250 тс при разности уровней осей сцепления 50 мм не должны превышать предела текучести материала QТ;
напряжения в упорных плитах, тяговых хомутах и клиньях или валиках тяговых хомутов при наиболее невыгодном приложении продольной сжимающей или растягивающей силы 250 тс не должны превышать 0,75Qт;
напряжения в передних и задних упорах автосцепного устройства при наиболее невыгодном приложении продольной сжимающей или растягивающей силы 250 тс не должны превышать напряжений, допускаемых для расчетного режима I (см. гл. П). Перемычку, соединяющую угольники упора, рассчитывают на действие перерезывающей силы 100 тс.
Под наиболее невыгодным приложением продольной силы понимают случай ее действия с перекосом, когда разность уровней осей сцепления может достигать 100 мм, а на угольники одного упора передаются усилия разной величины.
К поглощающим аппаратам автосцепного устройства помимо требований по прочности предъявляют специальные требования, определяемые назначением этих устройств. Продольная сила между вагонами, возникающая при трогании с места и осаживании однородного поезда весом до 10 тыс. тс, а также при маневровых соударениях одиночных вагонов со скоростью не менее 7,5 км/ч, не должна превышать 200 тс. Силу закрытия аппарата, на действие которой рассчитывают его прочность, принимают равной 250 тс.
Энергоемкость поглощающих аппаратов определяют из расчета на соударение со скоростью не менее 7,5 км/ч полностью загруженных одиночных вагонов данного типа. При этом продольное усилие между вагонами не должно превышать 200 тс. Ориентировочно энергоемкость поглощающего аппарата Э = mv^2/8, где т — масса вагона брутто; v — скорость соударения. Энергоемкость аппарата пассажирских вагонов должна быть не менее 3 тем, а максимальное продольное усилие при их соударении со скоростью до 7,5 км/ч — не более 150 тс.
Отдача поглощающего аппарата грузовых вагонов рекомендована не более 30%, а пассажирских — не более 50%, усилие предварительной затяжки — соответственно не более 20 и 5 тс. При статическом нагружении конечное усилие сопротивления поглощающего аппарата грузового вагона должно быть не менее 100 тс, а пассажирского — не менее 75 тс. Поглощающий аппарат должен обладать достаточно высокой надежностью, износостойкостью, и не допускать ускорений при соударении вагонов, превышающих уровень, определяемый принятыми нормами.
Сложные условия эксплуатации автосцепного устройства обусловливают высокие требования не только к конструкции его узлов и деталей, но и к материалу и качеству изготовления. Материал и качество изготовления литых деталей автосцепных устройств регламентированы соответствующими техническими условиями и стандартами. Корпус автосцепки