Добавлен: 08.11.2023
Просмотров: 269
Скачиваний: 4
ВНИМАНИЕ! Если данный файл нарушает Ваши авторские права, то обязательно сообщите нам.
СОДЕРЖАНИЕ | |
Введение....................................................................................................... 1. Организация работы контрольного пункта автосцепки…………….. 1.1 Характеристика и назначение контрольного пункта автосцепки…. 1.2 Конструкция и основные типы автосцепного устройства………. 1.3 Требования, предьявляемые автосцепным устройствам………….. 1.4 Автосцепное устройство и его неисправности…………………….. 2. Ремонт корпуса автосцепки и деталей механизма…………………... 2.1 Техническое состояние п ремонт автосцепного устройства………. 2.2 Система технического осмотра автосцепного устройства………… 2.3 Анализ повреждаемости автосцепного / устройства………………. 2.4Повреждаемость автосцепного устройства…..................................... 2.5 Технологических процесс ремонта автосцепного устройства……. 2.6 Технология замены дефектных деталей автосцепки………………. | |
1.Организация работы контрольного пункта автосцепки.
-
Характеристика и назначение контрольного пункта автосцепки.
Контрольный пункт автосцепки предназначен для ремонта, испытания автосцепки СА-З и СА-3М, поглощающих аппаратов Ш-1-ТМ, Ш-6-ТО-4.
В состав КПА входят следующие участки:
-
участок наружной очистки; -
участок разборки и дефектоскопирования; -
участок правильных работ; -
участок сварочно-наплавочных работ; -
участок механической обработки; -
участок сборки автосцепок; -
участок ремонта поглощающих аппаратов, тяговых хомутов, упорных плит и других деталей.
При полном осмотре съемные узлы и детали автосцепного устройства снимают с подвижного состава независимо от их состояния и направляют в КПА для проверки и ремонта.
К несъемным деталям автосцепного устройства относятся: ударная розетка, передние и задние упоры, располагающиеся на хребтовой балке, детали расцепного привода (фиксирующий кронштейн, кронштейн и расцепной рычаг). Ремонт и проверку несъемных деталей производят на вагоне, за исключением случаев, требующих их демонтажа.
Ремонт деталей автосцепного устройства, не снимаемых с подвижного состава, производят слесари по ремонту подвижного состава комплексной бригадой вагоносборочного участка.
КПА должен иметь два комплекта проверочных и один комплект контрольных шаблонов. Шаблоны должны проверяться не реже одного раза в год с постановкой даты проверки.
Автосцепное устройство относится к ответственным частям вагона. Оно предназначено для соединения (сцепления) вагонов и локомотивов, удержания их на определенном расстоянии друг от друга, передачи и смягчения действия продольных (растягивающих и сжимающих) усилий, развивающихся во время движения поезда.
Велико влияние исправного состояния автосцепного оборудования на безопасность движения. Не выявленные своевременно износы приводят к саморасцепу автосцепок или падению поврежденных деталей на путь, вызывая угрозу схода подвижного состава с рельсов.
Перевод подвижного состава на автосцепку позволил: рационально использовать силу тяги локомотивов, увеличить массу поезда и тем самым повысить провозную и пропускную способность железных дорог, устранить тяжелый и опасный труд сцепщика, ускорить процесс формирования поездов и оборот вагона, уменьшить тару вагонов за счет снятия буферных комплектов, облегчения боковых и концевых балок.
В процессе эксплуатации грузовых вагонов появляются различные неисправности автосцепного устройства: трещины, изломы, отсутствие деталей, уширение зева и износы деталей, повреждение или отсутствие ограничителей у автосцепок вагонов, зазор между потолком розетки и хвостовиком корпуса автосцепки менее 25 мм, протертости корпуса поглощающего аппарата, вызывающие потерю упругих свойств, просадка поглощающего аппарата, обрыв тягового хомута, изломы клина тягового хомута или верхней полосы, упорной плиты или поглощающего аппарата.
К эксплуатации не допускается подвижной состав со следующими неисправностями автосцепного оборудования: трещины, изломы, отсутствие деталей, уширение зева и износы деталей, высота автосцепки над уровнем головок рельсов более 1080 мм у порожних, 950 мм у грузовых загруженных вагонов, неправильная постановка маятниковых подвесок, повреждение или отсутствие ограничителей у автосцепок вагонов, длинная или короткая цепь расцепного привода, зазор между потолком розетки и хвостовиком корпуса автосцепки менее 25 мм, протертости корпуса поглощающего аппарата, вызывающие потерю упругих свойств.
Автосцепное устройство относится к ударно-тяговому оборудованию вагона. Оно предназначено для сцепления вагонов между собой и локомотивом, удержания их на определенном расстоянии друг от друга, восприятия передачи и смягчения воздействия растягивающих и сжимающих усилий, возникающих во время движения.
Это оборудование относится к объединенным устройствам, где совмещаются все функции ударных и тягово-сцепных приборов. До перевода подвижного состава железных дорог на автосцепку он оборудовался раздельными приборами, когда в качестве ударных приборов устанавливали буферные комплекты, а сцепных - винтовую упряжь. На каждом вагоне современной конструкции установлено два комплекта автосцепного устройства, размещенных по концам вагонной рамы. Автосцепное устройство состоит из корпуса автосцепки с деталями механизма расцепного привода, ударно-центрирующего прибора, упряжного устройства с поглощающим аппаратом и опорных частей. Основные части автосцепного устройства размещаются в консольной части хребтовой балки 5 рамы кузова вагона (рисунок 1.1).
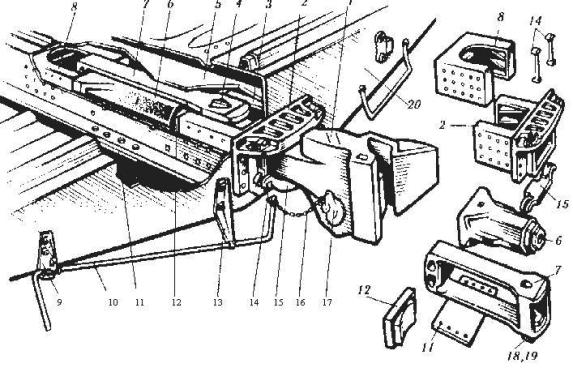
Рисунок 1.1 – Автосцепное устройство четырехосного вагона
Корпус 1 с механизмом сцепления предназначен для сцепления и расцепления вагонов, восприятия и передачи ударно-тяговых усилий упряжному устройству. Корпус автосцепки установлен в окно ударной розетки 2 и своим хвостовиком соединён с тяговым хомутом 7 при помощи клина 4, который вставляется снизу и опирается на два болта 18, закреплённых запорными шайбами и гайками. Расцепной привод служит для расцепления автосцепок и закреплён на концевой балке 20 рамы. Он состоит из двуплечного рычага 10, кронштейна с полочкой 9, державки 13 и цепи 16 для соединения рычага 10 с приводом механизма автосцепки 17. Ударно-центрирующий прибор воспринимает от корпуса автосцепки избыточную энергию удара после полного сжатия поглощающего аппарата и центрирует корпус автосцепки. Он состоит из ударной розетки 2, прикреплённой в средней части к концевой балке 20 рамы, двух маятниковых подвесок 14 и центрирующей балочки 15, на которую опирается корпус автосцепки 1. Упряжное устройство включает в себя тяговый хомут 7, клин 4, упорную плиту 12 и два болта 18 с планкой 19, запорными шайбами и шплинтом. Внутри тягового хомута 7 находится поглощающий аппарат 6, который размещается между задними упорами 8 и упорной плитой 12, взаимодействующей с передними упорами 3. Задние упоры 8 объединены между собой перемычкой и укреплены к вертикальным стенкам хребтовой балки 5 рамы. Передние упоры 3 объединены между собой посредством ударной розетки 2 и также жёстко прикреплены к вертикальным стенкам хребтовой балки 5. Упряжное устройство предохраняется от падения поддерживающей планкой 11, прикреплённой снизу к горизонтальным полкам хребтовой балки 5 восемью болтами.
Автосцепка (рисунок 1.2) состоит из корпуса и механизма сцепления. Корпус автосцепки представляет собой пустотелую фасонную отливку, состоящую из головной части и хвостовика.
Внутри головной части размещены детали механизма автосцепки. Она имеет большой 1 и малый 4 зубья, которые соединяясь образуют полость - зев. Торцевые поверхности малого зуба и зева воспринимают сжимающие усилия, а тяговые усилия передаются задними поверхностями большого и малого зубьев. На вертикальной стенке зева возле малого зуба имеется окно для замка 3, а рядом – окно для замкодержателя 2. В верхней части головы отлит выступ 5, который воспринимает жесткий удар при полном сжатии и передает его через розетку на раму. В пустотелом хвостовике сделано продолговатое отверстие 6 для клина, соединяющего корпус с тяговым хомутом. Торец хвостовика 7 служит для передачи ударных нагрузок и имеет цилиндрическую поверхность. Горизонтальная проекция зубьев, зева и выступающей части замка называется корпусом заземления.
Характеристика и назначение контрольного пункта автосцепки.
- участок дефектоскопирования, разборки и сборки автосцепки на этом участке автосцепки, поступившие в ремонт, очищают от грязи, разбирают, дефектоскопируют и обмеряют шаблонами для определения дальнейшего обьема работ, так же производится сборка отремонтированных автосцепок;
- участок сварочно-наплавочных работ: на этом участке производят сварочно-наплавочные работы на всех деталях автосцепного устройства;
- участок механической обработки: на этом участке производят механическую обработку после проведения на деталях автосцепного устройства сварочно-наплавочных работ:
- участок ремонта поглощающих аппаратов: на этом участке производят осмотр, разборку, ремонт, сборку и испытание поглощающих аппаратов, а так же ремонт центрирующих балочек, маятниковых подвесок, клиньев и упорных плит
- участок упрочнения индукционно-металлургическим способом: на этом участке производят упрочнения корпусов автосцепок, замков и замкодержателей
Контрольный пункт автосцепки входит в систему производственного участка по ремонту и изготовлению запасных частей вагонов пассажирского Вагонного депо и предназначен для ремонта деталей автосцепки типа СА-3, СА-3M, поглощающих аппаратов типа ЦНИИ-Н6, Р-2П, Р-5П, а так же тяговых хомутов, упорных плит, маятниковых подвесок, центрирующих балочек, корпусов автосцепки и поддерживающих плит. Весь объем работ производится согласно технологическому процессу
Участок дефектроскопирования, разборки и сборки автосцепок.
Снятое с вагонов автосцепное устройство и обмытое в моечной машине для тележек, транспортируется на тележке в КПА на участок разборки и очистки.
Автосцепки кран-балкой снимают с тележки и размещают на эстакаде для разборки. Корпуса без механизма сцепления с помощью кран-балки подаются на кантователь для дефектоскопирования. Продефектоскопированные автосцепки с помощью кран-балки устанавливают на кантователь для обмера шаблонами, производится обмер и размеловка корпуса автосцепки. Детали механизма сцепления проверяются шаблонами на верстаке
Корпуса автосцепок, не требующие ремонта сваркой, проверяют магнитопорошковым способом на стенде дефектоскопом МД-12 ПС и при отсутствии трещин устанавливают на сборочный стенд
Корпуса автосцепок, требующие проведения сварочных работ, так же подвергаются магнитному контролю и транспортируются на участок сварочных работ при помощи самоходной тележки.
Детали. имеющие износы и трещины, допускаемые к заварке, подаются на участок сварочных работ.
Обработанные детали проверяют шаблонами и клеймят на верстаке.
Собранная автосцепка проверяется шаблонами на стенде и кран-балкой подается на участок хранения отремонтированных автосцепок в сборочный цех.
Участок сварочно-наплавочных работ.
На сварочном столе при помощи приспособлений для наплавки деталей механизма сцепления производятся сварочно-наплавочные работы и заварка трещин. На кантователе производят сварочно-наплавочные работы корпусов автосцепок, на другом кантователе производят сварочно-наплавочные работы тяговых хомутов. При помощи кран-балки корпуса автосцепок, тяговые хомуты и детали укладывают на самоходную тележку и транспортируют на участок механической обработки
Участок механической обработки.
Наплавленные корпуса автосцепок обрабатываются на фрезерном станке до чертежных размеров. Тяговые хомуты и детали механизма обрабатываются на втором фрезерном станке, на котором так же обрабатываются упорные плиты и поддерживающие планки. Шип автосцепки отчерстия для валика подъемника и тыльная поверхность хвостовика автосцепки обрабатываются приспособлениями, конструкции которых разработаны Вагонным депо
Челябинск - Пассажирский совместно с ПКБ ЦВ
Участок ремонта поглощающих аппаратов.
Поглощающие аппараты осматривают проверяют