Файл: 2. Высокоскоростная револьверная головка на 12 инструментов с поворотом без автоматического подъема.docx
ВУЗ: Не указан
Категория: Не указан
Дисциплина: Не указана
Добавлен: 09.11.2023
Просмотров: 30
Скачиваний: 1
ВНИМАНИЕ! Если данный файл нарушает Ваши авторские права, то обязательно сообщите нам.
*****ДЕФЕКТНАЯ ВВЕПДОМОСТЬ И РЕМОНТ 2х ДЕТАЛЕЙ*****
Технология ремонта оборудования.
Ремонт металлорежущих станков начинается
с подготовительного этапа, в результате которого станок
внимательно осматривают и определяют дефекты. Техник и
мастер по ремонту составляют ведомость, где отражаются
выявленные дефекты и прилагаются чертежи подлежащих
замене деталей. Дефекты выявляются путем включения
оборудования и запуска его работы, в ходе которой
замечаются неточности, находящие отражение в журнале
записей и подвергающиеся тщательному анализу в целях
предотвращения возникновения подобной ситуации в
будущем. Затем наступает этап очистки, когда все детали
станка, в том числе и его корпус, очищаются от пыли, грязи и
смазывающей жидкости, выполняющей роль охлаждения.
Чтобы ремонт проходил качественно и посторонние
предметы не мешали работнику, место вокруг оборудования
освобождают. Так же освобождают внутренние резервуары
станка от масла, разъединяют полумуфту, снимают ремни,
предварительно отключив станок от питания, готовятся
необходимые инструменты и запчасти.
Этап разборки всех частей и деталей станка
подразумевает наличие конкретного плана действий,
намеченного в результате осмотра. Иногда требуется
разобрать только часть оборудования без осмотра ее
деталей. Иногда требуется разобрать полностью все детали
и механизмы станка, чтобы ясно представлять себе картину
восстановления его работы. Поэтому объем ремонтных
работ в каждом случае индивидуален. Однако существуют
особые правила, согласно которым необходимо разбирать
станок. К ним относятся:
1. Соблюдение последовательности разбора: от отдельных
частей до деталей. Иначе нарушается плотность соединения
механизмов;
2. Ознакомление с паспортом станка, схемами его деталей,
составление графика разборочно-сборочных работ;
3. Составление кинематической и гидравлической схем в
случае их отсутствия;
4. Составление дефектной ведомости после проверки всех
деталей на наличие отклонений в работе;
Изм. Лист № докум. Подп. Дата
Лист
5. Разборку следует организовывать таким образом, чтобы
обеспечить доступ к основным частям оборудования,
поэтому сначала снимаются вспомогательные детали, такие
как: дверцы, щитки, крышки, кожухи и т.д.;
6. Применение только исправных инструментов. Иначе
можно повредить годные детали;
7. Использование прессов, съемных или винтовых
приспособлений, чтобы снять шкивы, зубчатые колеса,
муфты и др. детали;
8. Использование молотков предполагает наличие выколоток
или подставок из мягкого металла во избежание
повреждений деталей;
9. Подогрев детали для облегчения ее снятия;
10. Аккуратность в снятии деталей, чтобы исключить
возможность повреждений;
11. Снятие деталей без применения силы;
12. Маркировка и расположение каждой детали в отдельном
ящике позволяет облегчить задачу поиска и хранения;
13. Закрытие ящика крышкой во избежание утраты детали;
14. Расположение крупных деталей на подставках недалеко
от станка;
15. Проставление отметок на узлах нерабочих поверхностей;
16. Применение ключей и отверток соответствующей формы
к гайкам и болтам;
17. Устранение ржавчины с помощью керосина, раствор
которого необходимо оставить на обрабатываемой
поверхности на 8-10 часов;
18. Применение механических инструментов при разборке
резьбовых соединений;
19. Удаление остатков сломанных деталей.
В результате разборочных работ происходит замена
устаревших деталей или их обновление с помощью
Изм. Лист № докум. Подп. Дата
Лист
промывочных растворов – керосина, соды, чистящих и
абразивных веществ. Дефективные детали помечают
маркером или краской.
Следующий этап – сборка, которую следует проводить
согласно чертежам и только после очистительных работ.
Монтаж оборудования.
Точность обработки режущим инструментом зависит от
правильности установки станка.
Однако как бы хорошо ни были обработаны поверхности
скольжения, точность обработки значительно снизится при
неправильной установке. Это наиболее частая причина неточности в
обработке.
Необходимо четко следовать заводским инструкциям по
установке оборудования; это – гарантия точности обработки.
Меры предосторожности при установке станка
ВНИМАНИЕ!
Не переносить тяжелые предметы в одиночку. Использовать подручных.
К работе на вилочном подъемнике или кране, а также к строповке станка допускаются только рабочие, имеющие соответствующую квалификацию.
При работе на вилочном подъемнике или кране следует соблюдать осторожность, чтобы не повредить окружающие предметы.
Использовать тросы или стропы соответствующей грузоподъемности.
Проверить цепной блок, тросы, стропы, таль и другое грузоподъемное оборудование перед эксплуатацией. Запрещается использовать неисправное грузоподъемное оборудование, поврежденные тросы и стропы.
ОСТОРОЖНО!
Правильно поднимать станок. Перед началом подъема следует слегка приподнять станок, чтобы убедиться в правильности его балансировки.
Угол наклона троса или стропа не должен превышать 60°.
Если в подъеме станка участвуют два или более рабочих, они должны согласовывать свои действия с помощью сигналов.
Во время подъема не допускать ударов станка, устройства ЧПУ или электрошкафа о другие предметы.
Перед подъемом станка следует убедиться в надежной фиксации узлов, а также в отсутствии на станке инструментов и других предметов.
Узел подачи СОЖ доставляется отдельно от станка.
Подготовка к подъему
(1) Зафиксировать револьверную головку, суппорт, заднюю бабку и измерительную
головку инструмента TOOL EYE (????) при включенном питании.
Зафиксировать револьверную головку на расстоянии 100 мм от нулевой точки оси X.
Для станков модели 500U необходимо зафиксировать суппорт на расстоянии –60 мм
от нулевой точки оси Z.
Для станков модели 1000U необходимо зафиксировать суппорт в нулевой точке оси Z.
Зафиксировать заднюю бабку в ее нулевой точке.
Зафиксировать измерительную головку инструмента TOOL EYE в отведенном
положении.
Установить все необходимые транспортировочные фиксаторы, чтобы закрепить
револьверную головку, суппорт и измерительную головку инструмента TOOL EYE.
См. подраздел 6-2-3.
(2) Выключить питание станка и главный цеховой рубильник. Отсоединить силовой
кабель от главного рубильника станка.
(3) Отсоединить от станка кабель и шланг насоса подачи СОЖ.
Отсоединить кабель, вынув из гнезда цилиндрическую вилку со стороны
электрошкафа.
Отсоединить шланг от насоса. Из шланга начнет вытекать оставшаяся в нем СОЖ,
которую следует слить в тару для отработанного масла. Объем вытекшей СОЖ будет равен примерно двум литрам.
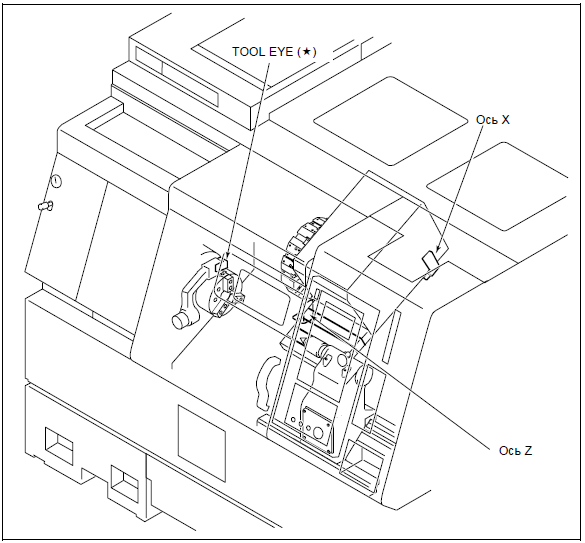
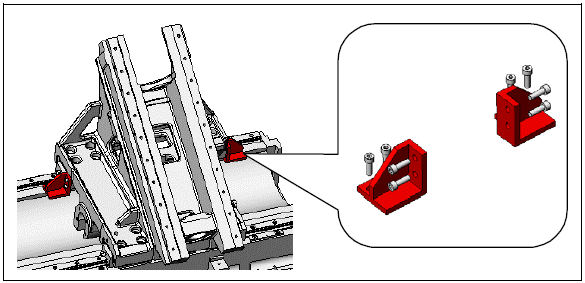
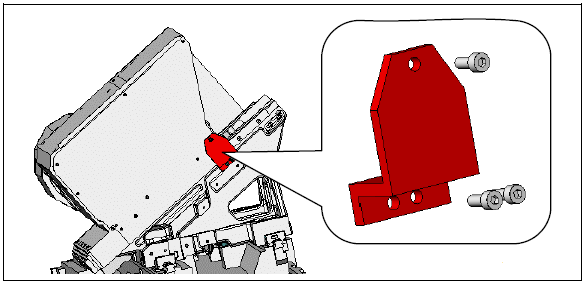
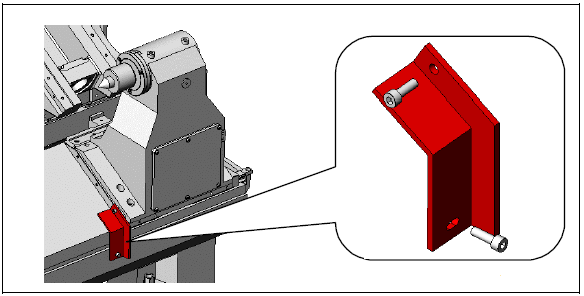
Подъем станка
Как правило, подъемом и перемещением станка на место установки занимается персонал
компании-производителя. Если эту работу берет на себя компания-заказчик, следует
принять все необходимые меры предосторожности и следовать указанному порядку
действий при подъеме станка.
(1) Зацепить подъемные тросы за крюк на станине и за оба конца трубы, проходящей
поперек станины.
Требования к подъемным приспособлениям приведены на рис. 6-5.
Для подъема станка модели 500U следует использовать кран грузоподъемностью не
менее 5 тонн. Для подъема станка модели 1000U грузоподъемность крана должна
быть не менее 6 тонн.
(2) Надеть тросы на крюк крана.
Во избежание повреждения станка при перемещении его краном рекомендуется
поместить между станком и тросами деревянные бруски или прокладки
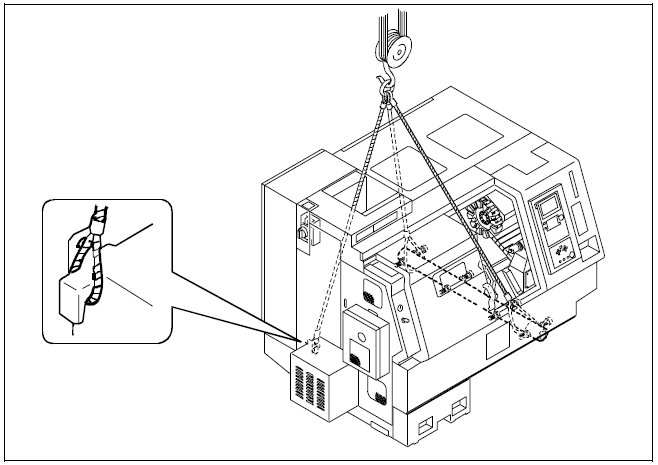
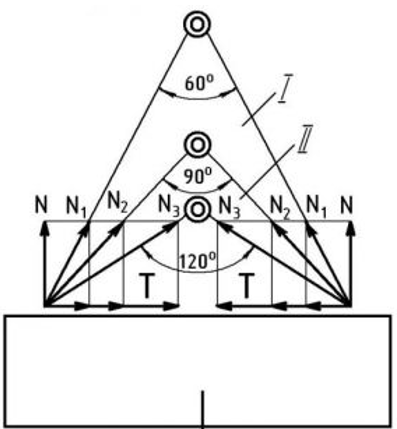
Стропа для груза рассчитывается по формуле :
S =
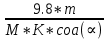
Где :
m – Масса станка
M – количество ветвей
К – до 4 используется значение коэффициента 1, а когда 4 ветви и более, применяется 0,75
∝ - угол отклонения ветвей от вертикальной оси.
S =

Порядок действий при установке станка
Точность обработки на станке во многом зависит от правильности его установки. Установке
станка следует уделять особое внимание и соблюдать при этом предельную осторожность.
1. Временное выравнивание
(1) Приподнять станок и вставить фундаментные болты, регулировочные болты, гайки и
фундаментные плиты в соответствующие отверстия в станине станка.
(2) Медленно опустить станок так, чтобы анкерные болты точно вошли в фундаментные
отверстия согласно чертежу фундамента.
* На этом этапе регулировочные болты не могут быть использованы; приподнять
станок над фундаментом.
(3) Провести временное выравнивание станка с помощью подкладных клиньев под
станком.
(4) После временного выравнивания станка закрепить анкерные болты строительным
раствором.
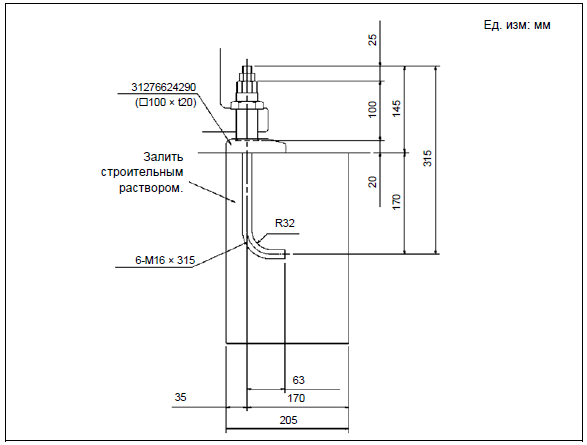
Проверка подсоединений
После завершения временного выравнивания станка и перед включением питания
необходимо проверить и убедиться в правильности выполнения следующих требований:
- сопротивление заземления – не более 10 Ом;
- винты клеммных колодок (должны быть плотно затянуты),
- соединители типа и другие соединители должны быть плотно затянуты;
- реле и таймеры должны быть установлены и подключены правильно;
- установки таймеров и тепловых реле должны быть правильными.
Подсоединение шланга подачи воздуха
Если станок оснащен дополнительными пневматическими устройствами, то необходимо
подсоединить шланг подачи воздуха к патрубку пневмоблока, который расположен под
крышкой с левой стороны станка. Шланг должен быть подсоединен надежно и правильно.
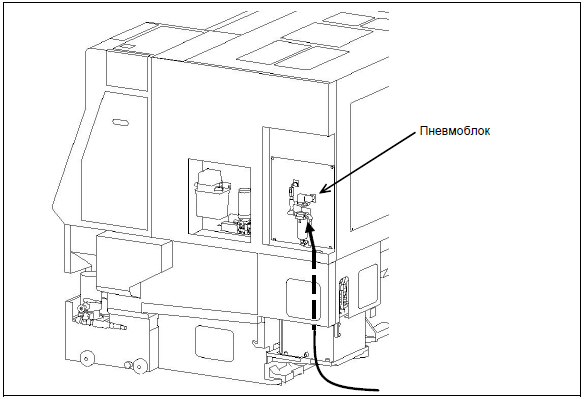
Пробный пуск
После подсоединения к станку силового кабеля и шланга подачи воздуха перед пробным
пуском станка необходимо убедиться, что
- отсутствуют какие-либо повреждения станка или его деталей;
- нет отсутствующих деталей или приспособлений;
- используемые марки масел, смазки и гидравлической жидкости соответствуют
требованиям производителя;
- патрон должным образом смазан;
- трубы и шланги гидросистемы надежно подсоединены;
- шланг подачи воздуха надежно подсоединен;
- бак СОЖ установлен правильно;
- сняты все приспособления для подъема станка и транспортировочные фиксаторы.