Файл: Эффективность тормозных средств является одним из важнейших условий, определяющих возможность повышения веса и скорости движения поездов, пропускной и провозной способности железных дорог.docx
ВУЗ: Не указан
Категория: Не указан
Дисциплина: Не указана
Добавлен: 09.11.2023
Просмотров: 96
Скачиваний: 2
ВНИМАНИЕ! Если данный файл нарушает Ваши авторские права, то обязательно сообщите нам.
Введение.
Эффективность тормозных средств является одним из важнейших условий, определяющих возможность повышения веса и скорости движения поездов, пропускной и провозной способности железных дорог. От свойств и состояния тормозного оборудования подвижного состава в значительной степени зависит безопасность движения.
Первая попытка применения автоматического тормоза на подвижном составе была предпринята в 1847 г. Этот тормоз был механическим и управлялся с помощью троса, натянутого вдоль поезда.
В 1869 г. появился первый пневматический неавтоматический тормоз, который не обеспечивал торможение поезда при разъединении воздушных рукавов, а в 1872 г. -- автоматический, особенностью которого являлось наличие на каждом вагоне воздухораспределителя и запасного резервуара.
В России широкое внедрение автоматического тормоза началось в 1882 г., в связи с чем в Петербурге в 1899 г. фирмой «Вестингауз» был построен тормозной завод. Первым изобретателем отечественного автоматического тормоза был машинист Ф. П. Казанцев. Его двухпроводной «неистощимый тормоз» был успешно испытан в пассажирском поезде в 1910 г. В 1923 г. Московский тормозной завод выпустил первые образцы отечественных тормозов системы Ф. П. Казанцева для пассажирских поездов. В 1927 г. Ф. П. Казанцев создал воздухораспределитель нового типа. Вскоре такими воздухораспределителями были оборудованы грузовые поезда.
Большие заслуги в деле создания и оснащения подвижного состава отечественными пневматическими автотормозами принадлежат известному изобретателю И. К. Матросову. Воздухораспределитель усл. № 320 его конструкции в 1932 г. был принят в качестве типового для грузового подвижного состава. В 1950--60 гг. практически весь подвижной состав железных дорог СССР был оборудован воздухораспределителями усл. № 270 и усл. № 292 и концевыми кранами системы и конструкции И. К. Матросова.
Широкое применение электропневматических тормозов на электропоездах началось с 1948 г., а в пассажирских поездах с локомотивной тягой с 1958 г., когда Московский тормозной завод приступил к серийному выпуску электровоздухораспределителей усл. № 170 и усл. № 305.
С 1947 г. вагонный парк железных дорог СССР начал оснащаться автоматическими регуляторами тормозной рычажной передачи, а с 1966 г. -- автоматическими регуляторами режимов (авторежимами торможения). Начиная с 1964 г. вагоны стали оборудоваться композиционными колодками, эксплуатационные и технологические качества которых продолжают совершенствоваться и сегодня.
Большую роль в развитии отечественного тормозостроения сыграли работы по теории торможения, основоположником которой является профессор Н. П. Петров. Современное развитие наука о торможении получила в трудах известных ученых В. Ф. Егорченко, В.Г.Иноземцева, Б.Л.Карвацкого, В.М.Казаринова и др.
В процессе развития и совершенствования тормозов большое внимание уделяется созданию новых устройств и систем безопасности, связанных с работой приборов тормозного оборудования, систем автоведения поезда, систем автоматического управления тормозами (САУТ), локомотивных скоростемеров. Только за последнее десятилетие были разработаны и внедрены в эксплуатацию устройство контроля параметров движения поезда «Дозор», телеметрическая система контроля бодрствования машиниста (ТСКБМ), электронный скоростемер КПД-3 (КПД-ЗВ), комплексное локомотивное устройство безопасности (КЛУБ) и др.
Каждый локомотив в процессе его эксплуатации требует систематической проверки состояния оборудования для своевременного обнаружения, устранения и предотвращения возможных неисправностей. На железных дорогах России принята система технического обслуживания и текущих ремонтов для подержания локомотивов в работоспособном состоянии.
Ремонт- совокупность технических мероприятий проводимых с целью восстановления первоначальных характеристик какого-либо технического устройства локомотива или локомотива в целом которые были утрачены в следствие износов или при возникновении нештатных ситуаций. В ремонтной практике различают 2 основных варианта системы технического обслуживания и ремонта: по наработке и по состоянию. Ремонт по наработке- локомотив изымается из эксплуатации при достижении определенной наработке, заданной заранее и независящей от технического состояния его оборудования. К этому типу относиться действующая система в ООО РЖД планово предупредительных ремонтов. Она позволяет объединить ремонтные операции различного оборудования и таким образом снижать продолжительность простоя локомотива. При этом осуществляется долговременное планирование программы и объема ремонтов различного вида, а также поставка необходимых запасных частей и материалов. Ремонт по состоянию- локомотив ставят в ремонт только в случае отказа какого либо устройства или при его состоянии, близком к отказу. При этом виде ремонта объем и периодичность ремонтных операций определяется в зависимости от фактического состояния оборудования локомотива. В системе планово предупредительных ремонтов есть методы организации технического обслуживания и ремонта локомотивов: Индивидуальный метод основан на возвращение снятых и отремонтированных деталей, узлов и агрегатов на тот же локомотив. При агрегатном методе на ремонтируемый локомотив устанавливают заранее отремонтированы или новые детали, узлы и агрегаты из технического запаса. Агрегатный метод дает существенно сокращение простоя локомотив в ремонте, особенно эффективность
обеспечивает крупно агрегатный метод, при котором предусматривается замена на ремонтах крупных узлов и агрегатов в сборе. Непременным условием агрегатного или крупно агрегатного метода ремонта является взаимозаменяемость деталей, узлов, агрегатов.
В ОАО РЖД в ремонтных депо применяют следующие формы организации ремонтных работ: стационарная - локомотив в течении всего периода ремонта находиться на одном рабочем месте (стойле), оборудованном в соответствии с объемом и характером ремонтных работ, и обслуживается комплексной бригадой слесарей по установленной технологии. Поточная форма - при этой форме объем выполняемых работ разбивают на ряд технологически однородных, равных по суммарной трудоемкости частей и закрепляют их за специально оборудованными рабочими местами (постами) образующую единую поточную линию. Каждый пост обслуживается специализированной группой слесарей. В данной работе отражено организация технологии ремонта крана вспомогательного тормоза усл. №254. В данной работе я рассмотрел назначение, конструкцию и работу крана вспомогательного тормоза усл. №254, а также его наиболее частые неисправности и методы устранения неполадок.
ЦЕЛЬ РАБОТЫ. Заданием на дипломную работу мне было предложено детально изучить назначение, конструкцию и работу крана вспомогательного тормоза усл. №254, а также, с учетом практических навыков, приобретенных во время прохождения производственной практики, описать технологический процесс его ремонта, правила охраны труда и рассчитать экономическую часть при ремонте одного крана вспомогательного тормоза усл. №254.
1.ОРГАНИЗАЦИОННО-ТЕХНОЛОГИЧЕСКАЯ ЧАСТЬ.
1.1Назначение и устройство крана вспомогательного тормоза усл. №254.
Для управления тормозами локомотивов отдельно от автоматических тормозов составов применяются краны вспомогательного тормоза (КВТ) № 254 и № 4ВК. Последний, трехходовый, золотниковый с неавтоматическими перекрышами кран устанавливался на локомотивах до 1957 г Впоследствии, на локомотивах более поздней постройки и до настоящего времени применяется кран № 254 с автоматическими перекрышами и реле давления
Кран вспомогательного тормоза (КВТ усл. №254) используется для управления тормозом локомотива независимо от тормозов состава. Кран вспомогательного тормоза №254 клапанно-поршневого типа, который восполняет утечки сжатого воздуха из тормозных цилиндров в тормозных положениях и имеет автоматические перекрыши с помощью крана обеспечивается постоянство времени наполнение тормозных цилиндров и отпуска при торможении воздухораспределителем, происходит ускоренное наполнение тормозных цилиндров при торможении краном №254, автоматически перекрыша с восполнением утечки из тормозных цилиндров, возможность приведения в действие и отпуска тормоза локомотива, не зависимо от тормозов состава.
КВТ усл. №254 включает в себя части: верхнюю(регулировочную), среднюю (повторительное реле) и нижнюю (привалочную плиту).
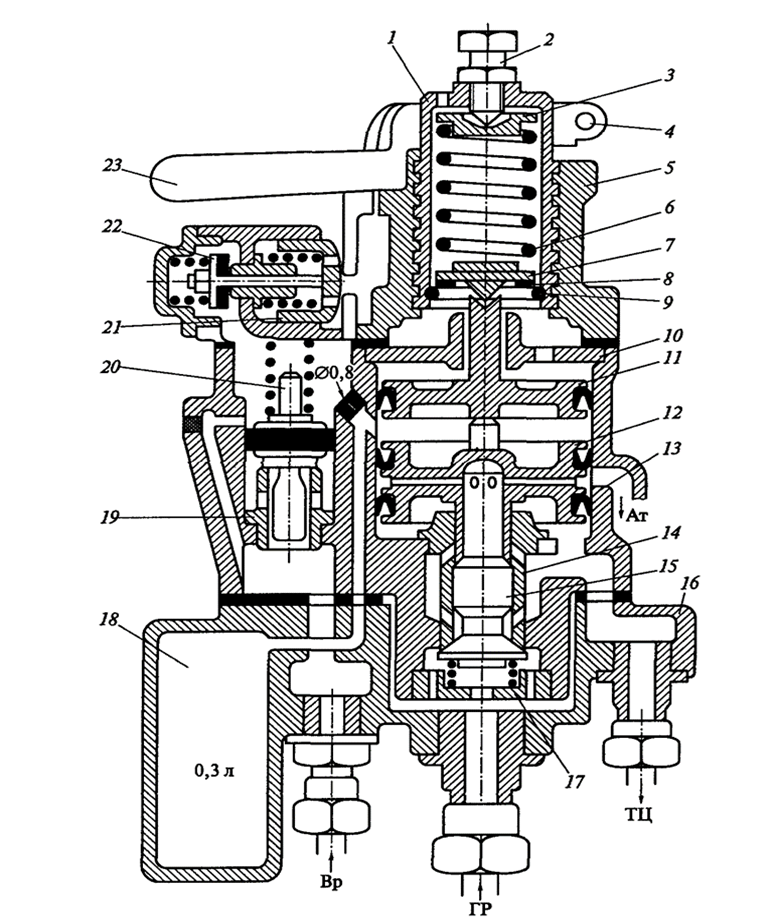
Рис. 1.1.1 Кран вспомогательного локомотивного тормоза усл. № 254:
1 — регулировочный стакан; 2 — регулировочный винт; 3, 7 — центрирующие (упорные) шайбы; 4 — винт крепления ручки на стакане; 5 — корпус верхней части; 6— регулировочная пружина; 8, 17— опорные шайбы; 9 — стопорное кольцо; 10 — направляющий диск; 11 — верхний поршень; 12 — нижний (двойной) поршень; 13 — корпус средней части; 14 — направляющая втулка; 15 — двух седельчатый клапан; 16 — корпус нижней части; 18 — камера объемом 0,3 л; 19 — седло переключательного поршенька; 20 — переключательный поршенек; 21 — втулка буфера отпуска; 22 — отпускной клапан; 23 — ручка.
Корпус крана выполнен из ковкого чугуна, на котором выбивают год и месяц выпуска крана, порядковый номер с начала года, клейма ОТК завода и инспектора МПС на заводе. В настоящее время ручку КВТ усл. №254 вместо ковкого чугуна изготавливают из пресс-материала АГ-4В. Вместо стальных шайб применяются шайбы из полиэтилена диаметром 45X24 мм и высота 3 мм. Уплотнительные прокладки выполнены из маслостойкой резины. Все винты выполнены из стали, а регулировочные клапана из латуни или меди. Также привалочная плита и регулировочный стакан изготавливаются из ковкого чугуна.
Верхняя часть состоит из корпуса (рис. 1.1.1), в котором расположен регулировочный стакан с левой двухзаходной резьбой, регулировочной пружиной и регулировочным винтом. В нижней части стакана стопорным кольцом закреплена опорная шайба.
Ручка закреплена на стакане винтом. Регулировочная пружина зажата в центрирующих (упорных) шайбах. В приливе корпуса верхней части расположен буфер отпуска, состоящий из подвижной втулки с атмосферными отверстиями и отпускного клапана, нагруженных соответствующими пружинами.
В корпусе средней части находятся уплотненные резиновыми манжетами верхний одиночный поршень, направляющий диск и нижний двойной поршень. В поездном положении ручки крана между хвостовиком верхнего поршня и центрирующей шайбой (направляющим упором) имеется зазор. Нижний поршень имеет полый шток и ряд радиальных отверстий между дисками. Полость между дисками нижнего поршня сообщена с атмосферой. Полость под нижним поршнем сообщена с ТЦ.
Под нижним поршнем находится двух седельчатый клапан, на который снизу действует пружина, упирающаяся вторым концом в шайбу. Верхняя (выпускная) часть клапана притерта к хвостовику нижнего поршня. Нижняя конусная часть клапана является впускной частью.
В приливе корпуса средней части в седле расположен нагруженный пружиной и уплотненный резиновой манжетой переключательный поршенек.
В нижней части корпуса крана (привалочной плите) расположены дополнительная камера объемом 0,3л и штуцеры для подключения трубопроводов от главных резервуаров ГР, воздухораспределителя Вр и тормозных цилиндров ТЦ.
Полости над переключательным поршеньком и между поршнями и дополнительная камера объемом 0,3л сообщаются через калиброванное отверстие диаметром 0,8мм.
Кран усл. № 254 имеет шесть рабочих положений ручки: 1 — отпускное (подвижная втулка буфера отпуска утоплена в прилив верхней части); 2 — поездное; 3 — 6 — тормозные (рис. 1.1.2).
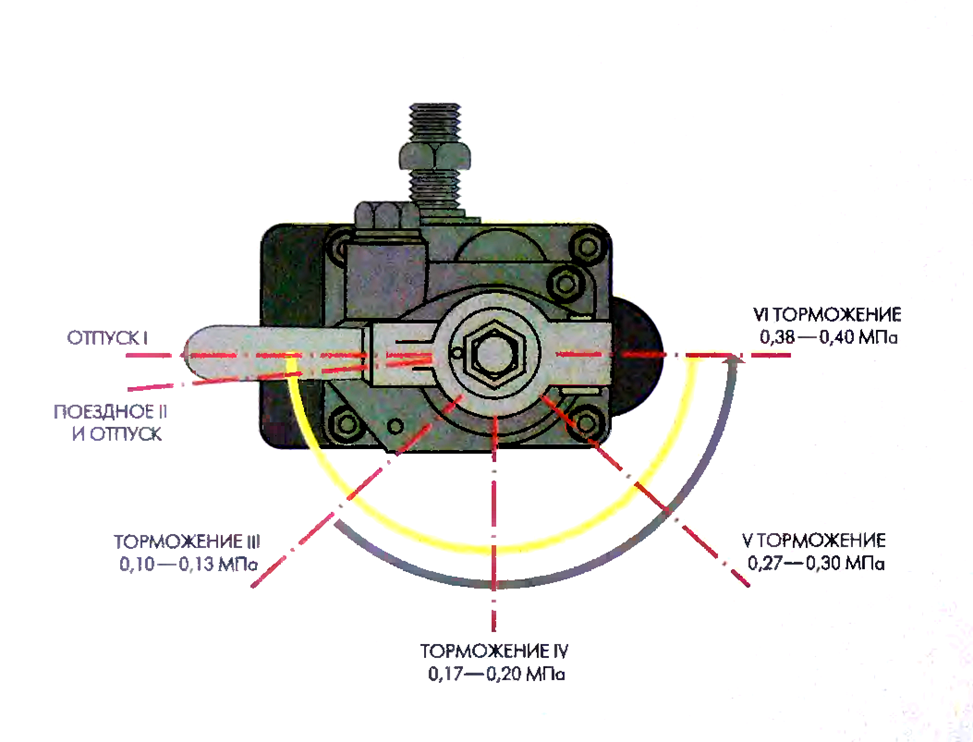
Рис. 1.1.2 Положения ручки вспомогательного крана машиниста усл. №254.
Если краном вспомогательного тормоза не пользуются, то его ручка находится в поездном положении под усилием пружины, действующей на втулку буфера отпуска.
Кран усл. № 254 может работать по двум схемам включения: независимой (кран отключен от Вр) и в качестве повторителя. При включении крана по независимой схеме к привалочной плите подключены только два трубопровода — от ГР и ТЦ.
Каждому тормозному положению ручки КВТ соответствует определенное усилие регулировочной пружины и, следовательно, определенное давление в ТЦ.
-
в положении III – 1,0 – 1,3 кгс/см²; -
в положении IV - 1,7 – 2,0 кгс/см²; -
в положении V – 2,7 – 3,0 кгс/см²; -
в положении VI – 3,8 – 4,0 кгс/см².
1.2 Работа крана вспомогательного тормоза усл. № 254.
1.2.1 Действие крана при независимой схеме включения.
При нахождении ручки КВТ в поездном положении усилие регулировочной пружины (см. рисунок 1.1.1) передается на опорную шайбу, закрепленную в стакане стопорным кольцом.
Для торможения локомотива ручку крана устанавливают в одно из тормозных положений. При этом регулировочный стакан вворачивается в корпус, выбирая зазор между центрирующей шайбой и хвостовиком верхнего поршня, и сжимает регулировочную пружину, усилие которой передается на верхний поршень. Последний опускается и перемещает вниз нижний двойной поршень, который своим хвостовиком отжимает от седла впускную конусную поверхность двух седельчатого клапана. При этом сжатый воздух из ГР начинает перетекать в ТЦ и одновременно под нижний поршень. Как только давление воздуха на нижний поршень преодолеет усилие регулировочной пружины, поршни переместятся на незначительное расстояние вверх, и двух седельчатый клапан под действием своей пружины закроется. Установившееся в ТЦ давление будет поддерживаться автоматически.