ВУЗ: Не указан
Категория: Не указан
Дисциплина: Не указана
Добавлен: 22.11.2023
Просмотров: 49
Скачиваний: 1
ВНИМАНИЕ! Если данный файл нарушает Ваши авторские права, то обязательно сообщите нам.
4. Плавка чугуна в дуговых печах
Устройство и работа электродуговых печей. Дуговые печи (рис. 8) питаются трехфазным током и имеют три электрода 1. Между электродами и шихтой или расплавленным металлом 7 в рабочем пространстве печи горят электрические дуги 4. Под действием тепла, излучаемого мощными дугами, шихта расплавляется, а затем жидкий металл нагревается до нужной температуры. Для подвода тока и регулирования мощности дуг печная установка имеет специальное электрооборудование, а для перемещения электродов, подъема и поворота свода, наклона печи и вращения ее корпуса – специальное механическое оборудование.
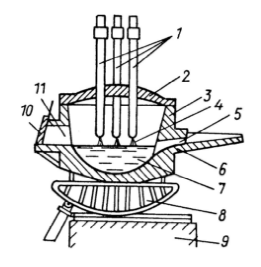
Рис. 8. Схема электродуговой печи:
1 – электрод;
2 – свод;
3 – корпус;
4 – электрическая дуга;
5 – выпускное отверстие;
6 – желоб;
7 – жидкий металл;
8 – опорные сектора;
9 – опорная станина;
10 – заслонка;
11 – рабочее окно
Печь состоит из корпуса 3 и съемного свода 2 с отверстиями для прохода электродов. На большинстве печей с механизированной загрузкой шихты в начале плавки корпус печи освобождается от свода. Бадья с предварительно загруженной в нее шихтой вводится в печь сверху, после чего дно бадьи открывается, и шихта высыпается в печь. Для проведения различных операций по ходу плавки, например для присадки добавочных материалов вручную (лопатами) или с помощью завалочной машины (мульдами), в печи имеется рабочее окно 11, закрываемое заслонкой 10. Для выпуска плавки (готового металла и шлака) через выпускное отверстие 5 и желоб 6 печь наклоняют. Для скачивания шлака по ходу плавки печь можно наклонять в сторону рабочего окна. При наклоне опорные сектора 8 люльки, на которой находится корпус печи, перекатываются по опорным станинам 9.
У корпуса печи (рис. 9) кожух, как правило, цилиндроконической формы, футерованный изнутри огнеупорами. Свод печи имеет водоохлаждаемое кольцо 4 и выполнен из термостойкого магнезитового кирпича 3 с кольцевыми вставками 2 из высокоглиноземистых или динасовых кирпичей, обладающих повышенным электросопротивлением и предотвращающих замыкание токов между электродами. Толщина футеровки свода составляет 230-300 мм для небольших печей и 380-460 мм – для крупных печей. Для уплотнения стыка свода с корпусом печи устанавливается песчаный затвор
1 в форме желоба, опоясывающего в виде кольца верхнюю часть кожуха. Нож кольца свода входит в песчаный затвор,
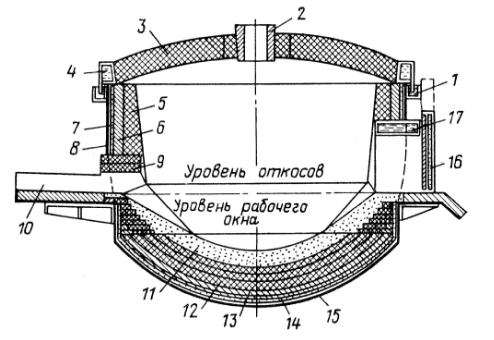
Рис. 9. Схема футеровки дуговой печи:
1 – песчаный затвор;
2 – кольцевая вставка;
3 – магнезитовый кирпич;
4 – водоохлаждаемое кольцо;
5 – огнеупорный слой;
6 – теплоизоляционный слой;
7 – теплоизоляционная засыпка;
8 – листовой асбест;
9 – арка;
10 – желоб;
11 – магнезитовый слой;
12 – магнезитовая футеровка;
13 – шамотный кирпич;
14 – теплоизоляционная засыпка; 15 – листовой асбест; 16 – заслонка; 17 – водоохлаждаемая коробка.
Внутренний (огнеупорный) слой 5 стен основных печей выполнен из магнезита или хромомагнезита, а теплоизоляционный слой – из шамота 6, засыпки 7 и нескольких слоев листового асбеста 8. Общая толщина стен на уровне откосов составляет 330-400 мм – для небольших печей и 600-700 мм – для крупных печей.
Арочка 9 выпускного отверстия изготовляется из тех же материалов, что и стены печи. Желоб 10 печи футеруется шамотным кирпичом. Под основной печи состоит из набивного магнезитового слоя 11, слоя магнезитовой футеровки 12, шамотного кирпича 13, теплоизоляционной засыпки 14 и листового асбеста 15. Толщина слоя набивки на современных печах не велика и в зависимости от их вместимости составляет 75-175 мм.
Рабочее окно обрамляется столбиками и аркой или водоохлаждаемой коробкой 17. Использование коробки предпочтительно, так как позволяет увеличить продолжительность работы этой части печи без ремонта. Заслонка 16 в малых и средних печах футерована изнутри огнеупорным кирпичом, а в крупных печах выполняется водоохлаждаемой с покрытием слоем огнеупорного цемента.
Огнеупорный слой футеровки кислых печей выполняется целиком из динасового кирпича, а теплоизоляционный – из тех же материалов, которые используются для футеровки аналогичного слоя основных печей.
Общая характеристика и физико-химические особенности дуговой плавки чугуна. Для плавки чугуна применяют трехфазные дуговые печи с зависимой дугой, в которых электрическая дуга образуется между электродами и металлом. Дуговые печи могут иметь как кислую, так и основную футеровку. Соответственно и процесс плавки является кислым или основным. Все приведенные выше положения относительно взаимодействия фаз при тех или иных шлаках действительны и для плавки чугуна в дуговых печах, т.е. при кислом процессе кремний угорает меньше, марганец больше, чем при основном; при основном процессе можно удалить серу и фосфор по реакциям:
FeS + СаО = CaS + FeO; FeS + Mg = MgS + Fe; 2Р + 5FeO = Р2О5 + 5Fe; 3FeO + Р2О5 = (FeO)3Р2О5; (FeO)3P2O5 + 4CaO = (CaO)4P2О5 + 3FeO.
После загрузки шихты электроды опускают, и начинается процесс плавки, который характеризуется высоким усвоением теплоты шихтой, со всех сторон окружающей дугу (в период расплавления КПД достигает 85 %). В шихте проплавляются так называемые колодцы. Этот период плавки сопровождается сильным шумом, треском, выделением большого количества дыма. Когда весь металл расплавится, дуга горит более спокойно, и передача теплоты происходит лишь у поверхности расплавленного металла: интенсивно в районах дуговых разрядов и менее интенсивно по остальной поверхности. Поэтому КПД при перегреве ниже. Элементы выгорают при высоких температурах и наличии в атмосфере печи кислорода. Железо окисляется, затем уже оксид железа окисляет элементы (С, Si, Мn):
Fe + 1/2О2 = FeO; (17)
FeO + Me = МеО + Fe. (18)
Характерной особенностью дуговой плавки чугуна является недопустимость закипания ванны, т.е. протекания реакции
[FeO] + [С] = [Fe] + {СО}. (19)
В связи с этим содержание FeO в шлаке не должно превышать 12 %, что достигается регулярным раскислением шлака вводимым в него карбюризатором
(FeO) + (С) = [Fe] + {СО}, (20)
в связи с чем, равновесие распределения (FeO) ↔ [FeO] сдвигается влево и закипания ванны, т.е. выделение СО по реакции (20), не допускается.
Технология плавки чугуна монопроцессом в дуговой печи. В качестве шихты используют в основном чугунный и стальной лом, возврат, а также некоторое количество свежих чушковых чугунов. Расчет шихты производится исходя из химического состава имеющихся шихтовых материалов и угара элементов. Обычно принимают угар углерода 10 %, кремния 10 % и марганца 20 %. Следует учитывать, что при применении в шихте стружки угар элементов значительно возрастет.
Перед каждой плавкой проводят мелкий ремонт футеровки путем заправки подины и откосов, которая заключается в том, что на имеющиеся на подине и откосах углубления сразу по окончании предыдущей плавки наносят смесь, состоящую из 90-92 % кварцевого песка, 5-6 % жидкого стекла и 3-4 %
Н2О. При основной футеровке заправку выполняют доломитовой или магнезитовой массой.
Загрузка шихты производится при помощи специализированной бадьи, в которую на шихтовом дворе помещают определенную порцию шихты (обычно масса порции составляет около половины емкости печи). Для загрузки шихты в ванну печи свод отводится в сторону, бадью устанавливают соосно с ванной печи и раскрывают днище. В бадью или непосредственно в печь перед загрузкой вводят карбюризатор в количестве 75 % от расчетного (электродный бой, электродная крошка и т.п.).
В загруженной и закрытой сводом печи начинают процесс плавки, т.е. электроды под напряжением вводят до контакта с шихтой. После установления устойчивых дуговых разрядов печь включают на высшую ступень мощности. По мере расплавления шихты нерасплавившиеся куски сталкивают в образовавшиеся колодцы. Для наведения шлака вводят шлакообразующие компоненты – известь и песок. Их массу выбирают таким образом, чтобы к концу плавки металл был покрыт слоем шлака толщиной около 50 мм. Шлак должен иметь невысокую вязкость (легко сливаться с пробной ложки), а после затвердевания иметь плотный излом с зеленоватой поверхностью. Черный цвет и пузырчатый излом шлака в твердом состоянии свидетельствуют о его высокой окисленности. В этом случае шлак надо частично удалить и ввести новые шлакообразующие компоненты.
Для наведения основного шлака в печь с основной футеровкой вводят известь в количестве 0,15 кг на 1 т металла для удаления 0,001 % S.
После полного расплавления берут пробу на химический анализ и на отбел, а печь включают на вторую ступень и перегревают металл до 1400-1450 °С. Затем скачивают, т.е. удаляют, шлак, вводят в печь оставшиеся от общей расчетной массы 25 % карбюризатора, а также песок и известь. По результатам первого экспресс-анализа добавляют в печь ферросплавы. Затем металл перегревают до 1440-1480 °С и выпускают его в ковш.
Преимуществами плавки чугуна в дуговых печах являются возможность форсированного расплавления при большой удельной мощности (до 1000 кВт на 1 т шихты) и высоком КПД, использование практически любых шихтовых материалов и широкие возможности по металлургической обработке расплава шлаками, которые имеют высокую активность благодаря нагреву от дуговых разрядов.
К недостаткам плавки чугуна в дуговых печах относятся высокий уровень шума дуговых разрядов, обильное выделение бурого дыма и низкий КПД при перегреве.
5. Плавка чугуна в индукционных печах
Устройство и работа индукционных печей. Индукционные печи используются в качестве первичного агрегата для плавки на твердой шихте или в качестве вторичного агрегата (миксера), при выдержке или подогреве жидкого металла, полученного в другом плавильном агрегате.
Индукционные тигельные печи. Для плавки чугуна на твердой шихте широко применяют тигельные индукционные печи ИЧТ (рис. 10). Такие печи удобны в эксплуатации, в них легко получать различные чугуны. Печь состоит из следующих основных узлов: металлического каркаса 1, индуктора 2, тигля 3, крышки с механизмом подъема 6, рабочей площадки 7, токо- и водоподводящих устройств, заключенных в кожух 8.
Р
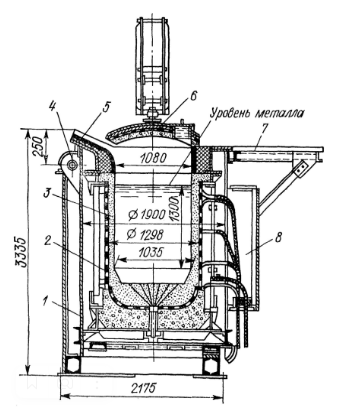
1 – каркас;
2 – индуктор;
3 – тигель;
4 – ось поворота печи;
5 – сливной носок;
6 – крышка с механизмом подъема;
7 – рабочая площадка;
8 – кожух
Каркас печи представляет собой сварную конструкцию, выполненную из листовой стали. Жесткость каркаса обеспечивается ребрами жесткости, равномерно расположенными по диаметру обечайки. Под сливным носком 5 расположена ось 4 поворота печи. Ось крепится в подшипниках, установленных на колоннах.
Печь имеет гидравлический механизм наклона, состоящий из маслонапорной установки, аппаратуры гидропривода и двух плунжеров. Посредством гидравлического механизма осуществляется наклон печи в одну сторону на любой угол до 100о для выдачи металла.
Главной частью печи является индуктор, представляющий собой медную водоохлаждаемую трубу. Катушки индуктора изолированы стеклолентой и микалентой; во избежание осевого перемещения индуктора он зафиксирован специальными прижимами из немагнитного материала. Индуктор печи окружен венцом из стальных пластин, которые вместе с прижимами создают надежное крепление индуктора, что особенно важно при наклоне печи.
Воротник печи и рабочая площадка составляют съемную сварную конструкцию. Воротник футеруется шамотными кирпичами, а для отвода дымовых газов в нем предусмотрен канал