ВУЗ: Не указан
Категория: Не указан
Дисциплина: Не указана
Добавлен: 22.11.2023
Просмотров: 51
Скачиваний: 1
ВНИМАНИЕ! Если данный файл нарушает Ваши авторские права, то обязательно сообщите нам.
в), за исключением графита. Особенно эффективно применение силикобария.
Обычно модификаторы вводят на желоб, в струю металла или в ковш. Расход модификатора зависит от его состава, состава чугуна, природы шихтовых материалов, условий плавки, технологии ввода, конструкции отливки и марки чугуна и колеблется, например, при использовании ФС75 в пределах 0,1-1,5 % от массы металла. Обычно считают, что 0,1 % ФС75 снижает отбел на 1 мм, и, исходя из требуемого снижения отбела, определяют количество вводимого модификатора. После ввода модификатора металл целесообразно перемешать механически, вибрационно, барботацией и другими методами. Перегрев чугуна при модифицировании должен быть тем больше, чем выше марка чугуна; обычно он находится в пределах 1370-1430 °С. Во избежание демодифицирования продолжительность выдержки чугуна не должна быть больше живучести модификатора. Например, для ФС75 выдержка не должна превышать следующих значений:
В случае появления признаков демодифицирования чугуна рекомендуется повторная обработка его модификатором. Контроль качества модифицирования производится по высоте отбела клиновой пробы.
Повышенной живучестью обладают новые комплексные модификаторы на основе силикобария. Они обеспечивают высокую стабильность процесса независимо от степени эвтектичности чугуна и существенно, в 2-3 раза, увеличивают продолжительность модифицирующего эффекта.
Иногда применяют модифицирование жидкими добавками. Например, при сливе двух жидких чугунов с различными составами или чугуна с жидкой сталью происходит не просто смешивание и выравнивание химического состава до среднего, а более сложные процессы, подобные модифицированию, которые способствуют измельчению структуры и увеличению механических свойств.
Для обработки чугуна газами и пылегазовыми смесями применяют кислород, азот, аргон, углекислый газ и углеводороды. В струю газа могут быть введены пылевидные добавки (модификаторы и т.п.). Применение кислорода для продувки чугуна значительно влияет на химический состав и свойства чугуна. При продувке другими газами изменяется газосодержание чугуна, которое также влияет на его свойства, при этом может произойти активизация или подавление процесса графитизации (активизация происходит при удалении из расплава водорода и азота, а подавление – при коагуляции центров кристаллизации). Обработка жидкого чугуна газами оказывает также влияние на форму графитовых включений и размеры эвтектического зерна. Эвтектическое зерно укрупняется при обработке аргоном и азотом и измельчается при обработке водородом, углекислым газом, кислородом и природным газом.
Для внепечной десульфурации может производиться обработка чугуна синтетическими шлаками. Обработка чугуна синтетическими шлаками, получаемыми из смеси 5-10 % плавикового шпата, 25-30 % электрокорунда, 60-70 % извести, позволяет снизить содержание серы на 90 % от первоначального. Синтетический шлак приготовляют в специальной шлакоплавильной печи, затем сливают его в ковш и заливают жидкий чугун, который, перемешиваясь со шлаком, подвергается десульфурации.
Обработка чугуна физическими методами – механическим перемешиванием и вибрацией производится в специальных устройствах (лопастных мешалках, вращающихся ковшах, виброустановках). На поверхность металла вводят рафинирующую смесь, содержащую, например, известь, плавиковый шпат, карбид кальция. При такой обработке жидкого чугуна в течение 2-4 мин в ковше содержание серы снижается с 0,1 до 0,01-0,02 %.
Наибольшее распространение в литейном производстве получила внепечная обработка чугуна модификаторами.
Лучшим вариантом промышленной технологии получения высококачественного серого чугуна является плавка в электропечах или дуплекс-процессом. В этом случае чугун заданного химического состава, выплавленный в первичном агрегате, сливают в печь ожидания. Из печи ожидания берут пробу на отбел. Если отбел до модифицирования больше требуемого, то в печь вводят смесь ФС75 и графита.
Наилучшие результаты по модифицированию достигаются при введении смеси ФС75 (0,15-0,6 % от массы металла), силикокальция (0,1-0,2 % от массы металла) и графита в зернах (0,1-0,2 % от массы металла).
Путем модифицирования можно получить вермикулярную форму графита в чугуне. Для плавки в этом случае применяют дуговые и индукционные печи, в отдельных случаях – дуплекс-процесс: вагранка – индукционная тигельная печь. В качестве исходного чугуна наиболее широко используют чугун эвтектического и близкого к нему состава (3,4-3,6 % С, 2,0-2,8 % Si, 0,3-0,6 % Мn, ≤ 0,2 % Р, ≤ 0,02 % S). До модифицирования целесообразно произвести десульфурацию чугуна. В качестве десульфураторов применяют известь, соду, технический карбид кальция или смеси на их основе.
Основой получения вермикулярной формы графита является модифицирование чугуна лигатурами, в состав которых входят элементы-сфероидизаторы (Mg, Y, Се), а также Аl и Ti; лигатурами Ni-Mg-Се, Се-V и другими редкоземельными элементами (РЗЭ).
Наиболее стабилен процесс получения вермикулярной формы графита путем модифицирования расплава лигатурами, содержащими РЗЭ, например, лигатура «СИИТМИШ», содержащая 25-30 % РЗЭ (большей частью иттрия), 7-10 %
Al, 55-60 % Si, ост. Fe.
В зависимости от условий производства лигатуру можно вводить непосредственно в печь при 1350-1400 °С, на дно разливочного ковша или в струю металла при 1430-1480 °С из расчета получения в чугуне остаточного содержания РЗЭ в пределах 0,1-0,15 %. Масса присадки лигатуры определяется количеством в ней РЗЭ и зависит в основном от содержания серы в исходном расплаве. Для чугуна, содержащего 0,015-0,03 % S, присадка лигатуры составляет 0,7-0,8 % от массы жидкого металла. Для ваграночного чугуна (0,08-0,1 % S) присадка лигатуры возрастает до 2,0-2,5 %. В этом случае целесообразна предварительная десульфурация ваграночного чугуна. После обработки лигатурой требуется дополнительное модифицирование чугуна графитизирующими присадками (ФС75 и др.), чтобы предотвратить образование в отливках ледебурита или структурно-свободного цементита.
Технология получения высокопрочного чугуна с шаровидным графитом включает два основных этапа: плавку и обработку чугуна добавками, сфероидизирующими графит. Получение требуемой микроструктуры достигается либо непосредственно в литом состоянии, либо путем термической обработки.
Состав шихты должен обеспечивать получение требуемого химического состава чугуна. Этот чугун имеет повышенное значение углеродного эквивалента. При ваграночной плавке в шихте содержится повышенное количество чушковых чугунов.
Наиболее целесообразно применять электроплавку и особенно дуплекс-процессы, например дуговая печь – индукционная тигельная печь. В состав шихты водят возврат, стальные отходы, графит, ферросилиций, ферромарганец. Чугун, переливаемый в индукционную печь, имеет следующий химический состав, %: 3,8 С, 1,7-1,8 Si, 0,3-0,4 Мn, ≤ 0,012 S, ≤ 0,06 Р, ≤ 0,05 Сr, ≤ 0,4-0,65 Ni, ≤ 0,01-0,03 Сu. По сравнению с серым чугуном он имеет на 0,4 % больше углерода, на 0,2-0,3 % меньше марганца и очень низкое содержание серы.
Процесс плавки должен обеспечивать получение чугуна с заданной температурой: температура чугуна на выдаче из печи по термопаре погружения составляет 1480-1530 °С, а температура начала заливки по пирометру соответственно 1370-1400 °С.
Получение шаровидной формы графита в чугуне возможно путем обработки расплава различными модификаторами, содержащими Mg, Се, Y и другие РЗЭ. Для сфероидизации графита в высокопрочном чугуне применяют лигатуры Ni-Сu-Mg, Ni-Сu-Si-Mg, Ni-Si-Са-Mg и др., а также комплексные модификаторы, в состав которых входят
Mg, Са, Si и РЗЭ.
Для получения высокопрочного чугуна применяют цериевые модификаторы: ферроцерий (40-55 % Се, 18-25 % La, 10-12 % Nd, 5-7 % Рr), мишметалл (52 % Се, 24 % La, 18 % Nd, 5 % Рr), цериевый мишметалл МЦ40, МЦ65, МЦ75 (цифра обозначает минимальное содержание Се). Кроме того, используют кремнийцериевые лигатуры типа «СИИТМИШ». Однако стабильное получение шаровидной формы графита в чугуне при помощи этих лигатур возможно лишь для тонкостенного литья или при заливке в кокиль.
Для стабильного получение чугуна с шаровидным графитом и воспроизводимости свойств металла в отливках с толщиной стенки до 150 мм используют комплексные модификаторы: Ц1 (6-15 % РЗЭ, 2-4 % Mg, 4-12 % Ва, 10-18 % Al, 29-17 % Si, остальное – Fe) и Ц2 (11-18 % РЗЭ, 1,5-3,5 % Mg, 0,05-5,0 % Al, 0,2-1,8 % Zr, 12-27 % Fe, остальное – Si). Расход этих модификаторов для получения ВЧ составляет 1,2-2,0 % от массы металла. При вводе 0,6-0,8 % модификатора получается чугун с вермикулярным графитом.
В противоположность сфероидизирующим модификаторам некоторые элементы являются демодификаторами, в связи с чем их содержание в чугуне не должно превышать, %: 0,009 Рb, 0,003 Bi, 0,026 Sb, 0,08 As, 0,04 Ti, 0,13 Sn, 0,3 Al. Влияние демодификаторов частично и полностью устраняется добавкой ремодификаторов, например Се.
При вводе в чугун металлического магния происходит его интенсивное испарение. Пары магния сгорают с выделением белого дыма. Реакция происходит очень быстро и носит бурный характер. Для уменьшения пироэффекта применяют лигатуры с содержанием магния не выше 12-15 % или смеси как с большой плотностью, содержащие никель и медь, так и более легкие, содержащие кремний и кальций.
Для получения отливок без отбела рекомендуется после ввода сфероидизирующего модификатора проводить вторичное графитизирующее модифицирование,которое способствует также уменьшению усадочных дефектов и внутренних напряжений. При этом в качестве модификатора применяют ферросилиций ФС75.
Способы обработки жидкого чугуна сфероидизирующими модификаторами связаны с применением специальных устройств для ввода магния или лигатур, дающих пироэффект, которые помещают в колокол или зарядную камеру. При помощи колокола модификатор можно вводить в копильник или в ковш в автоклаве (рис. 14).
Р
ис. 14. Устройство для ввода магния в жидкий чугун в автоклаве:
1 – автоклав;
2 – ковш;
3 – механизм запирания камеры;
4 – шток подачи колокола в ковш;
5 – механизм подачи и перемешивания;
6 – крышка;
7 – полость для магния;
8 – мешалка;
9 – механизм открывания крышки
Широкое распространение получили герметизированные ковши конвертерного или барабанного типа (рис. 15).
Рис. 15. Герметизированный ковш:
а – положение ковша перед обработкой;
б – положение ковша во время обработки
Лигатуры, не дающие пироэффекта, можно вводить в открытый ковш или в форму; можно применять магниевый пруток, механически вводимый в расплав или в испаритель, стыкуемый с герметизированным ковшом.
Наиболее простым способом является модифицирование лигатурами в ковше. Например, лигатуру Ni-Mg-Се вводят непосредственно в разливочный ковш. Вместе с лигатурой дают также ферросилиций и легирующие добавки. Однако лигатура Ni-Mg-Се имеет высокую стоимость, и большее распространение получили способы модифицирования чистым магнием.
При модифицировании чугуна происходят также обессеривание и дегазация, поэтому дозировка модификатора определяется расходом его на эти процессы, главным образом на соединение с серой. Необходимое количество магния (%от массы металла) можно определить по формуле
Mg = [(0,04÷0,1) + 0,76 ∙ (Sи – Sо)] ∙ А–1, (23)
где Sи, и Sо – исходное и остаточное содержание серы; 0,04÷0,1 % – остаточное содержание магния в чугуне (0,04 – для высококачественных чушковых чугунов; 0,05 – для чугунов с худшими наследственными свойствами и до 0,1 – для толстостенных отливок); А – коэффициент усвоения магния (зависит от способа модифицирования и температуры чугуна; при введении лигатуры Ni-Mg при 1400 °С А = 0,6÷0,7, при 1500 °С А = 0,44÷0,5).
При недостаточном количестве остаточного магния образуется смешанный или вермикулярный графит, а при избытке – частичный или полный отбел. При вводе модификатора в виде чистого магния в ковшах открытого типа или в копильник при помощи колокола расход магния в зависимости от температуры чугуна составляет 0,4-0,7 %;причем, чем выше температура металла, тем меньше расход магния. Магний в виде лигатуры вводят в количестве 2,0-2,5 % от массы металла. Расходы магния и лигатур снижаются, если их вводить в специальных автоклавах или в ковшах под давлением. При этом возрастает температура кипения магния, обеспечивается медленное парообразование, создаются условия для максимального усвоения магния.
Обычно модификаторы вводят на желоб, в струю металла или в ковш. Расход модификатора зависит от его состава, состава чугуна, природы шихтовых материалов, условий плавки, технологии ввода, конструкции отливки и марки чугуна и колеблется, например, при использовании ФС75 в пределах 0,1-1,5 % от массы металла. Обычно считают, что 0,1 % ФС75 снижает отбел на 1 мм, и, исходя из требуемого снижения отбела, определяют количество вводимого модификатора. После ввода модификатора металл целесообразно перемешать механически, вибрационно, барботацией и другими методами. Перегрев чугуна при модифицировании должен быть тем больше, чем выше марка чугуна; обычно он находится в пределах 1370-1430 °С. Во избежание демодифицирования продолжительность выдержки чугуна не должна быть больше живучести модификатора. Например, для ФС75 выдержка не должна превышать следующих значений:

В случае появления признаков демодифицирования чугуна рекомендуется повторная обработка его модификатором. Контроль качества модифицирования производится по высоте отбела клиновой пробы.
Повышенной живучестью обладают новые комплексные модификаторы на основе силикобария. Они обеспечивают высокую стабильность процесса независимо от степени эвтектичности чугуна и существенно, в 2-3 раза, увеличивают продолжительность модифицирующего эффекта.
Иногда применяют модифицирование жидкими добавками. Например, при сливе двух жидких чугунов с различными составами или чугуна с жидкой сталью происходит не просто смешивание и выравнивание химического состава до среднего, а более сложные процессы, подобные модифицированию, которые способствуют измельчению структуры и увеличению механических свойств.
Для обработки чугуна газами и пылегазовыми смесями применяют кислород, азот, аргон, углекислый газ и углеводороды. В струю газа могут быть введены пылевидные добавки (модификаторы и т.п.). Применение кислорода для продувки чугуна значительно влияет на химический состав и свойства чугуна. При продувке другими газами изменяется газосодержание чугуна, которое также влияет на его свойства, при этом может произойти активизация или подавление процесса графитизации (активизация происходит при удалении из расплава водорода и азота, а подавление – при коагуляции центров кристаллизации). Обработка жидкого чугуна газами оказывает также влияние на форму графитовых включений и размеры эвтектического зерна. Эвтектическое зерно укрупняется при обработке аргоном и азотом и измельчается при обработке водородом, углекислым газом, кислородом и природным газом.
Для внепечной десульфурации может производиться обработка чугуна синтетическими шлаками. Обработка чугуна синтетическими шлаками, получаемыми из смеси 5-10 % плавикового шпата, 25-30 % электрокорунда, 60-70 % извести, позволяет снизить содержание серы на 90 % от первоначального. Синтетический шлак приготовляют в специальной шлакоплавильной печи, затем сливают его в ковш и заливают жидкий чугун, который, перемешиваясь со шлаком, подвергается десульфурации.
Обработка чугуна физическими методами – механическим перемешиванием и вибрацией производится в специальных устройствах (лопастных мешалках, вращающихся ковшах, виброустановках). На поверхность металла вводят рафинирующую смесь, содержащую, например, известь, плавиковый шпат, карбид кальция. При такой обработке жидкого чугуна в течение 2-4 мин в ковше содержание серы снижается с 0,1 до 0,01-0,02 %.
Наибольшее распространение в литейном производстве получила внепечная обработка чугуна модификаторами.
Лучшим вариантом промышленной технологии получения высококачественного серого чугуна является плавка в электропечах или дуплекс-процессом. В этом случае чугун заданного химического состава, выплавленный в первичном агрегате, сливают в печь ожидания. Из печи ожидания берут пробу на отбел. Если отбел до модифицирования больше требуемого, то в печь вводят смесь ФС75 и графита.
Наилучшие результаты по модифицированию достигаются при введении смеси ФС75 (0,15-0,6 % от массы металла), силикокальция (0,1-0,2 % от массы металла) и графита в зернах (0,1-0,2 % от массы металла).
Путем модифицирования можно получить вермикулярную форму графита в чугуне. Для плавки в этом случае применяют дуговые и индукционные печи, в отдельных случаях – дуплекс-процесс: вагранка – индукционная тигельная печь. В качестве исходного чугуна наиболее широко используют чугун эвтектического и близкого к нему состава (3,4-3,6 % С, 2,0-2,8 % Si, 0,3-0,6 % Мn, ≤ 0,2 % Р, ≤ 0,02 % S). До модифицирования целесообразно произвести десульфурацию чугуна. В качестве десульфураторов применяют известь, соду, технический карбид кальция или смеси на их основе.
Основой получения вермикулярной формы графита является модифицирование чугуна лигатурами, в состав которых входят элементы-сфероидизаторы (Mg, Y, Се), а также Аl и Ti; лигатурами Ni-Mg-Се, Се-V и другими редкоземельными элементами (РЗЭ).
Наиболее стабилен процесс получения вермикулярной формы графита путем модифицирования расплава лигатурами, содержащими РЗЭ, например, лигатура «СИИТМИШ», содержащая 25-30 % РЗЭ (большей частью иттрия), 7-10 %
Al, 55-60 % Si, ост. Fe.
В зависимости от условий производства лигатуру можно вводить непосредственно в печь при 1350-1400 °С, на дно разливочного ковша или в струю металла при 1430-1480 °С из расчета получения в чугуне остаточного содержания РЗЭ в пределах 0,1-0,15 %. Масса присадки лигатуры определяется количеством в ней РЗЭ и зависит в основном от содержания серы в исходном расплаве. Для чугуна, содержащего 0,015-0,03 % S, присадка лигатуры составляет 0,7-0,8 % от массы жидкого металла. Для ваграночного чугуна (0,08-0,1 % S) присадка лигатуры возрастает до 2,0-2,5 %. В этом случае целесообразна предварительная десульфурация ваграночного чугуна. После обработки лигатурой требуется дополнительное модифицирование чугуна графитизирующими присадками (ФС75 и др.), чтобы предотвратить образование в отливках ледебурита или структурно-свободного цементита.
8. Получение высокопрочного чугуна с шаровидным графитом
Технология получения высокопрочного чугуна с шаровидным графитом включает два основных этапа: плавку и обработку чугуна добавками, сфероидизирующими графит. Получение требуемой микроструктуры достигается либо непосредственно в литом состоянии, либо путем термической обработки.
Состав шихты должен обеспечивать получение требуемого химического состава чугуна. Этот чугун имеет повышенное значение углеродного эквивалента. При ваграночной плавке в шихте содержится повышенное количество чушковых чугунов.
Наиболее целесообразно применять электроплавку и особенно дуплекс-процессы, например дуговая печь – индукционная тигельная печь. В состав шихты водят возврат, стальные отходы, графит, ферросилиций, ферромарганец. Чугун, переливаемый в индукционную печь, имеет следующий химический состав, %: 3,8 С, 1,7-1,8 Si, 0,3-0,4 Мn, ≤ 0,012 S, ≤ 0,06 Р, ≤ 0,05 Сr, ≤ 0,4-0,65 Ni, ≤ 0,01-0,03 Сu. По сравнению с серым чугуном он имеет на 0,4 % больше углерода, на 0,2-0,3 % меньше марганца и очень низкое содержание серы.
Процесс плавки должен обеспечивать получение чугуна с заданной температурой: температура чугуна на выдаче из печи по термопаре погружения составляет 1480-1530 °С, а температура начала заливки по пирометру соответственно 1370-1400 °С.
Получение шаровидной формы графита в чугуне возможно путем обработки расплава различными модификаторами, содержащими Mg, Се, Y и другие РЗЭ. Для сфероидизации графита в высокопрочном чугуне применяют лигатуры Ni-Сu-Mg, Ni-Сu-Si-Mg, Ni-Si-Са-Mg и др., а также комплексные модификаторы, в состав которых входят
Mg, Са, Si и РЗЭ.
Для получения высокопрочного чугуна применяют цериевые модификаторы: ферроцерий (40-55 % Се, 18-25 % La, 10-12 % Nd, 5-7 % Рr), мишметалл (52 % Се, 24 % La, 18 % Nd, 5 % Рr), цериевый мишметалл МЦ40, МЦ65, МЦ75 (цифра обозначает минимальное содержание Се). Кроме того, используют кремнийцериевые лигатуры типа «СИИТМИШ». Однако стабильное получение шаровидной формы графита в чугуне при помощи этих лигатур возможно лишь для тонкостенного литья или при заливке в кокиль.
Для стабильного получение чугуна с шаровидным графитом и воспроизводимости свойств металла в отливках с толщиной стенки до 150 мм используют комплексные модификаторы: Ц1 (6-15 % РЗЭ, 2-4 % Mg, 4-12 % Ва, 10-18 % Al, 29-17 % Si, остальное – Fe) и Ц2 (11-18 % РЗЭ, 1,5-3,5 % Mg, 0,05-5,0 % Al, 0,2-1,8 % Zr, 12-27 % Fe, остальное – Si). Расход этих модификаторов для получения ВЧ составляет 1,2-2,0 % от массы металла. При вводе 0,6-0,8 % модификатора получается чугун с вермикулярным графитом.
В противоположность сфероидизирующим модификаторам некоторые элементы являются демодификаторами, в связи с чем их содержание в чугуне не должно превышать, %: 0,009 Рb, 0,003 Bi, 0,026 Sb, 0,08 As, 0,04 Ti, 0,13 Sn, 0,3 Al. Влияние демодификаторов частично и полностью устраняется добавкой ремодификаторов, например Се.
При вводе в чугун металлического магния происходит его интенсивное испарение. Пары магния сгорают с выделением белого дыма. Реакция происходит очень быстро и носит бурный характер. Для уменьшения пироэффекта применяют лигатуры с содержанием магния не выше 12-15 % или смеси как с большой плотностью, содержащие никель и медь, так и более легкие, содержащие кремний и кальций.
Для получения отливок без отбела рекомендуется после ввода сфероидизирующего модификатора проводить вторичное графитизирующее модифицирование,которое способствует также уменьшению усадочных дефектов и внутренних напряжений. При этом в качестве модификатора применяют ферросилиций ФС75.
Способы обработки жидкого чугуна сфероидизирующими модификаторами связаны с применением специальных устройств для ввода магния или лигатур, дающих пироэффект, которые помещают в колокол или зарядную камеру. При помощи колокола модификатор можно вводить в копильник или в ковш в автоклаве (рис. 14).
Р
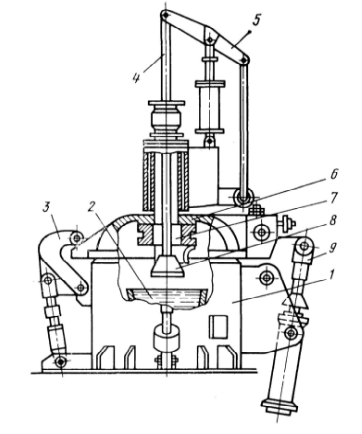
1 – автоклав;
2 – ковш;
3 – механизм запирания камеры;
4 – шток подачи колокола в ковш;
5 – механизм подачи и перемешивания;
6 – крышка;
7 – полость для магния;
8 – мешалка;
9 – механизм открывания крышки
Широкое распространение получили герметизированные ковши конвертерного или барабанного типа (рис. 15).
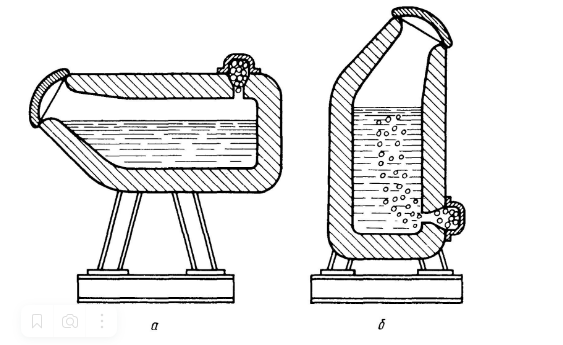
Рис. 15. Герметизированный ковш:
а – положение ковша перед обработкой;
б – положение ковша во время обработки
Лигатуры, не дающие пироэффекта, можно вводить в открытый ковш или в форму; можно применять магниевый пруток, механически вводимый в расплав или в испаритель, стыкуемый с герметизированным ковшом.
Наиболее простым способом является модифицирование лигатурами в ковше. Например, лигатуру Ni-Mg-Се вводят непосредственно в разливочный ковш. Вместе с лигатурой дают также ферросилиций и легирующие добавки. Однако лигатура Ni-Mg-Се имеет высокую стоимость, и большее распространение получили способы модифицирования чистым магнием.
При модифицировании чугуна происходят также обессеривание и дегазация, поэтому дозировка модификатора определяется расходом его на эти процессы, главным образом на соединение с серой. Необходимое количество магния (%от массы металла) можно определить по формуле
Mg = [(0,04÷0,1) + 0,76 ∙ (Sи – Sо)] ∙ А–1, (23)
где Sи, и Sо – исходное и остаточное содержание серы; 0,04÷0,1 % – остаточное содержание магния в чугуне (0,04 – для высококачественных чушковых чугунов; 0,05 – для чугунов с худшими наследственными свойствами и до 0,1 – для толстостенных отливок); А – коэффициент усвоения магния (зависит от способа модифицирования и температуры чугуна; при введении лигатуры Ni-Mg при 1400 °С А = 0,6÷0,7, при 1500 °С А = 0,44÷0,5).
При недостаточном количестве остаточного магния образуется смешанный или вермикулярный графит, а при избытке – частичный или полный отбел. При вводе модификатора в виде чистого магния в ковшах открытого типа или в копильник при помощи колокола расход магния в зависимости от температуры чугуна составляет 0,4-0,7 %;причем, чем выше температура металла, тем меньше расход магния. Магний в виде лигатуры вводят в количестве 2,0-2,5 % от массы металла. Расходы магния и лигатур снижаются, если их вводить в специальных автоклавах или в ковшах под давлением. При этом возрастает температура кипения магния, обеспечивается медленное парообразование, создаются условия для максимального усвоения магния.