ВУЗ: Не указан
Категория: Не указан
Дисциплина: Не указана
Добавлен: 22.11.2023
Просмотров: 50
Скачиваний: 1
ВНИМАНИЕ! Если данный файл нарушает Ваши авторские права, то обязательно сообщите нам.
, расположенный непосредственно под площадкой.
Плавильным пространством печи является тигель, выполняемый набивкой. В качестве набивочных материалов для изготовления тигля применяют кислые, основные и нейтральные огнеупорные массы.
Рабочее пространство печи закрывается крышкой из немагнитной стали, футерованной изнутри огнеупорным бетоном и теплоизолирующим материалом. Крышка снабжена механизмом подъема и поворота с ручным приводом рычажного типа. Загрузка шихты в печь производится сверху.
Токоподвод к печи осуществляется гибкими водоохлаждаемыми кабелями. Регулирование мощности печи производится автоматически регулятором режима.
Для управления наклоном печи предусмотрен пульт управления.
Индукционные канальные печи. При выдержке или подогреве жидкого металла, полученного в другом плавильном агрегате, например в вагранке, используют индукционные канальные печи со стальным сердечником ИЧКМ (рис. 11). Канальные печи обеспечивают получение чугуна высокого качества, а перегрев чугуна выше 1300 оС обходится значительно дешевле, чем в других плавильных агрегатах. Кроме того, они легко встраиваются в производственный комплекс с плавильными печами при реконструкции чугунолитейных цехов.
Рис. 11. Схема индукционной канальной печи: 1 – индукционная единица; 2 – стальной кожух; 3 – механизм поворота печи; 4 – сифон для заливки металла; 5 – сифон со сливным носком
Нагрев жидкого металла в каналах печи до заданной температуры производится в индукционных единицах 1, имеющих каналы и индукторы. Работа индукционной единицы построена на принципе трансформатора, где первичной обмоткой являются витки катушки индуктора, а вторичной – короткозамкнутый виток расплавленного металла в канале. Токи, индуктируемые в витке металла, нагревают его и создают условия для перемешивания жидкого металла в канале и в ванне печи.
В большинстве случаев печь имеет форму горизонтально расположенного стального барабана с двумя лобовыми стенками – стальной кожух 2, футерованный изнутри. Индукционная единица 1, как правило, выполняется отъемной, сменной и устанавливается в наиболее глубокой части ванны, что предотвращает возможность опорожнения канала при повороте печи механизмом 3. Металл из первичного плавильного агрегата поступает в миксер (канальную печь) через сифон
4. Для выдачи металла служит сифон 5 со сливным носком.
Футеровка стенок ванны состоит из наружного слоя – асбеста, прилегающего к кожуху, термоизоляционного кирпича и внутреннего рабочего слоя, выкладываемого несколькими рядами шамотного кирпича. В индукционной единице каналы выполняются в набивной футеровке из специальных материалов с высокой огнеупорностью, низким коэффициентом расширения и нейтральными свойствами по металлическому шаблону. Футеровка печи подвергается сушке и прокаливанию.
Физико-химические особенности плавки в индукционных печах. В отличие от вагранок и дуговых печей плавка в индукционных печах ведется с загрузкой шихты в жидкий металл, оставшийся от предыдущей плавки. В связи с этим нагрев и расплавление (рис. 2, б) шихты связаны с растворением ее компонентов в жидком металле, которое сопровождается массопереносом между фазами и поглощением теплоты не только на нагрев, но и на растворение. Например, растворение углерода протекает со значительным поглощением теплоты, а растворение кремния – с выделением. Отсюда следует важный вывод, что в индукционных печах энергетически выгоднее использовать низкокремнистые шихтовые материалы, а содержание кремния доводить до требуемого при помощи ферросплавов.
Второй важной особенностью плавки чугуна в индукционной печи является протекание тигельной реакции. Угары элементов и весь процесс плавки в индукционной печи с кислой футеровкой тесно связаны с равновесием тигельной реакции. На рис. 12 представлена диаграмма равновесных концентраций углерода и кремния при различных температурах. Если в индукционной печи плавить чугун с низким содержанием кремния и высоким содержанием углерода, то при достижении равновесной для данных концентраций кремния и углерода температуры начнет протекать тигельная реакция, что приведет к повышенному износу тигля печи и быстрому выходу ее из строя. В связи с этим температурный режим плавки в печи с кислой футеровкой необходимо выбирать в зависимости от химического состава перегреваемого жидкого чугуна.
Т
ехнология плавки в индукционной печи. Технологический процесс плавки в индукционной печи включает следующие операции: загрузку шихты, нагрев и расплавление, перегрев, науглероживание и доведение химического состава чугуна до заданного, а также термовременную обработку (выдержку). Загружаемая шихта частично погружается в расплав, создавая сплошную электропроводную среду, в которой индуктором наводятся вихревые токи. Загрузка в жидкий металл (остаток от предыдущей плавки, называемый «болотом») необходима потому, что при использовании электрического тока промышленной частоты в дискретных элементах шихты наведение вихревых токов малоэффективно.
Вихревые токи разогревают металл, и он плавится. Масса «болота» доходит до 50 % от общей массы металла в печи (емкости печи) и соответственно влияет на длительность периодов плавки. При этом загрузка в «болото» может осуществляться в несколько стадий.
Во время нагрева и плавления шихты происходят процессы окисления железа (Fe + 1/2О2 = FeO). Кислород воздуха окисляет также примеси железа. Оксиды железа, кремния, марганца образуют шлак. Оксид железа окисляет элементы чугуна: углерод, кремний, марганец (FeO + Me = МеО + Fe).
При плавке чугуна в индукционных печах для восстановления железа из оксида железа (FeO) целесообразно расходовать карбюризатор и экономить ферросплавы. Плавку необходимо вести при низком содержании кремния и марганца в расплаве и высоком содержании углерода. Для этого карбюризатор необходимо вводить на дно тигля в завалку, а ферросилиций и ферромарганец – в жидкий чугун после его расплавления и перегрева. Например, при загрузке углеродсодержащих присадок и ферросплавов (ФС75, ФМн5) в завалку угар углерода, кремния и марганца составляет соответственно 18-25, 30-32 и 52-55 % и наоборот, при вводе карбюризатора в завалку, а ферросплавов после перегрева до 1550 °С и охлаждения в печи до 1440-1460 °С угар углерода увеличивается до 30-35 %, а угар кремния и марганца резко снижается и составляет 5-7 и 18-24 % соответственно. В связи с этим, а также учитывая тепловые эффекты растворения компонентов, в первую очередь необходимо загружать карбюризатор и стальной лом. После их расплавления и растворения следует производить загрузку чугунного лома и возврата, ферросплавы вводить в последнюю очередь (при доводке).
Шлаки индукционной плавки обладают большой вязкостью, так как содержат 60-70 % SiО2 и имеют низкую температуру, что может привести к значительным потерям металла со шлаком. Их состав связан с режимом плавки, угаром элементов и переходом оксидов из поверхностного слоя футеровки в шлак. Кислотность шлаков возрастает от 0,9-1,1 в начале плавки до 6-8 при достижении температуры 1500 °С, содержание оксида железа в шлаке уменьшается с 40 до 10 %, соответственно увеличивается содержание SiO2 с 40 до 70 %. Содержание остальных компонентов изменяется незначительно (2-3 % СаО, 0,5-2,5 % МnО, 7-14 % Аl2О3). Увеличение содержания
SiО2 объясняется переходом ее из футеровки в результате образования сложных соединений типа SiО2·nFeO·mМnО, имеющих низкую температуру плавления, а также повышением ее удельной доли в шлаке вследствие снижения содержания FeO, который восстанавливается при высокой температуре преимущественно углеродом чугуна.
Науглероживание чугуна и доведение его до определенного химического состава является одной из основных операций индукционной плавки чугуна.
Заключительной операцией индукционной плавки чугуна является термовременная обработка, которую проводят с целью гомогенизации расплава и уменьшения вредного влияния наследственности исходных шихтовых материалов. Термовременная обработка представляет собой выдержку при температуре на 50 °С превышающей равновесную температуру тигельной реакции. Длительность выдержки, например, от 5 мин для СЧ15 до 20 мин для СЧ45.
Для получения чугуна требуемого качества необходимо осуществлять контроль качества исходных шихтовых материалов, флюсов, карбюризаторов, химического состава чугуна и его температуры, отбела, твердости.
Качество исходных шихтовых материалов контролируется в соответствии с ГОСТами на отбор проб и химическим анализом образцов. Их характеристики должны удовлетворять требованиям ГОСТов на соответствующие шихтовые материалы. Дозировка составляющих шихты производится массоизмерительными устройствами.
Контроль химического состава готового чугуна осуществляется либо спектральным экспресс-анализом, либо специальными приборами для экспресс-анализа углерода; содержание кремния можно определить по значению термо-ЭДС. Наиболее эффективно применение квантометров. Многоканальные вакуумные фотоэлектрические спектральные приборы позволяют за 3 мин определить содержание в чугуне С, Si, Мn, S, Р, Сr, Ni и других элементов.
Определение углеродного эквивалента может быть произведено термографическим методом по кривой охлаждения чугуна. Жидкий чугун заливают в специальную пробу, в которой установлена термопара, и фиксируют кривую охлаждения. В зависимости от температуры ликвидуса и температурного интервала затвердевания
Сэк = 12,8 – 0,0075 ∙ tл; (21)
Сэк = 4,28 – 0,0072 ∙ Dtинт. (22)
Эти формулы не являются универсальными. Они пригодны только для немодифицированных чугунов СЧ15, СЧ20, СЧ25.
Контроль механических свойств при плавке производится по величине отбела и твердости металла пробы. На рис. 13 приведены пробы для определения отбела и твердости.
Р
ис. 13. Формы проб:
а – клин на отбел;
б – проба для определения твердости;
1 – стержень;
2 – металлическая пластина;
3 – проба;
4 – место замера твердости
Контроль температуры жидкого чугуна производится при помощи оптических пирометров и термопар погружения. Точность измерения температуры оптическим пирометром низкая (±28 градусов). Кроме того, яркостная температура ниже истинной, т.е. замеряемой термопарой погружения. Тем не менее, в цехах практически очень часто пользуются пирометрами. Это позволяет в идентичных условиях работы иметь сравнительные данные по температуре чугуна.
Получение серого чугуна базируется на использовании качественных шихтовых материалов, применении электроплавки на заключительной стадии получения жидкого чугуна, контроле процесса на всех этапах с оперативным воздействием на него и внепечной обработке чугуна.
Качество шихтовых материалов особенно важно при ваграночной плавке: мелкая и тем более окисленная шихта не может быть основой качественного чугуна, в то же время чрезмерно крупные куски чугуна или стального лома также недопустимы, так как они не расплавляются в зоне плавления, доходят до фурм и нарушают ход ваграночного процесса.
Применение электроплавки – основа получения высококачественного чугуна, так как в этом случае значительно расширяются возможности достижения требуемой температуры чугуна, доводки его по химическому составу, включая введение различных добавок, улучшающих и стабилизирующих его свойства.
На заключительной стадии получения готового жидкого сплава наиболее важной является внепечная обработка жидкого чугуна, т.е. обработка чугуна дополнительно вводимыми веществами (модификаторами и другими добавками), или обработка методами внешнего воздействия.
Обработка чугуна модификаторами и другими добавками получила широкое распространение в литейном производстве благодаря своей простоте и высокой эффективности. В настоящее время разработано много различных модификаторов. Наибольшее распространение как модификатор в производстве отливок из серого чугуна получил ферросилиций, введение которого позволяет получить чугун с мелкозернистой структурой, уменьшает отбел и улучшает механические свойства чугуна. Наиболее эффективно отбел снимается смесями алюминия и ферросилиция, алюминия и графита. Модификаторы, содержащие РЗМ, также эффективно снижают отбел, но до определенного предела их расхода, при введении более 0,2 % отбел начинает увеличиваться. Введение некоторых элементов даже в весьма малых количествах оказывает значительное влияние на формирование структуры и свойства чугуна. Все модификаторы увеличивают предел прочности при растяжении (σ
Плавильным пространством печи является тигель, выполняемый набивкой. В качестве набивочных материалов для изготовления тигля применяют кислые, основные и нейтральные огнеупорные массы.
Рабочее пространство печи закрывается крышкой из немагнитной стали, футерованной изнутри огнеупорным бетоном и теплоизолирующим материалом. Крышка снабжена механизмом подъема и поворота с ручным приводом рычажного типа. Загрузка шихты в печь производится сверху.
Токоподвод к печи осуществляется гибкими водоохлаждаемыми кабелями. Регулирование мощности печи производится автоматически регулятором режима.
Для управления наклоном печи предусмотрен пульт управления.
Индукционные канальные печи. При выдержке или подогреве жидкого металла, полученного в другом плавильном агрегате, например в вагранке, используют индукционные канальные печи со стальным сердечником ИЧКМ (рис. 11). Канальные печи обеспечивают получение чугуна высокого качества, а перегрев чугуна выше 1300 оС обходится значительно дешевле, чем в других плавильных агрегатах. Кроме того, они легко встраиваются в производственный комплекс с плавильными печами при реконструкции чугунолитейных цехов.

Рис. 11. Схема индукционной канальной печи: 1 – индукционная единица; 2 – стальной кожух; 3 – механизм поворота печи; 4 – сифон для заливки металла; 5 – сифон со сливным носком
Нагрев жидкого металла в каналах печи до заданной температуры производится в индукционных единицах 1, имеющих каналы и индукторы. Работа индукционной единицы построена на принципе трансформатора, где первичной обмоткой являются витки катушки индуктора, а вторичной – короткозамкнутый виток расплавленного металла в канале. Токи, индуктируемые в витке металла, нагревают его и создают условия для перемешивания жидкого металла в канале и в ванне печи.
В большинстве случаев печь имеет форму горизонтально расположенного стального барабана с двумя лобовыми стенками – стальной кожух 2, футерованный изнутри. Индукционная единица 1, как правило, выполняется отъемной, сменной и устанавливается в наиболее глубокой части ванны, что предотвращает возможность опорожнения канала при повороте печи механизмом 3. Металл из первичного плавильного агрегата поступает в миксер (канальную печь) через сифон
4. Для выдачи металла служит сифон 5 со сливным носком.
Футеровка стенок ванны состоит из наружного слоя – асбеста, прилегающего к кожуху, термоизоляционного кирпича и внутреннего рабочего слоя, выкладываемого несколькими рядами шамотного кирпича. В индукционной единице каналы выполняются в набивной футеровке из специальных материалов с высокой огнеупорностью, низким коэффициентом расширения и нейтральными свойствами по металлическому шаблону. Футеровка печи подвергается сушке и прокаливанию.
Физико-химические особенности плавки в индукционных печах. В отличие от вагранок и дуговых печей плавка в индукционных печах ведется с загрузкой шихты в жидкий металл, оставшийся от предыдущей плавки. В связи с этим нагрев и расплавление (рис. 2, б) шихты связаны с растворением ее компонентов в жидком металле, которое сопровождается массопереносом между фазами и поглощением теплоты не только на нагрев, но и на растворение. Например, растворение углерода протекает со значительным поглощением теплоты, а растворение кремния – с выделением. Отсюда следует важный вывод, что в индукционных печах энергетически выгоднее использовать низкокремнистые шихтовые материалы, а содержание кремния доводить до требуемого при помощи ферросплавов.
Второй важной особенностью плавки чугуна в индукционной печи является протекание тигельной реакции. Угары элементов и весь процесс плавки в индукционной печи с кислой футеровкой тесно связаны с равновесием тигельной реакции. На рис. 12 представлена диаграмма равновесных концентраций углерода и кремния при различных температурах. Если в индукционной печи плавить чугун с низким содержанием кремния и высоким содержанием углерода, то при достижении равновесной для данных концентраций кремния и углерода температуры начнет протекать тигельная реакция, что приведет к повышенному износу тигля печи и быстрому выходу ее из строя. В связи с этим температурный режим плавки в печи с кислой футеровкой необходимо выбирать в зависимости от химического состава перегреваемого жидкого чугуна.
Т
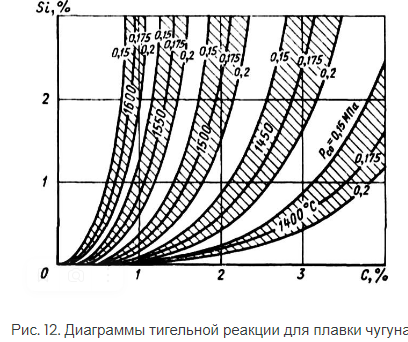
Вихревые токи разогревают металл, и он плавится. Масса «болота» доходит до 50 % от общей массы металла в печи (емкости печи) и соответственно влияет на длительность периодов плавки. При этом загрузка в «болото» может осуществляться в несколько стадий.
Во время нагрева и плавления шихты происходят процессы окисления железа (Fe + 1/2О2 = FeO). Кислород воздуха окисляет также примеси железа. Оксиды железа, кремния, марганца образуют шлак. Оксид железа окисляет элементы чугуна: углерод, кремний, марганец (FeO + Me = МеО + Fe).
При плавке чугуна в индукционных печах для восстановления железа из оксида железа (FeO) целесообразно расходовать карбюризатор и экономить ферросплавы. Плавку необходимо вести при низком содержании кремния и марганца в расплаве и высоком содержании углерода. Для этого карбюризатор необходимо вводить на дно тигля в завалку, а ферросилиций и ферромарганец – в жидкий чугун после его расплавления и перегрева. Например, при загрузке углеродсодержащих присадок и ферросплавов (ФС75, ФМн5) в завалку угар углерода, кремния и марганца составляет соответственно 18-25, 30-32 и 52-55 % и наоборот, при вводе карбюризатора в завалку, а ферросплавов после перегрева до 1550 °С и охлаждения в печи до 1440-1460 °С угар углерода увеличивается до 30-35 %, а угар кремния и марганца резко снижается и составляет 5-7 и 18-24 % соответственно. В связи с этим, а также учитывая тепловые эффекты растворения компонентов, в первую очередь необходимо загружать карбюризатор и стальной лом. После их расплавления и растворения следует производить загрузку чугунного лома и возврата, ферросплавы вводить в последнюю очередь (при доводке).
Шлаки индукционной плавки обладают большой вязкостью, так как содержат 60-70 % SiО2 и имеют низкую температуру, что может привести к значительным потерям металла со шлаком. Их состав связан с режимом плавки, угаром элементов и переходом оксидов из поверхностного слоя футеровки в шлак. Кислотность шлаков возрастает от 0,9-1,1 в начале плавки до 6-8 при достижении температуры 1500 °С, содержание оксида железа в шлаке уменьшается с 40 до 10 %, соответственно увеличивается содержание SiO2 с 40 до 70 %. Содержание остальных компонентов изменяется незначительно (2-3 % СаО, 0,5-2,5 % МnО, 7-14 % Аl2О3). Увеличение содержания
SiО2 объясняется переходом ее из футеровки в результате образования сложных соединений типа SiО2·nFeO·mМnО, имеющих низкую температуру плавления, а также повышением ее удельной доли в шлаке вследствие снижения содержания FeO, который восстанавливается при высокой температуре преимущественно углеродом чугуна.
Науглероживание чугуна и доведение его до определенного химического состава является одной из основных операций индукционной плавки чугуна.
Заключительной операцией индукционной плавки чугуна является термовременная обработка, которую проводят с целью гомогенизации расплава и уменьшения вредного влияния наследственности исходных шихтовых материалов. Термовременная обработка представляет собой выдержку при температуре на 50 °С превышающей равновесную температуру тигельной реакции. Длительность выдержки, например, от 5 мин для СЧ15 до 20 мин для СЧ45.
6. Контроль процесса плавки чугуна
Для получения чугуна требуемого качества необходимо осуществлять контроль качества исходных шихтовых материалов, флюсов, карбюризаторов, химического состава чугуна и его температуры, отбела, твердости.
Качество исходных шихтовых материалов контролируется в соответствии с ГОСТами на отбор проб и химическим анализом образцов. Их характеристики должны удовлетворять требованиям ГОСТов на соответствующие шихтовые материалы. Дозировка составляющих шихты производится массоизмерительными устройствами.
Контроль химического состава готового чугуна осуществляется либо спектральным экспресс-анализом, либо специальными приборами для экспресс-анализа углерода; содержание кремния можно определить по значению термо-ЭДС. Наиболее эффективно применение квантометров. Многоканальные вакуумные фотоэлектрические спектральные приборы позволяют за 3 мин определить содержание в чугуне С, Si, Мn, S, Р, Сr, Ni и других элементов.
Определение углеродного эквивалента может быть произведено термографическим методом по кривой охлаждения чугуна. Жидкий чугун заливают в специальную пробу, в которой установлена термопара, и фиксируют кривую охлаждения. В зависимости от температуры ликвидуса и температурного интервала затвердевания
Сэк = 12,8 – 0,0075 ∙ tл; (21)
Сэк = 4,28 – 0,0072 ∙ Dtинт. (22)
Эти формулы не являются универсальными. Они пригодны только для немодифицированных чугунов СЧ15, СЧ20, СЧ25.
Контроль механических свойств при плавке производится по величине отбела и твердости металла пробы. На рис. 13 приведены пробы для определения отбела и твердости.
Р
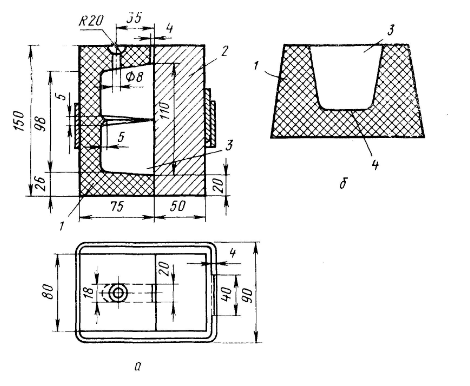
а – клин на отбел;
б – проба для определения твердости;
1 – стержень;
2 – металлическая пластина;
3 – проба;
4 – место замера твердости
Контроль температуры жидкого чугуна производится при помощи оптических пирометров и термопар погружения. Точность измерения температуры оптическим пирометром низкая (±28 градусов). Кроме того, яркостная температура ниже истинной, т.е. замеряемой термопарой погружения. Тем не менее, в цехах практически очень часто пользуются пирометрами. Это позволяет в идентичных условиях работы иметь сравнительные данные по температуре чугуна.
7. Получение серого чугуна с пластинчатым графитом
Получение серого чугуна базируется на использовании качественных шихтовых материалов, применении электроплавки на заключительной стадии получения жидкого чугуна, контроле процесса на всех этапах с оперативным воздействием на него и внепечной обработке чугуна.
Качество шихтовых материалов особенно важно при ваграночной плавке: мелкая и тем более окисленная шихта не может быть основой качественного чугуна, в то же время чрезмерно крупные куски чугуна или стального лома также недопустимы, так как они не расплавляются в зоне плавления, доходят до фурм и нарушают ход ваграночного процесса.
Применение электроплавки – основа получения высококачественного чугуна, так как в этом случае значительно расширяются возможности достижения требуемой температуры чугуна, доводки его по химическому составу, включая введение различных добавок, улучшающих и стабилизирующих его свойства.
На заключительной стадии получения готового жидкого сплава наиболее важной является внепечная обработка жидкого чугуна, т.е. обработка чугуна дополнительно вводимыми веществами (модификаторами и другими добавками), или обработка методами внешнего воздействия.
Обработка чугуна модификаторами и другими добавками получила широкое распространение в литейном производстве благодаря своей простоте и высокой эффективности. В настоящее время разработано много различных модификаторов. Наибольшее распространение как модификатор в производстве отливок из серого чугуна получил ферросилиций, введение которого позволяет получить чугун с мелкозернистой структурой, уменьшает отбел и улучшает механические свойства чугуна. Наиболее эффективно отбел снимается смесями алюминия и ферросилиция, алюминия и графита. Модификаторы, содержащие РЗМ, также эффективно снижают отбел, но до определенного предела их расхода, при введении более 0,2 % отбел начинает увеличиваться. Введение некоторых элементов даже в весьма малых количествах оказывает значительное влияние на формирование структуры и свойства чугуна. Все модификаторы увеличивают предел прочности при растяжении (σ