Файл: Отчёт по итогам практики по профилю специальности 22. 02. 06 Сварочное производство.docx
Добавлен: 22.11.2023
Просмотров: 451
Скачиваний: 20
ВНИМАНИЕ! Если данный файл нарушает Ваши авторские права, то обязательно сообщите нам.
Установки, предназначенные для использования с проволоками сплошного сечения диаметром до 1,2 мм применяются в основном для сварки в углекислом газе корневого слоя с обратным формированием. Установки имеют сложную осциллограмму напряжения и тока дуги. Использование металлопорошковых проволок требует проведения серьезных технологических исследований. Наиболее известным представителем является инверторный источник INVERTEC STT2 фирмы LINCOLN ELECTRIC.
4.3 Подбор вспомогательного (технологического) оборудования
Подбор технологического оборудования производится с учетом требований по технологичности сварной конструкции и их габаритных размеров. Так, для установки сварных цилиндрических конструкций (по типу труб и пр.) применяются: ложементы, роликоопоры, роликовые вращатели, кантователи и сварочные горизонтальные/с наклонной планшайбой вращатели.
Для балочных и рамных конструкций подходит такое технологическое оборудование – кантователь, который позволяет поворачивать изделие в процессе сварки.
Для малогабаритных конструкций разного типа применяют сборочные столы с сопутствующим оборудованием: струбцины, пальцы, упоры и т.д.
4.4 Паспортные данные и технические характеристик сварочного оборудования
Полуавтомат ESAB C340 PRO
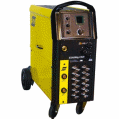
Рис. 3 - Полуавтомат ESAB C340 PRO
Используем его для сборки и прихватки изделия
Применяют для сварки низкоуглеродистых и низколегированных сталей плавящимся электродом в среде углекислого газа.
Комплектуют подающим устройством на тележке, сварочной горелкой, шкафом управления.
Технические характеристики сварочного полуавтомата ESAB C340 PRO, приведены в таблице 5.
Таблица 9 - Технические данные полуавтомата ESAB C340 PRO
Номинальный сварочный ток, А | 340 |
Продолжительность работы | 30% |
Пределы регулирования сварочного тока, А | 40-340 |
Пределы регулирования рабочего напряжения, В | 16-40 |
Диаметр электродной проволоки, мм | 0,6-1,2 |
Скорость подачи электродной проволоки, м/ч | 1,9-20 |
Длина гибкого шланга, м | 5 |
Масса, кг | 120 |
Тип охлаждения сварочной горелки | самоохлаждаемая |
Расход охлаждающей воды, л/ч | - |
Расход защитного газа (углекислый газ), л/ч | - |
Сварочный аппарат MIG 200 PRO (N220).
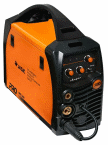
Рис. 4 - Сварочный аппарат MIG 200 PRO
Заводские данные о товаре
Бренд
Сварог
Модель
MIG 200 PRO (N220)
Артикул производителя
92563
Код товара
100023199299
Основные характеристики
Max ток, А
200
Min ток, А
10
MMA сварка
Да
Max мощность, кВт 9.1
Режим сварки
с газом
Min диаметр проволоки, мм
0.6
Max диаметр проволоки, мм
1
ПВ на максимальном токе, %
60
Комплектность
Комплект поставки
горелка
Кейс
Нет
Дополнительные характеристики
Напряжение, В
380
Функции
сварка порошковой проволокой
Степень защиты, IP
ip21s
Наличие сетевой вилки
Нет
Количество подающих роликов
4
Разъем горелки
EURO
Тип горелки
съемная
Габариты
Высота, мм
315
Длина, мм
470
Ширина, мм
190
Вес, кг
13.3
5. Определение режимов сварки
5.1 Выбор режимов полуавтоматической сварки в зависимости от сварочной конструкции
Режимы сварки при полуавтоматической и ручной дуговой сварке выбираются по толщине свариваемого металла на основании специально разработанных расчетных формул, либо из справочных данных, либо «на звук» (для п/а), «по характеру горения дуги» (для РДС).
Расчётные формулы для выбора режимов сварки:
Допустим, нужно сварить 2 листа марки Ст3сп, толщиной 8 мм, в нижнем положении:
-
При полуавтоматической сварке:
Выбираю проволоку диаметром 1,6 мм для двух проходов:
Iсв = = ≈ 241 А
Uд = = = 29 В
νсв = = ≈ 17 м/ч
νпп = = ≈ 209 м/ч
Qр = 18-20 л/мин (справочная информация).
6. Необходимость проведения термической обработки сварных конструкций.
6.1 Группы свариваемости сталей в зависимости от содержания углерода и легирующих элементов (эквивалент углерода)
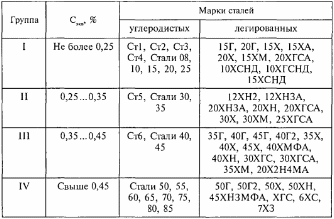
6.2 Виды термической обработки сварных соединений и их назначение
-
После термического отдыха уменьшается остаточное напряжение и количество водорода внутри шва. Процесс проводят при температуре до 300⁰C с выдержкой в течение 1,5 — 2 часов. Этим способом обрабатывают сварные соединения на толстостенных конструкциях, когда нет возможности применить другие виды. -
Отпуском за счет разрушения закалочных структур добиваются уменьшения напряжения на 90%, увеличения пластичности и стойкости к ударным нагрузкам. Нагрев до 600 — 700⁰C, выдержка до 3 часов. Метод применяют на перлитных сталях. -
Нормализацию выполняют при 800⁰C с выдержкой 20 — 40 минут на тонкостенных деталях. После завершения процесса структура становится мелкозернистой и однородной. -
Аустенизацию проводят на высоколегированных видах стали для снятия напряжений и восстановления пластичности. Нагрев до 1100⁰C, двухчасовая выдержка с последующим естественным охлаждением. -
Для отжига после сварки термообработку выполняют при 970⁰C с выдержкой в течение 3 часов и остыванием в естественных условиях. Используют при работе с высоколегированными сталями для улучшения стойкости к коррозии.
6.3 Необходимость сопутствующего или предварительного подогрева
Предварительный и сопутствующий подогрев
Сопутствующее принудительное охлаждение являются технологическими способами регулирования параметров термического цикла, а, следовательно, структуры, механических характеристик и коррозионной стойкости сварных соединений. Процесс термической обработки связан с изменением структурного и напряженного состояния металла, что способствует стабилизации и восстановлению свойств металла, повышению работоспособности конструктивных элементов.
Предварительный и сопутствующий подогрев, дающий положительные результаты при сварке сталей перлитного класса, применительно к аустенитным сталям в ряде случаев не дает (с точки зрения снижения склонности к образованию горячих трещин) заметного эффекта, а скорее сказывается отрицательно вследствие расширения зоны пластического деформирования основного материала или нижележащих валиков металла шва и, как следствие, усиливает действие этого фактора.
7. Неразрушающий метод контроля
7.1 Контроль ВИК, работа с шаблоном сварщика (УШС-3)
Стандартизированный инструмент входит в набор контроллеров для визуального метода исследования сварных соединений. Универсальным шаблоном сварщика 3 проверяют до 11 параметров, контролируют положение заготовок (определяют зазор, сдвиг деталей относительно линии горизонта), подготовку к сварке (измеряют скос кромок).
У сварного шва контролируют:
-
размер дефектов (глубину) и стыкового усиления; -
основные параметры шовного валика (выпуклость и вогнутость), притупление; -
подрез основания шва (несовпадение катета запланированному положению).
Диапазон измерений – по углам до 45°, по ширине и глубине до 50 мм.
7.2 Рентгеновский контроль, ультразвуковой контроль. Назначение и сущность гидроиспытаний закрытых ёмкостей
Ультразвуковая диагностика основывается на том, что колебания с высокой частотой (примерно 20 тысяч Гц) способны проникать в металл и отражаться от дефектов. Узконаправленная волна, создаваемая дефектоскопом, проходит сквозь проверяемое изделие. При наличии дефекта она распространяется с отклонениями, которые можно зафиксировать на экране прибора. Показания, полученные в ходе УЗК, позволяют узнать информацию о характере выявленного дефекта. Например: по времени прохождения ультразвукового сигнала – измеряется расстояние до неровности; по амплитуде колебания отражённой волны – примерные размеры дефекта.
Рентгенографический контроль основан на поглощении рентгеновских лучей, которое зависит от плотности среды и атомного номера элементов, образующих материал среды. Наличие дефектов приводит к тому, что проходящие через материал лучи ослабляются в различной степени. Регистрируя распределение интенсивности проходящих лучей, можно определить наличие и расположение различных неоднородностей материала.
Гидроиспытание закрытых ёмкостей
В процессе проверки изделие полностью заполняется водой, важно обеспечить отток воздуха из заполняемых водой полостей (при наличии воздуха в процессе дальнейших испытаний избыточным давлением изделие может попросту лопнуть, и не обязательно по сварочному шву). Заполнение жидкостью производится при помощи насосов, которые могут плавно увеличивать давление в системе. Желательно наличие у этого оборудования реверсивных возможностей для быстрого удаления воды из изделий при необходимости. Когда система полностью заполнена, производится дополнительная накачка воды с целью создания избыточного давления (обычно не более 2.2 раза от типичных рабочих параметров эксплуатации). В качестве дополнительных проверок запаса прочности часто применяется метод аккуратного постукивания молотком по зоне сварного шва
7.3 Дефекты сварных швов, причины и способы устранения