Добавлен: 23.11.2023
Просмотров: 61
Скачиваний: 3
ВНИМАНИЕ! Если данный файл нарушает Ваши авторские права, то обязательно сообщите нам.
3.3. Сброс с предохранительных клапанов
Оборудование и аппараты по очистке сточной воды и нефти снабжены предохранительными пружинными клапанами (ППК) для предохранения от повышения давления выше заданного значения. Направление сброса ППК указано в таблице № 11. Жидкость из этих аппаратов автоматически откачивается на начало процесса.
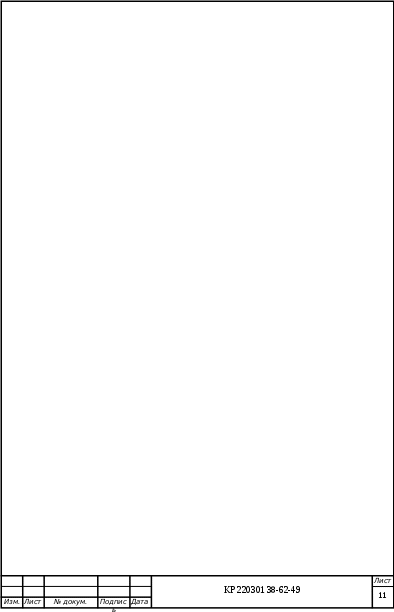
Для подготовки аппаратов и трубопроводов установки к ремонту предусмотрена возможность их опорожнения насосами Н-3, Н-9,10. Остатки нефтепродуктов сливаются в подземные емкости ЕК-100, откуда жидкость откачивается погружными насосами на блок предварительного сброса воды.
3.5. Канализация.
Дождевые стоки с площадок по самотечным сетям поступают в емкость производственно-дождевых стоков ЕД=100м3, оборудованную погружными насосами для перекачки стоков в трубопровод поступления сырья с ДНС-10с на СТХУ. Промышленная канализация предназначена для сбора сальниковых утечек насосов, а также аварийных сбросов с технологического оборудования в ЕК-100. Далее промышленные стоки откачив откачиваются погружными насосами на линию приема сырья в ОПС-1а,2а,3а.
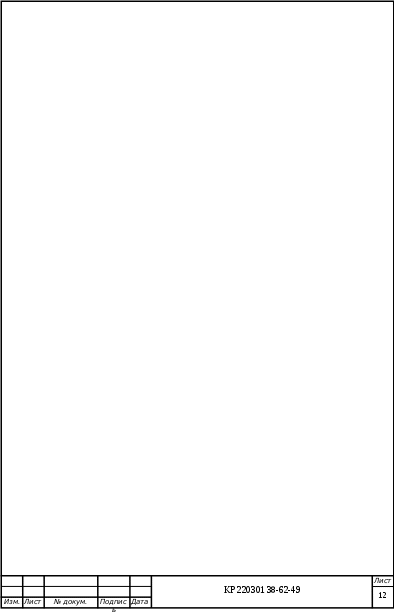
4.1. Иерархическая многоуровневая структура автоматизированной системы контроля и управления
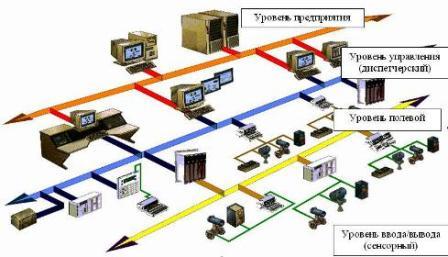
Рис.4.1. Структура комплекса технических средств АСУ ТП
АСУ ТП включают в себя следующие подсистемы, распределенные по уровням управления и контроля:
-
Уровень I (нижний) – - это уровень датчиков, измерительных преобразователей и исполнительных устройств, которые установлены непосредственно на технологическом оборудовании. -
Уровень II (средний) уровень контроллеров . -
Уровень III (верхний) – диспетчерский пункт (ДП) - включает одну или несколько станций управления, представляющих собой автоматизированное рабочее место (АРМ) диспетчера/оператора.

Основными целями и задачами любой автоматизированной системы управления технологическими процессами в общем случае являются:
-
обеспечение безопасности работы технологического оборудования при заданном режиме; -
сработка сигнализации при отклонении от заданных параметров работы технологического оборудования; -
получение информации о параметрах технологического процесса в режиме реального времени.
Задачами автоматизации технологического процесса являются:
-
автоматическое поддержание уровня и давления в технологических аппаратах; -
регулирование расхода водонефтяной эмульсии и промывочной воды; -
подача заданного объема химических реагентов и защита от аварийных режимов.
На нижнем уровне – уровне технологического оборудования – реализуются следующие основные функции:
-
сбор и обработка сигналов с датчиков; -
автоматическое регулирование параметров технологического процесса и оборудования;
-
программно-логическое управление;
-
передача информации на верхний уровень и получение команд и данных с верхнего уровня.
На верхнем уровне – уровне автоматизированных рабочих мест – реализуются следующие функции:
-
формирование и отображение оперативной информации о текущих значениях параметров, состоянии оборудования и исполнительных устройств; -
предупредительная и предаварийная сигнализация, тренды; -
дистанционное управление технологическим оборудованием и ИУ; -
управление работой контуров регулирования; -
ведение базы данных, архивов нарушений, событий, действий оператора, технологического журнала;
диагностика состояния технических средств и электрических цепей.
4.3. Состав комплекса технических средств АСУТП
Для поддержания работы технологического процессов в СТХУ необходимо постоянно отслеживать технологические параметры, такие как уровень, расход, давление, температура. Для этого в используется комплекс технических средств – датчиков, измерительных преобразователей, устройств связи, контроллеров, и технических средств высших уровней. Все показания с приборов нижнего уровня с помощью дистанционной передачи по каналам связи передаются в операторную . Рассмотрим перечень приборов, установленных на технологических объектах СТХУ.
Таблица 4.1
Тип | Назначение | Принцип действия |
Метран-49 | Уровень и межфазный уровень | Предназначен для работы в системах автоматического контроля, регулирования, управления технологическими процессами и обеспечивают непрерывное преобразование в унифицированный аналоговый токовый выходной сигнал и/или цифровой сигнал в стандарте протокола HART. |
Вега | Уровень | Передает сигнал устройству фомирования сигнала для дальнейшей обработки. |
Амперметр | ![]() | Действия магнитоэлектрического прибора основан на создании крутящего момента, благодаря взаимодействию между полем постоянного магнита и током, который проходит через обмотку рамки. С рамкой соединена стрелка, которая перемещается по шкале. Угол поворота стрелки пропорционален силе тока. |
Метран-253 | Температура на выходе | Предназначены для измерения температуры жидких и газообразных химически неагрессивных сред, а также агрессивных, не разрушающих материал защитной арматуры во взрывоопасных зонах и помещениях, в которых могут содержаться аммиак, азотоводородная смесь, углекислый или природный газы. |
Альбатрос | Взлив | Предназначены для измерения относительного и абсолютного давлений газов, паров и жидкостей; преобразователи давления |
РОС 101 | Уровень | Датчики-реле предназначены для контроля уровня электропроводных и неэлектропроводных жидкостей, твёрдых сред, зерна и продуктов его размола, а также раздела сред: вода — светлые нефтепродукты, сжиженные углеводородные газы — вода и других жидкостей с резко отличающимися диэлектрическими проницаемостями в стационарных и корабельных условиях. |
Датчик ДЗК | Проверка загазованности | предназначены для непрерывного измерения концентрации горючих газов (с калибровкой по метану) или концентрации сероводорода на уровне ПДК (предельная допустимая концентрация) в воздухе рабочей зоны. |
Трансформатор тока | межфазный уровень | Первичная обмотка трансформатора тока включается последовательно в цепь с измеряемым переменным током, а во вторичную включаются измерительные приборы. Ток, протекающий по вторичной обмотке трансформатора тока, пропорционален току, протекающему в его первичной обмотке. |
ГАММА-8М | управления технологическим оборудованием | обеспечивает дистанционный контроль состояния и выполняет функции управления технологическим оборудованием, устанавливается непосредственно на технологическом объекте. |
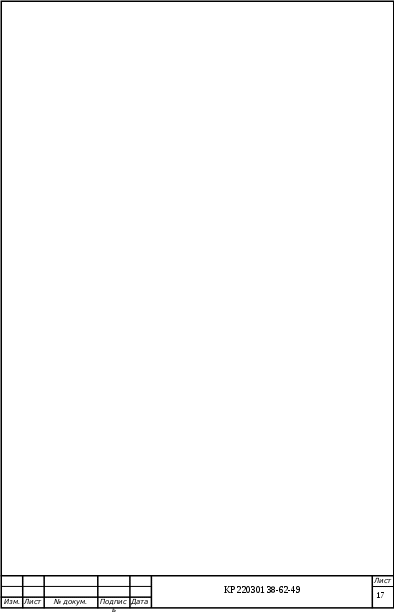
Состав программных средств САУ СТХУ
ПО САУ СТХУ состоит из:
-
ПО АРМ диспетчера; -
ПО АРМ оператора; -
ПО блок автоматики; -
ПО системы контроля загазованности.
ПО АРМ диспетчера построено на основе операционной системы Windows XP Home Edition SP1 и работающего под её управлением пакета HMI-client FlexView 3.1.1, предоставляющего интерфейс диспетчера.
ПО АРМ оператора построено на основе операционной системы QNX v4.2xx и работающего под её управлением SCADA – пакетом , выполняет заданный проектом алгоритм и прямого интерфейса с оператором не имеет.
SCADA – пакет адаптирован для проекта автоматизации технологических объектов ТХУ и установлен на компьютере АРМ оператора ТХУ. На основе технологических схем разработаны мнемосхемы объектов контроля и управления. В базе данных описаны параметры телеизмерений, телесигнализаций и телеуправления с указанием предупредительных и аварийных уставок, классов тревог.
ПО системы контроля загазованности состоит из ПО датчиков загазованности ДЗК-03, ПО управляющего контроллера МКСА-04, сервисного ПО.
-
Архитектура FlexView
FlexView устанавливается на клиентские места для работы с SCADA RealFlex.
FlexView - это программное обеспечение отображения информации на интерфейсе компьютера пользователя в операционной системе Windows.
-
HMI SCADA для всех серверов -
Консоль оператора -
Отображение информации SCADA -
Контроль за системой -
Подключение к-
RealFlex 4 Использование FlexServ -
RealFlex 6 -
FlexWin
-
Комплект компонентов
FlexView - HMI
FlexBuilder - Показать Builder
FlexGallery - библиотека символов
FlexLanguage - Поддержка нескольких языков.
HMI - интерфейс пользователя с повышенной безопасностью
-
Безопасные связи -
Один порт для удобной настройки брандмауэра -
Аппаратный ключ и динамического шифрования -
Вход подключенных пользователей -
Повышенная безопасность
-
Группы -
Политики для групп -
Пользователи - назначить группу -
Сложные пароли -
Жизни для паролей
FlexView устанавливается на клиентские места для работы с SCADA RealFlex.
FlexView - это программное обеспечение отображения информации на интерфейсе компьютера пользователя в операционной системе Windows.
-
HMI SCADA для всех серверов -
Консоль оператора -
Отображение информации SCADA -
Контроль за системой
HMI - интерфейс пользователя с повышенной безопасностью
-
Безопасные связи -
Один порт для удобной настройки брандмауэра -
Аппаратный ключ и динамического шифрования -
Вход подключенных пользователей -
Повышенная безопасность
-
Группы -
Политики для групп -
Пользователи - назначить группу -
Сложные пароли -
Жизни для паролей
FlexView Время для RealWin (FVRW300)
FlexView является HMI клиент для сервера RealWin SCADA. Это позволяет пользователю просматривать все живое и исторических данных, а также позволяет управлять процессом для зарегистрированных пользователей. Динамика имеются такие, как веб-ссылки, калибровочные и управления веб-камерой, а также телеметрии редактор для водителей.
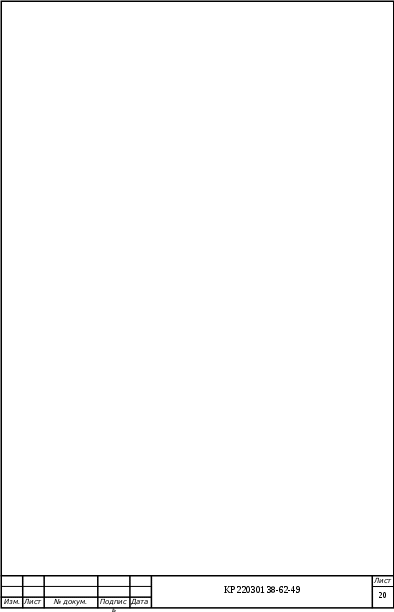
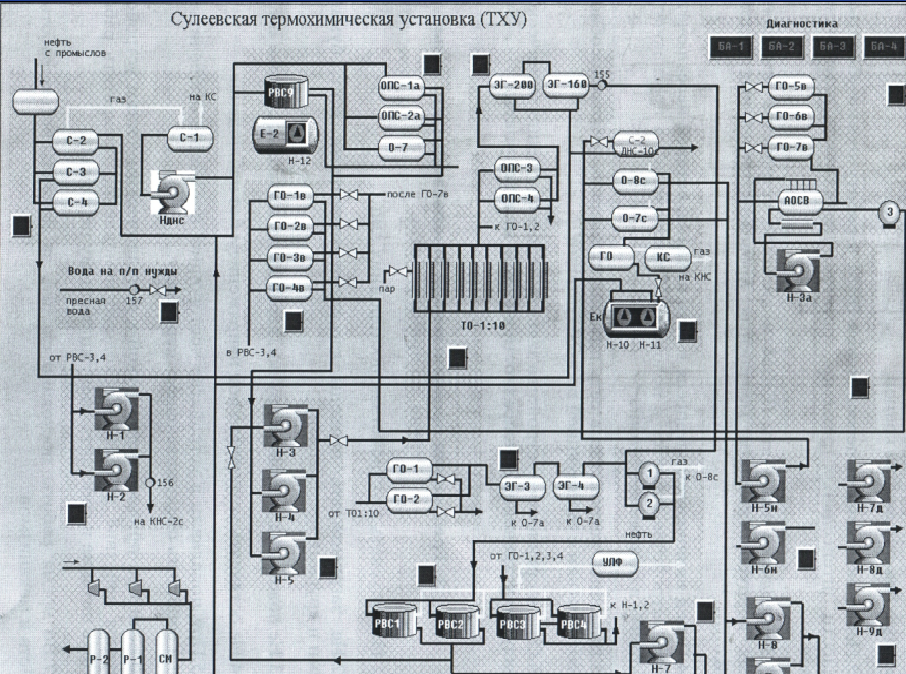
рис. 4.2. Окно визуализации площадки
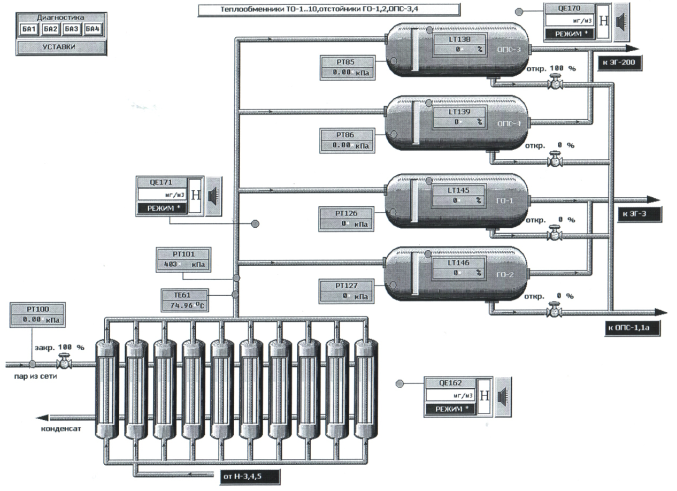
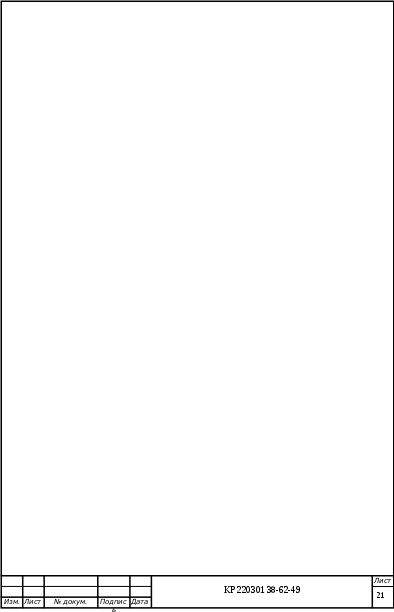
Автоматизация классифицируется на следующие основные виды: управление, контроль, сигнализация, блокировка, защиты и регулирование.
Управление — это совокупность действий, направленных на поддержание функционирования объекта в соответствии с заданной программой, выполняемых на основе определенной информации о значениях параметров управляемого процесса (приведенное определение термина «управление» имеет в основном технический смысл применительно к изучаемому предмету).
Любой процесс управления в каждый момент времени характеризуется одним или несколькими показателями, которые отражают физическое состояние управляемого объекта (температура, скорость, давление, электрическое напряжение, ток, электромагнитное поле и т. д.). Эти показатели в процессе управления должны изменяться по какому-либо закону или оставаться неизменными при изменении внешних условий и режимов работы управляемого устройства. Такие показатели называются параметрами управляемого процесса.