Файл: Курсовой проект кптм51152022 2022 Министерство образования и молодёжной политики Свердловской области.docx
ВУЗ: Не указан
Категория: Не указан
Дисциплина: Не указана
Добавлен: 23.11.2023
Просмотров: 111
Скачиваний: 1
ВНИМАНИЕ! Если данный файл нарушает Ваши авторские права, то обязательно сообщите нам.
Сверлильный станок 2Р135Ф2 применяют при обработке корпусных деталей и деталей типа «фланец», «крышка», «плита», «рычаг», «кронштейн».
Электросхема и ЧПУ позволяют осуществить на станке следующие технологические операции:
-
Сверление; -
Подрезка торца (цекование); -
Расточка; -
Нарезание резьб; -
Глубокое сверление; -
Фрезерование.
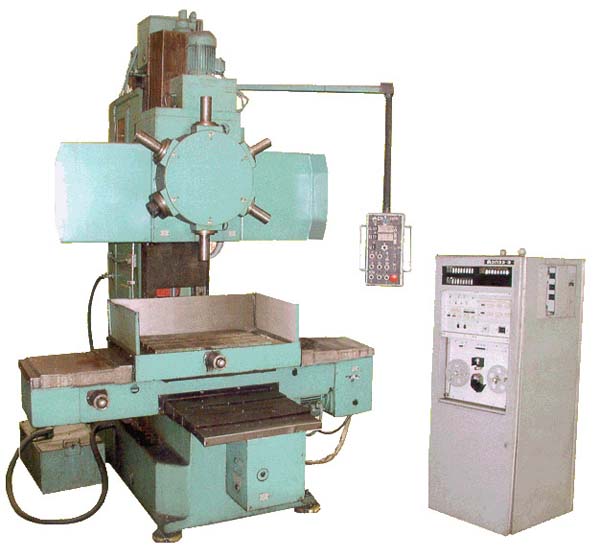
Рисунок 2.9. - Вертикально – сверлильный станок 2Р135Ф2
Таблица 2.5 - Технические характеристики вертикально – сверлильного станка 2Р135Ф3
Основные параметры станка | |
Наибольший диаметр сверления в стали 45, мм | 35 |
Наибольший диаметр нарезаемой резьбы в стали 45, мм | М24 |
Наименьшее и наибольшее расстояние от торца шпинделя до поверхности стола, мм | 40..600 |
Расстояние от оси вертикального шпинделя до направляющих стойки (вылет), мм | 450 |
Наибольший диаметр фрезы, мм | 100 |
Наибольшая глубина фрезерования, мм | 2 |
Наибольшая ширина фрезерования, мм | 60 |
Продольное перемещение стола по направляющим салазок (Ось Х), мм | 630 |
Поперечное перемещение салазок по направляющим станины по программе (Ось Y), мм | 360 |
Наибольшее перемещение шпиндельной бабки по программе (ось Z), мм | 560 |
Суппорт. Шпиндельная бабка. Шпиндель | |
Частота вращения шпинделя, об/мин | 45..2000 31..1400 |
Количество скоростей шпинделя | 12 |
Скорость быстрого перемещения суппорта (шпиндельной бабки), м/мин | 4 |
Количество подач суппорта по оси Z, мм | 18 |
Подачи суппорта, мм | 10..500 |
Наибольший допустимый крутящий момент, Нм | 200 |
Конус шпинделя | |
Рабочий стол | |
Размеры рабочей поверхности стола, мм | 400 х 710 |
Максимальная нагрузка на стол (по центру), кг | |
Число Т-образных пазов Размеры Т-образных пазов | 3 |
Скорость быстрого перемещения стола и салазок, м/мин | 7 |
Скорость подачи стола и салазок при фрезеровании, м/мин | 0,22 |
Минимальная скорость перемещения стола, м/мин | 0,05 |
Точность позиционирования стола и салазок на длине хода, мм | 0,05 |
Система ЧПУ 2П32-3 | |
Число управляемых координат | 3 |
Число одновременно управляемых координат | 2 |
Дискретность задания перемещения стола, салазок и суппорта, мм | 0,01 |
Электрооборудование, привод | |
Электродвигатель привода главного движения, кВт | 3,7 |
Электродвигатель привода перемещения шпиндельной бабки (суппорта), кВт | 1,3 |
Электродвигатель привода перемещения салазок и стола, кВт | 1,1 |
Электродвигатель привода вращения револьверной головки, кВт | 0,75 |
Электронасос охлаждающей жидкости Х14-22М, кВт | 0,125 |
Габарит станка | |
Габариты станка, мм | 1800 х 2170 х 2700 |
Масса станка, кг | 5390 |
025 Термообработка (подумать над перемещением в ТП)
Установка индукционного нагрева TIS 100/ALC-HPH-1000 предназначена для поверхностного упрочнения изделий с нагревом поверхностного слоя металла выше критических температур в результате образования вихревых токов, индуцируемых высокочастотным электромагнитным полем индуктора, с последующим охлаждением. Установка индукционного нагрева представлена на рисунке 2.9.
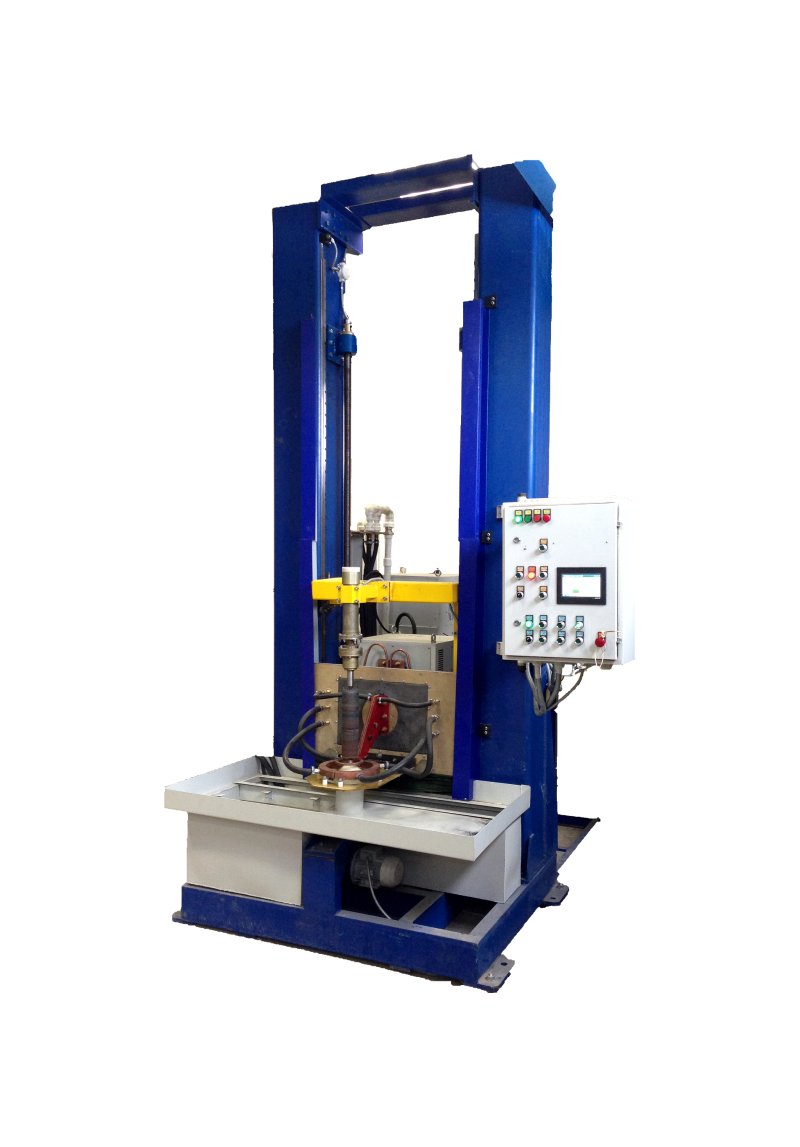
Рисунок 2.10 Установка индукционного нагрева TIS 100/ALC-HPH-1000
Оборудование имеет съёмные панели для обеспечения доступа ко всем узлам и механизмам оборудования, в том числе преобразователя, нагревательного поста и системы сперейерирования и других, с целью их ремонта.
Конструкция закалочного механизма выполнена на несущих колоннах профильной конструкции.
Колонны объединены в два блока: блок перемещения поста и блок зажима изделия. Оба блока крепятся к общей раме и имеют регулировки для обеспечения сносности между обрабатываемым изделием и индуктором.
Фиксация изделия осуществляется верхним подвижным центром, который имеет свои направляющие и привод с редуктором.
Для облегчения работы оператора управление верхним центром вынесено на переносной кнопочный пульт. В случае, если для обработки изделия не требуется верхний центр, он может быть отведен в крайнее верхнее положение.
Для обеспечения строгой сносности индуктора и обрабатываемого изделия типа вала на всей протяженности процесса закалки в конструкции механизма применены профильные рельсовые направляющие. Закалочный механизм позволяет производить закалку изделий, как в ручном, так и автоматическом режиме, по заранее отрегулированным зонам закалки.
Автоматический режим работы комплекса позволяет получать повторяемость процесса закалки серий однотипных изделий, имеющих несколько зон закалки, с высокой точностью. Оператор имеет возможность задавать до трёх различных зон закалки. При этом, в конструкции применен оптический энкодер с целью исключения большего количества концевых выключателей, обозначающих зоны регулировки.
Кроме этого, реализована возможность закалки шестерен, в том числе в масло, внутренних и наружных поверхностей деталей. При этом нижний центр заменяется на план шайбу, универсальную или подготовленную специально для конкретного типа деталей.
Ручной режим работы обеспечивает возможность производить закалку единичных и нестандартных изделий.
Логическая часть установки построена на базе промышленного контроллера.
Плавность регулировок вращения изделия и перемещения индуктора обеспечивается двумя частотно-асинхронными приводами.
Пульт управления имеет как светодиодную индикацию режимов установки, так и цветной жидкокристаллический монитор с сенсорным экраном.
Технические характеристики установки приведены в таблице 2.7.
Таблица 2.6. Технические характеристики TIS 100/ALC-HPH-1000
Модель | TIS 100/ALC-HPH-1000 |
Параметры питающей сети | 380/220В, 50Гц |
Максимально установленная мощность | 100 кВатт |
Частота преобразования | 4-50 кГц |
Максимальный диаметр деталей | 300 мм |
Максимальная длина деталей | 1000 мм |
Масса закаливаемых деталей, не более | 1000 кг |
Скорость вертикального перемещения индуктора относительно детали | 1…20 мм/сек |
Частота вращения деталей | 50…300 об/мин |
Производительно насоса закалочной среды | не более 2,5 м3/ч |
Производительность насоса для охлаждения TIS | 0,5 м3/ч |
030 Круглошлифовальная
OKAMOTO 350 NCAGB прецизионный станок, оснащенный системой ЧПУ Fanuc 21iТ (одновременное управление по двум координатам) изображен на рисунке 2.7. Ось шлифовального круга расположена под углом к оси заготовки. Автоматическая правка и профилирование шлифовального круга по программе с коррекцией позиции. Встроенная интерактивная система программирования. Технические характеристики круглошлифовального станка с ЧПУ OKAMOTO 350 NCAGB приведены в таблице 2.7
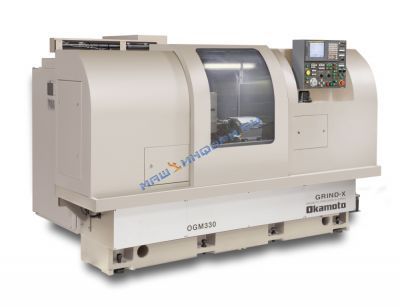
Рисунок 2.11 – Круглошлифовальный станок OKAMOTO 350 NCAGB
Таблица 2.7 - Технические характеристики круглошлифовального станка
OKAMOTO 350 NCAGB
Вместимость | |
Высота центров, мм | 320 |
Расстояние между центрами, мм | 500 |
Макс. шлифуемый диаметр, мм | 300 |
Макс. масса между центрами, кг | 150 в центрах / 40 в патроне |
Шлифовальный круг | |
Размеры, мм | Ø510×75 x Ø203,2 |
Скорость вращения (шкив), об/мин | 1685 / 2247 |
Макс. скорость шлифования, м/с | 45 |
Шлифовальная бабка | |
Макс. поперечное перемещение, мм | 300 |
Угол разворота, град | 30 (постоянный) |
Минимальная команда, мм | 0,0001 |
Постоянная подача, мм/мин | 0 10000 |
Ускоренная подача мм/мин | 10000 |
Стол | |
Макс. продольное перемещение, мм | 800 |
Диапазон разворота, град | не поворачивается |
Минимальная команда, мм | 0,0001 |
Постоянная подача, мм/мин | 010000 |
Ускоренная подача, мм/мин | 10000 |
Передняя бабка | |
Тип шпинделя | Режим неподвижного и свободного шпинделя |
Центр | Конус Морзе № 4 |
Внутренний диаметр шпинделя, мм | 20 |
Скорость вращения, об/мин | 10500 |
Диапазон разворота, град | Не поворачивается |
Задняя бабка | |
Ход шпинделя, мм | 30 |
Центр | Конус Морзе № 4 |
Двигатели | |
Шлифовальный шпиндель, кВт | 7,5 |
Шпиндель передней бабки, кВт | 0,75 (двигатель переменного тока) |
Подача стола, кВт | 2,1 (двигатель переменного тока) |
Подача шлифовальной бабки, кВт | 2,1 (двигатель переменного тока) |
Емкость | |
Смазка, л | 3 |
СОЖ, л | 120 |
Масса, кг | |
Вес, кг | 4500 |
- 1 2 3 4 5