Добавлен: 23.11.2023
Просмотров: 77
Скачиваний: 2
ВНИМАНИЕ! Если данный файл нарушает Ваши авторские права, то обязательно сообщите нам.
1.4. Выбор исходной заготовки
1. Исходя из типа подшипника, определяется и технология его производства, которая часто бывает весьма различной. Рассмотрим стадии изготовления наиболее распространенного типа подшипника – шарикового однорядного радиального подшипника основного конструктивного исполнения. Изготовление колец подшипника: 1. Производство исходной заготовки по заданному диаметру подшипника (металлической трубы или прута (рис. 7)).
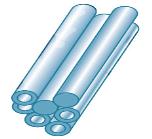
Рис.7. Металлическая труба (исходная заготовка)
2. Обработка давлением и вальцевание исходной заготовки (металлической трубы или прута). Вальцевание представляет собой плющение и сдавливание исходного слоя для придания ему большей плотности, гладкости и равномерной толщины. Происходит это посредством пропуска заготовки между двумя вращающимися валами (отсюда термин – вальцевание).
3. Токарная обработка заготовки – нарезка из заготовок отдельных колец и обработка всех поверхностей с целью придания будущему кольцу подшипника нужных диаметров (внешнего и внутреннего) и ширины.
4. Термическая обработка колец подшипника – закалка (нагрев до температуры 850 градусов Цельсия и быстрое охлаждение в жидкости) и отпуск (содержание колец при температуре 170 градусов).
5. Шлифовка поверхностей колец подшипника – внешние и внутренние и боковые стороны. Шлифовка дорожек качения на внутреннем и внешнем кольцах подшипника.
6. Суперфиниширование – Шлифование дорожек качения до окончательной степени гладкости (зависимости от требований к их шероховатости – обозначается в номере подшипника литерой У, У1, У2).
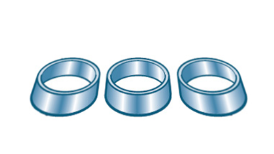
Рис.8. Кольца, полученные из заготовки
Изготовление тел качения подшипника (шарики):
1. Нарезка исходных заготовок из специальной стальной проволоки заданных размеров в зависимости от диаметра тел качения.
2. Сдавливание предварительных заготовок и придание им шарообразной формы вплоть до размеров близких к окончательным – с разницей до 100 микрон.
3. Термическая обработка тел качения – закаливание, охлаждение и отпуск.
4. Шлифовка тел качения, придание им окончательных размеров и последующая полировка.
Изготовление сепаратора 1. Пробивка исходной заготовки (стального листа определенной ширины и толщины) под отверстия для тел качения (шариков).
2. Штамповка предварительного сепаратора – придание отверстиям и профилю сепаратора необходимой формы.
3. Сверление отверстий под заклепки, с помощью которых кольца сепаратора будут соединены в одно целое.
Сборка подшипника из готовых деталей. Подшипники собираются следующим образом – внутреннее кольцо укладывается в наружное, между ними укладывается ряд шариков.
Один из краев внутреннего кольца поднимается для возможности укладки всего ряда шариков, а затем подшипник «защелкивается» и тела качения плотно встают на дорожках качения.
С двух сторон заклепками крепится сепаратор (латунный, металлический, полиамидный и т.д.).
Сдача готовых подшипников, их проверка, маркировка, смазка, и комплектация в тару. Проверенные на заводе подшипники отечественного производства легко различаются по темной поверхности внешнего кольца (подшипники проверяются обычно выборочно из партии).
Эксплуатация подшипников:
Необходимо периодически осматривать и обслуживать подшипник и контролировать условия его работы для того, чтобы продлить срок службы подшипника. Обычно применяют следующие методы:
а) Проверка состояния подшипникового узла в рабочем режиме
Для определения срока замены подшипника и интервала добавления смазочного материала, изучите ее свойства, принимая во внимание такие факторы, как рабочая температура, вибрации, шумы подшипников
б) Контроль состояния подшипников
Старайтесь тщательно обследовать подшипник во время периодических осмотров машины и замены неисправных деталей.
Проверьте состояние дорожки качения. Проверьте наличие повреждений.
Подтвердите возможность дальнейшего использования подшипника или необходимость его замены.
Причины поломок и критерии расчёта подшипников
Главная особенность динамики подшипника – знакопеременные нагрузки.
Циклическое перекатывание тел качения может привести к появлению усталостной микротрещины. Постоянно прокатывающиеся тела качения вдавливают в эту микротрещину смазку.
Пульсирующее давление смазки расширяет и расшатывает микротрещину, приводя к усталостному выкрашиванию и в конце концов, к поломке кольца.
Чаще всего ломается внутреннее кольцо, т.к. оно меньше наружного и там, следовательно, выше удельные нагрузки. Усталостное выкрашивание – основной вид выхода из строя подшипников качения.
В подшипниках также возможны статические и динамические перегрузки, разрушающие как кольца, так и тела качения.
Следовательно, при проектировании машины необходимо определить, во-первых, количество оборотов (циклов), которое гарантированно выдержит подшипник, а, во-вторых – максимально допустимую нагрузку, которую выдержит подшипник.
Вывод: работоспособность подшипника сохраняется при соблюдении двух критериев:
Долговечность; Грузоподъёмность.
Глава 2. Практическая часть
2.1. Разработка операций технологического процесса
Изготовление колец подшипника:
1. Производство исходной заготовки по заданному диаметру подшипника
2. Обработка давлением и вальцевание исходной заготовки (металлической трубы или прута). Вальцевание представляет собой плющение и сдавливание исходного слоя для придания ему большей плотности, гладкости и равномерной толщины. Происходит это посредством пропуска заготовки между двумя вращающимися валами (отсюда термин — вальцевание).
3. Токарная обработка заготовки — нарезка из заготовок отдельных колец и обработка всех поверхностей с целью придания будущему кольцу подшипника нужных диаметров (внешнего и внутреннего) и ширины.
4. Термическая обработка колец подшипника — закалка (нагрев до температуры 850 градусов Цельсия и быстрое охлаждение в жидкости) и отпуск (содержание колец при температуре 170 градусов).
5. Шлифовка поверхностей колец подшипника — внешние и внутренние и боковые стороны. Шлифовка дорожек качения на внутреннем и внешнем кольцах подшипника.
6. Суперфиниширование — Шлифование дорожек качения до окончательной степени гладкости
Изготовление тел качения подшипника (шарики):
1. Нарезка исходных заготовок из специальной стальной проволоки заданных размеров в зависимости от диаметра тел качения.
2. Сдавливание предварительных заготовок и придание им шарообразной формы вплоть до размеров близких к окончательным — с разницей до 100 микрон.
3. Термическая обработка тел качения — закаливание, охлаждение и отпуск.
4. Шлифовка тел качения, придание им окончательных размеров и последующая полировка.
Изготовление сепаратора:
1. Пробивка исходной заготовки (стального листа определенной ширины и толщины) под отверстия для тел качения (шариков).
2. Штамповка предварительного сепаратора — придание отверстиям и профилю сепаратора необходимой формы.
3. Сверление отверстий под заклепки, с помощью которых кольца сепаратора будут соединены в одно целое.
Завершительным этапом является сборка подшипника.
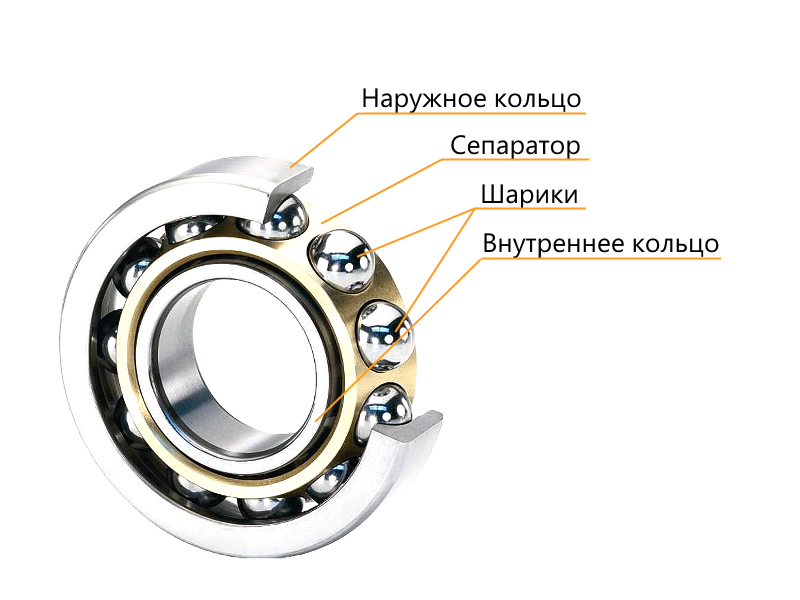
Рис.9. Строение подшипника.
2.2. Расчет технического нормирования операции
Подобрать подшипник качения для вала редуктора с цапфой d = 40 мм.
Проверить долговечность при частоте вращения
n = 1000 об/мин; радиальная нагрузка Fr= 2500 Н, осевая нагрузка Fa= 0, Lhmin = 10000 час, рабочая температура подшипника 100оС
Дано:
d = 40 мм
n = 1000 об/мин
1) Fr= 2500 H
2) Fa= 0
3) Lh min= 10000час
Решение:
Для заданных условий (вал редуктора) выберем подшипник радиальный однорядный шариковый.
Проверим подшипник для посадочного диаметра d = 40 мм, начиная с легкой серии - № 208, у которого статическая грузоподъемность (см. табл. 3):

динамическая грузоподъемность
С = 32кН = 32000 Н
Примем по таблице 1 коэффициент безопасности Кб = 1,4
и по таблице 2 температурный коэффициент КT = 1
Так как


Х=1, Y=0
V =1 - вращается внутреннее кольцо,
Эквивалентная динамическая нагрузка:

Р = 1*1*2500*1,4*1 = 3500 Н
Расчетный ресурс в миллионах оборотов:

L = (32000/3500)3 =764,2 млн. об.
Расчетная долговечность в часах:

Lh = 764,2*106/ (60*1000) = 12736 час. 1000 час.
Что допустимо, так как минимальная долговечность 10000 час.
Если долговечность получится меньше требуемой нормы, то необходимо проверить подшипник средней серии, если и он не подойдет, то проверяется подшипник тяжелой серии.
Характер нагрузки | Кб | Примеры |
Спокойная без толчков | 1,0 | Ролики ленточных транспортеров |
Легкие толчки. Кратковременные перегрузки до 125%, от расчетной нагрузки | 1,1 - 1,2 | Прецизионные зубчатые передачи, блоки, легкие вентиляторы, воздуходувки |
Умеренные толчки и вибрации. Кратковременные перегрузки до 150% от расчетной нагрузки | 1,3 - 1,5 | Редукторы всех конструкций |
То же в условиях повышенной надежности | 1,6 - 1,8 | Центрифуги и сепараторы, энергетическое оборудование |
Значительные толчки и вибрации. Кратковременные перегрузки до 200% от расчетной нагрузки | 1,9 - 2,4 | Валики среднесортных прокатных станов; дробилки, ковочные машины |
С сильными ударами и кратковременными перегрузками, достигающими 300% от расчетной нагрузки | 2,5 - 3,0 | Тяжелые ковочные машины; валки крупносортных прокатных станов; лесопильные рамы |