Файл: Отчет по практическим работам 16 по дисциплине Материаловедение и технология конструкционных материалов.docx
Добавлен: 30.11.2023
Просмотров: 125
Скачиваний: 2
ВНИМАНИЕ! Если данный файл нарушает Ваши авторские права, то обязательно сообщите нам.
размеров профиля при прессовании выше, шероховатость поверхности меньше. Возможность получения тонкостенных бесшовных труб большого диаметра с малой разностенностью. Возможность обработки давлением металлов и сплавов с пониженной пластичностью (высокопрочные алюминиевые сплавы, бронзы, жаропрочные стали и сплавы и др.). Пластичность при прессовании увеличивается, т.к. металл находится в условиях всестороннего неравномерного сжатия. Возможность высоких степеней деформации (92 % по сечению и более), что обеспечивает высокие механические свойства, в том числе вибропрочность и сопротивление усталости.
Недостатки прессования. Значительный износ инструмента, матриц и особенно игл, из-за больших контактных напряжений и температур, особенно при прессовании никелевых сплавов, сталей и жаропрочных сталей и сплавов. Высокая стоимость инструмента. Неравномерность механических свойств по длине прессованного изделия из-за неравномерности течения металла. Большие технологические отходы, особенно при прессовании труб большого диаметра.
Волочение
Волочение - процесс протягивания обрабатываемой заготовки через постепенно суживающееся отверстие инструмента (волоки). При волочении площадь поперечного сечения уменьшается, приобретая постоянное сечение по всей длине.
Рисунок 4.5 - Схемы волочения: а – волочение проволоки, прутка, сплошного профиля; б – волочение трубы на оправке; 1- заготовка; 2 – волока; 3 – оправка; 4 – обойма (бандаж); P – усилие волочения
Волочение производят, как правило, в условиях холодной деформации. Волочение проволоки из вольфрама, молибдена, нихрома и цинка производят в горячем состоянии. Волочение в ряде случаев применяется для калибровки сортового проката. Для этого производят одну или несколько протяжек, что повышает точность размеров сечения и улучшает качество поверхности.
Ковка
Ковка - процесс обработки давлением, при котором для получения изделия заданных форм и размеров по заготовке наносится ряд последовательных ударов бойками молота или нажимов пресса. Изделие, получаемое ковкой или горячей штамповкой, называют поковкой.
Все оборудование для ковки и штамповки можно разделить на две группы: машины статического действия и машины динамического действия.
К машинам статического действия относятся ковочные гидравлические прессы. Ковочные гидравлические прессы строят с номинальной силой до 200 МН и более. Поковки массой 3...5 Мг и более куют только на гидравлических прессах.
К машинам динамического действия относятся ковочные молоты различных конструкций, с ударной массой от 50 кг до 800 Мг и энергией удара от 0,8 до 200 кДж.
Исходным материалом для ковки служат слитки, прокат и прессованные заготовки.
Основные операции ковки. Осадка – уменьшение высоты заготовки при увеличении ее диаметра (рисунок 4.6, а). Осадку применяют для получения поковок типа «диск»; как предварительную операцию перед прошивкой; при изготовлении пустотелых заготовок; для уничтожения литой дендритной структуры, измельчения зерна. Протяжка – удлинение заготовки или ее части (разгонка) за счет уменьшения ее площади поперечного сечения (4.6, в). Протяжку производят последовательными ударами плоского или вырезного бойка по отдельным участкам заготовки, с подачей последней вдоль оси протяжки и переворотом (при необходимости) на 90°.
Рисунок 4.6 - Основные операции ковки: а – осадка; б – высадка; в – протяжка; г – протяжка с оправкой; д – раскатка на оправке; е – гибка; ж – отрубка; з – прошивка неглубоких полостей; и – прошивка глубоких полостей; к – прошивка сквозных полостей; л - высадка с подкладкой; стрелками указаны направления действия силы ковки
Объемная штамповка
Объемная штамповка - метод обработки, основанный на применении специального инструмента - штампа. Штамп состоит из двух или нескольких частей, которые в сомкнутом состоянии образуют одну или несколько полостей. При сближении частей штампа происходит принудительное перераспределение металла заготовки, в результате чего полость штампа заполняется, получаются заданные формы и размеры поковки.
Горячая штамповка
Горячая штамповка, по сравнению с ковкой, имеет ряд преимуществ: значительно более высокая производительность; стабильность формы и размеров, более высокая точность размеров; возможность получения поковок более сложной формы. Однако для штамповки требуются штампы, имеющие высокую стоимость и ограниченную стойкость. По мере увеличения массы (объема) поковок стоимость штампа увеличивается, а стойкость уменьшается. Исходные материалы для штамповки - стальной прокат в виде прутков (обычно круглого, а также квадратного, прямоугольного и других сечений), блюмсов, труб и профилей переменного сечения (периодический прокат), прессованные прутки и трубы из бронзы, алюминиевых сплавов и других сплавов с пониженной пластичностью. Для штамповки на автоматах и точной горячей штамповки применяют калиброванный прокат.
Технологический процесс горячей штамповки включает: разделку исходных материалов на заготовки, нагрев заготовок, штамповку, первичную термообработку поковок и отделку поковок. В соответствии с этим в штамповочных цехах имеются заготовительное, штамповочное, термическое и отделочное отделения.
Рисунок 4.7 - Открытая штамповка: а, б, в – начальный, промежуточный и конечный моменты штамповки; 1 – нижняя часть штампа; 2 – верхняя часть штампа; 3 – заготовка; 4 – канавка для облоя; 5 – магазин; 6 – промежуточная поковка; 7 – поковка; 8 – облой
Штамповка в закрытых штампах (рисунок 4.8) не предусматривает образование облоя. Практически весь объем заготовки идет на образование поковки. При закрытой штамповке во избежание перегрузки штампа и оборудования (что особенно опасно для машин кривошипного действия) предъявляются жесткие требования к точности равенства объема заготовки и объема полости штампа, на которую влияет множество факторов
Рисунок 4.8 - Закрытая штамповка: 1 - поковка; 2 – выталкиватели
Холодная объемная штамповка
Холодная объемная штамповка (ХОШ) - это способ получения в штампах заготовок и деталей из сортового проката и прессованных прутков, основанный на процессе холодной деформации.
Основные операции ХОШ: высадка открытая и закрытая, выдавливание и вдавливание.
Высадку(рисунок 4.9) применяют для получения ступенчатых деталей с образованием фланцев и других местных утолщений, для набора металла последующей штамповкой. На процессе высадки основано производство крепежных деталей (болтов, винтов, заклепок, гвоздей и т.п.), шаровых пальцев автомобилей и других деталей с шаровой головкой, штуцеров и т.п.
При ХОШ применяют все виды выдавливания: прямое, обратное, поперечное, комбинированное и радиальное (рисунок 4.10).
Рисунок 4.9 - Схемы высадки: а – открытой; б – закрытой.
Рисунок 4.10 - Схема радиального выдавливания
Прямое выдавливание применяется для получения болтов, гаек, ступенчатых валов, деталей со шлицами и продольными канавками. Выдавленная часть может иметь переменное сечение (детали с отростками, бобышками и др.).
При обратном выдавливании внешний и внутренний контуры поперечного сечения штампованной заготовки имеют форму круга или многоугольника или их сочетания. Его для получения гильз, колпачков, стаканов и других полых, трубчатых деталей, а также для получения полых и трубчатых заготовок для прямого и обратного выдавливания, а также для вытяжки при листовой штамповке. Радиальным выдавливанием получают звездочки, шестерни.
ХОШ - один из наиболее прогрессивных методов производства ступенчатых и полых заготовок и деталей из цветных металлов и сплавов, углеродистых и легированных сталей.
ХОШ имеет следующие преимущества: Деформационное упрочнение, отсутствие надрезов волокна, образующихся при обработке резанием, направленность волокна вдоль конфигурации детали, улучшение микрогеометрии поверхности. Благодаря этому повышается сопротивление динамическим нагрузкам и вибропрочность. Переход на холодную объемную штамповку в ряде случаев позволяет использовать менее легированные стали и сплавы.
Основные ограничения процесса на данном уровне развития науки и техники: Низкая стойкость инструмента при штамповке заготовок из сталей и сплавов повышенной прочности. Ограниченность размеров и сложности формы детали. Необходимость применения специальных режимов разупрочняющей термической обработки и нанесения покрытий носителями смазочных материалов, что удлиняет и усложняет цикл производства.
Практическое занятие № 5. Основы обработки резанием
Физико-механические основы обработки материалов резанием
Обработка материалов резанием – это процесс срезания режущим инструментом с поверхности заготовкислоя металла в виде стружки, с целью получения заданной геометрической формы, точности размеров, взаиморасположения и шероховатости поверхности детали.
Резание металлов – это сложный процесс физико-механического взаимодействия режущего клина инструмента, заготовки и окружающей среды.
Главным движением (Dр) называется движение, определяющее скорость деформирования и отделения стружки.
Движением подачи (Ds) называется движение, обеспечивающее непрерывность врезания режущей кромки инструмента в материал заготовки.
При обработке заготовок резанием образуется стружка: сливная, скалывания и надлома.
6.1 Лезвийная обработка деталей машин
В лезвийной обработке (зависимости от вида и направления движений резания, вида обработанной поверхности) можно выделить следующие технологические методы: точение, строгание, сверление, фрезерование, протягивание.
Точение
Точение – лезвийная обработка резанием (ЛОР) цилиндрических и торцевых поверхностей; главное движение – вращательное, придается заготовке или режущему инструменту; движение подачи - прямолинейное или криволинейное, придается режущему инструменту вдоль, перпендикулярно или под углом к оси вращения. Точением обрабатываются шейки и торцевые поверхности круглых стержней (валов); наружные и внутренние цилиндрические поверхности и торцы дисков; внутренние цилиндрические торцевые поверхности некруглых стержней и корпусных деталей.
Недостатки прессования. Значительный износ инструмента, матриц и особенно игл, из-за больших контактных напряжений и температур, особенно при прессовании никелевых сплавов, сталей и жаропрочных сталей и сплавов. Высокая стоимость инструмента. Неравномерность механических свойств по длине прессованного изделия из-за неравномерности течения металла. Большие технологические отходы, особенно при прессовании труб большого диаметра.
Волочение
Волочение - процесс протягивания обрабатываемой заготовки через постепенно суживающееся отверстие инструмента (волоки). При волочении площадь поперечного сечения уменьшается, приобретая постоянное сечение по всей длине.
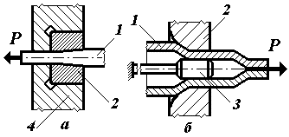
Рисунок 4.5 - Схемы волочения: а – волочение проволоки, прутка, сплошного профиля; б – волочение трубы на оправке; 1- заготовка; 2 – волока; 3 – оправка; 4 – обойма (бандаж); P – усилие волочения
Волочение производят, как правило, в условиях холодной деформации. Волочение проволоки из вольфрама, молибдена, нихрома и цинка производят в горячем состоянии. Волочение в ряде случаев применяется для калибровки сортового проката. Для этого производят одну или несколько протяжек, что повышает точность размеров сечения и улучшает качество поверхности.
Ковка
Ковка - процесс обработки давлением, при котором для получения изделия заданных форм и размеров по заготовке наносится ряд последовательных ударов бойками молота или нажимов пресса. Изделие, получаемое ковкой или горячей штамповкой, называют поковкой.
Все оборудование для ковки и штамповки можно разделить на две группы: машины статического действия и машины динамического действия.
К машинам статического действия относятся ковочные гидравлические прессы. Ковочные гидравлические прессы строят с номинальной силой до 200 МН и более. Поковки массой 3...5 Мг и более куют только на гидравлических прессах.
К машинам динамического действия относятся ковочные молоты различных конструкций, с ударной массой от 50 кг до 800 Мг и энергией удара от 0,8 до 200 кДж.
Исходным материалом для ковки служат слитки, прокат и прессованные заготовки.
Основные операции ковки. Осадка – уменьшение высоты заготовки при увеличении ее диаметра (рисунок 4.6, а). Осадку применяют для получения поковок типа «диск»; как предварительную операцию перед прошивкой; при изготовлении пустотелых заготовок; для уничтожения литой дендритной структуры, измельчения зерна. Протяжка – удлинение заготовки или ее части (разгонка) за счет уменьшения ее площади поперечного сечения (4.6, в). Протяжку производят последовательными ударами плоского или вырезного бойка по отдельным участкам заготовки, с подачей последней вдоль оси протяжки и переворотом (при необходимости) на 90°.
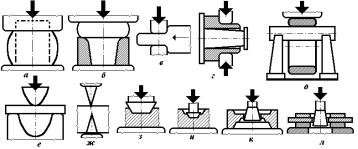
Рисунок 4.6 - Основные операции ковки: а – осадка; б – высадка; в – протяжка; г – протяжка с оправкой; д – раскатка на оправке; е – гибка; ж – отрубка; з – прошивка неглубоких полостей; и – прошивка глубоких полостей; к – прошивка сквозных полостей; л - высадка с подкладкой; стрелками указаны направления действия силы ковки
Объемная штамповка
Объемная штамповка - метод обработки, основанный на применении специального инструмента - штампа. Штамп состоит из двух или нескольких частей, которые в сомкнутом состоянии образуют одну или несколько полостей. При сближении частей штампа происходит принудительное перераспределение металла заготовки, в результате чего полость штампа заполняется, получаются заданные формы и размеры поковки.
Горячая штамповка
Горячая штамповка, по сравнению с ковкой, имеет ряд преимуществ: значительно более высокая производительность; стабильность формы и размеров, более высокая точность размеров; возможность получения поковок более сложной формы. Однако для штамповки требуются штампы, имеющие высокую стоимость и ограниченную стойкость. По мере увеличения массы (объема) поковок стоимость штампа увеличивается, а стойкость уменьшается. Исходные материалы для штамповки - стальной прокат в виде прутков (обычно круглого, а также квадратного, прямоугольного и других сечений), блюмсов, труб и профилей переменного сечения (периодический прокат), прессованные прутки и трубы из бронзы, алюминиевых сплавов и других сплавов с пониженной пластичностью. Для штамповки на автоматах и точной горячей штамповки применяют калиброванный прокат.
Технологический процесс горячей штамповки включает: разделку исходных материалов на заготовки, нагрев заготовок, штамповку, первичную термообработку поковок и отделку поковок. В соответствии с этим в штамповочных цехах имеются заготовительное, штамповочное, термическое и отделочное отделения.
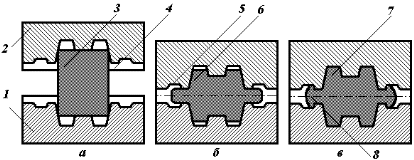
Рисунок 4.7 - Открытая штамповка: а, б, в – начальный, промежуточный и конечный моменты штамповки; 1 – нижняя часть штампа; 2 – верхняя часть штампа; 3 – заготовка; 4 – канавка для облоя; 5 – магазин; 6 – промежуточная поковка; 7 – поковка; 8 – облой
Штамповка в закрытых штампах (рисунок 4.8) не предусматривает образование облоя. Практически весь объем заготовки идет на образование поковки. При закрытой штамповке во избежание перегрузки штампа и оборудования (что особенно опасно для машин кривошипного действия) предъявляются жесткие требования к точности равенства объема заготовки и объема полости штампа, на которую влияет множество факторов
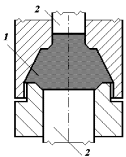
Рисунок 4.8 - Закрытая штамповка: 1 - поковка; 2 – выталкиватели
Холодная объемная штамповка
Холодная объемная штамповка (ХОШ) - это способ получения в штампах заготовок и деталей из сортового проката и прессованных прутков, основанный на процессе холодной деформации.
Основные операции ХОШ: высадка открытая и закрытая, выдавливание и вдавливание.
Высадку(рисунок 4.9) применяют для получения ступенчатых деталей с образованием фланцев и других местных утолщений, для набора металла последующей штамповкой. На процессе высадки основано производство крепежных деталей (болтов, винтов, заклепок, гвоздей и т.п.), шаровых пальцев автомобилей и других деталей с шаровой головкой, штуцеров и т.п.
При ХОШ применяют все виды выдавливания: прямое, обратное, поперечное, комбинированное и радиальное (рисунок 4.10).
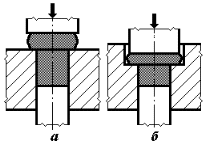
Рисунок 4.9 - Схемы высадки: а – открытой; б – закрытой.
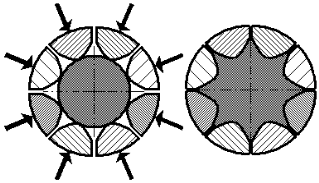
Рисунок 4.10 - Схема радиального выдавливания
Прямое выдавливание применяется для получения болтов, гаек, ступенчатых валов, деталей со шлицами и продольными канавками. Выдавленная часть может иметь переменное сечение (детали с отростками, бобышками и др.).
При обратном выдавливании внешний и внутренний контуры поперечного сечения штампованной заготовки имеют форму круга или многоугольника или их сочетания. Его для получения гильз, колпачков, стаканов и других полых, трубчатых деталей, а также для получения полых и трубчатых заготовок для прямого и обратного выдавливания, а также для вытяжки при листовой штамповке. Радиальным выдавливанием получают звездочки, шестерни.
ХОШ - один из наиболее прогрессивных методов производства ступенчатых и полых заготовок и деталей из цветных металлов и сплавов, углеродистых и легированных сталей.
ХОШ имеет следующие преимущества: Деформационное упрочнение, отсутствие надрезов волокна, образующихся при обработке резанием, направленность волокна вдоль конфигурации детали, улучшение микрогеометрии поверхности. Благодаря этому повышается сопротивление динамическим нагрузкам и вибропрочность. Переход на холодную объемную штамповку в ряде случаев позволяет использовать менее легированные стали и сплавы.
Основные ограничения процесса на данном уровне развития науки и техники: Низкая стойкость инструмента при штамповке заготовок из сталей и сплавов повышенной прочности. Ограниченность размеров и сложности формы детали. Необходимость применения специальных режимов разупрочняющей термической обработки и нанесения покрытий носителями смазочных материалов, что удлиняет и усложняет цикл производства.
Практическое занятие № 5. Основы обработки резанием
Физико-механические основы обработки материалов резанием
Обработка материалов резанием – это процесс срезания режущим инструментом с поверхности заготовкислоя металла в виде стружки, с целью получения заданной геометрической формы, точности размеров, взаиморасположения и шероховатости поверхности детали.
Резание металлов – это сложный процесс физико-механического взаимодействия режущего клина инструмента, заготовки и окружающей среды.
Главным движением (Dр) называется движение, определяющее скорость деформирования и отделения стружки.
Движением подачи (Ds) называется движение, обеспечивающее непрерывность врезания режущей кромки инструмента в материал заготовки.
При обработке заготовок резанием образуется стружка: сливная, скалывания и надлома.
6.1 Лезвийная обработка деталей машин
В лезвийной обработке (зависимости от вида и направления движений резания, вида обработанной поверхности) можно выделить следующие технологические методы: точение, строгание, сверление, фрезерование, протягивание.
Точение
Точение – лезвийная обработка резанием (ЛОР) цилиндрических и торцевых поверхностей; главное движение – вращательное, придается заготовке или режущему инструменту; движение подачи - прямолинейное или криволинейное, придается режущему инструменту вдоль, перпендикулярно или под углом к оси вращения. Точением обрабатываются шейки и торцевые поверхности круглых стержней (валов); наружные и внутренние цилиндрические поверхности и торцы дисков; внутренние цилиндрические торцевые поверхности некруглых стержней и корпусных деталей.