Файл: Розробка методів по монтажу, експлуатації, технічному сервісу обладнання для виготовлення дражованого.doc
ВУЗ: Не указан
Категория: Не указан
Дисциплина: Не указана
Добавлен: 03.12.2023
Просмотров: 32
Скачиваний: 1
ВНИМАНИЕ! Если данный файл нарушает Ваши авторские права, то обязательно сообщите нам.

Знаходимо для кожної з машин кількість середніх, поточних ремонтів та обслуговувань у ремонтному періоді.
Дражувач: Кс=Тц/Тс-1=36/18-1=1;
Кп=Тс/Тп-1=18/3-1=5;
Ко=Тп/То-1=3/1,5-1=1.
Насос : Кс=Тц/Тс-1=12/6-1=1;
Кп=Тс/Тп-1=6/3-1=1;
Ко=Тп/То-1=3/1-1=2.
Бак: Кс=Тц/Тс-1=48/24-1=1;
Кп=Тс/Тп-1=24/12-1=1;
Ко=Тп/То-1=12/1-1=11.
Таблиця 3.4 – Норми часу на ремонтні роботи.
Найменування обладнання | Категорія складності | Норми часу на ремонтні роботи | |||
К | С | П | О | ||
1 | 2 | 3 | 4 | 5 | 6 |
Дражувач | 1,2 | 42,0 | 25,2 | 8,4 | 1,2 |
Насос | 0,17 | 6,0 | 3,6 | 1,2 | 0,17 |
Бак | 0,2 | 7 | 4,2 | 1,4 | 0,2 |
Розрахунок річної трудомісткості роботи ППР:
Дражувач:
Для капітального ремонту: Тк=К*Кк*n=42*0*1=0;
Для середнього ремонту: Тс=С*Кс*n=25,2*1*1=25,2;
Для поточного ремонту: Тп=П*Кп*n=8,4*5*1=42,5;
Для огляду: То=О*Ко*n=1,2*1*1=39,6.
Насос :
Для капітального ремонту: Тк=К*Кк*n=6*1*1=6;
Для середнього ремонту: Тс=С*Кс*n=3,6*1*1=3,6;
Для поточного ремонту: Тп=П*Кп*n=1,2*1*1=1,2;
Для огляду: То=О*Ко*n=0,17*2*1=0,34

Для капітального ремонту: Тк=К*Кк*n=7*0*1=0;
Для середнього ремонту: Тс=С*Кс*n=4,2*1*1=4,2;
Для поточного ремонту: Тп=П*Кп*n=1,4*1*1=1,4;
Для огляду: То=О*Ко*n=0,2*11*1=2,2.
За даними, які одержали в таблиці , будуємо річний графік ППР для обладнання цеху.

Рисунок 3.1 – Річний графік ППР для обладнання цеху.

3.6 РЕМОНТ ДЕТАЛЕЙ ШПОНОЧНИХ І ШЛІЦЕВИХ З'ЄДНАНЬ
У шпоночних з'єднаннях найчастіше зустрічаються наступні види зносу і пошкоджень:
-
пошкодження робочих поверхонь, граней або головок; -
зріз шпонок під дією недопустимих крутних моментів;
3) зминання або викришування робочих поверхонь канавок шпонок;
4) знос канавок шпонок по довжині в з'єднаннях з ковзаючою шпонкою.

Канавки шпонок на новому місці роблять у випадках значного зносу і руйнувань канавок, тобто коли відновлення їх раніше вказаними способами неможливо, але за умовами міцності можна допустити ослаблення перетину валу виготовленням ще однієї канавки. Нові канавки щодо старих розташовують під кутом 90, 135 або 180°.
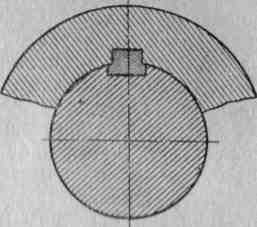
При відновленні канавок шпонок в маточинах їх розпилюють до більшого розміру або роблять канавку на новому місці. Виготовлення канавки шпонки на новому місці проводять на довбальних, поперечно-стругальних або протяжних верстатах. Якщо в результаті відновлення канавки шпон валу і отвору матимуть різну ширину, то застосовують ступінчасті шпонки, що спеціально виготовляються за розмірами відновлених канавок. При цьому ступені шпонки повинні бути розташовані строго симетрично .
Рис. 3
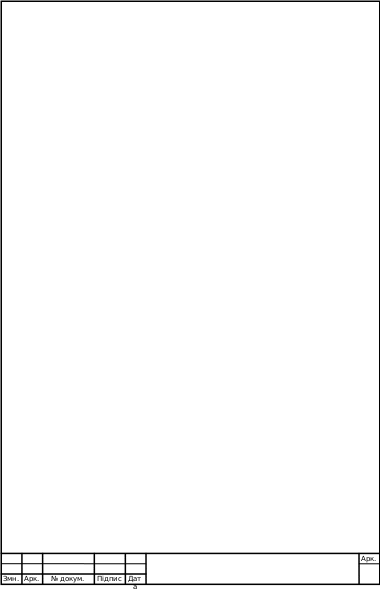
Випробування установки проводиться прокручуванням механізмів вручну, вхолосту а потім під нагрузкою. Обкатку установки на холостому ходу робити з короткочасними зупинками на періоди огляду.
У період обкатування перевіряють:
- включення і вимикання механізмів грубого привалу;
- температуру всіх підшипникових вузлів, що не повинна перевищувати
60°С;
-
переміщення заслінки; -
кріплення нарізних сполучень; -
стан ременів, електричних ланцюгів ї апаратури; -
правильність роботи електричної схеми;
- переміщення очисників вальців.
Перед обкатуванням перевіряється: наявність мастила в кожусі межвальцевої передачі і редукторах живильних пристроїв. Перевірка робиться після провертання рукою від себе шківа привода вальців при їхньому привалі, а також при знятих кришках кожуха міжвальцевої передачі і редуктора живильних пристроїв. (При обертанні шківа до себе буде відгвинчуватися шестірня в лівій опорі привода живильних пристроїв);
наявність консистентного змащення в підшипникових вузлах мелючих вальців, в опорах ексцентрикових валів.
Перед обкатуванням перевірте кріплення упорів з метою виключення затягування у вальці пучків полімерної нитки в щіткових очисників
При виявленні яких-небудь несправностей у роботі установки потрібно зупинити його й усунути несправності

Обслуговування установки допускаються особи, що пройшли спеціальну підготовку по вивченню установки. Персонал, що обслуговує установку, повинний володіти безпечними методами роботи і дотримувати запобіжного заходу
Електропроводка не повинна мати порушень ізоляції, а місця підключення повинні бути ретельно ізольовані.
При обслуговуванні установки не дозволяється:
-захаращувати проходи до установки;
-виконувати ремонтні операції без зняття клинових ременів електропривода;
-робити регулювання на ходу діапазону харчування в зоні плоскоременной передачі.
Не допускати скупчення молочного пилу на внутрішній і зовнішній поверхнях верстата.
Електроустаткування і установка повинні бути заземлені.
При відсутності заземлення забороняється включати електроустаткування.
Усі роботи з огляду, ремонтові й очищенню електроустаткування повинні вироблятися тільки при цілком знятій напрузі.

Аналіз стану використання машин та обладнання у харчовій промисловості свідчить, що вибір однотипних засобів механізації для виконання однойменних операцій, дотримання заводських інструкцій під час монтажу машин, кваліфіковане проведення пусконалагоджувальних робіт та чітка організація і дотримання технології технічного обслуговування в процесі експлуатації здатні суттєво (до 5 разів) підвищити надійність і довговічність техніки порівняно з тими підприємствами, де вказані умови порушуються.
В результаті виконання розрахунково-графічної роботи мною проведе- но аналіз існуючих конструкцій технологічної лінії дражування. Вивчено принцип роботи та облаштування, розроблена методика монтажу, діагностування, обслуговування та ремонту дражувача.
Розроблена схема розбирання машини, дефектування та запропонований метод ремонту та відновлення шпонки .
Також в роботі розроблені випробування та правила техніки безпеки при обслуговуванні машини.
Список використаної літератури:

1.Вечерский П.А. К вопросу динамикио брабатываюмого сыпучего вещества в адгезионном грануляторе.-«Пищевая технология»,1969,6:94-96.
2.Добротворцева А.В. Обволакивание свеклосемян удобрениями.-«Сахарная промышленность», 1951,2:39-42,
3.Мухин В.Д. Дражирование семян сельськохозяйственных культур.М.,»Колос», 1971,88.
4.С.В. Харламов Практикум по расчету и конструированию машин и аппаратов пищевых производств.1991-256 с.
5. В.И.Соколов Расчет и конструирование машин и апаратов пищевых производств 1992-200 с.
ДОДАТКИ

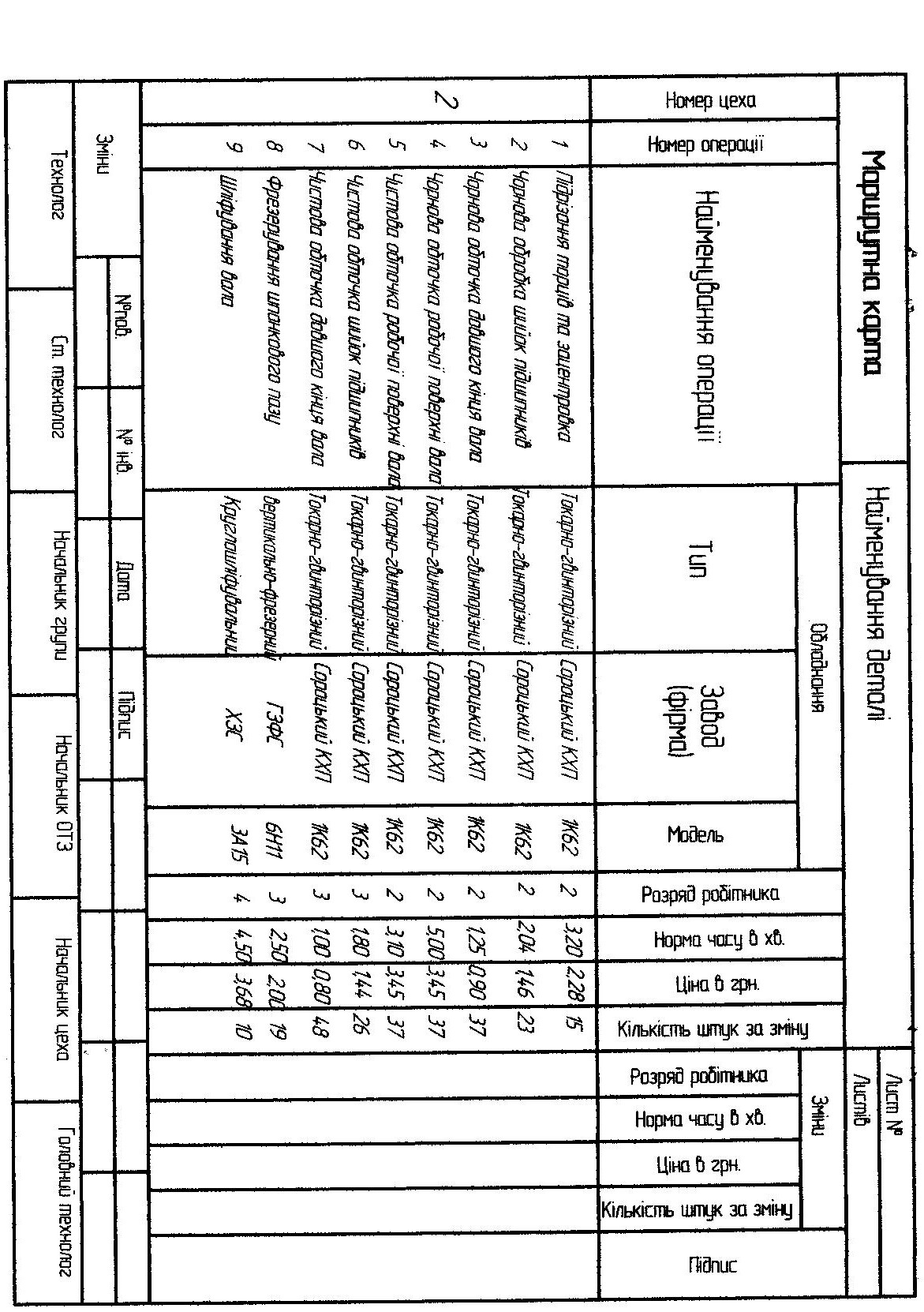
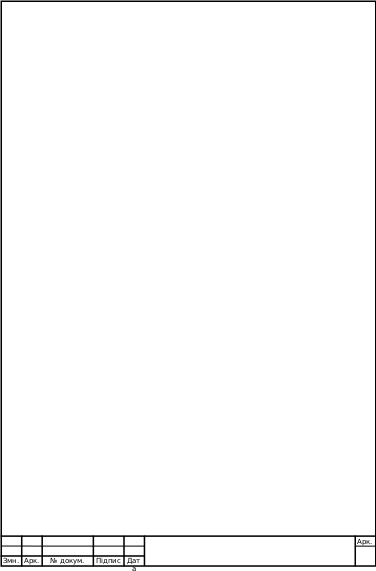
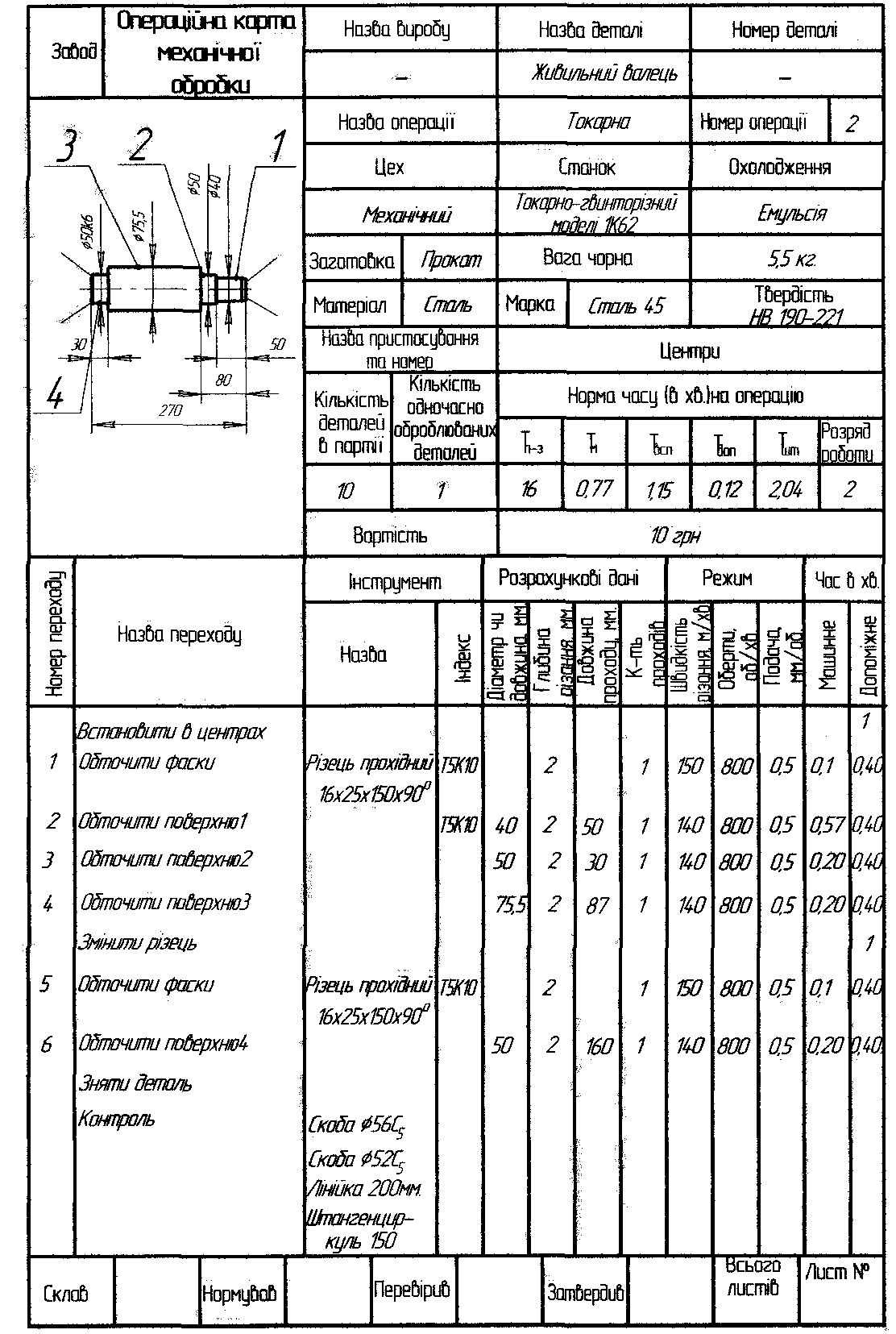
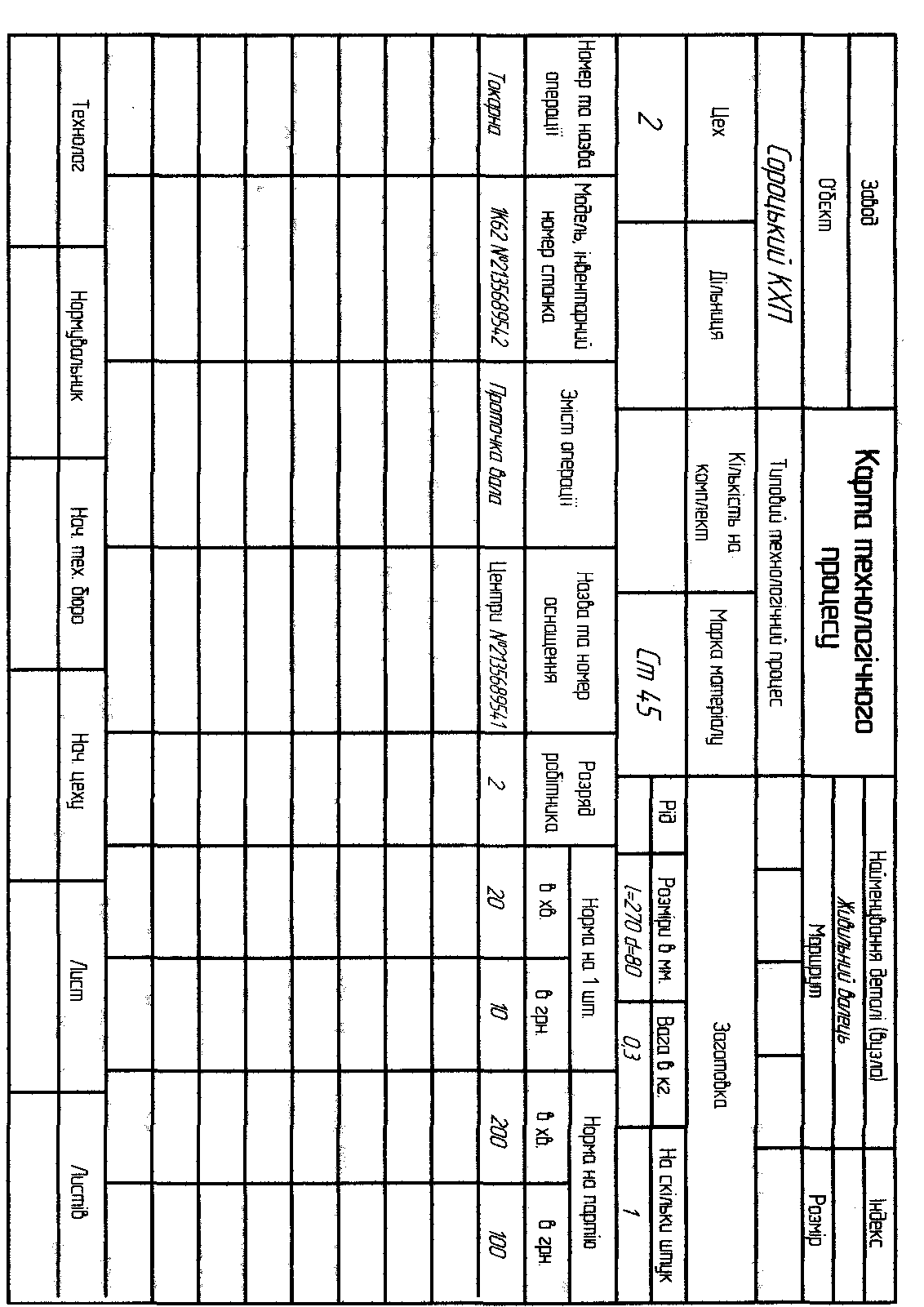
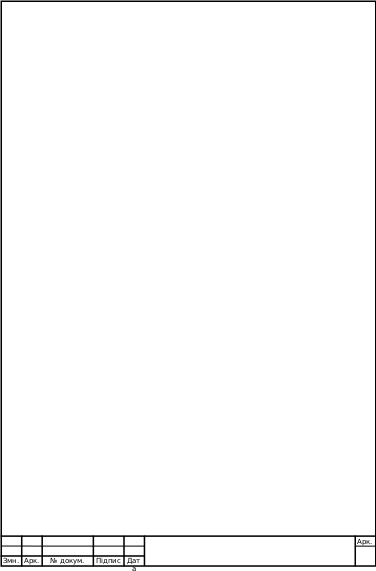