ВУЗ: Не указан
Категория: Не указан
Дисциплина: Не указана
Добавлен: 03.12.2023
Просмотров: 145
Скачиваний: 2
ВНИМАНИЕ! Если данный файл нарушает Ваши авторские права, то обязательно сообщите нам.
СОДЕРЖАНИЕ
5 на рис. 5) металл затвердевает, не имея кристаллического строения. Такой металл называется аморфным или металлическим стеклом.
Чем чище жидкий металл, тем более он склонен к переохлаждению. При затвердевании очень чистых металлов степень переохлаждения ∆Т может быть очень велика. Однако чаще степень переохлаждения не превышает 10…30 °C.
Основы теории кристаллизации были разработаны основоположником науки о металлах Д.К. Черновым, который установил, что процесс кристаллизации состоит из двух стадий: зарождения мельчайших частиц кристаллов (центров кристаллизации или зародышей) и роста кристаллов из этих центров. При переохлаждении сплава ниже температуры Т0 на многих его участках образуются устойчивые, способные к росту кристаллические зародыши (рис. 6).
Рисунок 6. Схема кристаллизации металла
Пока образовавшиеся кристаллы растут свободно, они имеют более или менее правильную геометрическую форму. Однако при столкновении растущих кристаллов их правильная форма нарушается, так как на этих участках рост граней прекращается. Рост продолжается только на тех направлениях, где есть свободный доступ «питающей» жидкости. В результате растущие кристаллы, имевшие сначала геометрически правильную форму, после затвердевания получают неправильную внешнюю форму и поэтому называются кристаллитами или зернами.
В жидком металле атомы не расположены хаотично, как в газообразном состоянии. И в то же время в их расположении нет той правильности, характерной для твердого кристаллического тела (рис. 7, а), в котором атомы сохраняют постоянство межатомных расстояний и угловых соотношений на больших расстояниях – дальний порядок.
В жидком металле (рис. 7, б) сохраняется лишь так называемый ближний порядок, когда упорядоченное расположение атомов распространяется на очень небольшое расстояние. Вследствие интенсивного теплового движения атомов ближний порядок динамически неустойчив. Микрообъемы с правильным расположением атомов, возникнув, могут существовать некоторое время, затем рассасываться и возникать вновь в другом элементарном объеме жидкости и т.д. С понижением температуры степень ближнего порядка и размер таких микрообъемов возрастают.
При температурах, близких к температуре плавления, в жид‑ ком металле возможно образование небольших группировок, в которых атомы упакованы так же, как в кристаллах. Такие группировки называются фазовыми (или гетерофазными) флуктуациями (рис. 7, в). В чистом от примесей жидком металле наиболее крупные гетерофазные флуктуации превращаются в зародыши (центры кристаллизации).
Рисунок 7. Модель кристаллической (а) и жидкой (б, в) фаз металла
Критическим размером зародыша называется минимальный размер зародыша RK, способного к росту при данных температурных условиях, а сам зародыш именуется критическим или равновесным. Величину критического зародыша можно определить из соотношения:
где
– удельное поверхностное натяжение на границе жидкость-кристалл, ∆GV — разность энергий Гиббса жидкого и твердого металла.
При температуре, близкой к Т0, размер критического зародыша должен быть очень велик, а вероятность его образования мала. С увеличением степени переохлаждения величина ∆GV возрастает, а величина поверхностного натяжения на границе раздела фаз изменяется незначительно. Следовательно, с увеличением степени переохлаждения (или с понижением температуры кристаллизации) размер критического зародыша уменьшается и будет уменьшаться работа, необходимая для его образования. В связи с этим с увеличением степени переохлаждения, когда становятся способными к росту зародыши все меньшего размера, сильно возрастает число зародышей (центров) кристаллизации и скорость образования этих зародышей.
Параметры, которыми можно охарактеризовать процесс кристаллизации: число зародышевых центров, возникающих в единице объема за единицу времени (n, мм–3 · с–1), т. е. скорость образования зародышей и линейная скорость их роста (c, мм/с), т.е. скорость увеличения линейных размеров растущего кристалла в единицу времени. Величина этих параметров предопределяет не только скорость процесса кристаллизации, но и размер образующегося зерна. Действительно, если в единице объема за единицу времени возникает мало зародышевых центров, а скорость роста зародышей велика, то исходная материнская фаза будет израсходована прежде, чем успеют возникнуть последующие порции зародышевых центров. В этом случае закристаллизовавшееся вещество получится крупнозернистым.
Конечный размер зерна при условии одинаковой степени переохлаждения по всему объему вещества зависит от соотношения скоростей зарождения и роста и может быть выражен следующей формулой:
где K – коэффициент пропорциональности, n – скорость образования зародышей, c – скорость роста.
Чем больше скорость образования зародышей и их роста, тем быстрее протекает процесс кристаллизации. При равновесной температуре кристаллизации Т0 число зародышей и скорость их роста равны нулю, и поэтому кристаллизация не происходит (рис. 8).
Рисунок 8. Схема зависимости числа центров кристаллизации (n) и линейной скорости роста (с) от степени переохлаждения
При увеличении степени переохлаждения скорость образования зародышей и скорость их роста возрастают, а при определенной степени переохлаждения достигают максимума, после чего снижаются. С увеличением степени переохлаждения скорость образования зародышей, а следовательно, и их число возрастают быстрее, чем скорость их роста. Такой характер изменения n и c в зависимости от степени переохлаждения объясняется следующим. С повышением степени переохлаждения разность энергий Гиббса жидкого и твердого металлов ∆GV возрастает, что способствует повышению скорости кристаллизации, т.е. скорости образования зародышей и их роста (рис. 8). Однако для образования и роста зародышей требуется диффузионное перемещение атомов в жидком металле. В связи с этим при больших степенях переохлаждения (низких температурах) и при уменьшении скорости диффузии образование зародышей и их рост затруднены. Вследствие этого число зародышей и скорость их роста уменьшаются.
Величина зерна. С увеличением степени переохлаждения параметр n (число центров кристаллизации) увеличивается более интенсивно, чем параметр c (скорость роста), поэтому увеличение степени переохлаждения способствует получению более мелкого зерна. Однако размер зерна кристаллизующегося металла зависит не только от степени переохлаждения, но и от степени развития так называемой несамопроизвольной (гетерогенной) кристаллизации.
В жидком металле всегда имеются те или иные примеси в виде посторонних твердых частиц. В том случае, когда поверхностное натяжение на границе раздела фаз между зародышем и посторонней частицей меньше, чем поверхностное натяжение между зародышем и жидкой фазой, зародышу энергетически легче образоваться на такой частице. Эти частицы называются поверхностно-активными, а образование на них зародышевых центров — несамопроизвольной кристаллизацией. Количество несамопроизвольно возникающих зародышевых центров зависит не только от количества и характера примесей, но и от температуры жидкого металла. Чем выше температура жидкого металла, тем больше растворяется посторонних твердых частиц, а следовательно, меньше образуется зародышевых центров и зерно получается более крупным. Поэтому незначительный нагрев жидкого металла, при котором сохраняется большое количество поверхностно-активных частиц, способствует получению мелкого зерна.
Для получения мелкого зерна проводят процесс модифицирования, т.е. вводят в жидкий металл специальные примеси – модификаторы. Существует два способа модифицирования: 1) в расплав вводятся порошки тугоплавких веществ, которые при охлаждении способствуют интенсивному развитию несамопроизвольной кристаллизации и получению мелкого зерна; 2) в жидкий металл вводят растворимые добавки, снижающие поверхностное натяжение на границе раздела между твердой и жидкой фазами и тем самым облегчающие образование зародышевых центров.
Таким образом, размер зерна кристаллизующегося металла зависит от степени переохлаждения и от количества зародышевых центров, возникающих несамопроизвольным путем. При этом следует учитывать, что для чистых металлов обычно не удается достигнуть значительных степеней переохлаждения, и поэтому ведущую роль играет второй фактор. В связи с тем, что при кристаллизации сплавов удается получать значительное переохлаждение, размер зерна сплавов может в сильной мере зависеть от степени развития как несамопроизвольной, так и самопроизвольной кристаллизации.
При модифицировании алюминиевых сплавов применяют Ti, V, Zr; стали – Al, V, Ti. Бор используют в качестве поверхностно-активного модификатора для никелевых и железных сплавов, магний – для чугуна.
Кристаллизация и структура слитка (отливки). Условия отвода теплоты при кристаллизации значительно влияют на форму зерен. Кристаллы растут преимущественно в направлении, обратном отводу теплоты. Поэтому при направленном теплоотводе образуются вытянутые (столбчатые) кристаллы. Если теплота от растущего кристалла отводится во всех трех направлениях с приблизительно одинаковой скоростью, то формируются равноосные кристаллы.
Структура слитка зависит от многих факторов, основные из которых следующие: количество и свойства примесей в чистом металле или легирующих элементов в сплаве, температура разливки, скорость охлаждения при кристаллизации, а так‑ же конфигурация, температура, теплопроводность, состояние внутренней поверхности литейной формы.
Рисунок 9. Схемы макроструктур слитков: а - типичная; б - транскристаллическая; в - однородная мелкозернистая.
а) типичная структура слитка состоит из трех зон: 1 – зона мелких равноосных кристаллов, образованная на поверхности слитка благодаря большой степени переохлаждения. Отсутствие направленного роста кристаллов этой зоны объясняется их случайной ориентацией, которая является причиной столкновения кристаллов и прекращения их роста. Ориентация кристаллов, в свою очередь, зависит от состояния поверхности формы (шероховатость, адсорбированные газы и т.д.) и наличия в жидком металле оксидов, немет. включений; 2 – зона столбчатых кристаллов, наиболее благоприятно ориентированных по отношению к теплоотводу; 3 – зона равноосных кристаллов больших размеров, образованных в середине слитка, где наблюдается наименьшая степень переохлаждения и не ощущается направленного отвода теплоты.
б) транскристаллическая структура, состоящая практически из одних столбчатых кристаллов. Формирование такое структуры происходит за счёт перегрева сплавов перед разливкой и быстрого охлаждения при кристаллизации. Подобную структуру имеют слитки очень чистых металлов;
в) однородная мелкозернистая структура – структура, состоящая из равноосных кристаллов. Такая структура может быть получена при низкой температуре разливки, продувке жидкого металла инертными газами, вибрации, модифицировании – эти процессы приводят к уменьшению или даже исчезновению зоны столбчатых кристаллов.
Чем чище жидкий металл, тем более он склонен к переохлаждению. При затвердевании очень чистых металлов степень переохлаждения ∆Т может быть очень велика. Однако чаще степень переохлаждения не превышает 10…30 °C.
Основы теории кристаллизации были разработаны основоположником науки о металлах Д.К. Черновым, который установил, что процесс кристаллизации состоит из двух стадий: зарождения мельчайших частиц кристаллов (центров кристаллизации или зародышей) и роста кристаллов из этих центров. При переохлаждении сплава ниже температуры Т0 на многих его участках образуются устойчивые, способные к росту кристаллические зародыши (рис. 6).
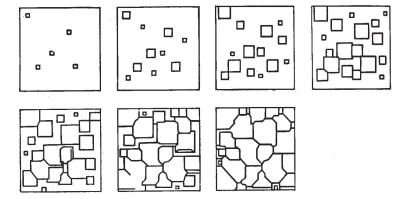
Рисунок 6. Схема кристаллизации металла
Пока образовавшиеся кристаллы растут свободно, они имеют более или менее правильную геометрическую форму. Однако при столкновении растущих кристаллов их правильная форма нарушается, так как на этих участках рост граней прекращается. Рост продолжается только на тех направлениях, где есть свободный доступ «питающей» жидкости. В результате растущие кристаллы, имевшие сначала геометрически правильную форму, после затвердевания получают неправильную внешнюю форму и поэтому называются кристаллитами или зернами.
В жидком металле атомы не расположены хаотично, как в газообразном состоянии. И в то же время в их расположении нет той правильности, характерной для твердого кристаллического тела (рис. 7, а), в котором атомы сохраняют постоянство межатомных расстояний и угловых соотношений на больших расстояниях – дальний порядок.
В жидком металле (рис. 7, б) сохраняется лишь так называемый ближний порядок, когда упорядоченное расположение атомов распространяется на очень небольшое расстояние. Вследствие интенсивного теплового движения атомов ближний порядок динамически неустойчив. Микрообъемы с правильным расположением атомов, возникнув, могут существовать некоторое время, затем рассасываться и возникать вновь в другом элементарном объеме жидкости и т.д. С понижением температуры степень ближнего порядка и размер таких микрообъемов возрастают.
При температурах, близких к температуре плавления, в жид‑ ком металле возможно образование небольших группировок, в которых атомы упакованы так же, как в кристаллах. Такие группировки называются фазовыми (или гетерофазными) флуктуациями (рис. 7, в). В чистом от примесей жидком металле наиболее крупные гетерофазные флуктуации превращаются в зародыши (центры кристаллизации).
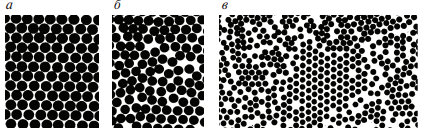
Рисунок 7. Модель кристаллической (а) и жидкой (б, в) фаз металла
Критическим размером зародыша называется минимальный размер зародыша RK, способного к росту при данных температурных условиях, а сам зародыш именуется критическим или равновесным. Величину критического зародыша можно определить из соотношения:

где

При температуре, близкой к Т0, размер критического зародыша должен быть очень велик, а вероятность его образования мала. С увеличением степени переохлаждения величина ∆GV возрастает, а величина поверхностного натяжения на границе раздела фаз изменяется незначительно. Следовательно, с увеличением степени переохлаждения (или с понижением температуры кристаллизации) размер критического зародыша уменьшается и будет уменьшаться работа, необходимая для его образования. В связи с этим с увеличением степени переохлаждения, когда становятся способными к росту зародыши все меньшего размера, сильно возрастает число зародышей (центров) кристаллизации и скорость образования этих зародышей.
Параметры, которыми можно охарактеризовать процесс кристаллизации: число зародышевых центров, возникающих в единице объема за единицу времени (n, мм–3 · с–1), т. е. скорость образования зародышей и линейная скорость их роста (c, мм/с), т.е. скорость увеличения линейных размеров растущего кристалла в единицу времени. Величина этих параметров предопределяет не только скорость процесса кристаллизации, но и размер образующегося зерна. Действительно, если в единице объема за единицу времени возникает мало зародышевых центров, а скорость роста зародышей велика, то исходная материнская фаза будет израсходована прежде, чем успеют возникнуть последующие порции зародышевых центров. В этом случае закристаллизовавшееся вещество получится крупнозернистым.
Конечный размер зерна при условии одинаковой степени переохлаждения по всему объему вещества зависит от соотношения скоростей зарождения и роста и может быть выражен следующей формулой:

где K – коэффициент пропорциональности, n – скорость образования зародышей, c – скорость роста.
Чем больше скорость образования зародышей и их роста, тем быстрее протекает процесс кристаллизации. При равновесной температуре кристаллизации Т0 число зародышей и скорость их роста равны нулю, и поэтому кристаллизация не происходит (рис. 8).
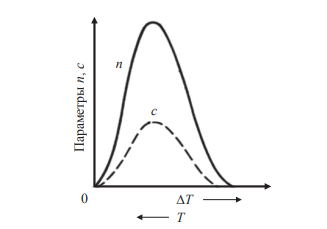
Рисунок 8. Схема зависимости числа центров кристаллизации (n) и линейной скорости роста (с) от степени переохлаждения
При увеличении степени переохлаждения скорость образования зародышей и скорость их роста возрастают, а при определенной степени переохлаждения достигают максимума, после чего снижаются. С увеличением степени переохлаждения скорость образования зародышей, а следовательно, и их число возрастают быстрее, чем скорость их роста. Такой характер изменения n и c в зависимости от степени переохлаждения объясняется следующим. С повышением степени переохлаждения разность энергий Гиббса жидкого и твердого металлов ∆GV возрастает, что способствует повышению скорости кристаллизации, т.е. скорости образования зародышей и их роста (рис. 8). Однако для образования и роста зародышей требуется диффузионное перемещение атомов в жидком металле. В связи с этим при больших степенях переохлаждения (низких температурах) и при уменьшении скорости диффузии образование зародышей и их рост затруднены. Вследствие этого число зародышей и скорость их роста уменьшаются.
Величина зерна. С увеличением степени переохлаждения параметр n (число центров кристаллизации) увеличивается более интенсивно, чем параметр c (скорость роста), поэтому увеличение степени переохлаждения способствует получению более мелкого зерна. Однако размер зерна кристаллизующегося металла зависит не только от степени переохлаждения, но и от степени развития так называемой несамопроизвольной (гетерогенной) кристаллизации.
В жидком металле всегда имеются те или иные примеси в виде посторонних твердых частиц. В том случае, когда поверхностное натяжение на границе раздела фаз между зародышем и посторонней частицей меньше, чем поверхностное натяжение между зародышем и жидкой фазой, зародышу энергетически легче образоваться на такой частице. Эти частицы называются поверхностно-активными, а образование на них зародышевых центров — несамопроизвольной кристаллизацией. Количество несамопроизвольно возникающих зародышевых центров зависит не только от количества и характера примесей, но и от температуры жидкого металла. Чем выше температура жидкого металла, тем больше растворяется посторонних твердых частиц, а следовательно, меньше образуется зародышевых центров и зерно получается более крупным. Поэтому незначительный нагрев жидкого металла, при котором сохраняется большое количество поверхностно-активных частиц, способствует получению мелкого зерна.
Для получения мелкого зерна проводят процесс модифицирования, т.е. вводят в жидкий металл специальные примеси – модификаторы. Существует два способа модифицирования: 1) в расплав вводятся порошки тугоплавких веществ, которые при охлаждении способствуют интенсивному развитию несамопроизвольной кристаллизации и получению мелкого зерна; 2) в жидкий металл вводят растворимые добавки, снижающие поверхностное натяжение на границе раздела между твердой и жидкой фазами и тем самым облегчающие образование зародышевых центров.
Таким образом, размер зерна кристаллизующегося металла зависит от степени переохлаждения и от количества зародышевых центров, возникающих несамопроизвольным путем. При этом следует учитывать, что для чистых металлов обычно не удается достигнуть значительных степеней переохлаждения, и поэтому ведущую роль играет второй фактор. В связи с тем, что при кристаллизации сплавов удается получать значительное переохлаждение, размер зерна сплавов может в сильной мере зависеть от степени развития как несамопроизвольной, так и самопроизвольной кристаллизации.
При модифицировании алюминиевых сплавов применяют Ti, V, Zr; стали – Al, V, Ti. Бор используют в качестве поверхностно-активного модификатора для никелевых и железных сплавов, магний – для чугуна.
Кристаллизация и структура слитка (отливки). Условия отвода теплоты при кристаллизации значительно влияют на форму зерен. Кристаллы растут преимущественно в направлении, обратном отводу теплоты. Поэтому при направленном теплоотводе образуются вытянутые (столбчатые) кристаллы. Если теплота от растущего кристалла отводится во всех трех направлениях с приблизительно одинаковой скоростью, то формируются равноосные кристаллы.
Структура слитка зависит от многих факторов, основные из которых следующие: количество и свойства примесей в чистом металле или легирующих элементов в сплаве, температура разливки, скорость охлаждения при кристаллизации, а так‑ же конфигурация, температура, теплопроводность, состояние внутренней поверхности литейной формы.
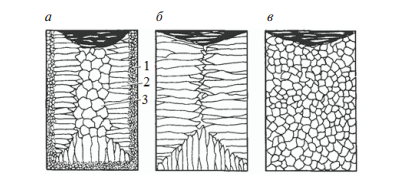
Рисунок 9. Схемы макроструктур слитков: а - типичная; б - транскристаллическая; в - однородная мелкозернистая.
а) типичная структура слитка состоит из трех зон: 1 – зона мелких равноосных кристаллов, образованная на поверхности слитка благодаря большой степени переохлаждения. Отсутствие направленного роста кристаллов этой зоны объясняется их случайной ориентацией, которая является причиной столкновения кристаллов и прекращения их роста. Ориентация кристаллов, в свою очередь, зависит от состояния поверхности формы (шероховатость, адсорбированные газы и т.д.) и наличия в жидком металле оксидов, немет. включений; 2 – зона столбчатых кристаллов, наиболее благоприятно ориентированных по отношению к теплоотводу; 3 – зона равноосных кристаллов больших размеров, образованных в середине слитка, где наблюдается наименьшая степень переохлаждения и не ощущается направленного отвода теплоты.
б) транскристаллическая структура, состоящая практически из одних столбчатых кристаллов. Формирование такое структуры происходит за счёт перегрева сплавов перед разливкой и быстрого охлаждения при кристаллизации. Подобную структуру имеют слитки очень чистых металлов;
в) однородная мелкозернистая структура – структура, состоящая из равноосных кристаллов. Такая структура может быть получена при низкой температуре разливки, продувке жидкого металла инертными газами, вибрации, модифицировании – эти процессы приводят к уменьшению или даже исчезновению зоны столбчатых кристаллов.