ВУЗ: Не указан
Категория: Не указан
Дисциплина: Не указана
Добавлен: 03.12.2023
Просмотров: 58
Скачиваний: 1
ВНИМАНИЕ! Если данный файл нарушает Ваши авторские права, то обязательно сообщите нам.
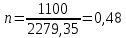
Вывод: запас прочности составляет 0,48. Условие прочности не выполняется, следовательно, канат для использования в заданных условиях не пригоден.
2 Раздел монтажа и ремонта нефтегазопромыслового оборудования
2.1 Монтаж оборудования
2.1.1 Монтаж подъемного агрегата А2-32М
При подземном ремонте глубоких скважин применяют эксплуатационные вышки и мачты, стационарные или передвижные, предназначенные для подвески талевой системы, поддержания на весу колонны труб или штанг при ремонтных работах, проводимых на скважине.
Стационарные вышки и мачты используются крайне нерационально, т.к. ремонтные работы на каждой скважине проводятся всего лишь несколько дней в году, всё остальное время эти сооружения находятся в бездействии. Поэтому целесообразно использовать при подземном ремонте подъемники, несущие собственные мачты. Транспортной базой их служат тракторы и автомобили.
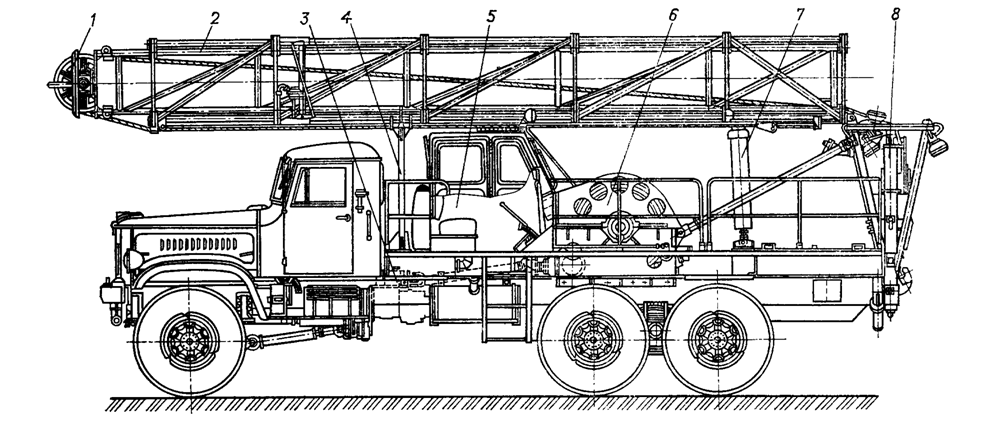
1 – талевая система; 2 – вышка; 3 – силовая передача; 4 – передняя опора; 5 – кабина оператора; 6 – лебедка; 7 – гидроцилиндр поднимания опоры; 8 – задняя опора
Рисунок 9 – Конструкция подъемного агрегата А2-32М
Выбирается, расчищается и при необходимости планируется площадка для установки подъемника, приемных мостов и стеллажей.
При установке подъемника запрещено находится в зоне движения подъемника к устью скважины.
Движением подъемника руководит старший вахты (старший оператор ТРС, бурильщик КРС).
Под колеса подъемника после его установки устанавливаются противооткатные упоры.
Под опорные домкраты устанавливаются деревянные подушки, брусья сбиваются между собой скобами.
Производится установка на домкраты и фиксация их контргайками.
Работы на высоте по монтажу, демонтажу и ремонту вышек и мачт в ночное время, при ветре со скоростью 8 м/с и выше, во время грозы, сильного снегопада, при гололедице, ливне, тумане видимостью менее 100 м должны быть приостановлены.
При подъеме мачты следить за выполнением работы, в случае отклонений немедленно сообщить машинисту подъемника.
Произвести монтаж оттяжек.
Силовые и ветровые оттяжки А2-32М должны закрепляться за якори на расстоянии 28 метров и под углом 45. Неточность установки якорей допускается ±1,5м.
Оттяжки к якорям присоединять при помощи винтовых оттяжек специальными цепями с приспособлением для их надежной фиксации или маркированными петлями и крепить не менее как четырьмя зажимами, расположенными между собой на расстоянии не менее 300мм.
Винтовые оттяжки должны иметь контрольные окна или установленные ограничители, исключающие полное выворачивание винтов из гаек.
На расстоянии 100 мм от вертикального конца врезается крестовина, диаметром 26 мм, на которую зацепляется петля из стального каната, диаметром не менее 18 мм.
Произвести заземление подъемного агрегата.
Силовые кабели уложить на треноги.
Произвести монтаж рабочей площадки.
Проверить центричность талевого блока по отношению к оси скважины, произвести центровку.
Регулировка тормозной системы буровых лебедок.
Грамотный и качественный монтаж подъемного агрегата с соблюдением всех требований и условий монтажа исключает возможность несчастного случая с персоналом и обеспечивает качество проведения ремонта скважины.
2.2 Ремонт оборудования
2.2.1 Ремонт оборудования, используемого при СПО
При проведении спуско-подъемных операций, проводимых на скважине с использованием подъемных агрегатов особое внимание уделяется талевой системе - грузонесущей части установки, которая представляет собой полиспаст, состоящий из кронблока, монтируемого на подкронблочных балках верхнего основания вышки, талевого блока, связанного с кронблоком канатной оснасткой, и грузоподъемного крюка, соединенного с талевым блоком или автоматическим элеватором для подвешивания бурильной колонны и обсадных труб.
При длительном использовании оборудования при спуско-подъемных операциях возникают неисправности оборудования и возникает необходимость его ремонта.
Кронблок – неподвижный узел талевой системы, предназначенный для поддержания на весу талевого блока, крюка и подвешенного на нем груза.
При разборке кронблока необходимо (рисунок 9): открыть и снять кожух 11; отсоединить от рамы вспомогательный ролик; освободить опоры 4 и 12; снять ось в сборе; отогнут лепестки стопорной шайбы и отвинтить гайку 3; удалить штифт 13; снять с оси опоры 4 и 12, втулку 6, блоки 10 с роликоподшипниками 8, а также дистанционные кольца 1 и 7; выпрессовать роликоподшипники из ступиц блоков и вынуть пружинные стопорные кольца 1 и 7; выпрессовать роликоподшипники из ступиц блоков и вынуть пружинные стопорные кольца 9; вывинтить масленки 2 из оси 5; очистить все детали кронблока от грязи и промыть; выявить дефекты деталей и составить дефектную ведомость.
Для облегчения выпрессовки подшипников ступицы блоков нагревают газовыми горелками до 90-100 °С. При ремонте кронблока заменяют роликоподшипники, крепежные и другие детали, износ которых превышает допустимый.
Смена роликоподшипников канатных блоков вызывается недопустимым люфтом или поломкой. Предельно допустимый люфт роликоподшипников № 42234 равен 0,3-0,4 мм. Подшипники, у которых радиальный зазор превышает 0,5 мм, подлежат замене. Перед установкой новых подшипников необходимо проверить размер отверстия в ступице блока, который в сопряжении с фактическим размером наружного диаметра верхнего кольца подшипника должен гарантировать сборку с натягом 0,035 мм. Перед установкой подшипника блок предварительно нагревают до 100-160 °С, что облегчает монтаж и уменьшает износ посадочного отверстия блока. При каждом капитальном ремонте ось кронблока проверяют магнитным дефектоскопом.

1 – кольцо; 2 – масленки; 3 – гайка; 4 – опора; 5 – ось; 6 – втулка; 7 – кольцо; 8 – роликоподшипники; 9 – стопорные кольца; 10 – блок; 11 – кожух; 12 – опора; 13 – штифт
Рисунок 10 - Кронблок
Наиболее быстро изнашиваются блоки, ближе расположенные к ходовому концу. Поэтому при сборке блоков целесообразно переставить их на оси блока и втулку.
Рама кронблока не должна иметь трещин и короблений; балки рамы должны быть параллельны; отклонение от параллельности по всей длине не должно превышать ± 5 мм, деформированную необходимо очистить от грязи каждый смазочный канал в оси, промывая его керосином или продувая сжатым воздухом. Затем, ввинтив масленки в торцы оси, продавливают смазку ручным насосом через все отверстия.
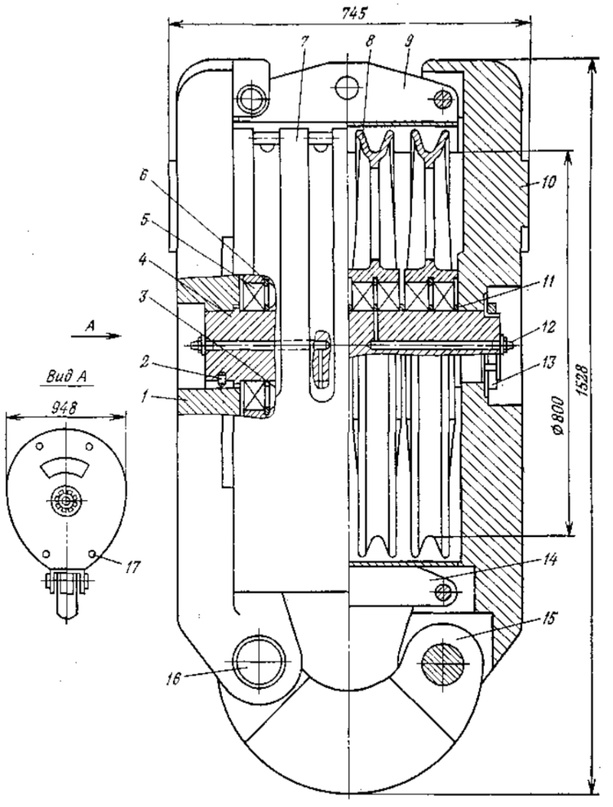
1 – щека; 2 – штифт; 3 – дистанционные кольца; 4 – ось; 5 – роликоподшипники; 6 - пружинные стопорные кольца; 7 – кожух; 8 - канатные блоки; 9 – траверса; 10 – щека; 11 – кольца; 12 – масленки; 13 – гайка; 14 – нижний щит; 15 – серьга; 16 – пальцы
Рисунок 11 – Талевый блок
Сборку отремонтированного кронблока производят в последовательности, обратной разборке. Перед посадкой блоков на ось необходимо обильно смазать роликоподшипники. После сборки проверяют от руки легкость вращения каждого канатного блока в отдельности. При вращении любого из блоков соседней не должен вращаться.
Торцевое биение ручья блока, измеренное в наиболее удаленных точках, не должно превышать 1 мм. На рабочих поверхностях ручья допускается заварка единичных раковин диаметром до 5 мм и глубиной до 2 мм с последующей зачисткой.
Сварочные швы рамы кронблока не должны иметь трещин, шлаковых включений, газовых пузырей, подрезов, пережога и других пороков, влияющих на прочность шва.
Талевый блок (рисунок 11) является подвижной частью талевой системы. Разбирать талевый блок следует в следующем порядке: отвинтить гайки, выбить болты 17 и снять кожух 7; открепить и снять траверсу 9 и нижний щит 14; выбить шплинты, отвинтить гайки, выбить пальцы 16 и отсоединить серьгу 15 от щек 1 и 10; талевый блок положить на щеку 1, отогнуть лепестки стопорной шайбы, отвинтить гайку 13 оси 4 и снять щеку 10; повернуть блок и освободить щеку 1; снять с оси кольца 11, дистанционные кольца 3 и канатные блоки 8 с роликоподшипниками 5; выпрессовать роликоподшипники из ступиц блоков и вынуть пружинные стопорные кольца 6; вывинтить масленки 12 из оси и выпрессовать при необходимости штифт 2; очистить все детали от грязи и промыть; составить дефектную ведомость.
Характер износа деталей талевого блока и виды ремонтных работ такие же, как у кронблока, за исключением восстановления серьги, пальцев серьги, верхнего щита, нижнего щита и щек.
На поверхности серьги талевого блока в плоскости опасного сечения допускается углубление от износа до 3 мм при ширине до 10 мм. Заварка изношенных поверхностей не рекомендуется. Каждые 6 месяцев необходимо проверять щеки, пальцы, серьги и ось магнитным или другим способом. Особое внимание при ремонте необходимо обращать на щеки талевого блока. В процессе бурения и при спуско-подъемных операциях он воспринимает статические, динамические и вибрационные нагрузки, которые повышают напряжения в отдельных элементах. В процессе эксплуатации отмечаются случаи обрыва щек вследствие ослабления посадки пальцев 16. При наличии трещин в щеках их необходимо заменить новыми. Выработку в щеках удаляют наплавкой электродами, близкими по составу основному металлу щек. Пальцы серьги с износом по диаметру более 2 мм подлежат замене. Вмятины кожуха выправляют после нагрева газовой горелкой, а надрывы заваривают.
Сборку талевого блока производят в последовательности, обратной разборке. Все резьбовые соединения должны быть надежно застопорены против самоотвинчивания под действием вибрационных нагрузок.
При ежедневном осмотре подъемного агрегата, проведении технического обслуживания с соблюдением графика планово-предупредительного ремонта (ППР) и качественном ремонте оборудования с соблюдением всех пунктов и требований ремонта кратно увеличивает срок службы и долговечности подъемного агрегата.
2.2.2 Ремонт НШ
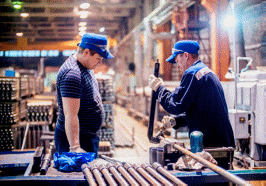
Рисунок 12 – Ремонт насосной штанги
Основные технологические операции ремонта насосных штанг
- Первичный визуальный контроль штанг:
При первичном визуальном контроле насосных штанг выявляются недопустимые дефекты, видимые невооруженным глазом: обрывы, глубокие механические повреждения, износ поверхностей муфты и штанги более допустимого, запредельное искривление штанг, которые делают их неремонтопригодными.
- Мойка штанг:
Прошедшие визуальный контроль штанги очищаются от нефтепродуктов и асфальтосмолопарафинов в моющей установке водой с добавлением моющих средств при температуре 80-90⁰ С.
- Контрольная визуальная и инструментальная отбраковка очищенных штанг и муфт, сортировка штанг по типоразмерам:
После мойки и механической очистки резьбовых элементов штанг производится визуальный контроль резьбы на отсутствие повреждений, инструментальный контроль резьбы калибрами и, при необходимости, исправление дефектных участков резьбы плашками или метчиками. Производится также визуально-инструментальный контроль тела насосных штанг на отсутствие дефектов, механических повреждений, износа или прогиба более допустимого. Штанги с недопустимыми дефектами отбраковываются и маркируются краской. Годные штанги сортируются по типоразмерам, товарному знаку, маркам стали и виду термообработки.