ВУЗ: Не указан
Категория: Не указан
Дисциплина: Не указана
Добавлен: 06.12.2023
Просмотров: 440
Скачиваний: 1
ВНИМАНИЕ! Если данный файл нарушает Ваши авторские права, то обязательно сообщите нам.
В качестве теплоизоляционного слоя СНиП 41 – 03 – 2003 «Тепловая изоляция оборудования и трубопроводов» рекомендуют к применению более 30 основных видов материалов, изделий, заводских продуктов общего назначения, обеспечивающих тепловой поток через изолированные поверхности оборудования и трубопроводов согласно заданному технологическому режиму или нормированной плотности теплового потока; исключение выделения в процессе эксплуатации вредных, пожароопасных, неприятно пахнущих веществ в количествах, превышающих предельно допустимые концентрации; исключение выделения в процессе эксплуатации болезнетворных бактерий, вирусов и грибков.
К числу таких эффективных традиционно используемых в тепловых сетях материалов относятся армопенобетон автоклавного твердения, битумперлит, асфальтокерамзитобетон, газосиликат, фенольные пенопласты, теплоизоляционные ваты, вулканитовые и некоторые другие материалы. Основные усредненные данные теплоизоляционных материалов и изделий представлены в табл. 1.8.
В качестве материалов для покрывного слоя тепловой изоляции при новом строительстве применяют конструкции заводского изготовления: 1) из металла (листы и тенты из алюминия и его сплавов, сталь тонколистовая кровельная и оцинкованная, оболочки гофрированные, металлопласты и др.); 2) на основе синтетических полимеров (стеклотекстолит конструкционный, стеклопластик рулонный, армопластмассовые материалы и др.); 3) на основе природных полимеров (рубероид, стеклорубероид, толь, пергамин кровельный и др.); 4) минеральные (стеклоцемент, листы асбоцементные плоские и волнистые, штукатурка асбоцементная и др.); 5) дублированные фольгой (фольга алюминиевая дублированная, фольгоизол и др).
Таблица 1.8
Основные данные теплоизоляционных материалов
и изделий
Материалы или изделия | Максимальная температура теплоносителя, 0С | Теплопроводность, Вт/(м·0С), при 20 0С и влажности, % | Плотность, кг/м3 | |
0 | 20 | |||
Минеральная вата | 600 | 0,05 | 0,13 | 200 |
Изоляция: из минеральной ваты из непрерывного стекловолокна из штапельного стекловолокна | 400 450 180 | 0,06 0,06 0,05 | 0,17 0,13 0,12 | 200 170 75 |
Изделия: совелитовые вулканитовые известково – кремнеземистые | 500 600 600 | 0,08 0,085 0,065 | - - - | 400 400 225 |
Монолитные: армобетон битумоперлит асфальтокерамзитобетон пенобетон фторопласт | 150 150 150 400 150 | 0,1 0,09 0,12 0,12 0,06 | 0,16 - - 0,16 - | 400 350 750 400 120 |
самоспекающийся асфальтоизол | 150 | 0,1 | - | 750 |
Плиты торфяные | 100 | 0,065 | 0,09 | 220 |
В качестве противокоррозионных и гидроизоляционных покрытий используются покрытия барьерного и протекторного типов – полимерные, металлизационные, силикатные и органосиликатные, а также защитные покрытия на битумном вяжущем.
Для бесканальной конструкции теплопроводов следует применять материалы со средней плотностью не более 600 кг/м3 и теплопроводностью не более 0,13 Вт/(м·0С). Конструкция тепловой изоляции при этом должна обладать прочностью на сжатие не менее 0,4 МПа. Расчетные технические характеристики материалов, применяемых для изоляции трубопроводов при бесканальной прокладке, представлены в табл. 1.9.
Таблица 1.9
Расчетные технические характеристики материалов,
применяемых для изоляции трубопроводов
при бесканальной прокладке
Материал | Условный проход трубопровода, мм | Средняя плотность , кг/м3 | Теплопроводность сухого материала , Вт/(м 0С) при 20 0С | Максимальная температура вещества, 0С |
Армопенобетон Битумоперлит Битумокерамзит Битумовермикулит Пенополиметбетон Пенополиуретан Фенольный поропласт ФП монолитный | 150 – 80050 400 До 500 До 500 100 – 400 100 – 400 До 1000 | 360 – 450 450 – 550 600 600 400 60 – 80 100 | 0,105 – 0,13 0,11 – 0,13 0.13 0,13 0,07 0,05 0,05 | 150 130 130 130 150 120 150 |
Допускается применение до температуры 150 0С при качественном методе отпуска теплоты.
На рис.1.20, 1,21 представлено несколько вариантов традиционных индустриальных конструкций теплопроводов.
Пенобетонная изоляция представляет собой легкий изоляционный материал, получаемый путем приготовления пеномассы и последующего отвержения ее в кассетном автоклаве при давлении 8 – 10 кгс/м2 в течение 11 – 17 ч.
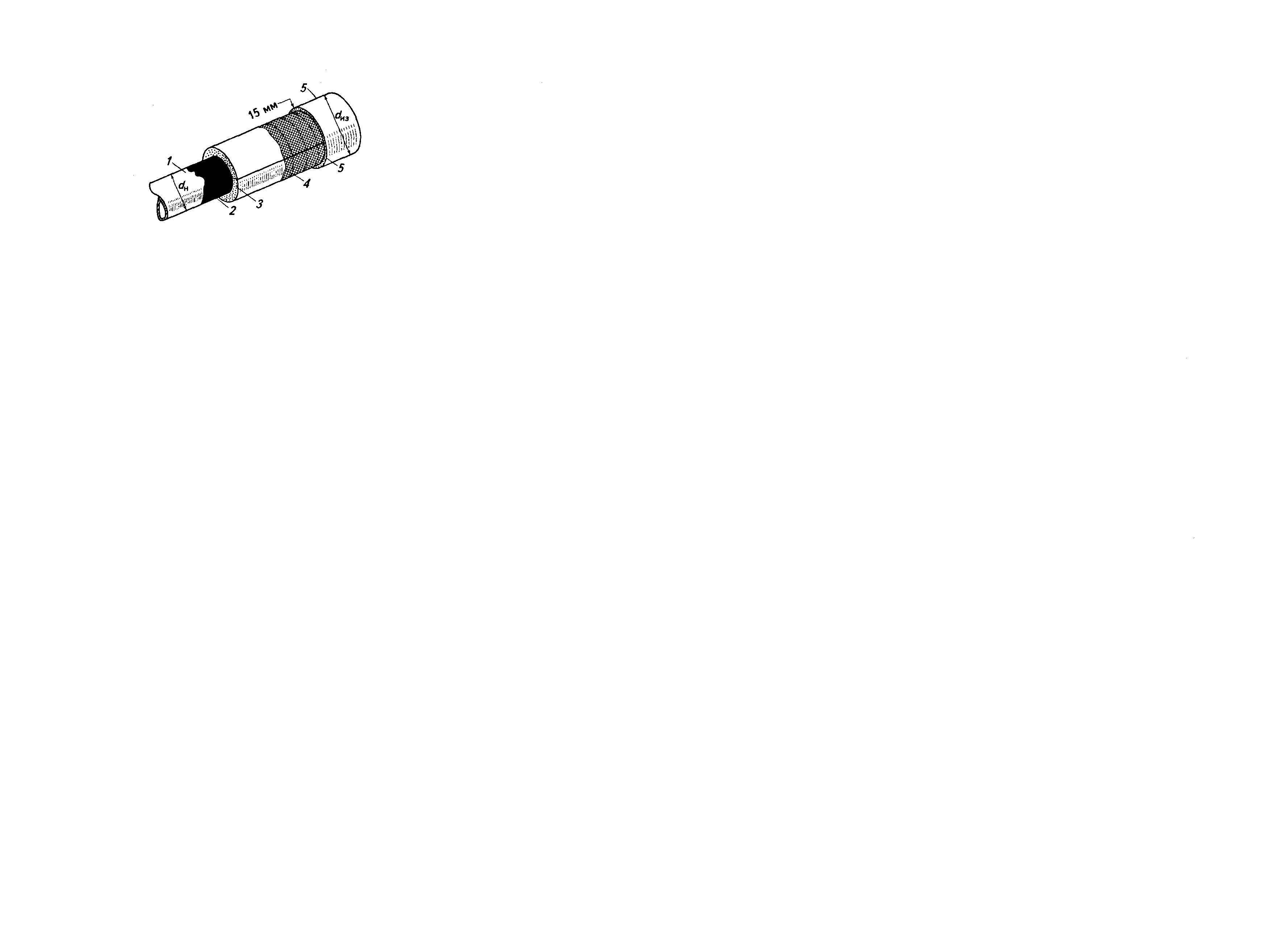
Рис. 1.20. Подвесная теплоизоляционная конструкция
1 – труба; 2 – антикоррозийное покрытие; 3 – мат из минеральной ваты; 4
– стальная сетка; 5 – асбестоцементная штукатурка
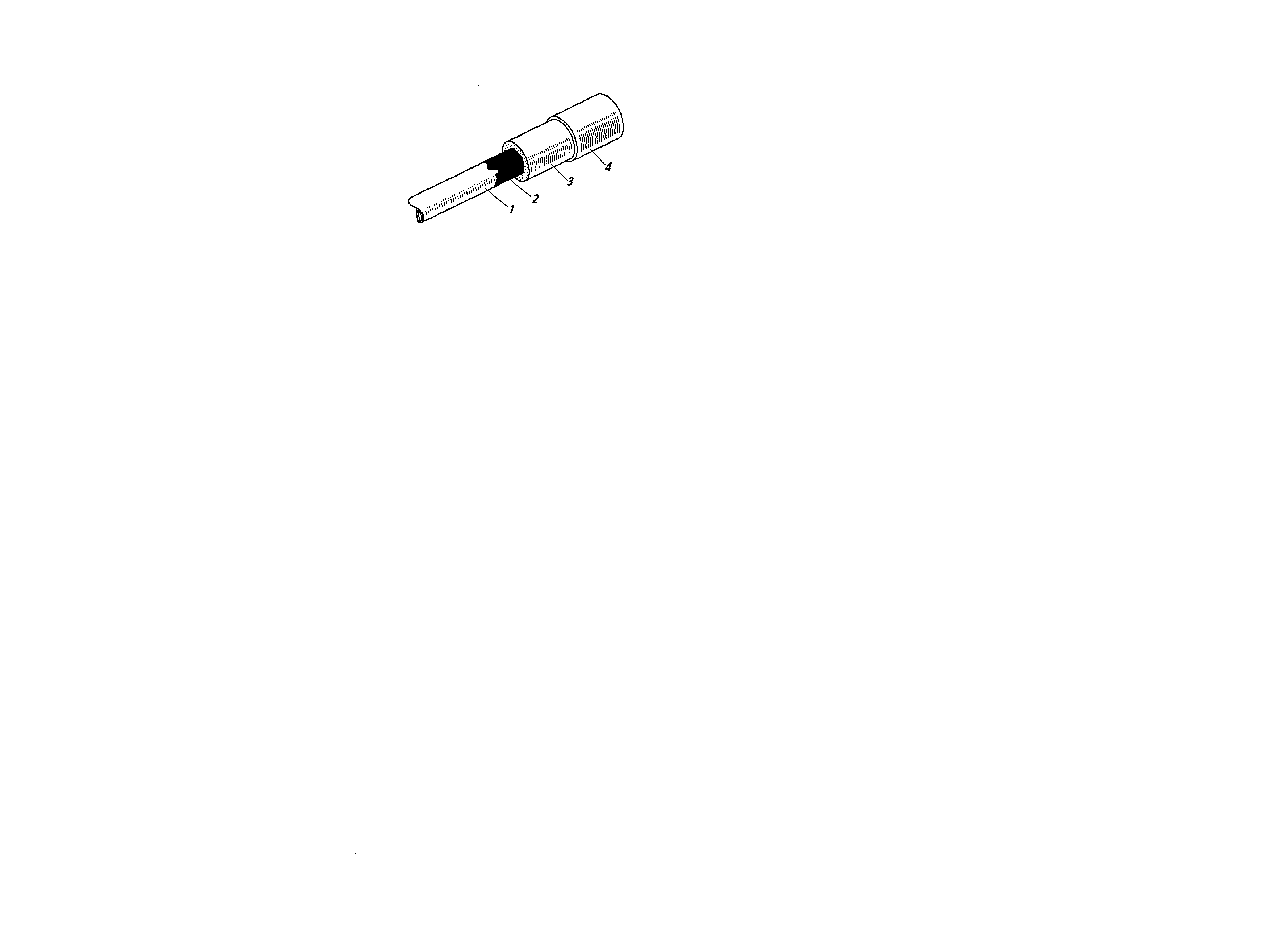
Рис.1.21. Теплоизоляционная конструкция с битумоперлитной изоляцией
1 – труба; 2 – антикоррозийное покрытие; 3 – битумоперлит;
4 – гидрозащитное покрытие из стеклоткани по лаку
Учитывая значительную хрупкость пенобетонной изоляции, ее армируют спиральным каркасом, располагаемым в наружной трети толщины изоляции.
После автоклава сушку пенобетона производят горячими газами при t = 200 0С в течение суток.
Такая конструкция получила широкое применение в прокладке распределительных и дворовых сетей.
Начиная с 1970 г. в Подмосковье (Дмитровские и Владимирские теплосети) стали применять пенополиуретановую (ППУ) изоляцию трубопроводов теплосети, изготавливаемую первоначально примитивным способом, вручную, в ремонтно - заготовительных мастерских.
Предварительно очищенную от окалины стальную трубу укладывали в корытообразный желоб (разрезанная вдоль труба большего диаметра) и закрывали таким же желобом сверху, затем в образовавшийся кольцевой зазор заливали под уклоном жидкий полимерный состав, состоящий из смеси смолы «полиизоционата» (компонент «А») и отвердителя – «полиола» (компонент «Б»). Этот состав в течение нескольких минут, реагируя, вспенивался, заполняя весь объем, затем застывал и превращался в пористую губчатую массу с закрытыми порами. В зависимости от выбранных пропорций компонентов удавалось получать изоляцию различной плотности – от мягкой структуры – поролона, до камнеподобной твердой губчатой массы, прочно схватывающейся с металлической поверхностью трубы. После завершения экзотермической реакции смеси компонентов и остывания конструкция желоба снималась, и изолированная таким образом труба шла в монтаж.
Описанная ручная технология легла в основу заводской с той разницей, что вместо самодельных коробов на заводах стали применять оболочки трубчатого типа из специально обработанного – экструдированного (для лучшего сцепления с пористой массой ППУ) полиэтилена или тонкостенных металлических труб. Улучшился также процесс предварительной механической очистки (до металлического блеска) наружной поверхности основной трубы и установлен входной и выходной заводской контроль качества продукции.
Основной трудностью в изготовлении такой изоляции до настоящего времени является острый дефицит исходных компонентов, так как отечественная химическая промышленность не в состоянии обеспечить потребности народного хозяйства (промышленности, транспорта, энергетики ВПК) и их приходится закупать по высоким ценам за рубежом. Это отражается и на цене пенополиуретановой изоляции.
Несмотря на это, в стране начали развиваться современные заводские технологии, учитывающие как отечественный, так и зарубежный опыт изоляции труб и оборудования с применением ППУ.
Современная производственная база (ЗАО «МосФлоулайн»), предоставленная российской стороной, была запроектирована и укомплектована ведущими западно - европейскими фирмами с учетом действующих на рынке технологий. Технологическое оборудование позволяет выпускать 2400 м изолированной и 60 шт. изолированных фасонных изделий в сутки. Продукция выпускается двух видов: в полиэтиленовой оболочке для подземной прокладки и в оцинкованной металлической оболочке для надземной прокладки тепловых сетей.
Для трубопроводов горячего и холодного водоснабжения в качестве рабочей трубы применяют оцинкованные трубы диаметром dу = 32 – 219 мм. Сборка оцинкованных фасонных изделий в заводских условиях выполняется цинконеразрушающим методом – пайкой.
Для тепловых сетей поставляется продукция диаметром
32 – 1220 мм со всеми фасонными изделиями. ЗАО «МосФлоулайн» пока единственное отечественное предприятие, обеспечивающее полный спектр сервисных услуг от проектирования до сдачи в эксплуатацию и выдачи 5 - летней гарантии на заводские элементы, работу по изоляции стыков и работоспособность системы оперативно - дистанционного контроля (ОДК) трубопроводов. Это пример освоения и внедрения новых технологий ХХ в.
На рис. 1.22 и рис. 1.23 показаны готовые изделия теплоизолированных трубопроводов ЗАО «МосФлоулайн», которые представляют собой жесткую конструкцию типа «труба в трубе», состоящую из стальной (рабочей) трубы, изолирующего слоя из жесткого пенополиуретана (ППУ) и внешней защитной оболочки из полиэтилена или оцинкованной стали.
Примечание. У пенополиуретановой изоляции есть существенный недостаток, о котором нужно всегда помнить – этот органический материал горюч и в процессе горения его выделяются сильнодействующие ядовитые вещества (СДЯВ), которые при пожарах являются основной причиной гибели людей. Поэтому в
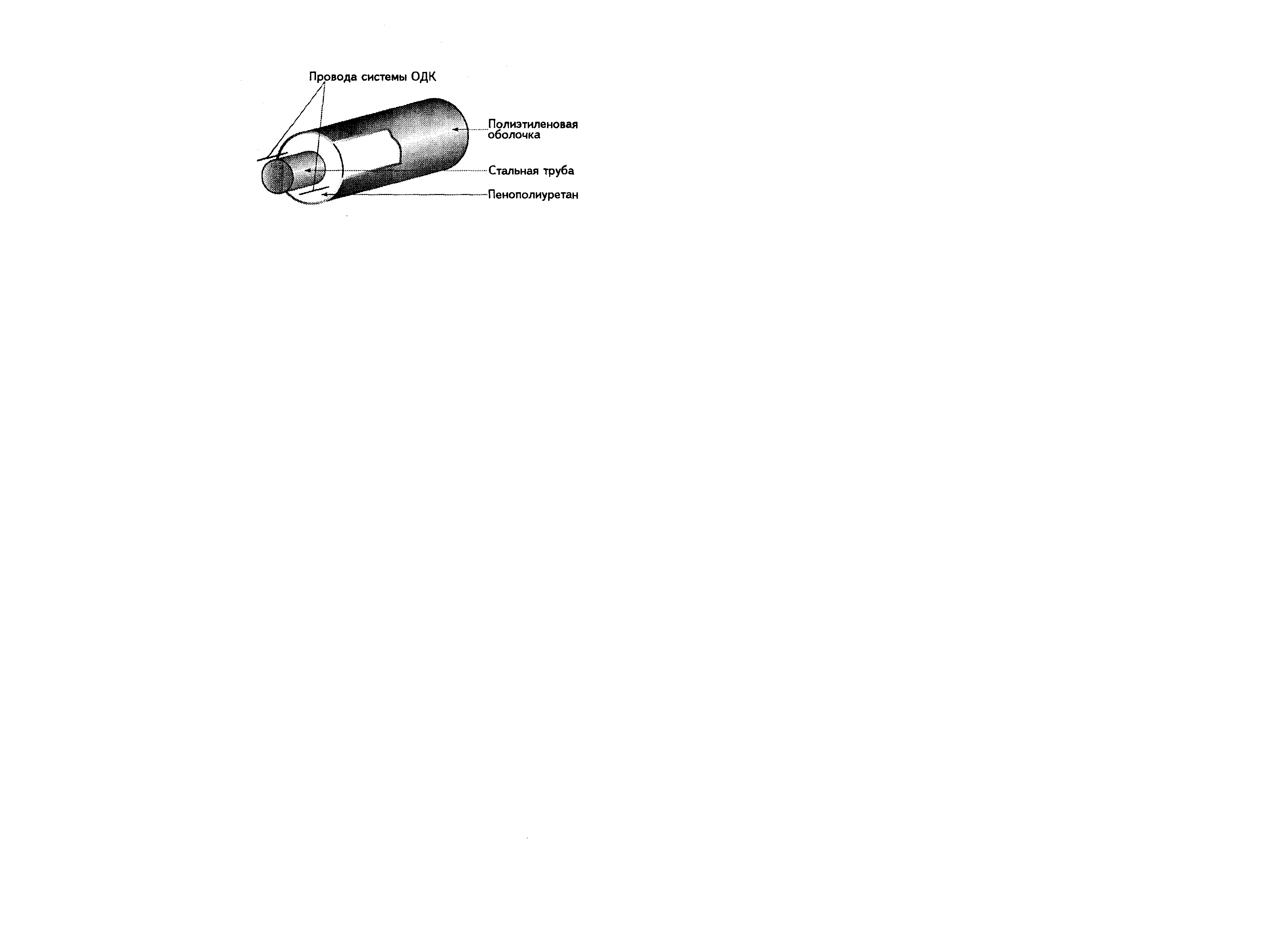
Рис .1.22.Конструкция ППУ – изоляции трубопровода по технологии ЗАО «МосФлоулайн»
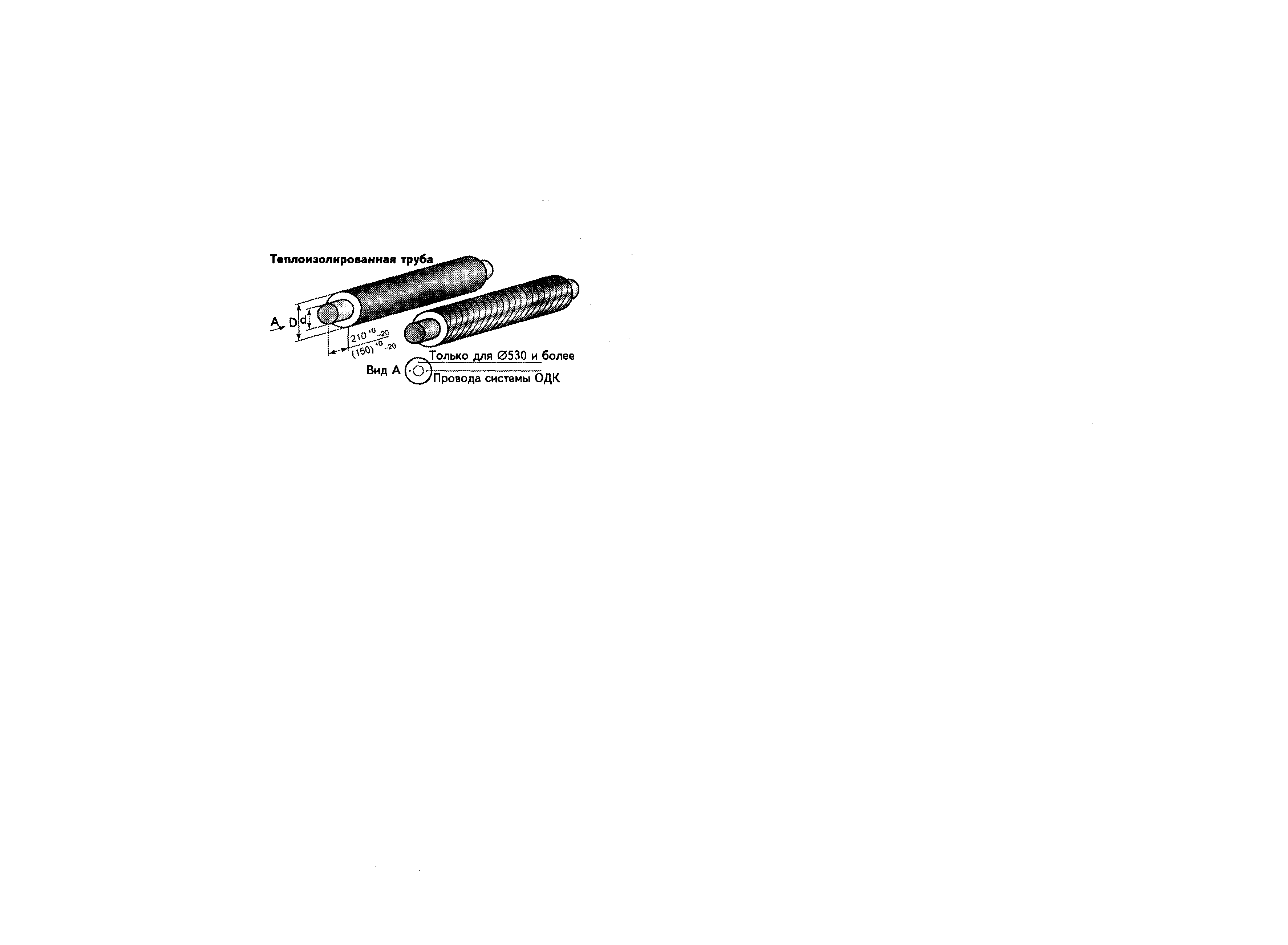
Рис. 1.23. Теплоизолированные ППУ трубы для бесканальной (в полиэтиленовой оболочке) и надземной прокладки тепловых сетей (в металлической оболочке)
подземных конструкциях тепловых сетей с ППУ изоляцией через каждые 300 м в тепловой изоляции устраивают негорючие вставки из минеральной изоляции.
1.4.4. Борьба с коррозией в системах централизованного теплоснабжения
Впервые с тяжелыми последствиями массового коррозионного поражения систем горячего и холодного водоснабжения в системе ЖКХ столкнулись в г. Москве в 1956 – 1958гг., когда системы ГВС и ХВС всех семи только что
построенных высотных зданий за 2 – 3 года эксплуатации прокорродировали до сквозных свищей и потребовали полной замены.
Замоноличенные в стенах и штробах стояки и разводки горячего и холодного водопроводов вызвали массовые протечки воды и затопление квартир и офисов.
Все это потребовало тщательного исследования процессов поражения систем и разработки защитных мер, которые легли в основу нормативных документов по строительству и эксплуатации систем ЦТ.
В формировании коррозионных отложений в трубопроводах решающую роль играют процессы кислородной коррозии, протекающей в форме электрохимической коррозии в паре «металл – вода».
Металлы, используемые при изготовлении труб, имеют в своем составе различные примеси, которые образуют ряд гальванических элементов, обуславливающих коррозию. Те частицы металла, которые являются анодами, разрушаются и переходят в раствор в виде ионов, образуя каверны и свищи.
Вследствие переменной валентности железа (двух-, трехвалентная), ионы его в коррозионном электрохимическом процессе переходят сперва в гидрат закиси железа по уравнению
Fe2+ + 2OH Fe(OH)2.
Затем при контакте с растворенным в воде кислородом гидрат закиси железа Fe(OH)2 переходит в более устойчивую форму оксида – гидрооксид железа Fe(OH)3, который отлагается на внутренней поверхности труб в виде бугристых отложений (ржавчины), по уравнению
4 Fe(OH)2 + O2 + H2O 4 Fe(OH)3.
В соответствии с этой реакцией 1 г растворенного кислорода реагирует с 2,33 г железа. Таким образом, 1 м