Файл: Федеральное агентство по образованию иркутский государственный технический университет.doc
ВУЗ: Не указан
Категория: Не указан
Дисциплина: Не указана
Добавлен: 09.12.2023
Просмотров: 863
Скачиваний: 2
ВНИМАНИЕ! Если данный файл нарушает Ваши авторские права, то обязательно сообщите нам.
СОДЕРЖАНИЕ
торцевой поверхности (при наличии пригонки)
Расчетные сопротивления срезу и растяжению болтов
Основные размеры элементов подкрановых балок
Расчетные сопротивления растяжению фундаментных болтовRba
Рис. 9.1 К определению расчетных усилий в разрезной подкрановой балке:
г – схема загружения балки одним краном для определения прогиба
По внешнему виду сварные швы должны удовлетворять следующим требованиям:
– иметь гладкую или мелкочешуйчатую поверхность (без наплывов, сужений, прожогов и перерывов) и плавный переход к основному металлу;
– наплавленный металл должен быть плотным по всей длине шва, не иметь трещин, скоплений и цепочек поверхностных пор (отдельно расположенные поры допускаются);
– подрезы основного металла, если в проекте нет дополнительных требований, допускают глубиной не более 0,5 мм при толщине свариваемого металла 4…10 мм и не более 1 мм при толщине свыше 10 мм;
– все кратеры должны быть заварены.
Металлографические исследования сварных швов стальных конструкций проводят чаще всего путем засверливания и последующего травления этих мест с целью определения качества провара и отсутствия внешних дефектов.
Химическим анализом сварных соединений (основного и наплавленного металлов) проверяют марки сталей и типы электродов, использованных для изготовления данной конструкции.
В результате механических испытаний сварных швов определяют основные прочностные характеристики при растяжении, ударную вязкость материала шва и соответствие их требованиям проекта и техническим условиям.
Испытания на статический изгиб (технологическая проба) проводят для стыковых сварных соединений (рис. 10.18). Эти испытания определяют квазистатическую вязкость сварного соединения, характеризующуюся углом загиба до образования первой трещины в растянутой зоне образца. Для хороших швов угол загиба α достигает 180о.
Физическим способам контроля качества шва подвергаются швы, принятые по внешнему виду и не имеющие внешних дефектов.
К наиболее часто используемым физическим способам контроля относятся ультразвуковая дефектоскопия, радиационный контроль с просвечиванием рентгеновскими лучами и гамма-лучами, магнитный метод.
Физические способы контроля предназначены для выявления в сварном шве и околошовной зоне внутренних и внешних дефектов, недоступных для внешнего осмотра.
Метод ультразвуковой дефектоскопии основан на том, что ультразвуковые колебания прямолинейно распространяются в металле и отражаются от границы раздела сред, имеющих различные акустические свойства.
Радиационный метод контроля с просвечиванием рентгеновскими или гамма-лучами основан на том, что проницаемость указанных лучей для различных материалов неодинаковая. Поэтому дефектные места шва (поры, трещины, непровары) пропускают такие лучи с меньшим поглощением, чем основной металл, благодаря чему такие участки выглядят как более яркие пятна на рентгеновской пленке или других запоминающих изображение слоях.
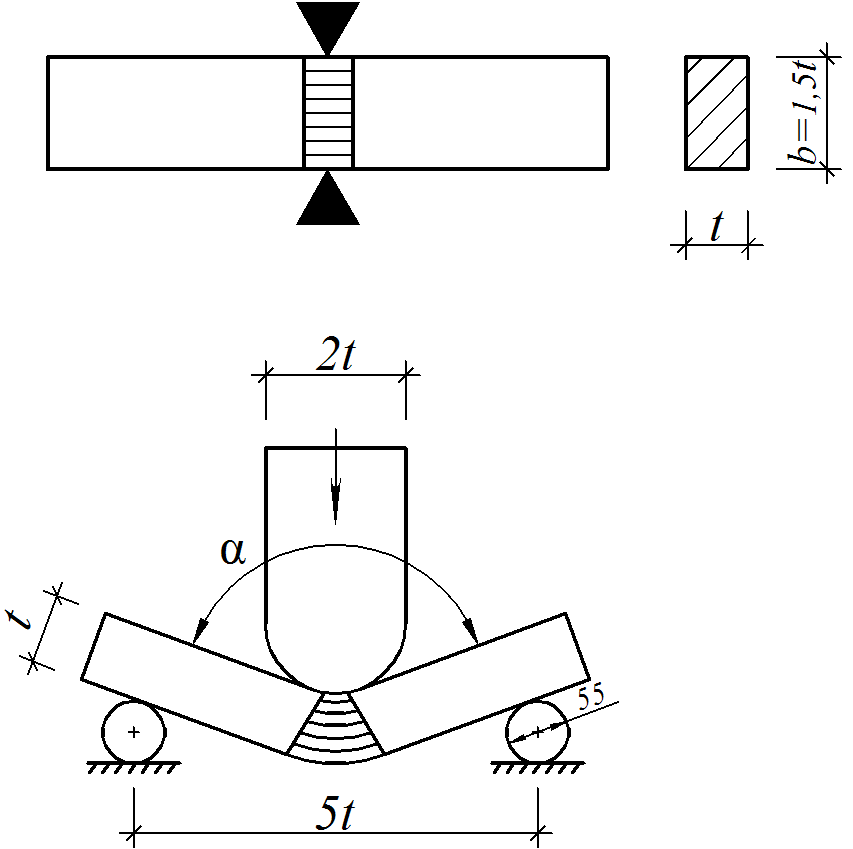
Рис. 10.18. Испытание металла шва на изгиб
Метод магнитной дефектоскопии основан на неодинаковой магнитной проницаемости α-железа и других фаз. В отличие от равномерного распределения магнитных потоков на участке сварного соединения без дефектов в шве с дефектом магнитный силовой поток будет огибать его, создавая магнитные потоки рассеивания.
Выбор методов и объемов неразрушающего контроля качества сварных соединений осуществляется проектной организацией, которая указывает их в конструкторской документации, согласованной с заводом-изготовителем и монтажной организацией.
10.1.12. Техника безопасности при электродуговых
способах сварки
1. Во избежание поражения электрическим током необходимо соблюдать следующие условия: сварочные провода должны иметь надежную изоляцию; рубильники для включения электрического тока должны иметь заземленные защитные кожухи; руки и рукавицы, обувь и одежда должны быть всегда сухими; провода не должны находиться в воде.
2. Ультрафиолетовое излучение дуги вызывает ожог кожи и поражение сетчатки глаз. Для защиты тела от влияния лучей сварщики и их подручные во время работы должны надевать брезентовые спецодежду и рукавицы, лицо закрывать специальным шлемом или щитком из малотеплопроводного, невоспламеняющегося от искр и не пропускающего ультрафиолетовые лучи материала. Если шлем или щиток имеют щели или трещины в стеклах, работать в них не разрешается. Нельзя смотреть самому или разрешать другим смотреть на электрическую дугу незащищенными глазами, а также через очки и стекла без специальной защиты.
3. В процессе сварки открытой дугой брызги и капли расплавленного металла могут попасть в складки одежды, карманы, ботинки, прожечь ткань одежды и причинить ожоги. Во избежание ожогов каплями жидкого металла сварщик должен быть одет в брезентовую спецодежду, работать в рукавицах и головном уборе. Рукавицы защищают руки не только от искр, но и от соприкосновения с горячим изделием после сварки. Карманы должны плотно закрываться клапанами. Не следует заправлять куртку в брюки, их надо носить поверх обуви. Ботинки должны быть с глухим верхом и плотно зашнурованы. В спецодежде, щитке или шлеме не должно быть отверстий. Куртка должна застегиваться на все пуговицы. При сварке вертикальных и горизонтальных швов следует надевать брезентовые нарукавники, завязывая их у кистей.
4. При всех видах дуговой сварки выделяется большое количество вредных газов и пыли. Выполнять дуговую сварку можно только при работающей вентиляции. Для уменьшения количества вредных газов и пыли применяют местную и общую вентиляции.
5. При поражении электрическим током человека необходимо:
– обесточить пострадавшего, немедленно выключив рубильником ток первичной цепи или используя сухие подручные материалы, не касаясь пострадавшего;
– обеспечить доступ к нему воздуха;
– экстренно вызвать скорую медицинскую помощь;
– при необходимости, не ожидая врача, сделать искусственное дыхание и массаж сердца.
10.1.13. Виды сварных соединений
По конструкции различают следующие сварные соединения: стыковые, нахлесточные, тавровые, угловые, комбинированные (табл. 10.8).
Стыковыми называются соединения, в которых элементы соединяются торцами или кромками и один элемент является продолжением другого. Место их соединения (зазор) заполняется сварным швом. Стыковые соединения наиболее рациональны и надежны, так как имеют наименьшую концентрацию напряжений при передаче усилий, отличаются экономичностью и удобны для контроля.
Толщина свариваемых элементов в соединениях такого вида почти не ограничена. Стыковое соединение листового металла может быть сделано
Таблица 1.8
Виды сварных соединений
Стыковые | Нахлесточные | Комбинирован- ные | Тавровые | Угловые | ||
угловыми швами | точечной сваркой | |||||
без накладок | с накладками | |||||
![]() ![]() | ![]() | ![]() | ![]() | ![]() | ![]() | ![]() |
прямым или косым швом. Стыковые соединения профильного металла применяются реже, так как затруднена обработка их кромок под сварку.
Сварные стыковые соединения листовых деталей, как правило, проектируют прямыми с полным проваром и с применением выводных планок. В монтажных условиях допускается односторонняя сварка с подваркой корня и сварка на остающейся стальной подкладке.
При соединении стальных листов различной толщины (или ширины) их размеры в месте стыка должны быть одинаковыми во избежание резкого изменения сечения. Для этого в более толстом (или широком) элементе устраивается скос с уклоном 1:5 с одной или двух сторон до толщины тонкой детали (рис. 10.19).
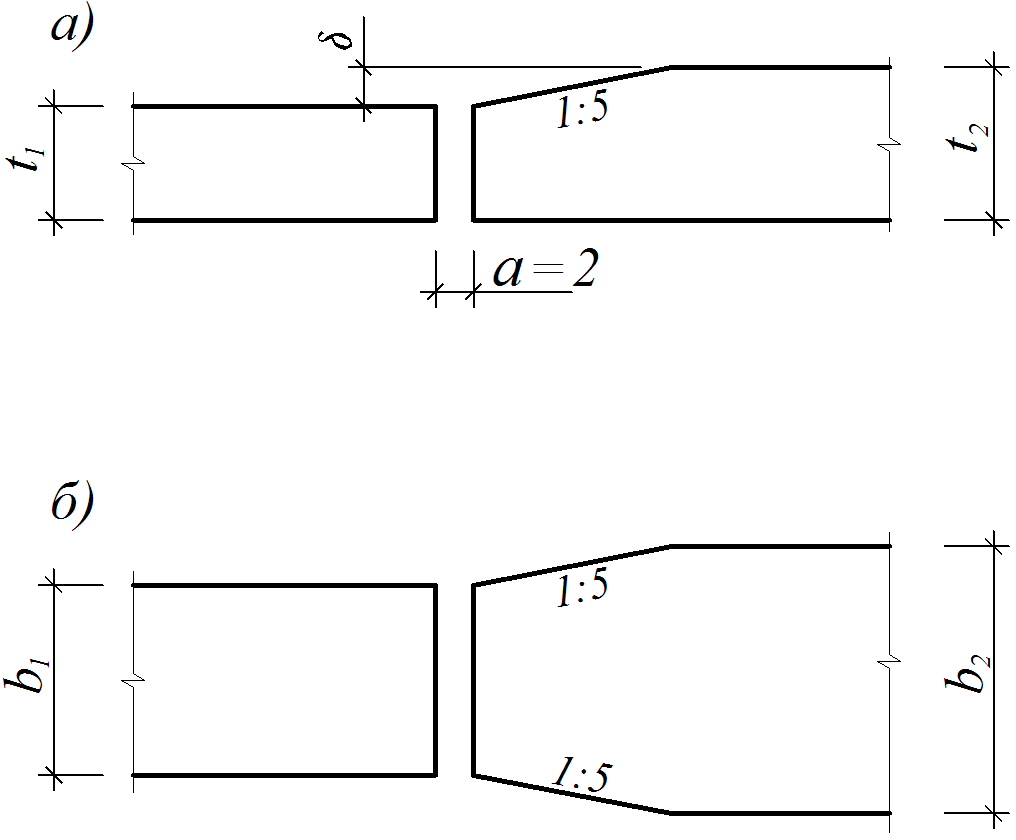
Рис. 10.19. Соединение элементов:
а – при разной толщине; б – при разной ширине
Длиной скоса листа регулируют плавный переход от толстой свариваемой детали к более тонкой, кроме того, длиной скоса устраняют концентраторы напряжений в сварных конструкциях. Стыки без скосов по толщине допускаются в деталях из углеродистой или низколегированной сталей с пределом текучести до 400 МПа при разнице толщин
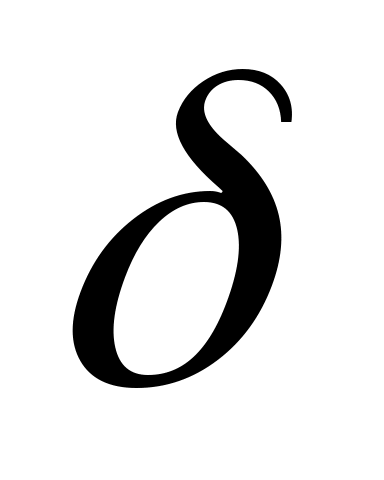
Нахлесточные соединенияминазываются такие, в которых поверхности свариваемых элементов частично находят друг на друга. Разновидностью соединений внахлестку являются соединения с накладками. Их применяют с одной или двумя накладками. Накладки служат для соединения частей изделия. Соединения внахлестку выполняются угловыми швами. Они отличаются
Таблица 10.9
Допустимая наибольшая разность толщин деталей,
свариваемых встык без скоса кромок
Толщина тонкой деталиt1, мм | Разность толщин деталей ![]() |
1…4 5…20 21…30 Св. 30 | 1 2 3 4 |
простотой обработки элементов под сварку, обеспечивают возможность подгонки размеров за счет регулирования величины нахлестки, но по расходу металла менее экономичны