Файл: Учебный курс для студентов очной и заочной форм обучения.doc
ВУЗ: Не указан
Категория: Не указан
Дисциплина: Не указана
Добавлен: 11.12.2023
Просмотров: 927
Скачиваний: 6
ВНИМАНИЕ! Если данный файл нарушает Ваши авторские права, то обязательно сообщите нам.
Б = 1,8 для подвижного состава),
КТ – коэффициент температурного режима (до 100оС КТ =1).
Грузоподъёмность это постоянная нагрузка, которую группа идентичных подшипников выдержит в течение одного миллиона оборотов. Здесь для радиальных и радиально упорных подшипников подразумевается радиальная нагрузка, а для упорных и упорно-радиальных - центральная осевая нагрузка. Если вал вращается медленнее одного оборота в минуту, то речь идёт о статической грузоподъёмности C0, а если вращение быстрее одного оборота в минуту, то говорят о динамической грузоподъёмности C. Величина грузоподъёмности рассчитывается при проектировании подшипника, определяется на экспериментальной партии подшипников и заносится в каталог.
Методика выбора подшипников качения
Опытный проектировщик может назначать конкретный тип и размер подшипника, а затем делать проверочный расчёт. Однако здесь требуется большой конструкторский опыт, ибо в случае неудачного выбора может не выполниться условие прочности, тогда потребуется выбрать другой подшипник и повторить проверочный расчёт.
Во избежание многочисленных "проб и ошибок" можно предложить методику выбора подшипников, построенную по принципу проектировочного расчёта, когда известны нагрузки, задана требуемая долговечность, а в результате определяется конкретный типоразмер подшипника из каталога.
Методика выбора состоит из пяти этапов:
1. Вычисляется требуемая долговечность подшипника исходя из частоты вращения и заданного заказчиком срока службы машины.
2. По найденным ранее реакциям опор выбирается тип подшипника (радиальный, радиально-упорный, упорно-радиальный или упорный), из справочника находятся коэффициенты радиальной и осевой нагрузок Х, У.
3. Рассчитывается эквивалентная динамическая нагрузка.
4. Определяется требуемая грузоподъёмность C =P*L(1/α).
5. По каталогу, исходя из требуемой грузоподъёмности, выбирается конкретный типоразмер ("номер") подшипника, причём должны выполняться два условия:
грузоподъёмность по каталогу не менее требуемой;
внутренний диаметр подшипника не менее диаметра вала.
Особенности проектирования подшипниковых узлов
Неточность монтажа, нагрев, деформации вала могут привести к заклиниванию вращающихся колёс, что, особенно в момент движения, чревато весьма неприятными последствиями. Предотвращение этого достигается различными мероприятиями:
Схемы установки подшипников
Применяют фиксированные и плавающие опоры. В фиксированных внутренние и наружные кольца неподвижны в осевом направлении. В плавающих внешнее кольцо может перемещаться в осевом направлении за счёт установки подшипника в специальном стакане с зазором. Плавающей обычно делают ту опору, где меньше радиальная нагрузка. При большом расстоянии между опорами (вал червяка) фиксированная опора для жёсткости имеет два подшипника. Для свободных температурных перемещений подходят радиальные роликоподшипники с цилиндрическими роликами и радиальные шарикоподшипники с незакреплёнными наружными кольцами.
К
ороткие валы при слабом нагреве можно устанавливать на подшипники враспор, когда один подшипник фиксирует осевое смещение вала в одну сторону, а другой – в другую. Схема с фиксацией подшипников враспор удобна в монтаже, но требует жёстких допусков на линейные размеры и опасна возможным защемлением тел качения при нагреве. При установке враспор для радиальных подшипников оставляют осевой зазор, а для радиально-упорных предусматривают осевую регулировку.
Крепление подшипников на валу и в корпусе
Для восприятия осевых нагрузок кольца подшипника закрепляют на валу и в корпусе.
Для закрепления внутренних колец на валу применяются различные средства:
уступы вала (а);
пружинные стопорные кольца (б,е);
торцовые шайбы (в);
упорные гайки (г,ж);
конические разрезные втулки (д,з).
Для фиксации наружных колец применяют:
уступы в корпусе и стакане (а);
крышки (б);
крышки и уступы (в,г);
упорные борта (д);
врезные крышки при разъёмных корпусах (е);
пружинные кольца (ж,з).
Радиально-упорные подшипники требуют осевого регулирования, которое делается смещением наружного кольца:
прокладками из металла (а);
крепёжным винтом (б,г) при малых осевых силах;
резьбовой крышкой или кольцом (в).
Жёсткость подшипников и их предварительный натяг
Деформации подшипников качения примерно равны деформациям валов. Поддержание высокой жёсткости подшипниковых узлов обеспечивает точность вращения системы. Максимальную жёсткость имеют точные роликоподшипники.
Жёсткость увеличивается предварительным натягом, суть которого в выборке зазоров и начальном сжатии тел качения. Это достигается взаимным осевым смещением колец посредством:
затяжки резьбы (а);
пружинами (б);
установкой втулок (в);
шлифовкой торцов колец (г).
Излишний преднатяг приводит к усилению износа сепаратора из-за набегания на него части тел качения и отставания другой части в связи с разными их диаметрами.
Уплотняющие устройства
Это специальные детали, выполненные из мягких упругих материалов (мягкие металлы, резина, пластмасса, войлок и т.п.), которые предотвращают вытекание смазки из подшипниковых узлов и попадание в них загрязнения.
По принципу действия уплотнения разделяются на:
контактные манжетные, войлочные, с металлическими кольцами (а,б), применяются на низких и средних скоростях, дают плотный контакт подвижных и неподвижных деталей;
щелевые и лабиринтные, препятствуют протеканию жидкостей и даже газа через каскад щелей и камер (в,г,д,е), так, типовая букса грузового вагона имеет четырёхкамерное лабиринтное уплотнение с зазором 0,8 мм;
центробежные (ж,з);
комбинированные.
Известны конструкции подшипников со встроенными уплотнениями.
Посадки подшипников на вал и в корпус
При проектировании подшипниковых узлов принципиальное значение имеет сопряжение (посадка) внутренних колец с валом и наружных с корпусом. Поскольку
подшипники являются стандартными узлами, то валы и корпуса должны приспосабливаться к ним. Внутренние кольца сажают на вал по системе отверстия, а наружные в корпус по системе вала. При том, что поле допусков внутреннего кольца направлено не в тело, а к центру, посадки на вал получаются более плотными, чем обычно в системе отверстия.
В зависимости от режима работы машины, чем больше нагрузка и сильнее толчки, тем более плотными должны быть посадки. Чем быстроходнее машина (меньше нагрузки, выше температуры), тем посадки должны быть свободнее.
Посадки роликоподшипников должны быть более плотными в связи с большими нагрузками. Посадки радиально-упорных подшипников плотнее, чем у радиальных, у которых посадочные натяги искажают зазоры. Посадки крупных подшипников из-за больших сил назначают плотнее, чем у средних и мелких. Рекомендации по выбору посадок по мере роста нагрузок в опорах можно сформулировать следующим образом:
Допуски валов при вращающемся вале – js6; k6;m6;n6.
Допуски валов при вращающемся корпусе – g6; h6.
Допуски корпуса при вращающемся вале – H7; H6; Js7; Js6; K7.
Допуски корпуса при вращающемся корпусе – K7; M7; N7; P7.
Монтаж и демонтаж подшипников
Нередко наблюдаются случаи, когда повреждения подшипников вызваны небрежным, безграмотным монтажом и демонтажом.
П
одшипники со значительным натягом на валу следует монтировать нагретыми в масле или охлаждать вал сухим льдом. В остальных случаях подшипники можно напрессовывать на вал с помощью пресса.
Посадка подшипника ударами молотка через оправку из мягкого металла допустима только при малых натягах для мелких и средних подшипников. Демонтаж допускается только с помощью специальных съёмников.
Общий принцип: усилие прикладывается только к тому кольцу, которое установлено с натягом и не должно передаваться на тела качения.
Смазка подшипников качения
Применяется как для снижения трения, так и для повышения теплоотвода.
Пластичные (густые) смазки более легки в обслуживании, меньше расходуются, удобны в применении в труднодоступных местах, куда закладываются при сборке, заполняют и герметизируют зазоры. Их недостаток в том, что в конструкции требуется предусматривать специальные полости. Эту полость первоначально заполняют на 2/3 объёма при n 1500 об/мин или на 1/2 объёма при n > 1500 об/мин. В дальнейшем обычно через каждые три месяца через специальные устройства (пресс-маслёнки) добавляют свежую смазку, а через год её меняют с предварительной разборкой и промывкой узла. При консистентной смазке необходимо применение щелевых, лабиринтных и центробежных уплотнений.
Жидкие смазки применяются при более высоких температурах, когда густые плавятся и вытекают. Обеспечивают минимальные потери на трение. Обычный способ в случае нижнего расположения червяка – организация масляных ванн (например, картер двигателя и т.п.), в которых масло налито до уровня нижнего тела качения. В зубчатых передачах колёса погружают не более чем на высоту зуба, во избежание больших потерь на перемешивание масла. Уровень масла контролируется щупом-маслоуказателем, как, например, в двигателях легковых автомобилей.
Разбрызгивание масла внутри корпуса механизмов происходит с помощью специальных лопастей-крыльчаток либо зубчатых колёс и применяется для создания масляного тумана, который способствует выравниванию температуры и теплоотводу от механизма. Однако проектировщику не следует надеяться на то, что разбрызгиванием будут достаточно смазаны подшипники, находящиеся выше уровня масляной ванны.
Вопросы для самопроверки
1. Что показано на рисунке?
1. Подшипники качения
2. Подшипники вращения
3. Шарики и ролики
4. Что-то странное
2. Что показано на рисунке?
КТ – коэффициент температурного режима (до 100оС КТ =1).
Грузоподъёмность это постоянная нагрузка, которую группа идентичных подшипников выдержит в течение одного миллиона оборотов. Здесь для радиальных и радиально упорных подшипников подразумевается радиальная нагрузка, а для упорных и упорно-радиальных - центральная осевая нагрузка. Если вал вращается медленнее одного оборота в минуту, то речь идёт о статической грузоподъёмности C0, а если вращение быстрее одного оборота в минуту, то говорят о динамической грузоподъёмности C. Величина грузоподъёмности рассчитывается при проектировании подшипника, определяется на экспериментальной партии подшипников и заносится в каталог.
Методика выбора подшипников качения
Опытный проектировщик может назначать конкретный тип и размер подшипника, а затем делать проверочный расчёт. Однако здесь требуется большой конструкторский опыт, ибо в случае неудачного выбора может не выполниться условие прочности, тогда потребуется выбрать другой подшипник и повторить проверочный расчёт.
Во избежание многочисленных "проб и ошибок" можно предложить методику выбора подшипников, построенную по принципу проектировочного расчёта, когда известны нагрузки, задана требуемая долговечность, а в результате определяется конкретный типоразмер подшипника из каталога.
Методика выбора состоит из пяти этапов:
1. Вычисляется требуемая долговечность подшипника исходя из частоты вращения и заданного заказчиком срока службы машины.
2. По найденным ранее реакциям опор выбирается тип подшипника (радиальный, радиально-упорный, упорно-радиальный или упорный), из справочника находятся коэффициенты радиальной и осевой нагрузок Х, У.
3. Рассчитывается эквивалентная динамическая нагрузка.
4. Определяется требуемая грузоподъёмность C =P*L(1/α).
5. По каталогу, исходя из требуемой грузоподъёмности, выбирается конкретный типоразмер ("номер") подшипника, причём должны выполняться два условия:
грузоподъёмность по каталогу не менее требуемой;
внутренний диаметр подшипника не менее диаметра вала.
Особенности проектирования подшипниковых узлов
Неточность монтажа, нагрев, деформации вала могут привести к заклиниванию вращающихся колёс, что, особенно в момент движения, чревато весьма неприятными последствиями. Предотвращение этого достигается различными мероприятиями:
Схемы установки подшипников
Применяют фиксированные и плавающие опоры. В фиксированных внутренние и наружные кольца неподвижны в осевом направлении. В плавающих внешнее кольцо может перемещаться в осевом направлении за счёт установки подшипника в специальном стакане с зазором. Плавающей обычно делают ту опору, где меньше радиальная нагрузка. При большом расстоянии между опорами (вал червяка) фиксированная опора для жёсткости имеет два подшипника. Для свободных температурных перемещений подходят радиальные роликоподшипники с цилиндрическими роликами и радиальные шарикоподшипники с незакреплёнными наружными кольцами.
К
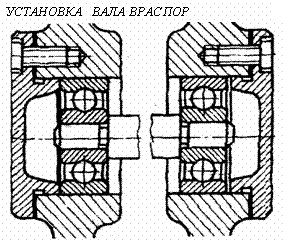
Крепление подшипников на валу и в корпусе
Для восприятия осевых нагрузок кольца подшипника закрепляют на валу и в корпусе.
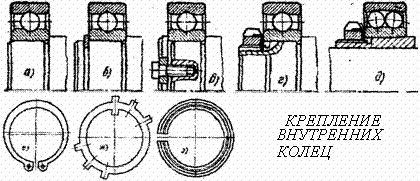
Для закрепления внутренних колец на валу применяются различные средства:
уступы вала (а);
пружинные стопорные кольца (б,е);
торцовые шайбы (в);
упорные гайки (г,ж);
конические разрезные втулки (д,з).
Для фиксации наружных колец применяют:
уступы в корпусе и стакане (а);
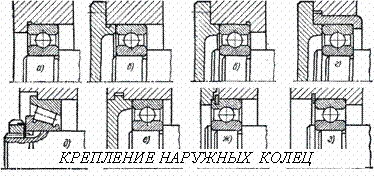
крышки (б);
крышки и уступы (в,г);
упорные борта (д);
врезные крышки при разъёмных корпусах (е);
пружинные кольца (ж,з).
Радиально-упорные подшипники требуют осевого регулирования, которое делается смещением наружного кольца:
прокладками из металла (а);
крепёжным винтом (б,г) при малых осевых силах;
резьбовой крышкой или кольцом (в).
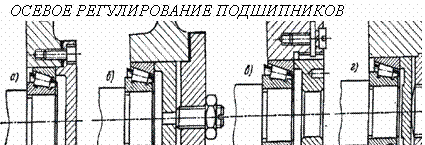
Жёсткость подшипников и их предварительный натяг
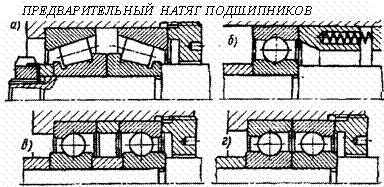
Деформации подшипников качения примерно равны деформациям валов. Поддержание высокой жёсткости подшипниковых узлов обеспечивает точность вращения системы. Максимальную жёсткость имеют точные роликоподшипники.
Жёсткость увеличивается предварительным натягом, суть которого в выборке зазоров и начальном сжатии тел качения. Это достигается взаимным осевым смещением колец посредством:
затяжки резьбы (а);
пружинами (б);
установкой втулок (в);
шлифовкой торцов колец (г).
Излишний преднатяг приводит к усилению износа сепаратора из-за набегания на него части тел качения и отставания другой части в связи с разными их диаметрами.
Уплотняющие устройства
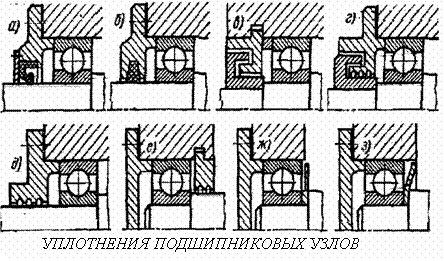
Это специальные детали, выполненные из мягких упругих материалов (мягкие металлы, резина, пластмасса, войлок и т.п.), которые предотвращают вытекание смазки из подшипниковых узлов и попадание в них загрязнения.
По принципу действия уплотнения разделяются на:
контактные манжетные, войлочные, с металлическими кольцами (а,б), применяются на низких и средних скоростях, дают плотный контакт подвижных и неподвижных деталей;
щелевые и лабиринтные, препятствуют протеканию жидкостей и даже газа через каскад щелей и камер (в,г,д,е), так, типовая букса грузового вагона имеет четырёхкамерное лабиринтное уплотнение с зазором 0,8 мм;
центробежные (ж,з);
комбинированные.
Известны конструкции подшипников со встроенными уплотнениями.
Посадки подшипников на вал и в корпус
При проектировании подшипниковых узлов принципиальное значение имеет сопряжение (посадка) внутренних колец с валом и наружных с корпусом. Поскольку
подшипники являются стандартными узлами, то валы и корпуса должны приспосабливаться к ним. Внутренние кольца сажают на вал по системе отверстия, а наружные в корпус по системе вала. При том, что поле допусков внутреннего кольца направлено не в тело, а к центру, посадки на вал получаются более плотными, чем обычно в системе отверстия.
| |
| ![]() |
В зависимости от режима работы машины, чем больше нагрузка и сильнее толчки, тем более плотными должны быть посадки. Чем быстроходнее машина (меньше нагрузки, выше температуры), тем посадки должны быть свободнее.
Посадки роликоподшипников должны быть более плотными в связи с большими нагрузками. Посадки радиально-упорных подшипников плотнее, чем у радиальных, у которых посадочные натяги искажают зазоры. Посадки крупных подшипников из-за больших сил назначают плотнее, чем у средних и мелких. Рекомендации по выбору посадок по мере роста нагрузок в опорах можно сформулировать следующим образом:
Допуски валов при вращающемся вале – js6; k6;m6;n6.
Допуски валов при вращающемся корпусе – g6; h6.
Допуски корпуса при вращающемся вале – H7; H6; Js7; Js6; K7.
Допуски корпуса при вращающемся корпусе – K7; M7; N7; P7.
Монтаж и демонтаж подшипников
Нередко наблюдаются случаи, когда повреждения подшипников вызваны небрежным, безграмотным монтажом и демонтажом.
П
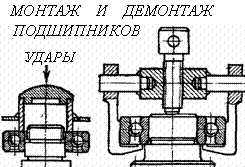
Посадка подшипника ударами молотка через оправку из мягкого металла допустима только при малых натягах для мелких и средних подшипников. Демонтаж допускается только с помощью специальных съёмников.
Общий принцип: усилие прикладывается только к тому кольцу, которое установлено с натягом и не должно передаваться на тела качения.
Смазка подшипников качения
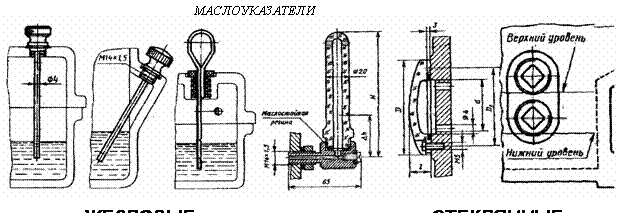
Применяется как для снижения трения, так и для повышения теплоотвода.
Пластичные (густые) смазки более легки в обслуживании, меньше расходуются, удобны в применении в труднодоступных местах, куда закладываются при сборке, заполняют и герметизируют зазоры. Их недостаток в том, что в конструкции требуется предусматривать специальные полости. Эту полость первоначально заполняют на 2/3 объёма при n 1500 об/мин или на 1/2 объёма при n > 1500 об/мин. В дальнейшем обычно через каждые три месяца через специальные устройства (пресс-маслёнки) добавляют свежую смазку, а через год её меняют с предварительной разборкой и промывкой узла. При консистентной смазке необходимо применение щелевых, лабиринтных и центробежных уплотнений.
Жидкие смазки применяются при более высоких температурах, когда густые плавятся и вытекают. Обеспечивают минимальные потери на трение. Обычный способ в случае нижнего расположения червяка – организация масляных ванн (например, картер двигателя и т.п.), в которых масло налито до уровня нижнего тела качения. В зубчатых передачах колёса погружают не более чем на высоту зуба, во избежание больших потерь на перемешивание масла. Уровень масла контролируется щупом-маслоуказателем, как, например, в двигателях легковых автомобилей.
Разбрызгивание масла внутри корпуса механизмов происходит с помощью специальных лопастей-крыльчаток либо зубчатых колёс и применяется для создания масляного тумана, который способствует выравниванию температуры и теплоотводу от механизма. Однако проектировщику не следует надеяться на то, что разбрызгиванием будут достаточно смазаны подшипники, находящиеся выше уровня масляной ванны.
Вопросы для самопроверки
1. Что показано на рисунке?
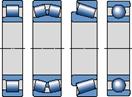
1. Подшипники качения
2. Подшипники вращения
3. Шарики и ролики
4. Что-то странное
2. Что показано на рисунке?
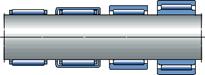