Файл: Изложение на 80 листах, приложение альбомчертежей и плокатов на 10 листах формата А1, альбом технологической документации. Содержание.docx
ВУЗ: Не указан
Категория: Не указан
Дисциплина: Не указана
Добавлен: 11.12.2023
Просмотров: 142
Скачиваний: 1
ВНИМАНИЕ! Если данный файл нарушает Ваши авторские права, то обязательно сообщите нам.
Подвергать входному контролю все материалы и заготовки поступающие на участок сборки сварки емкости. Качество исходных материалов (основного металла, сварочной проволоки, геометрические характеристики заготовок и.т.д.) на соответствие НТД и сертификатов. Если нет гарантии изготовителей, либо качество исходных материалов внушает опасения, то их дополнительно проверять на соответствие НТД и ГОСТ.
Проводить контроль технического уровня и состояния оборудования, согласно графику технического обслуживания, проводить периодические проверки оборудования на соответствие техническим нормам. В сварочных аппаратах проверять исправность регулирующих механизмов, наличие контролирующих приборов, исправность токопроводящих элементов, состояние электрических контактов, и.т.д. Периодически проводить аттестацию сборщиков, сварщиков, дефектоскопистов.
Качество подготовки и сборки заготовок под сварку проверять внешним осмотром и замерами. На предмет недопустимо больших и неравномерных зазоров, серповидности, вмятин, неправильных углов разделки кромок, их окисленность, загрязненность. Для измерения зазоров, углов разделки применять линейки, шаблоны специальные или универсальные. Строгий контроль заготовок и сборки во многом обеспечивает высокое качество сварки.
Подвергать контролю режимы сварки для соблюдения параметров процесса (св. тока, напряжения и скорости сварки в установленных пределах). Используя визуальное наблюдение по приборам и по внешнему виду шва.
После сварки изделие обязательно п
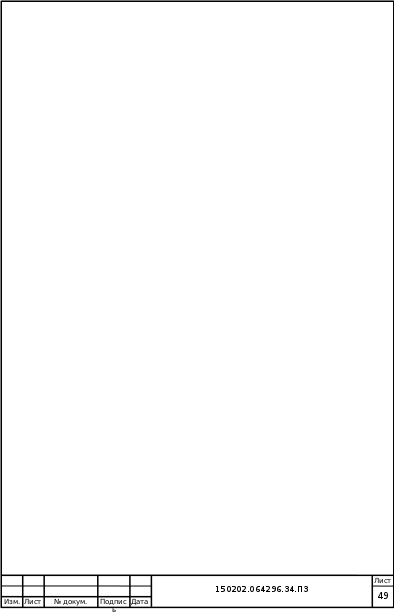
Прежде всего, внешним осмотром невооруженным глазом или в лупу проверяют наличие трещин, подрезов, свищей, прожогов, натеков, не проваров корня и кромок. Некоторые из указанных дефектов недопустимы и подлежат вырубке и заварке. При осмотре также определяют дефекты формы швов, распределение чешуек, характер распределения металла в усилении шва, величину проплава. Внешний вид поверхности шва характерен для каждого способа сварки, а также для пространственного положения, в котором производилась сварка. Неравномерная чешуйчатость, разная ширина и высота шва указывают на колебания мощности дуги, частые ее обрывы и неустойчивость горения. Допущенные дефекты при подготовке и сборке приводят к появлению сварочных дефектов. Наиболее характерные дефекты этого типа: неправильный угол скоса кромок в швах; слишком большое или малое притупление по длине стыкуемых кромок; непостоянство зазора между кромками; несовпадение стыкуемых плоскостей кромок; расслоения и загрязнения на кромках и т. п.
Причинами подобных дефектов могут быть неисправности оборудования, применяемого для изготовления заготовок и приспособлений для сборки, недоброкачественность исходных материалов, низкая квалификация обслуживающего персонала.
До начала сварных работ изготовить контрольный образец согласно ОСТ26-291-94 и направить на механические испытания. Контрольный образец изготавливается на партию до 24 единиц. Полученные результаты механических разнородных сталей контрольных сварных образцов принимать по стали, имеющей меньшие величины механических свойств.
Для обнаружения скрытых внутренних дефектов сварных швов применяем 100% УЗК. Метод основан на способности ультразвуковых волн проникать в металл на большую глубину и отра
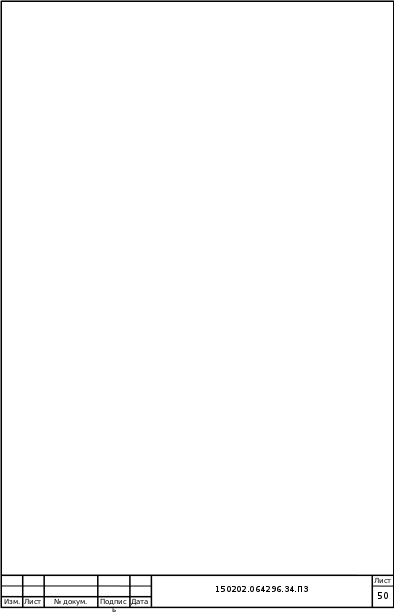
С появлением новых приборов ( например модели EPOCHII, EPOCHIII, EPOCHIIIB) процесс поиска дефектов упростился. Приборы данного типа позволяют вычислять реальные координаты дефекта: глубину залегания, расстояния вдоль поверхности ввода и по ходу луча, запоминание минимальной толщины, индикация количества отражений при контроле многократно отраженным лучом. Проводить измерение расстояния по переднему фронту или максимуму эхо сигнала. Обеспечивают запоминание огибающей эхо сигнала. В качестве дополнительных функций прибор оснащается : программами построения АРД-кривых, ВРЧ, В-скан. Позволяют документировать результаты посредством интерфейсной программы; кроме того плоский дизайн и небольшие размеры делают приборы данного типа удобными для работы в стесненных условиях.
Имеют широкополосный частотный диапазон 0,4-17,5МГц при -6дБ, диапазон развертки 1-5000мм, вес 1,2кг, большой яркий электролюминесцентный экран высокого разрешения с рабочим диапазоном температур от -25 0С до70 0С. Встроенная память на 140 изображений экрана (настройки дефектограммы) или 3000 измерений толщины.
Основные методы технологического процесса ультразвукового контроля соединений следующие :
-
Подготовка к контролю; -
Поиск дефектов; -
Измерение дефектов – их размеров, формы расположения; -
Оценка качества проконтролированного соединения.
Подготовка ультразвукового контроля в основном должны включать следующие этапы:
а) выбор основных параметров конт
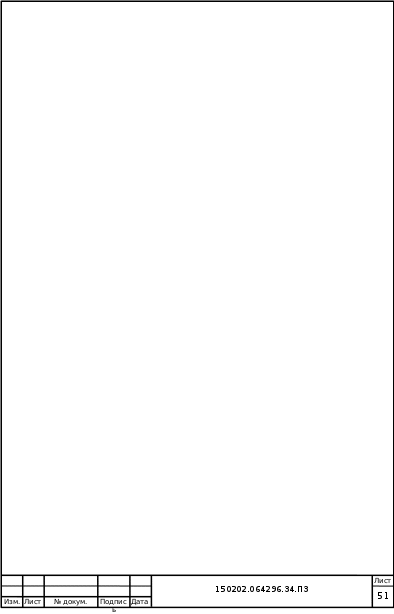
б) настройку дефектоскопа по контрольным образцам на заданные параметры;
в) очистку поверхности сканирования от брызг металла, грязи, отслаивающейся окалины и т.п.;
г) нанесение контролирующего смазочного материала на искатели и поверхности сканирования;
Очистка поверхности, по которой перемещают искатель, очень важна в отношении выявляемости дефектов и достоверности контроля, а также для сохранения искателей. В технологических картах на сварку следует предусматривать время и средства на очистку зон сканирования вблизи контролирующего шва. Ширина этих зон должна быть оговорена в НТД.
Контролирующие среды предназначены для обеспечения акустического контроля контакта искатель – изделия. Используют жидкие смазочные материалы (масла), смазочные материалы (минеральные масла, глицерин, воду) и вязкие на основе солидола, тавота. Применяют масла – ТУ-0253-048-0400169-02.
Поиск дефектов. Задача поиска обнаружение, обычно путем сканирования, дефектов с эквивалентной площадью Sэ большей чем заданная продольная чувствительность Sn,. Используют две схемы сканирования: поперечно-продольную и продольно-поперечную.
Провести сканирование контролируемого шва. Рассмотреть схему условного деления строк-импульса:
-
зона появления эхосигналов от дефектов, расположенных в корне шва; -
зона появления эхосигналов от дефектов в верхней части шва.
Провести оценку допустимости обнаруженных дефектов по амплитуде и условной протяженности.
Порядок контроля УЗД:
1. Застропить емкость и установить на ро

2. Проверить подготовку сварного шва и околошовную зону перед проведением контроля УЗД. Поверхность не должна иметь вмятин, неровностей, забоин, отслаивающейся и вдавленной окалины. Шероховатость поверхности не более 6,3.
3. Нанести на контролируемую поверхность контактную жидкость – глицерин (расход 0,3кг на 1 кв.моколошовной зоны).
4. Провести УЗД по схеме (рис. 12).
5. Застропить емкость, переместить на участок сварки.
6. Смыть контактную среду в течении 0,5-1 часа теплым содовым раствором (расход на 1 литр воды – 50г соды).
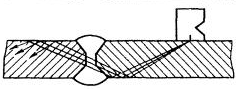
Рисунок12. Схема УЗК.
После проведения 100%-гоУЗК контроля, оформляют результаты контроля в соответствии с руководством.
После ультразвукового контроля проводят гидроконтроль герметичности гидродавлением. Данным методом, испытывают, как правило, замкнутые системы, работающие под давлением. Для гидравлических систем, как контрольное вещество используют обычно рабочую жидкость (вода- в нашем случае). Объект заполняют жидкостью, герметизируют и создают избыточное давление гидронасосами. Сначала изделие испытывают на прочность согласно ТУ при давлениях в 1.5-2 раза превышающих рабочее. После выдержки под давлением объект контролируют внешним осмотром, обнаруживая течи и места отпотевания после обнаружения течей давление либо их отсутствии давление сбрасывают. Предельный диаметр выявляемых дефектов до 0.05 мм. Выдержка до 24 часов. Результаты гидроиспытаний, фиксируются актом. Метод гидроконтроля довольно простой и эффективный.
Порядок гироиспытания.
Испытание расширительной емкости на прочность и герметичность проводят гидравлическим давлением 3,0 МПа ГОСТ 356-80 в течении 10 минут:
1. Установить расширительную емкость на стенд и закрепить на подставке.
2. Установить заглушки
3. Установить заглушку с манометром МТП-1601 ГОСТ 8625 на патрубок. Открыть вентиль с пульта управления.
4. Подсоединить трубопровод от гидронасоса к трубе.
5. Наполнить емкость водой до появления струи воды из крана.
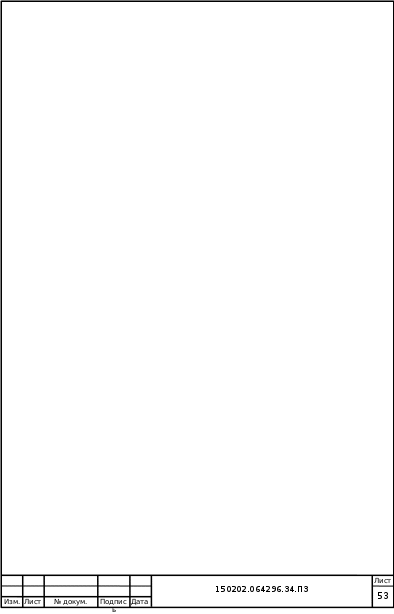
7. Произвести опрессовку пробным давлением 5,0 МПа в течении 10 минут.
8. Снизить давление до 3,0 МПа.
9. Осмотреть сварные швы. Емкость считается выдержавшей гидроиспытание, если не обнаружено течи, потения на сварных швах.
10. Снизить давление до нуля, открыв вентиль с пульта управления.
11. Открыть и снять заглушки с нижних штуцеров.
12. Слить воду.
13. Отсоединить трубопровод от гидронасоса.
14. Открепить и снять все заглушки.
15. Продуть емкость сжатым воздухом.
16. Гидроиспытание проводить в присутствии работников ОТК.
17. В случае потения, течи, вырезать дефектный участок сварного шва, заварить, произвести соответствующий контроль и повторить гидроиспытание.
Также рекомендуется проводить рентгеноконтроль. Рекомендуемый объем радио
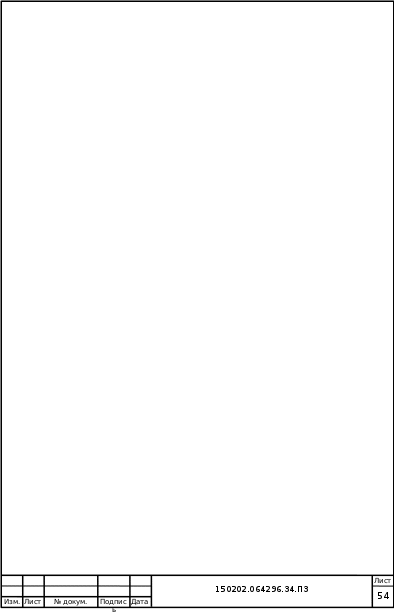
Вывод: качество изделий напрямую зависит от продуманного и хорошо организованного предварительного, и сопутствующего пооперационного контроля.
-
ПЛАНИРОВКА ЦЕХА
В соответствии с различными типами сварочных производств и разновидностями их организациями в практике проектирования участков установились определенные типовые схемы взаимного расположения включаемых в состав участков. В нашем случае используется следующая схема: 1. Промежуточный комплектовочный склад деталей. 2. Отделение узловой сборки и сварки. 3. Отделение общей сборки и сварки.
Даная разработанная схема удовлетворяет требованиям организации отдельных операций сварочного участка. При разработке нашего участка используется схема не симметричной кривой. Размер участка и расстановка оборудования подобраны методом уточнения с учетом габаритных, функциональных и рациональных параметров оборудования. Размер участка в соответствии с расстановкой оборудования, зон обслуживания, учетом проходов, зон обслуживания, а также с учетом направления движения деталей в ходе производственного процесса составил 576м2.
Состав основных рабочих согласно экономических расчетов при действительном годовом фонде времени 3600 часов и трудоемкости программы выпуска 3240 часов составило 2 человек. Согласно тому же расчету для данной программы выпуска согласно коэффициенту загрузки оборудования равному 1 принимается количество основного оборудования в количестве 8 штук. Участок обслуживается кран-балкой грузоподъемностью 6 тонн для обеспечения загрузки промежуточного склада заготовками на одну рабочую смену, а также применяется для транспортировки изделий с одного рабочего места на другое в процессе производства (масса изделия 890 кг). Высота цеха при использовании верхнего транспорта составило :
Hп = h1+h3+h4+h5+h6, (11)
Hз = Hп+h7+h8,
где : h1- наибольшая высота производственного оборудования,
h3- расстояние от уровня поверхности головки рельса подкрановых путей до низшей точки подъемного крюка в его наиболее высоком положении.
h4 – расстояни