Файл: Анизаций выполняющих строительство, реконструкцию, капитальный ремонт объектов атомной отрасли.doc
ВУЗ: Не указан
Категория: Не указан
Дисциплина: Не указана
Добавлен: 09.01.2024
Просмотров: 144
Скачиваний: 1
ВНИМАНИЕ! Если данный файл нарушает Ваши авторские права, то обязательно сообщите нам.
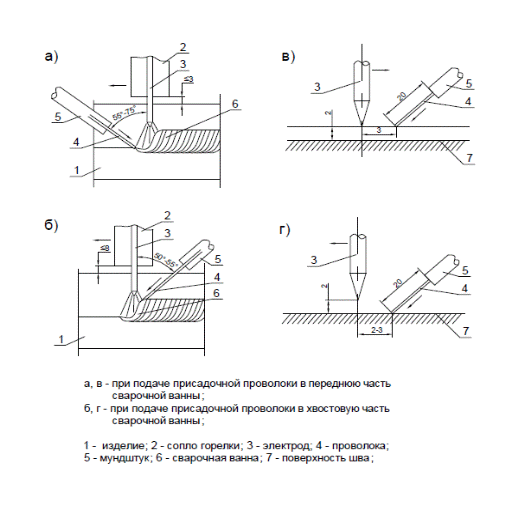
Рисунок 12.1 - Варианты подачи присадочной проволоки
-
При сварке труб из стали перлитного класса разрешается подавать присадочную проволоку либо в переднюю, либо в хвостовую (вслед движению электрода) часть ванны (рисунок 12.1). Настройка положения присадочной проволоки относительно электрода и поверхности изделия осуществлять согласно указаниям, приведённым на рисунке 12.1. Первый, второй и последний слои шва во всех случаях следует сваривать с подачей присадочной проволоки в переднюю часть сварочной ванны. -
При сварке слоёв шва, состоящих из отдельных параллельных валиков, присадочную проволоку подавать также в переднюю часть сварочной ванны. -
Сварку корневого слоя шва выполнять непрерывной дугой без поперечных колебаний электрода и проволоки. -
Сварку остальных слоёв шва (кроме облицовочных) осуществлять с поперечными колебаниями электрода и присадочной проволоки, с импульсным увеличением силы сварочного тока и скорости подачи проволоки в крайних точках амплитуды колебаний электрода. -
Сварку облицовочных слоёв выполнять с поперечными колебаниями электрода и проволоки без синхронизированного увеличения сварочного тока и скорости подачи проволоки. -
При ширине разделки кромок в месте выполнения очередного слоя шва до 16 мм (и ниже) сварку производить с колебаниями электрода от одной кромки до другой. При большой ширине разделки сварку каждого слоя шва выполнять за два или несколько перекрывающих друг друга валиков. При этом импульсно увеличивать сварочный ток и скорость подачи проволоки следует только при нахождении электрода у кромки разделки, т.е. только в одной крайней точке амплитуды колебаний электрода и проволоки. -
Толщина наплавляемого за один проход слоя шва не должны превышать:
-
при сварке с подачей проволоки в переднюю часть сварочной
ванны – 3,0 мм; -
при сварке с подачей проволоки в хвостовую часть сварочной
ванны – 4,5 мм.
-
При сварке соединения сварщик должен следить за формированием шва у кромок разделки. При возникновении пропусков шва у кромки (пустоты) сварка должна быть прекращена. Дефекты формирования шва должны быть удалены механическим путём или подварены. Сварка возобновляется вновь после корректировки параметра (параметров) режима, пришедшего к образованию дефекта.
-
1 2 3 4 5 6 7 8 9 10 11
Контроль качества подготовки деталей и сборочных единиц под сборку, сварку трубопроводов
-
Внешний осмотр при подготовке деталей и сборочных единиц под сборку, сварку и наплавку следует проводить для контроля:
-
наличия заводской маркировки; -
приемка полуфабрикатов, заготовок и деталей под сборку; -
правильности формы конструктивных элементов, подготовленных под сборку деталей; -
правильности формы конструктивных элементов, подготовленных под сборку деталей; -
выполнения плавных переходов (скосов) при подготовке деталей различной номинальной толщины под стыковые сварные соединения; -
правильности подготовки кромок под сварку, отсутствия дефектов на кромках; -
зачистки, подготовленных под сварку (наплавку) кромок (поверхностей) и примыкающих к ним участков изделий; -
расточки (калибровки, раздачи) концов труб (патрубков, штуцеров); -
чистоты поверхности основного металла, прилегающего к подлежащим сварке кромкам, и свариваемых кромок.
-
Измерение деталей проводится для проверки:
-
толщины деталей; -
овальности трубопроводов; -
угла разделки кромок; -
глубины разделки кромок; -
размера притупления кромок; -
положения вершины разделки; -
размера и положения наплавляемого притупления на кромке элемента.
-
Измерение при подготовке деталей под сварку выполняется для проверки:
-
перпендикулярности подготовленных под сварку цилиндрических изделий к их осям; -
размеров расточки (калибровки, раздачи) концов труб (патрубков, штуцеров); -
минимальной фактической толщины стенки на концах подготовленных под сварку деталей после расточки (раздачи) и зачистки.
-
Для измерения толщины стенок деталей допускается применять физические методы контроля (ультразвуковые дефектоскопы, толщиномеры и т.д.). -
Измерение деталей конструкций следует проводить не реже чем через каждый метр их длины и не менее чем в трех местах на каждой детали.
Детали трубопроводов следует измерять не менее чем в трех местах, расположенных равномерно по периметру стыка.
-
Контроль качества сборки деталей и сборочных единиц под сварку трубопроводов
-
Внешний осмотр при сборке деталей и сборочных единиц под сварку проводится для проверки:
-
наличия клейм (штампов), подтверждающих соответствие подготовки под сборку и сварку (наплавку) установленным требованиям и правильности технологической маркировки; -
чистоты поверхности свариваемых кромок; -
наличия и состояния используемых приспособлений и оборудования; -
порядка сборки; -
способов и надежности крепления свариваемых деталей; -
соблюдения условий, предотвращающих возникновение напряжений от собственной массы деталей в зоне подготовленных под сварку кромок; -
методов подгонки деталей; -
количества, расположения и качества прихваток; -
формы временных технологических креплений; -
качества приварки временных технологических креплений; -
смещения кромок (несовпадения поверхностей) собранных деталей, а также смещения притуплений собранных деталей с двусторонней разделкой кромок; -
дополнительной зачистки и обезжиривания подлежащих сварке кромок и примыкающих к ним поверхностей собранных деталей; -
наличия защитного покрытия от брызг в соответствии с требованиями, содержащимися в описании технологического процесса или в производственной инструкции; -
соответствия температуры подогрева деталей из перлитной стали, подлежащих сварке для наплавки с подогревом, требованиям, содержащимся в описании технологического процесса или производственной инструкции; -
условий транспортирования собранных деталей (сборочных единиц).
-
При сборке деталей под сварку измерения выполняются для проверки:
-
общего угла разделки кромок; -
величины зазора между деталями; -
смещения кромок (несовпадения поверхностей) собранных деталей, а также смещения притуплений собранных деталей с двусторонней разделкой кромок; -
размеров, количества и расположения временных технологических креплений; -
перелома осей соединяемых деталей.
-
Проверка смещения свариваемых кромок по внутреннему диаметру относительно друг друга проводится не менее чем в трех местах, расположенных равномерно по периметру стыка, а конструкцией не реже чем через каждый метр их длины, но не менее чем в трех местах на каждой детали. -
Качество выполнения прихваток и приварки технологических креплений проверяется внешним осмотром. При этом нормы оценки качества прихваток и приварок принимаются по категории собираемого под сварку соединения изделия.
-
Контроль в процессе сварки трубопроводов
-
При сварке или наплавке деталей внешний осмотр следует проводить для проверки:
-
наличия маркировки (штампов), подтверждающих соответствие сборки установленным требованиям; -
пространственных положений сварки или наплавки; -
количества и порядка наложения валиков и слоев шва (наплавки); -
качества зачистки свариваемых поверхностей соединений перед наложением последующих валиков, законченных швов и околошовной зоны от брызг металла, шлака, окалины и др. загрязнений; -
чистоты поверхности свариваемых и наплавляемых деталей
(не оставлены ли следы цветов побежалости при сварке химически активных металлов и до и после зачистки); -
наличия аргонодуговой обработки мест сопряжения шва с поверхностью основного металла (где это требуется по технологическому процессу); -
очередности выполнения швов; -
послойного визуального контроля качества швов (при невозможности проведения неразрушающих методов контроля полностью выполненного сварного соединения); -
зачистки поверхности валиков в процессе сварки (наплавки), а также поверхности шва и примыкающих к нему зон основного металла после окончания сварки; -
предварительной наплавки кромок при сварке деталей из разнородных сталей и в других предусмотренных случаях; -
маркировки (клеймения) сварных соединений и наплавленных элементов, выполнявшимися их сварщиками.
-
Измерения в процессе сварки выполняются для проверки:
-
количества и размеров наложения валиков и слоев шва (наплавка); -
минимального расстояния от края усиления шва до линии сплавления предварительной наплавки с основным металлом; -
толщины отдельных слоев и наплавленного антикоррозийного покрытия; -
температуры окружающей среды и температуры свариваемого металла.
-
Внешний осмотр, проводимый в процессе сварки и наплавки, должен обеспечивать не только выявление и своевременное исправление обнаруженных дефектов, но и принятие профилактических мер с целью предупреждения возникновения дефектов при последующей сварке. -
При выполнении сварных соединений изделий с номинальной толщиной стенки свыше 50мм мастер совместно с представителем СТК должны проводить внешний контроль свариваемого шва после выполнения каждых
пяти-десяти слоев. -
Результаты контроля послойным внешним осмотром сварных швов, контроль которых радиографическим или ультразвуковым методами технически невозможен, считаются удовлетворительным, если выдержаны требования по нормам на поверхностные дефекты в соответствии с требованиями Правил АЭУ [11].
-
Контроль качества сварных соединений
-
На сварном соединении, поступившем на контроль должно быть поставлено клеймо сварщика. -
Внешний осмотр сварных соединений следует проводить по всей их длине с целью выявления:
-
несоответствия формы шва или наплавки требованиям
нормативно-технической документации и рабочих чертежей; -
трещин; -
прожогов; -
незаваренных кратеров; -
свищей; -
пор; -
подрезов; -
усадочных раковин; -
шлаковых и нематаллических включений; -
пятен коротких замыканий электрода на основном металле и др. дефектов.
-
При внешнем осмотре проверяется также качество подготовки поверхности сварных соединений и наплавки изделий для проведения последующих контрольных операций. При этом шероховатость поверхности по ГОСТ 2789-73 должна быть не более:
-
RZ20 при капиллярных методах контроля; -
RZ40 при магнитно-порошковой и ультразвуковой дефектоскопии.
-
Качество удаления временных технологических креплений после тщательной зачистки (зашлифовки) места приварки проверяются травлением с последующим осмотром мест приварки через лупу 4-7- кратного увеличения. -
Измерение сварных соединений после выполнения сварки проводится для проверки:
-
формы, ширины и высоты усиления сварного шва; -
катетов швов угловых, тавровых и нахлесточных соединений; -
длины и шага прерывистых швов; -
превышения проплава и вогнутости корня шва (в доступных местах); -
величины западания между валиками шва; -
высоты чешуйчатости; -
расстояния от оси шва до реперных точек; -
величины нахлестки; -
утонений в местах зачистки швов и околошовной зоны; -
перелома осей соединяемых деталей; -
смещения вершины сварного шва; -
величины несовпадения поверхностей деталей в стыковых соединениях; -
размеров поверхностных дефектов сварных соединений.
-
При измерении угловых, тавровых и нахлесточных сварных швов, имеющих вогнутую или выпуклую форму усиления, величина катета и высоты шва измеряются по направлению биссектрисы угла соединения. -
При необходимости угловых, тавровых и нахлесточных сварных швов, имеющих вогнутую или выпуклую форму усиления, величина катета и высота шва измеряются по направлению биссектрисы угла соединения. -
При необходимости глубина и высота чешуйчатости сварного шва может быть определена по слепку, снятому с контролируемого участка шва. Слепок разрезают (не допуская его деформации) так, чтобы искомый размер лежал в плоскости разреза. Измерение проводится с помощью измерительной лупы. Материалом для слепка может служить пластилин, воск и другие пластичные материалы. -
Размеры сварных соединений под сварку контролируются в соответствии с технологическим процессом или настоящим стандартом не реже чем через один метр шва и не менее чем в трех местах по длине каждого шва. Измерение сварных соединений изделий проводится также в местах, где при внешнем осмотре предполагаются отклонения от установленных размеров.