Файл: Курсовой проект по дисциплине теория конструкции локомотивов Вариант 22 Выполнил студент гр. 752 Коновалов М. А.doc
ВУЗ: Не указан
Категория: Не указан
Дисциплина: Не указана
Добавлен: 10.01.2024
Просмотров: 164
Скачиваний: 2
ВНИМАНИЕ! Если данный файл нарушает Ваши авторские права, то обязательно сообщите нам.
12 — кронштейн опоры гяговых двигателей двойной; 13 — кронштейн опоры тягового электродвигателя одинарный; 14 — концевая балка задняя; 15, 16, 17, 18 — детали для крепления рычажной передачи тормоза; 19 — угольник литой, соединяющий боковину с концевыми поперечными балками; 20 — фланцы крепления кронштейнов подвешивания тяговых электродвигателей к концевым балкам
В средней части шкворневой балки имеется отверстие, в которое вваривают стальной литой стакан 7. Цилиндрическими частями балки вставляют в отверстия боковин и приваривают к наружным боковым стенкам боковин и к фланцам 9, приваренным к внутренним половинам боковин. В нижней средней части к наружному листу боковины и фланцу 9 приварена опора амортизатора листовой рессоры 10,
Концевые балки сварены продольным швом из корытообразных штампованных листов из стали 20 толщиной 10 мм. С боковинами концевые балки соединены стальными литыми угольниками. Передняя концевая балка 11 имеет большой прогиб средней части из-за расположения ее при сборке тепловоза под стяжным ящиком рамы кузова.
Боковины, шкворневые и концевые балки с приваренными к ним деталями до механической обработки проходят термическую обработку для снятия напряжения. Клиновые пазы в кронштейнах для соединения с буксовыми поводками 2 и 4 обрабатывают на станке после окончательной сварки рамы. Форма литых кронштейнов в местах, где сварное соединение делают встык со штампованным листом, предусматривает на максимально возможной длине плавное изменение жесткости узла. К шкворневым и концевым балкам крепят кронштейны подвешивания тяговых электродвигателей. Последние подвешены к раме тележки в трех точках (рис.8).
Со стороны моторно-осевых подшипников к остову тягового электродвигателя при помощи восьми болтов прикреплен литой кронштейн 2, который через опору 6, обойму 8 и резиновые амортизаторы 9 я 10 опирается на одинарный кронштейн Uболтами прикрепленный к поперечной балке рамы тележки. Между опорой 6 и обоймой 8 установлены регулировочные прокладки 7. Схема расположения тягового электродвигателя на тележке определила, что для первого и третьего электродвигателей одинарный кронштейн закреплен к концевым, а для второго — ко второй шкворневой балке рамы тележки. Две другие точки крепления (подвешивания) электродвигателя к раме тележки расположены на противоположной стороне остова. Конструктивно опоры тягового электродвигателя выполнены в виде двух литых лап,
изготовленных в отливке остова, которыми электродвигатель через опору и обойму опирается на резиновые амортизаторы 14 и 15, установленные на двойной литой кронштейн 3, болтами прикрепленный к двойному кронштейну 4 шкворневой балки рамы тележки. Крепление кронштейнов к шкворневым балкам рамы тележки необходимо производить динамометрическим ключом. Болты крепления кронштейнов изготовляют по чертежу с высокими требованиями к качеству и геометрии. При этом особое внимание обращают на увеличенный (до 3 мм) радиус перехода от стержня к головке болта и перпендикулярность плоскости прилегания головки. Для гашения высокочастотных вибраций в узлах подвешивания (крепления) тяговых электродвигателей к раме тележки имеются резиновые амортизаторы, выполненные в виде блоков, состоящих из двух плоских металлических колец, между которыми размещены резиновые прокладки. Кроме того, в узлах крепления тяговых электродвигателей установлены стальные шайбы толщиной 2—3 мм для регулирования положения полого вала относительно оси колесной пары. Подвешивание тягового электродвигателя на раму тележки, а следовательно, и положение полого вала относительно оси регулируют;
а) в продольном направлении тележки прл помощи прокладок 5 и 13 между вертикальным фланцем кронштейнов и рамой тележки или в отдельных случаях строжкой привалочных фланцев самих кронштейнов, но не более чем на 1 мм. Смещение осей колесных пар от номинальных размеров (2200 и 2400 мм) допускается не более ±0,5 мм;
б) в вертикальном положении постановкой прокладок (шайб) 7 и 16 между обоймой, устанавливаемой на амортизатор, и опорами 6 и 17 кронштейна или лапы тягового электродвигателя. Точность установки контролируют сравнением размеров зазора между пальцами привода полого вала и отверстиями для них в колесном центре. Отклонение от номинального размера (40 мм) допускается не более ±2 мм. В процессе эксплуатации необходимо следить за изменениями этих зазоров, нарушение которых, особенно на новых или вновь поставленных амортизаторах, может происходить из-за обмина деталей, входящих в узлы подвешивания электродвигателя;
в) в поперечном направлении тележки относительное положение тягового электродвигателя и колесной пары при помощи установки кронштейнов крепления электродвигателя. Несовпадение середины колесной пары с продольной осью тележки допускается не более 0,5 мм. Точность установки контролируют сравнением размеров на левой и правой стороне колесной пары между внутренней гранью бандажа и наружным торцом привода полого вала. Окончательный контроль подвешивания электродвигателя производят на прямом горизонтальном участке пути под рабочей нагрузкой после обкатки тепловоза.
Рис. 7. Подвешивание третьего тягового электродвигателя к раме тележки:
1 — кронштейн опорный; 2 — кронштейн крепления электродвигателя; 3 — кронштейн опорный двойной; 4 — двойной кронштейн; 5, 7, 11, 13, 16 — прокладки регулировочные; 6, 17-опоры; 8 — обойма; 9, 10, 14, 15 — амортизаторы; 12 — болт крепления кронштейна тягового электродвигателя
4. ВЫБОР СХЕМЫ И РАСЧЁТ НА ПРОЧНОСТЬ УПРУГИХ ЭЛЕМЕНТОВ РЕССОРНОГО ПОДВЕШИВАНИЯ
Перед расчетами необходимо привести схему рессорного подвешивания, согласно которой перечислить упругие элементы, подлежащие расчету на прочность. Как правило, в состав рессорного подвешивания входят: рессоры, пружины и резиновые амортизаторы.
При расчетах на прочность с учетом действующих на элемент силовых факторов, по допускаемым напряжениям, определяют геометрические свойства упругого элемента. В данном пункте раздела необходимо статический прогиб элемента fi.
4.1Расчет на прочность листовой рессоры
Статическая нагрузка действующая на рессору определяется по формуле:
(4.1)
кН,
где 2П – нагрузка на ось, кН;
q– неподрессоренный вес, приходящийся на одну колесную пару, кН:
q= 45 кН – при опорно-осевом подвешивании ТЭД.
Динамическая нагрузка определяется из выражения:
(4.2)
кН,
где
– коэффициент вертикальной динамики, определяемый по формуле:
, (4.3)
где vк – конструкционная скорость тепловоза, км/ч;
- номинальный статический прогиб рессорного подвешивания, мм.
Основные размеры листовой рессоры определяются по допустимым напряжениям изгиба при статической нагрузке [и] доп = 550 ÷ 650 МПа. Рессору рассматривают как балку постоянной толщины равного сопротивления изгибу.
Общее число листов в рессоре определяется исходя из соотношений между допускаемым напряжением изгиба, изгибающим моментом М и моментом сопротивления W одного листа:
. (4.4)
Таким образом общее число листов в рессоре определится из выражения:
(4.5)
n:=11
Изгибающий момент:
(4.6)
кН*м,
где l – длина рессоры, м.
Момент сопротивления:
(4.7)
м3,
где b – ширина рессоры, м;
h – толщина листа, м.
Общее число листов рессоры складывается из числа коренных ее листов nк = 2-3 и числа листов ступенчатой части nс:
n = nк + nс
nс=8
Рессоры проверяются по допускаемому напряжению изгиба при динамической нагрузке [и] max = 1000 МПа, при этом учитывается виляние хомута по формуле:
(4.8)
МПа
Рессора удовлетворяет условию прочности при динамической нагрузке, если
. 968,4<1000
Статический прогиб листовой рессоры, определяется для оценки ее деформации, по формуле:
, (4.9)
где Е = 2,05*105 МПа – модуль упругости для стали;
а – ширина хомута рессоры, м;
Статическая нагрузка действующая на пружину определяется по формуле:
(4.10)
кН
определяется по формулам (4.2) и (4.3), откуда
=21,5 кН
Основные размеры цилиндрической пружины определяют по допустимым касательным напряжениям при динамической нагрузке [] доп = 650 МПа.
Диаметр прутка определяется из уравнения прочности пружины:
(4.11)
МПа
откуда
м (4.12)
мм
где D – диаметр пружины, м;
К – коэффициент, учитывающий увеличение касательного напряжения в
сечении на внутренней поверхности витка пружины; принять К = 1,3.
Число рабочих витков определяется из уравнения деформации пружины:
, (4.13)
откуда
, (4.14)
где
В средней части шкворневой балки имеется отверстие, в которое вваривают стальной литой стакан 7. Цилиндрическими частями балки вставляют в отверстия боковин и приваривают к наружным боковым стенкам боковин и к фланцам 9, приваренным к внутренним половинам боковин. В нижней средней части к наружному листу боковины и фланцу 9 приварена опора амортизатора листовой рессоры 10,
Концевые балки сварены продольным швом из корытообразных штампованных листов из стали 20 толщиной 10 мм. С боковинами концевые балки соединены стальными литыми угольниками. Передняя концевая балка 11 имеет большой прогиб средней части из-за расположения ее при сборке тепловоза под стяжным ящиком рамы кузова.
Боковины, шкворневые и концевые балки с приваренными к ним деталями до механической обработки проходят термическую обработку для снятия напряжения. Клиновые пазы в кронштейнах для соединения с буксовыми поводками 2 и 4 обрабатывают на станке после окончательной сварки рамы. Форма литых кронштейнов в местах, где сварное соединение делают встык со штампованным листом, предусматривает на максимально возможной длине плавное изменение жесткости узла. К шкворневым и концевым балкам крепят кронштейны подвешивания тяговых электродвигателей. Последние подвешены к раме тележки в трех точках (рис.8).
Со стороны моторно-осевых подшипников к остову тягового электродвигателя при помощи восьми болтов прикреплен литой кронштейн 2, который через опору 6, обойму 8 и резиновые амортизаторы 9 я 10 опирается на одинарный кронштейн Uболтами прикрепленный к поперечной балке рамы тележки. Между опорой 6 и обоймой 8 установлены регулировочные прокладки 7. Схема расположения тягового электродвигателя на тележке определила, что для первого и третьего электродвигателей одинарный кронштейн закреплен к концевым, а для второго — ко второй шкворневой балке рамы тележки. Две другие точки крепления (подвешивания) электродвигателя к раме тележки расположены на противоположной стороне остова. Конструктивно опоры тягового электродвигателя выполнены в виде двух литых лап,
изготовленных в отливке остова, которыми электродвигатель через опору и обойму опирается на резиновые амортизаторы 14 и 15, установленные на двойной литой кронштейн 3, болтами прикрепленный к двойному кронштейну 4 шкворневой балки рамы тележки. Крепление кронштейнов к шкворневым балкам рамы тележки необходимо производить динамометрическим ключом. Болты крепления кронштейнов изготовляют по чертежу с высокими требованиями к качеству и геометрии. При этом особое внимание обращают на увеличенный (до 3 мм) радиус перехода от стержня к головке болта и перпендикулярность плоскости прилегания головки. Для гашения высокочастотных вибраций в узлах подвешивания (крепления) тяговых электродвигателей к раме тележки имеются резиновые амортизаторы, выполненные в виде блоков, состоящих из двух плоских металлических колец, между которыми размещены резиновые прокладки. Кроме того, в узлах крепления тяговых электродвигателей установлены стальные шайбы толщиной 2—3 мм для регулирования положения полого вала относительно оси колесной пары. Подвешивание тягового электродвигателя на раму тележки, а следовательно, и положение полого вала относительно оси регулируют;
а) в продольном направлении тележки прл помощи прокладок 5 и 13 между вертикальным фланцем кронштейнов и рамой тележки или в отдельных случаях строжкой привалочных фланцев самих кронштейнов, но не более чем на 1 мм. Смещение осей колесных пар от номинальных размеров (2200 и 2400 мм) допускается не более ±0,5 мм;
б) в вертикальном положении постановкой прокладок (шайб) 7 и 16 между обоймой, устанавливаемой на амортизатор, и опорами 6 и 17 кронштейна или лапы тягового электродвигателя. Точность установки контролируют сравнением размеров зазора между пальцами привода полого вала и отверстиями для них в колесном центре. Отклонение от номинального размера (40 мм) допускается не более ±2 мм. В процессе эксплуатации необходимо следить за изменениями этих зазоров, нарушение которых, особенно на новых или вновь поставленных амортизаторах, может происходить из-за обмина деталей, входящих в узлы подвешивания электродвигателя;
в) в поперечном направлении тележки относительное положение тягового электродвигателя и колесной пары при помощи установки кронштейнов крепления электродвигателя. Несовпадение середины колесной пары с продольной осью тележки допускается не более 0,5 мм. Точность установки контролируют сравнением размеров на левой и правой стороне колесной пары между внутренней гранью бандажа и наружным торцом привода полого вала. Окончательный контроль подвешивания электродвигателя производят на прямом горизонтальном участке пути под рабочей нагрузкой после обкатки тепловоза.
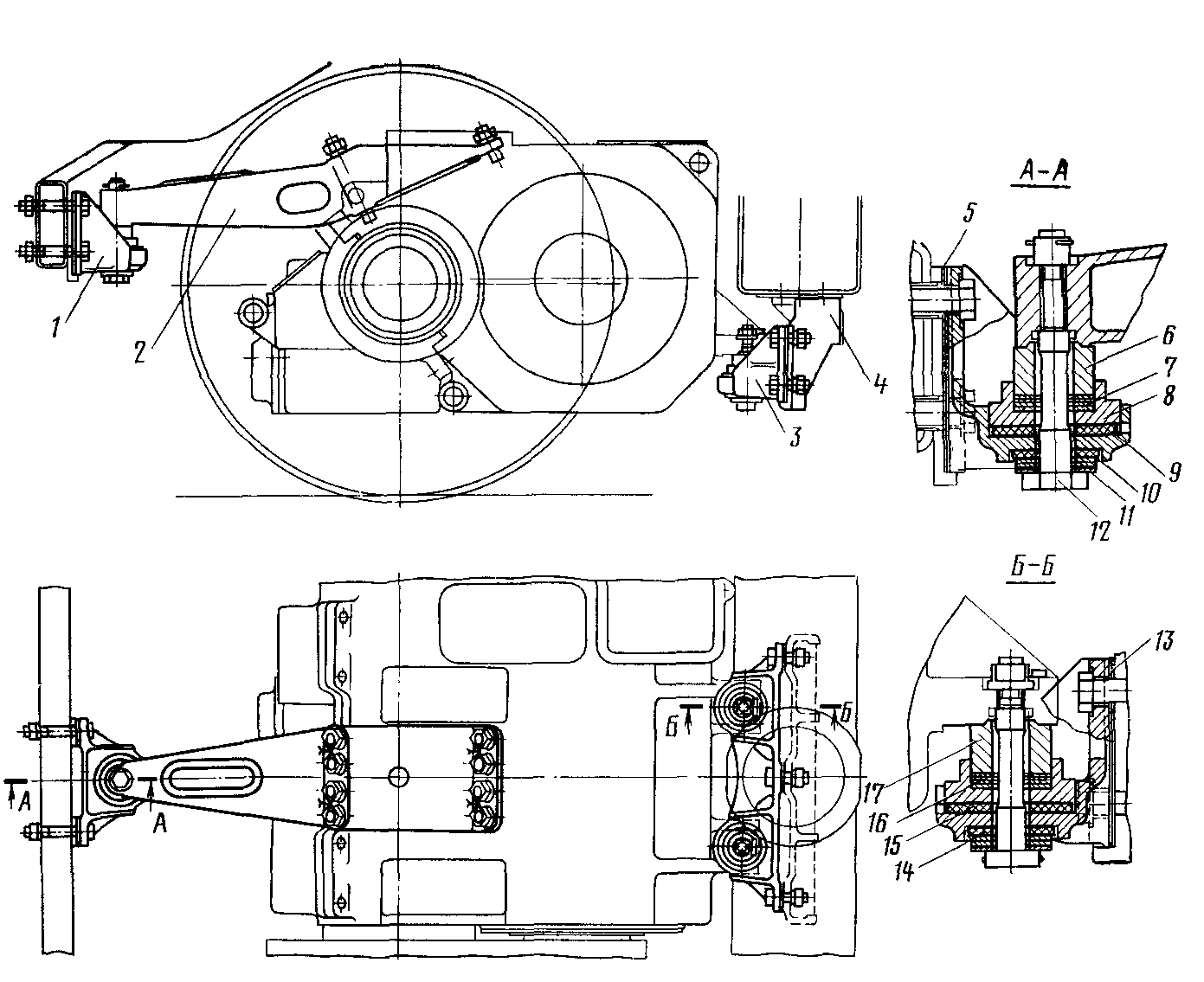
Рис. 7. Подвешивание третьего тягового электродвигателя к раме тележки:
1 — кронштейн опорный; 2 — кронштейн крепления электродвигателя; 3 — кронштейн опорный двойной; 4 — двойной кронштейн; 5, 7, 11, 13, 16 — прокладки регулировочные; 6, 17-опоры; 8 — обойма; 9, 10, 14, 15 — амортизаторы; 12 — болт крепления кронштейна тягового электродвигателя
4. ВЫБОР СХЕМЫ И РАСЧЁТ НА ПРОЧНОСТЬ УПРУГИХ ЭЛЕМЕНТОВ РЕССОРНОГО ПОДВЕШИВАНИЯ
Перед расчетами необходимо привести схему рессорного подвешивания, согласно которой перечислить упругие элементы, подлежащие расчету на прочность. Как правило, в состав рессорного подвешивания входят: рессоры, пружины и резиновые амортизаторы.
При расчетах на прочность с учетом действующих на элемент силовых факторов, по допускаемым напряжениям, определяют геометрические свойства упругого элемента. В данном пункте раздела необходимо статический прогиб элемента fi.
4.1Расчет на прочность листовой рессоры
Статическая нагрузка действующая на рессору определяется по формуле:
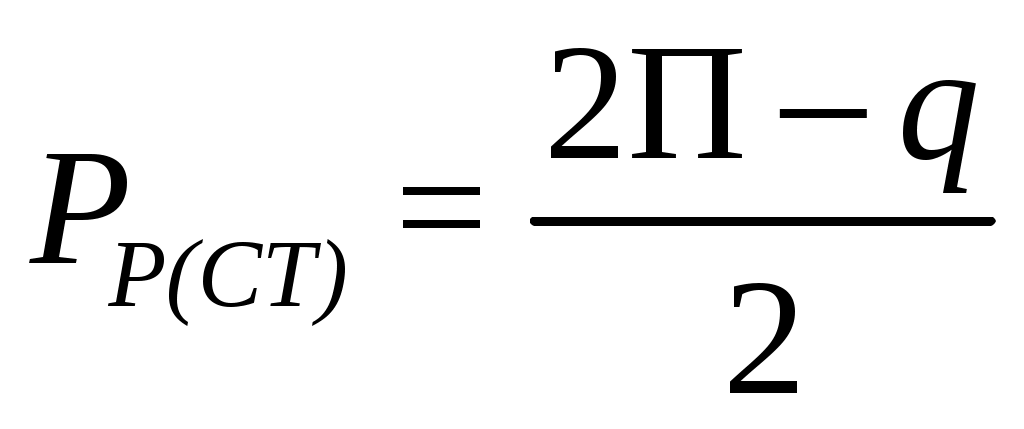

где 2П – нагрузка на ось, кН;
q– неподрессоренный вес, приходящийся на одну колесную пару, кН:
q= 45 кН – при опорно-осевом подвешивании ТЭД.
Динамическая нагрузка определяется из выражения:

(4.2)

где
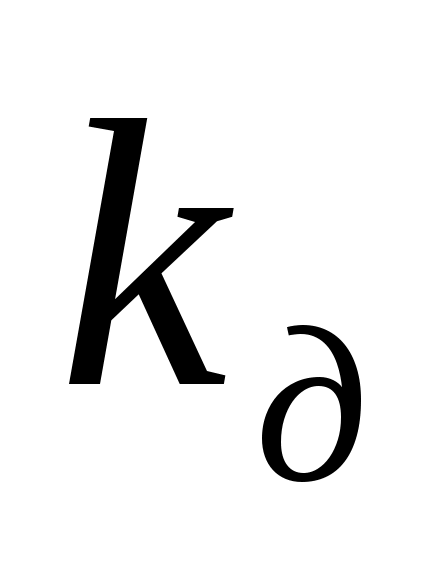

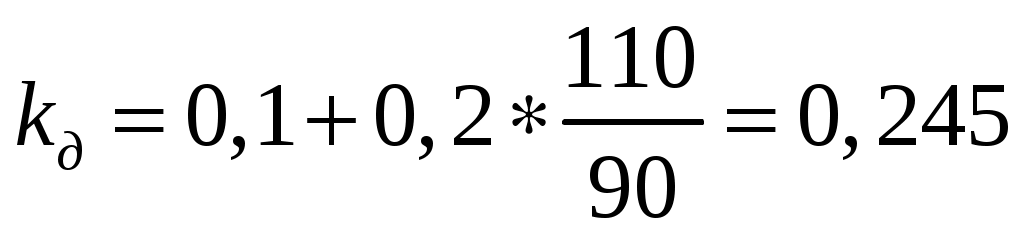
где vк – конструкционная скорость тепловоза, км/ч;
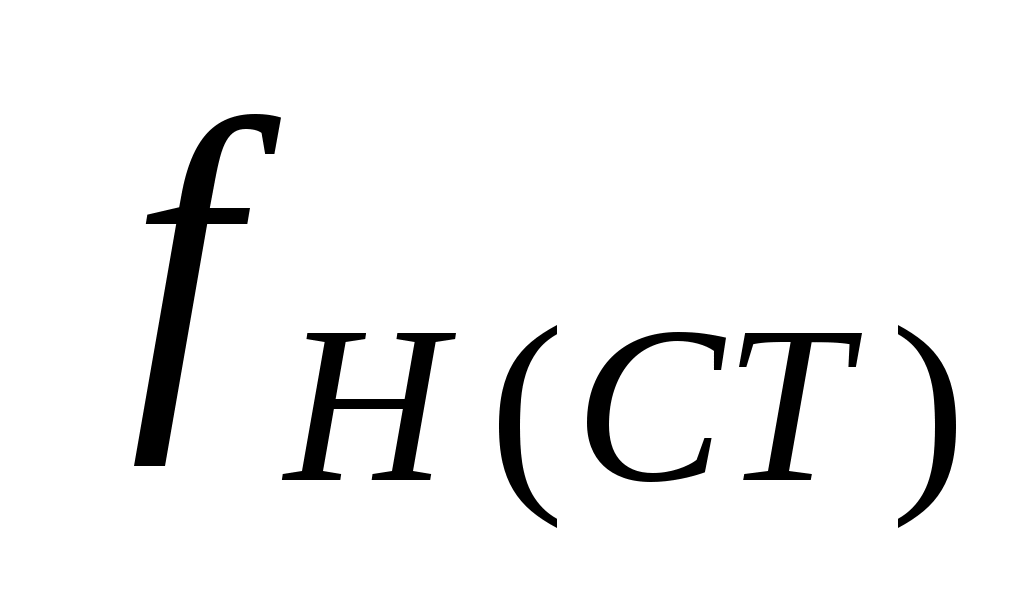
Основные размеры листовой рессоры определяются по допустимым напряжениям изгиба при статической нагрузке [и] доп = 550 ÷ 650 МПа. Рессору рассматривают как балку постоянной толщины равного сопротивления изгибу.
Общее число листов в рессоре определяется исходя из соотношений между допускаемым напряжением изгиба, изгибающим моментом М и моментом сопротивления W одного листа:
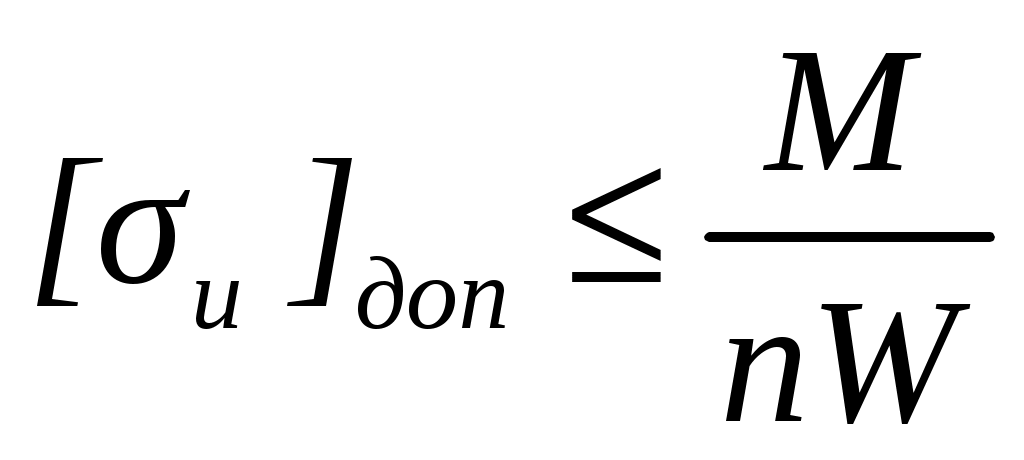
Таким образом общее число листов в рессоре определится из выражения:
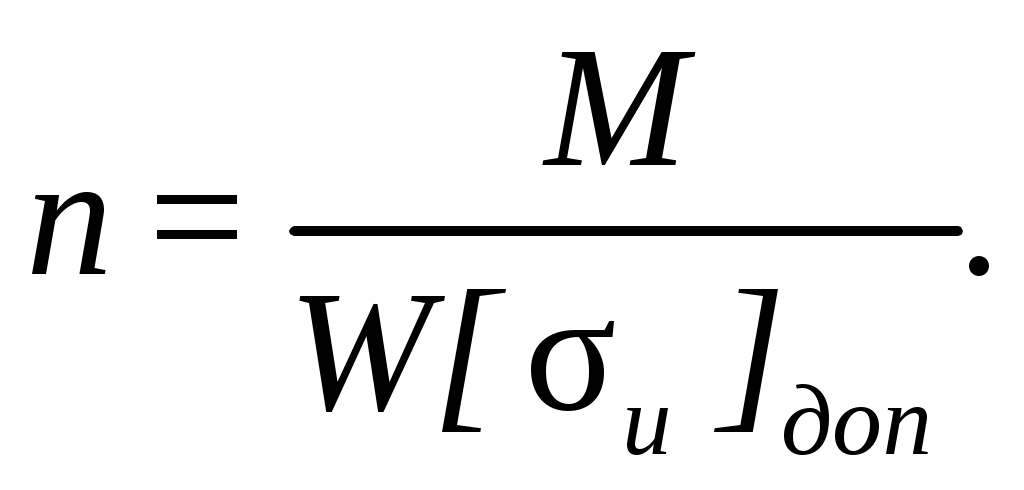
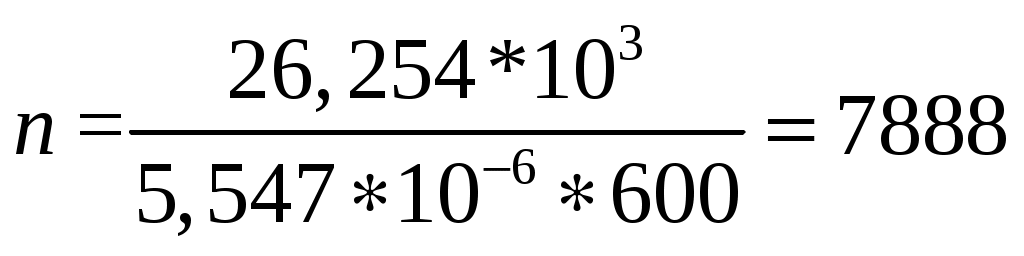
n:=11
Изгибающий момент:
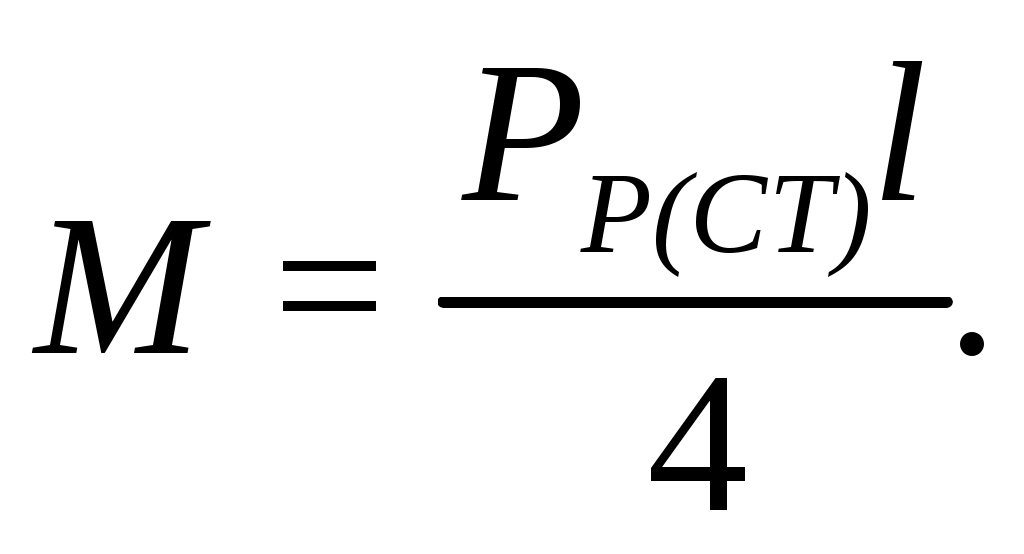
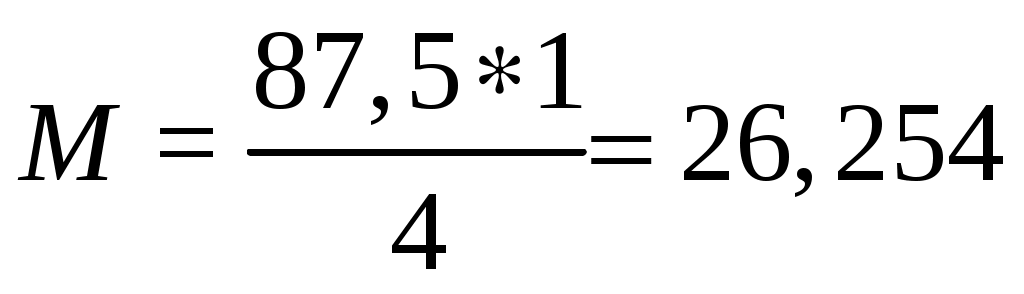
где l – длина рессоры, м.
Момент сопротивления:
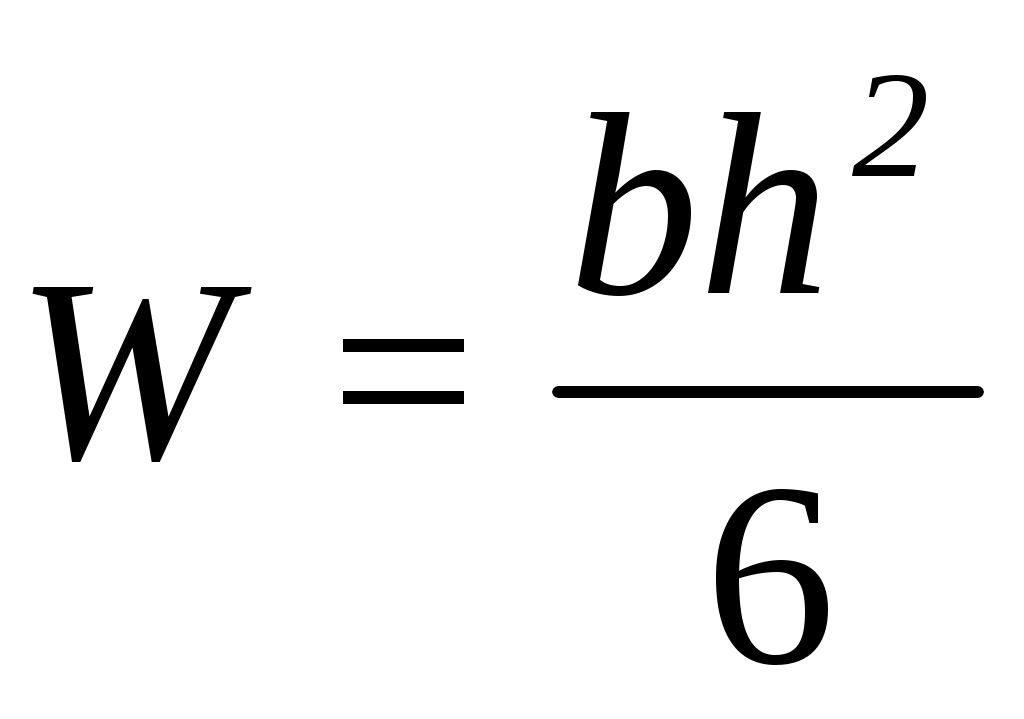
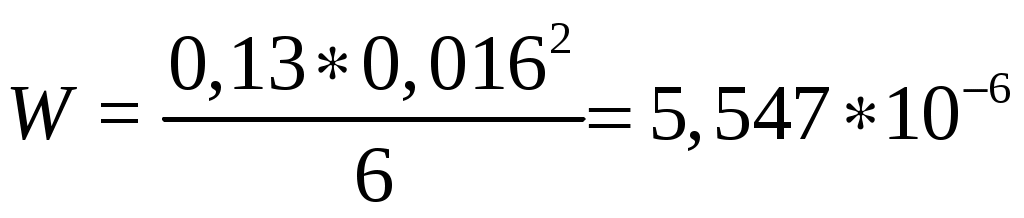
где b – ширина рессоры, м;
h – толщина листа, м.
Общее число листов рессоры складывается из числа коренных ее листов nк = 2-3 и числа листов ступенчатой части nс:
n = nк + nс
nс=8
Рессоры проверяются по допускаемому напряжению изгиба при динамической нагрузке [и] max = 1000 МПа, при этом учитывается виляние хомута по формуле:
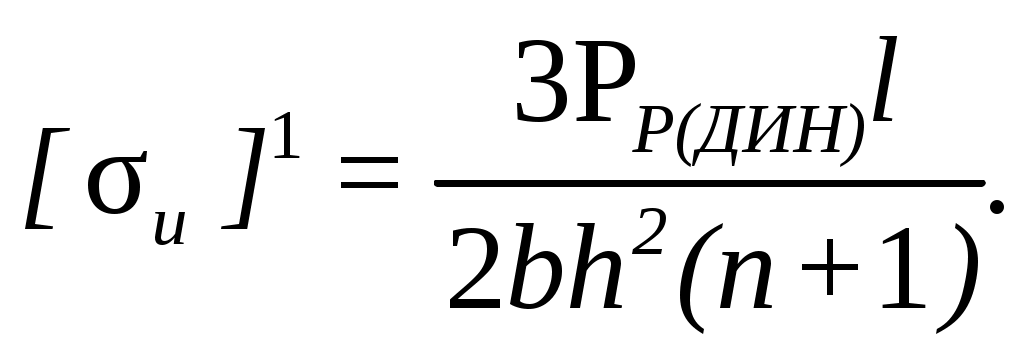

Рессора удовлетворяет условию прочности при динамической нагрузке, если
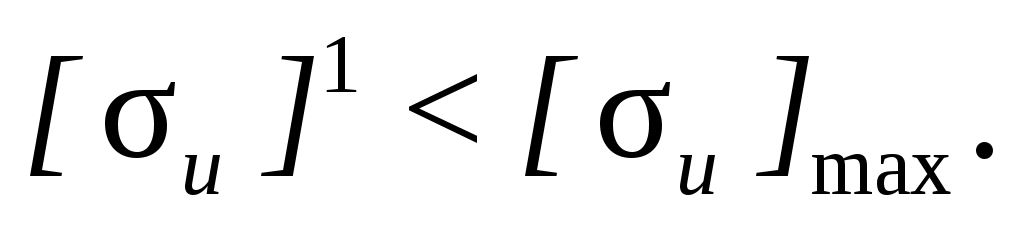
Статический прогиб листовой рессоры, определяется для оценки ее деформации, по формуле:
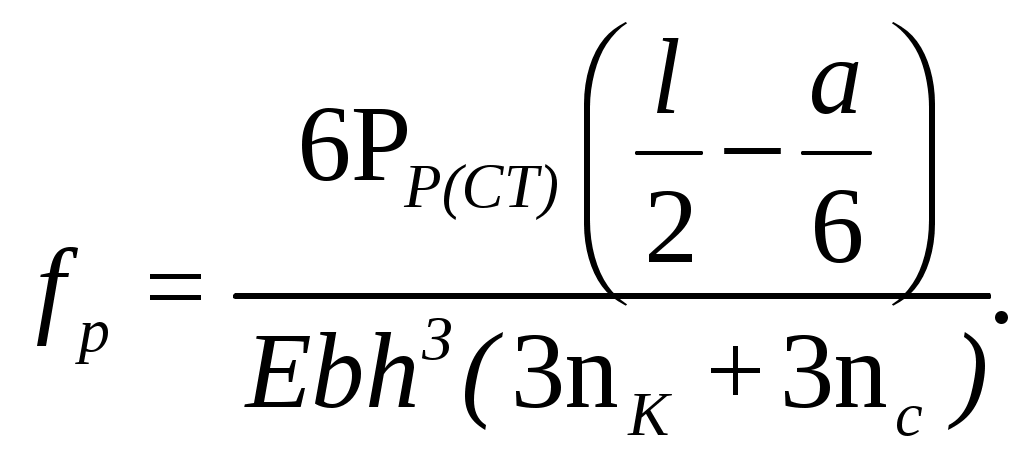
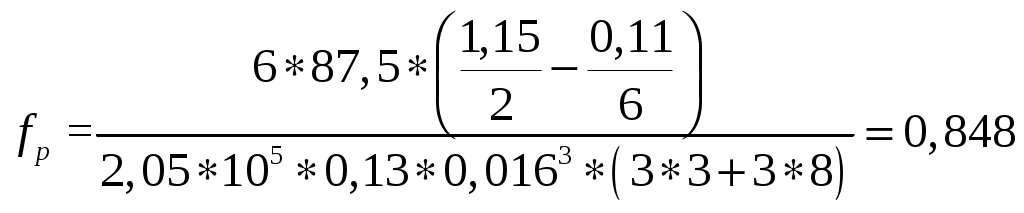
где Е = 2,05*105 МПа – модуль упругости для стали;
а – ширина хомута рессоры, м;
-
Расчет на прочность пружины
Статическая нагрузка действующая на пружину определяется по формуле:
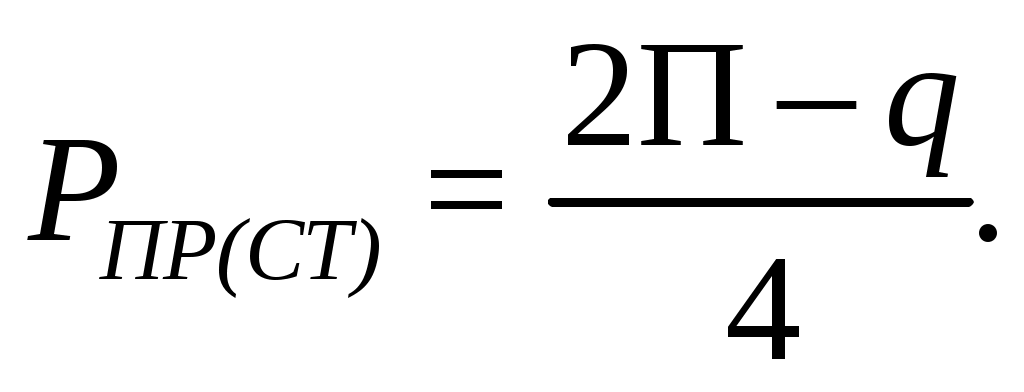
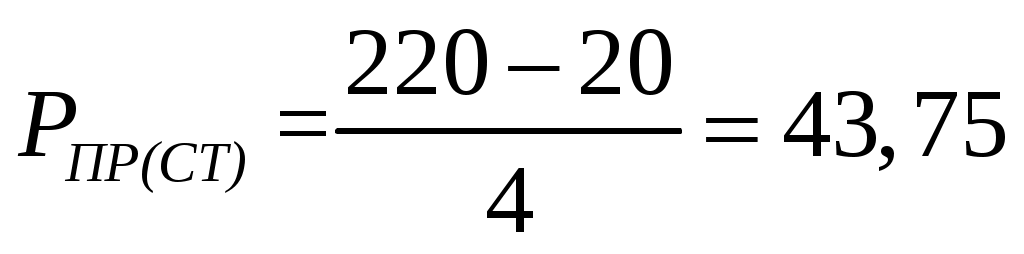
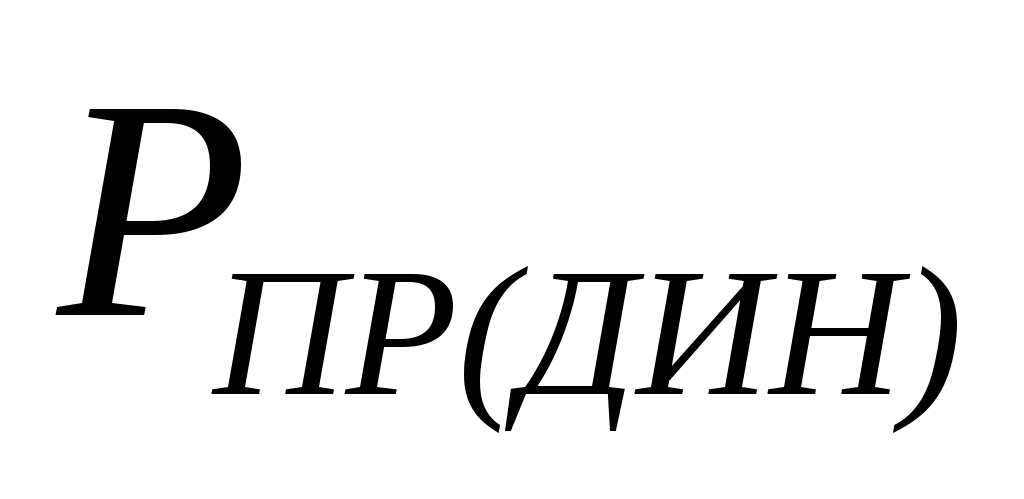
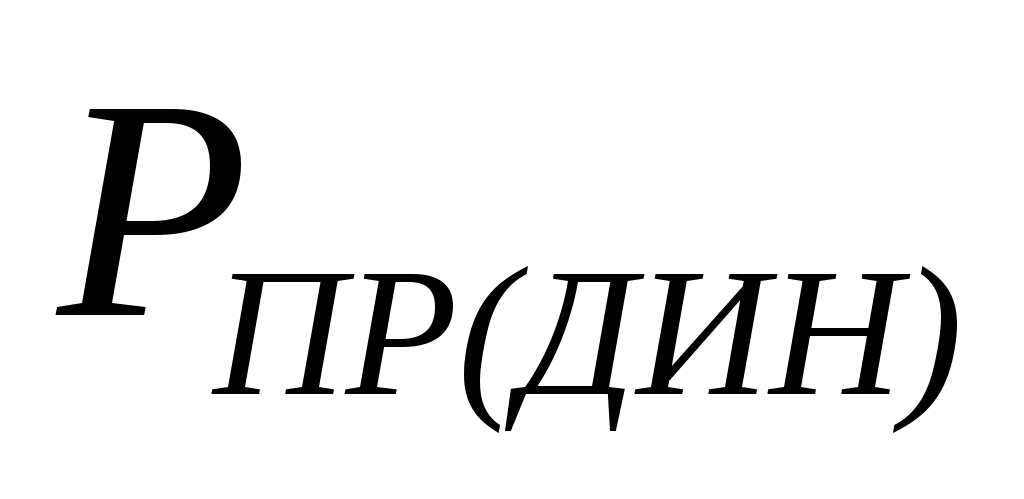
Основные размеры цилиндрической пружины определяют по допустимым касательным напряжениям при динамической нагрузке [] доп = 650 МПа.
Диаметр прутка определяется из уравнения прочности пружины:
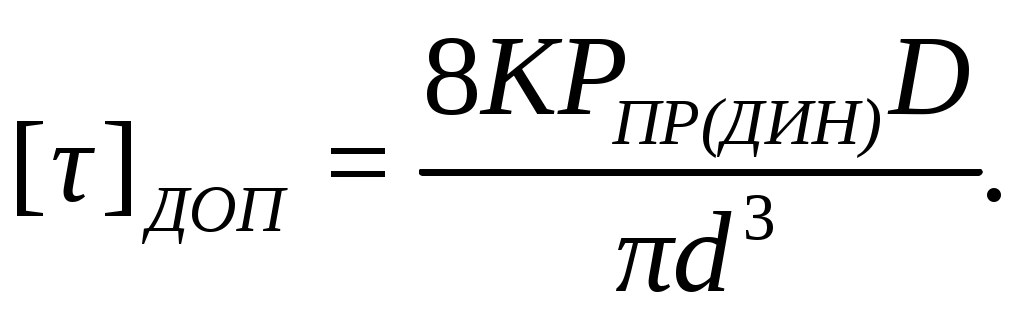
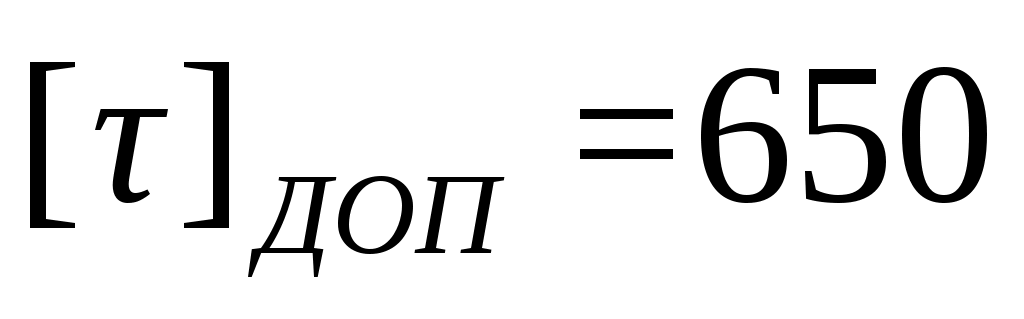
откуда
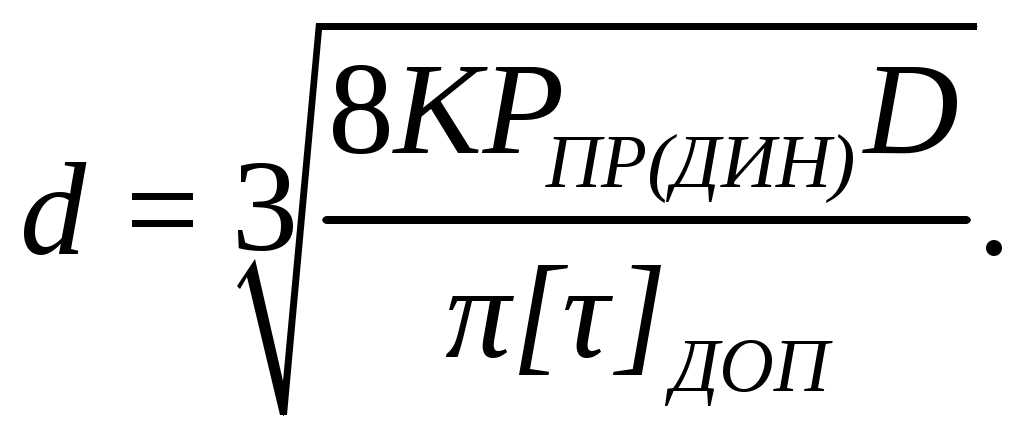
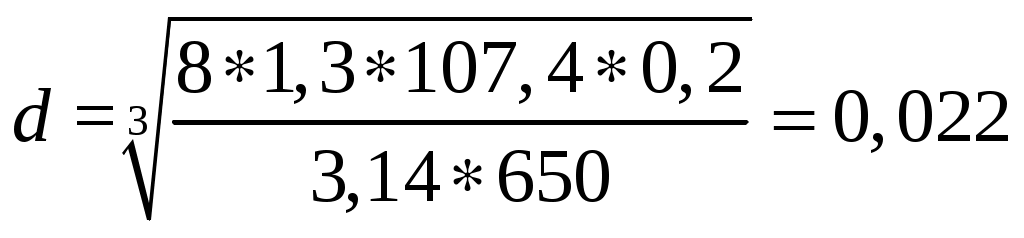
где D – диаметр пружины, м;
К – коэффициент, учитывающий увеличение касательного напряжения в
сечении на внутренней поверхности витка пружины; принять К = 1,3.
Число рабочих витков определяется из уравнения деформации пружины:
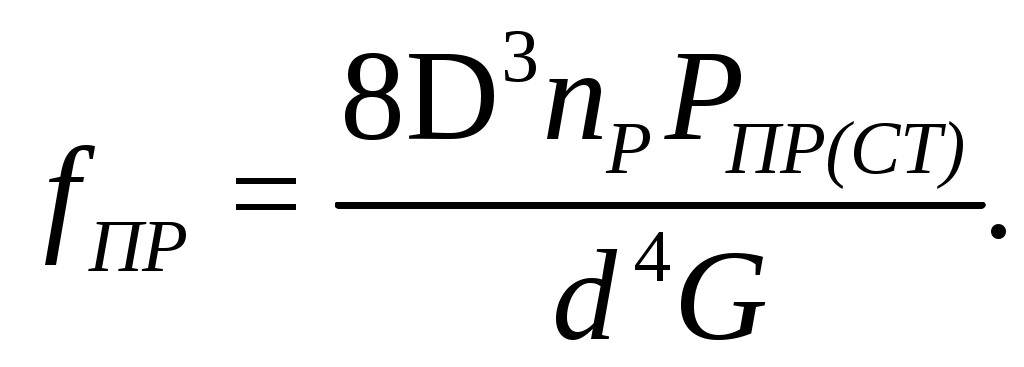
откуда
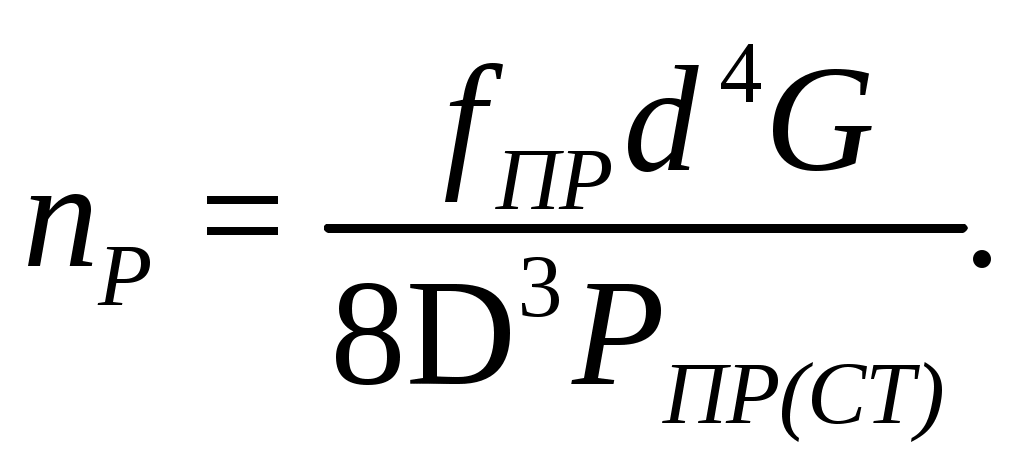
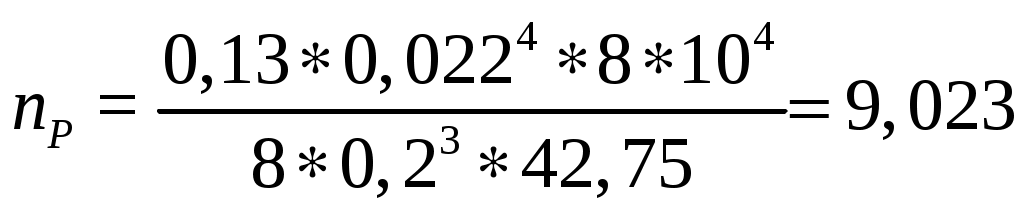
где
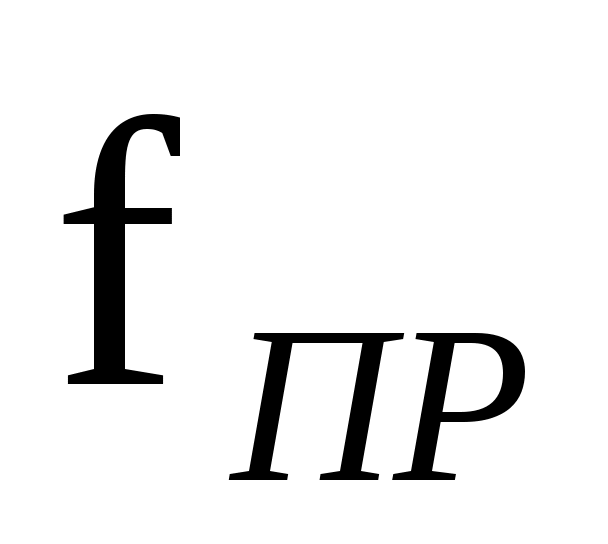