Файл: Отчет о химико технологической практике студентки 3 курса, 306 группы.doc
Добавлен: 11.01.2024
Просмотров: 62
Скачиваний: 1
ВНИМАНИЕ! Если данный файл нарушает Ваши авторские права, то обязательно сообщите нам.
Функции лаборатории:
-контроль за качеством поступающих в Общество с заводов-поставщиков сырья, материалов, комплектующих изделий для изготовления РТИ в необходимом объеме;
-контроль за качеством изготавливаемой Обществом продукции (резиновые смеси и резинотехнические изделия), за их соответствием нормативно-технической документации;
-проведение анализов и испытаний сырья, полуфабрикатов и готовой продукции по заявкам структурных подразделений Общества в необходимом объеме;
-проведение испытаний новых и модифицированных образцов продукции, а так же согласование технической документации на эту продукцию в целях обеспечения соответствия требований НД;
-внедрение в действующее производство совместно с другими подразделениями Общества новых видов сырья и материалов;
-участие в разработке новых методов и приборов для испытания сырья, полуфабрикатов и готовых изделий, и совершенствование действующих;
-разработка предложений о повышении требований к качеству изготавливаемой Обществом продукции, о совершенствовании нормативно-технической документации, устанавливающей эти требования, а также предложений, направленных на стимулирование выпуска продукции высокого качества и борьбу с выпуском несоответствующей продукции;
-выявление причин возникновения дефектов продукции, отмеченных в рекламациях и протоколах испытаний, направленных на предупреждение возникновения брака и устранение дефектов;
-выполнение функций испытательных центров;
-участие в реализации политики в области качества и экологии, в достижении целей в области качества и экологии;
-участие в функционировании и совершенствовании СМК и СЭМ.
Сектор испытания резин и РТИ проводит следующие испытания:
-испытание резин и готовой продукции на упругопрочностные, упругорелаксационные, адгезионные, антистатические свойства, морозостойкость, термостойкость, ударную прочность;
-испытание готовой продукции: определение упрогопрочностных, упругодеформационных, антистатических свойств, стойкость к термическому старению, озоностойкость, морозостойкость, ударная прочность, прочностные характеристики рукавов, ремней, конвейерных лент; испытание изделий медицинского назначения (пробки); стойкость в ненапряженном состоянии к воздействию агрессивных сред, плотность, термостатирование шлангов, подготовка рукавов (старение, морозостойкость) для дальнейшего проведения испытаний ОТК в цехе (разрушающее давление и пр.);
-проведение испытаний входного контроля: ткани, проволока, металл, бинтолента, нити, кордшнуры, шнуры, ленты х/б, канат;
-проведение опытных испытаний от технологического подразделения (отработки и доработки резиновых смесей), при корректировке режимов изготовления и пр.;
-проведение испытаний готовой продукции при выяснении причин брака (от технологического подразделения и цеховые доработки при забраковании продукции).
3.Схема размещения технологического оборудования и рабочих мест ИЛ
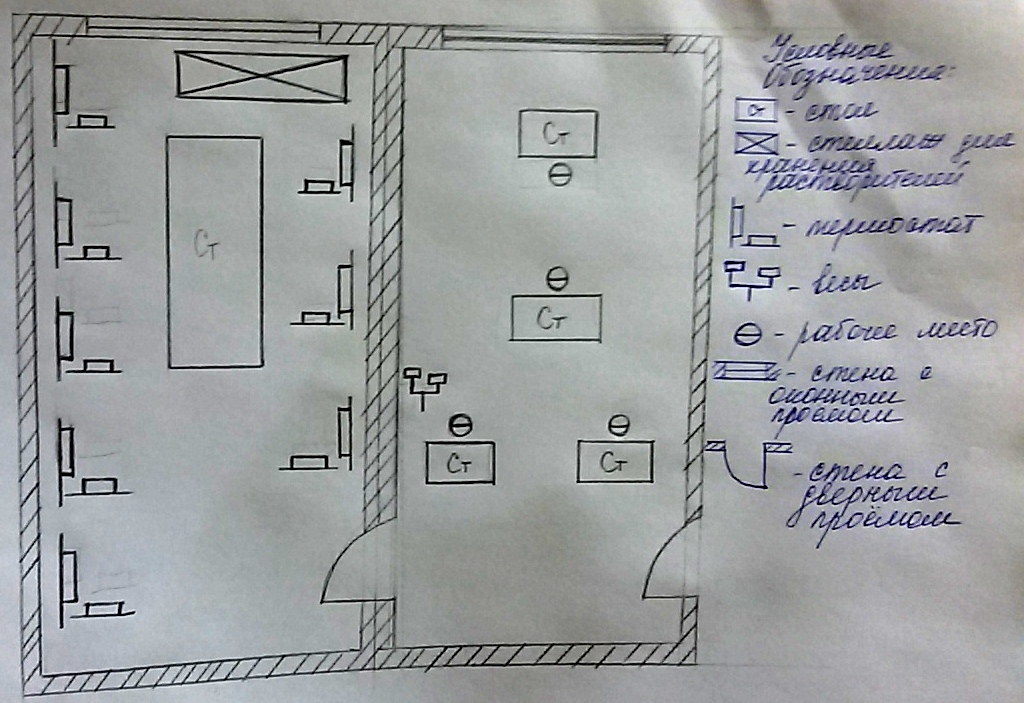
4.Показатели вид продукции ИЛ- объекта практики. Спецификация на конкретный вид продукции ИЛ- объекта практики (с цветным фото).
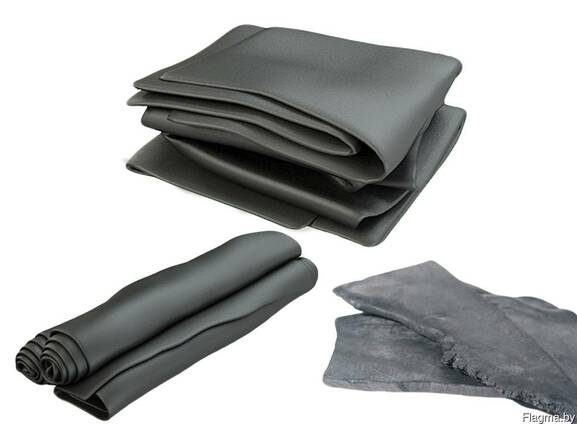
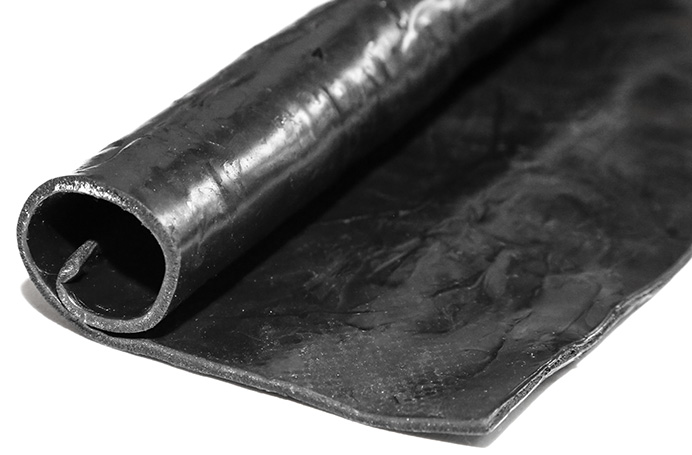
Наименование: | Резина марки 4004(СКН) |
Сопроводительные нормативные документы: | ГОСТ 18829-2017 |
Область применения: | Применяется для изготовления формовых изделий, работающих при многократных деформациях при различных условиях. Маслобензостойкие РТИ используются для изготовления прокладок, колец, сальников, манжет, шлангов, рукавов и др. А также для гуммировки хим. аппаратуры, уплотнителей, шлангов и др. |
Тип эластомера: | Бутадиен-нитрильный (СКН) ![]() |
Прочность при растяжении, мПА
| 3 – 7 10 – 30 |
Минимальная температура эксплуатации (в градусах) | - (15 – 60) |
Максимальная температура эксплуатации (в градусах)
| 90 – 130 110 – 160 |
Твердость по Шору А | 35 – 95 |
Сопротивление раздиру, кН/М | 25 – 85 |
Эластичность по отскоку, %
| 14 – 44 40 – 63 |
Износостойкость: | Х |
Удельное объемное электрическое сопротивление: | П |
Газонепроницаемость: | Х |
Огнестойкость: | П |
Радиационная стойкость: | Х |
Стойкость к окислению: | Х |
Озоностойкость: | У |
Светостойкость: | Х |
Стойкость к действию:
| О У П О О О О О Х У Х О |
Условия хранения: | Резиновые смеси при хранении должны быть защищены от пыли и попадания на них масел, бензина, керосина, и других разрушающих резину веществ, а также от действий кислот, щелочей и газов, вредно влияющих на резину. Резиновые смеси должны храниться в помещении при температуре от минус 5 до плюс 25°С на стеллажах или поддонах на расстоянии не менее 1 м от теплоизлучающих приборов. Резиновые смеси при хранении должны быть защищены от прямых солнечных лучей. Каландрованные резиновые смеси должны храниться на роликах в повешенном состоянии. |
Срок хранения: | Гарантийный срок хранения резиновых смесей ИРП-1078 (группы III-1б-23, III-2в-14, III-2в-23, III-3в-12) и НО-68-1 (группы III-1б-20, III-1б-23, III-2б-20) на летний период составляет 2 месяца. При хранении резиновых смесей в зимний период гарантийный срок хранения может быть увеличен по согласованию между изготовителем и потребителем. По ГОСТ ТУ 22.19.20.-111-75233153-2018 |
* Качественное обозначение некоторых показателей резины:
О – отличные
Х – хорошие
У – удовлетворительные
П – плохие
5. Технологическая схема (ТС) производства конкретной продукции ИЛ - объекта практики.
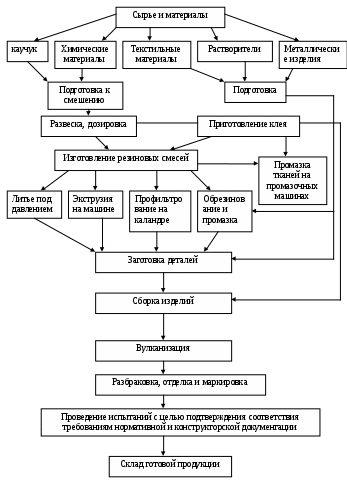
Основным компонентом в производстве резинотехнических изделий является каучук. Синтетические каучуки получают полимеризацией диеновых углеводородов и производных этилена. В промышленном масштабе производятся следующие синтетические каучуки: бутадиеновые, бутадиен-стирольные, бутадиен-метилстирольные, карбоксилатные, бутадиен-метилвинилпиридиновые, бутадиен-нитрильные, хлоропреновые, бутилкаучуки, этилен-пропиленовые, хлорсульфированный полиэтилен, силоксановые, фторкаучуки, акриловые, полисульфидные, уретановые.
Технологический процесс производства резиновых изделий из твёрдых каучуков включает две общие стадии: подготовительную — получение резиновой смеси совмещением каучука с необходимыми ингредиентами в закрытых резиносмесителях или на вальцах и заключительную — вулканизацию полуфабриката резинового изделия при 130 — 220 °С и давлениях 0,3 — 20 МН/м3 (3 — 200 кгс/см2); выбор вулканизационного оборудования (пресс, котёл, аппараты непрерывного действия различной конструкции и др.) определяется видом резиновых изделий. Используемые в производстве многих резиновых изделий текстильные материалы и металл подвергают предварительной обработке, цель которой — обеспечение прочной связи резины с этими материалами в различных условиях эксплуатации резиновых изделий. Текстильные материалы пропитывают на специальных машинах резиновыми клеями или др. адгезионными составами и промазывают на каландрах резиновыми смесями. Металлы обезжиривают органическими растворителями и наносят на них слой клея или латуни (т. н. латунирование, которое осуществляют в гальванической ванне).
Приготовление резиновых смесей – один из основных и ответственных технологических процессов производства резиновых изделий. Сущность процесса заключается в равномерном распределении порошкообразных, твёрдых и жидких ингредиентов в каучуке и получение резиновой смеси, однородной по составу, технологическим свойствам и физико-химическим показателям в результате многократных деформаций растяжения, сжатия, сдвига и кручения многокомпонентной системы, возникающих в процессе смешения.
В зависимости от специфики действия ингредиентов и влияния их на свойства резиновых смесей и вулканизатов ингредиенты подразделяются на несколько групп.
1) Вулканизующие вещества – сера, N,N'-дитиодиморфолин, ZnO, MgO, PbO, CaO, перекись бензоила, перекись кумила, перекись трет-бутила, тиурам, фенолоформальдегидные смолы, диамины, диизоцианаты – химически активные соединения, принимающие участие в образовании пространственной структуры вулканизата.
2) Ускорители вулканизации – MgO, PbO, гашеная известь, дитиокарбаматы, тиурамы, ксантогенаты, тиазолы, сульфенамиды, гуанидины – вещества, которые вводят в резиновую смесь для ускорения процесса вулканизации; активаторы вулканизации – PbO, MgO, CaO, CdO – вещества, в присутствии которых ускорители проявляют наибольшую активность; также активаторы повышают прочность при растяжении и сопротивление раздиру.
3) Наполнители резиновых смесей применяют для увеличения объема резиновой смеси. Активные наполнители – технический углерод, ZnO, MgO, каолин – увеличивают прочность при растяжении резины, сопротивление истиранию и раздиру; неактивные – мел, тальк, барит – не улучшают эти физико-механические свойства резины.
4) Красящие вещества – титановые белила, литопон, ртутная киноварь, CdS, Cr2O3, ультрамарин, пигмент оранжевый Ж – применяют для окраски резины.
5) Пластификаторы (мягчители) – мазут, парафин, вазелин, минеральные масла, каменноугольная смола, канифоль, сосновая смола, стеариновая кислота, олеиновая кислота, сложные эфиры – вещества, облегчающие изготовление и обработку резиновых смесей, снижающие температуру текучести и повышающие их пластичность.
6) Противостарители – фенил-β-нафтиламин, ионол, производные дигидрохинолина, парафин – вещества, которые вводят для замедления окисления и старения каучуков.
7) Ингредиенты специального назначения
Порообразующие вещества – NaHCO3, H2O, диазоаминобензол.
Вещества, предотвращающие преждевременную вулканизацию – бензойная кислота, о-фталевая кислота, фталевый ангидрид, N-нитрозодифениламин.
Ускорители пластикации каучуков – цинковая соль пентахлортиофенола, бис(о-бензамидофенил)дисульфид;
Модификаторы – нитрозопроизводные анилина, комплекс резорцина и уротропина.
Антипирены – Sb2O3, хлорпарафины – вещества, вводимые в резиновые смеси для повышения огнестойкости резины.
одоранты – гераниол, верникол, мирценаль – душистые вещества, применяемые для придания приятного запаха.
8) Вспомогательные материалы
антиадгезивы – мел, тальк, каолин, ПАВ – применяются для предохранения от склеивания и слипания полуфабрикатов.
смазочные материалы – полиметилсилоксановые жидкости, глицерин – применяются для облегчения выемки вулканизованных изделий из форм и для предупреждения их «приваривания» к формам.
Резиновая смесь представляет собой дисперсную сисетему, в которой каучук и растворенные в нем низкомолекулярные соединения (пластификаторы, противостарители) составляют непрерывную дисперсионную среду, а наполнители – дисперсную фазу.
В производство допускаются ингредиенты с влажностью 0,2 – 2,5 % в зависимости от гигроскопичности материала. При повышенной влажности качество получаемых изделий ухудшается, поэтому проводят сушку ингредиентов. При необходимости проводят измельчение, а также просев.
Для придания каучуку необходимой пластичности, с целью облегчения его дальнейшей обработки при смешении каучук пластицируют (механическая и термоокислительная пластикация).
Процесс смешения на вальцах можно подразделить на стадии: вальцевание каучука, введение ½ наполнителя, перемешивание, введение ½ наполнителя, введение диспергаторов и мягчителей, перемешивание, введение активаторов и ускорителей, перемешивание, введение противостарителей, красителей, ингредиентов специального назначения, перемешивание, введение вулканизирующего агента.
Резиновые смеси могут подвергаться каландрованию. К процессам каландрования относится листование и профилирование резиновых смесей для получения листов с гладкой поверхностью или с рисунком и профилированных листов с фигурным сечением, промазка тканей и обкладка тканей резиновой смесью, дублирование на каландрах.
Шприцевание – процесс формования заготовок заданного профиля (шнур, трубка) путем продавливания пластичной, предварительно разогретой резиновой смеси через профилирующее отверстие соответствующей формы и размеров под большим давлением. Осуществляется на шприц-машинах.
Сущность процесса литья резиновых смесей под давлением состоит в заполнении формы предварительно разогретой резиновой смесью при высоком давлении – 30 – 150 МПа. Заполнение формы производят через литьевой канал диаметром 10 – 12 мм.
При растворении резиновой смеси в соответствующем растворителе получают резиновый клей. Резиновые клеи применяют при сборке резиновых изделий из отдельных деталей для придания их поверхности достаточной клейкости, для промазки тканей при их прорезинивании. Путем промазки на клеепромазочных машинах изготовляют прорезиненные ткани широкого потребления и технического назначения: одежные, для спецодежды, для резиновой обуви.