Файл: Курсовая работа по разработке управленческих решений Разработка управленческих решений по развитию системы мотивации кадров.docx
Добавлен: 06.11.2023
Просмотров: 66
Скачиваний: 3
ВНИМАНИЕ! Если данный файл нарушает Ваши авторские права, то обязательно сообщите нам.
(4)
где п - количество деталей в обрабатываемой партии, штук;
к — число операций технологического процесса;
tШТі — норма времени на выполнение операции, минут.
Если при выполнении отдельных последовательных операций имеющиеся параллельные рабочие места, то продолжительность операционного цикла будет определяться по формуле (5):
(5)
где Ми - количество рабочих мест, занятых изготовлением партии деталей на каждой операции.
При последовательном виде движения деталей (изделий) отсутствуют перерывы в работе оборудования и рабочего на каждой операции, возможная высокая загрузка оборудования на протяжении изменения, но производственный цикл имеет наибольшую величину, которая уменьшает обращение оборотных средств.
Параллельный вид движения характеризуется передачей деталей (изделий) на следующую операцию немедленно после выполнения предыдущей операции независимо от готовности других деталей (изделий) в партии. Детали передаются из операции на операцию или поштучно операционными партиями. Процесс происходит беспрерывно, если достигнутая кратность выполнения операций во времени. Это характерно для поточных линий, такт которых исчисляется и подчинено правилу (6):
(6)
где r - такт поточной линии, минут.
Параллельный вид движения деталей (изделий) есть наиболее эффективным, но возможности его применения ограниченные, так как обязательным условием такого движения есть, как уже отмечалось, кратность продолжительности выполнения операций. В противоположном случае неминуемыми есть потери (перерыва) в работе оборудования и рабочего.
Операционный цикл партии обрабатываемых параллельно деталей определяется по формуле (7):
(7)
где tшTmax - время выполнения наиболее продолжительной в технологическом процессе операции, минут.
При передаче деталей (изделий) операционными партиями расчет операционного цикла осуществляется за формулой (8):
(8)
где р - размер операционной партии, в штуках.
Параллельно-последовательный (смешанный)
вид движения заключается в том, что изготовление деталей (изделий) на следующей операции начинается к истечению изготовления всей партии на предыдущей операции с таким расчетом, чтобы работа на каждой операции по обработке партии деталей (изделий) осуществлялась без перерывов. В отличие от параллельного вида движения здесь происходит лишь частичное соединение во времени выполнения сопредельных операций.
На практике существует два вида соединения сопредельных операций при условиях, когда:
- время выполнения следующей операции больше времени выполнения предыдущей операции;
- время выполнения следующей операции меньше времени выполнения предыдущей операции.
В первом случае целесообразно применять параллельный вид движения деталей и полностью загрузить рабочие места.
Во втором случае приемлемым есть параллельно-последовательный вид движения с максимально возможным соединением во времени выполнения обеих операций. Максимально соединенные операции при этом отличаются на время изготовления последней детали (последней ли операционной партии) на следующей операции.
Таким образом, продолжительность операционного цикла партии обрабатываемых параллельно-последовательным (смешанным) способом деталей определяется по формуле (9
(9)
где tшт кор и - время выполнения кратчайшей из сопредельных в технологическом процессе операций, минут.
При передаче деталей операционными партиями (р) расчет продолжительности операционного цикла осуществляется за формулой (10):
(10)
Параллельно-последовательный вид движения деталей (изделий) обеспечивает работу оборудования и рабочего без перерывов. Продолжительность производственного цикла при этом виде движения длинная в сравнении с параллельным, но меньшая, чем при последовательном.
Производственный цикл изделия (ТцВ) может быть рассчитанный за формулой (11):
(11)
где Тцд - производственный цикл изготовления ведущей детали;
ТцР - производственный цикл сборочных работ.
При определении продолжительности производственных циклов для разных видов движения обрабатываемых деталей (изделий) не были учтены перерывы. Итак, с учетом перерывов формула для определения продолжительности операционного цикла видоизменяется. Например, при последовательном движении (в календарных днях) она принимает вид (12):
(12)
где Тзм- продолжительность изменения, минут;
Пзм- количество изменений;
Кпер- переводной коэффициент (способ переведения рабочих дней в календарные);
Тмо - время межоперационных перерывов, минут;
Тпр - время естественных процессов, минут.
Сокращение производственного цикла имеет большое экономическое значение:
Длительность производственного цикла зависит от двух важнейших групп факторов:
Эти обе группы факторов взаимообуславливают и дополняют друг друга.
Основными направлениями снижения производственного цикла являются:
Поточное производство является наиболее эффективной формой организации производственного процесса.
Признаки поточного производства:
При поточном производстве реализуются принципы:
Поточное производство обеспечивает самую высокую производительность труда, низкую себестоимость продукции, наиболее короткий производственный цикл.
Основой (первичным звеном) поточного производства является поточная линия.
Расположение поточных линий (планировка) должна обеспечить:
Одной из актуальных задач всех предприятия является разработка мероприятий, связанных с сокращением длительности производственного цикла. Ее сокращают одновременно по двум направлениям: уменьшают рабочий период цикла и полностью ликвидируют или сводят к минимуму различные перерывы.
Все практические мероприятия по сокращению производственного цикла вытекают из принципов построения производственного процесса, в первую очередь из принципов пропорциональности, параллельности и непрерывности. Чем быстрее совершается производственный процесс (чем меньше длительность производственного цикла), являющийся одним из элементов кругооборота оборотных средств, тем больше будет и скорость их оборачиваемости, тем большее число оборотов они совершают в течение года, тем меньшая будет потребность в них для выполнения заданной производственной программы.
В результате происходит высвобождение денежных ресурсов, которые могут быть использованы для расширения производства на данном предприятии.
По этой же причине происходит сокращение объема незавершенного производства. А это означает высвобождение оборотных средств в их вещественной форме, т.е. в форме конкретных материальных ресурсов. Производственная мощность предприятия или цеха прямо зависит от длительности производственного цикла. Под производственной мощностью понимается максимально возможный выпуск продукции в плановом периоде. И поэтому ясно, что чем меньше затрачивается времени на производство одного изделия, тем большее их число может быть изготовлено за тот же период времени.
Путями сокращения длительности производственного цикла являются:
а) технический прогресс производства;
б) совершенствование организации труда;
в) производства и управления.
Эти группы факторов дополняют друг друга.
Обобщая вышесказанное, отметим основные направления снижения производственного цикла:
а) совершенствование технологий;
б) применение более производительных оборудования, инструментов, средств технологического оснащения;
в) автоматизация производственных процессов;
г) специализация и кооперирование производства;
д) организация поточного производства;
е) гибкость (многофункциональность) персонала.
Мероприятия по сокращению длительности производственного цикла дают комплексный экономический эффект. Они создают предпосылки улучшения использования производственных мощностей, снижения удельного веса накладных расходов в себестоимости единицы продукции.
Таким образом, сокращение длительности производственного цикла - один из важных источников интенсификации и повышения эффективности производства.
Сокращение длительности производственного цикла представляет собой одну из наиболее важных задач организации производства на предприятии, от надлежащего решения, которой в большой мере зависит его эффективная, рентабельная работа.
Технологическое время и время перерывов существенно сокращается в итоге совершенствования конструкций выпускаемой продукции, увеличения уровня ее технологичности, внедрения более оптимальных высокоэффективных технологических процессов, увеличения уровня механизации и автоматизации, внедрения робототехники. Сокращение трудозатратности технологических операций достигается методом использования более совершенного оборудования, подмены металла пластмассами, внедрения действенной специальной и универсальной оснастки.
Для совершенствования процессов контроля, транспортировки и складирования деталей целенаправленно их совмещение по времени с технологическим циклом, как это происходит, к примеру, на роторных автоматических линиях. Внедрение статистических способов контроля свойства продукции и регулирование технологических процессов позволяет перейти от сплошного контроля к выборочному, снижая тем время контрольных операций.
Сокращение времени транспортных и складских операций достигается с их помощью механизации и автоматизации, поэтому не только лишь ускоряется их выполнение, да и создается высочайшая степень надежности обслуживания производственного процесса.
где п - количество деталей в обрабатываемой партии, штук;
к — число операций технологического процесса;
tШТі — норма времени на выполнение операции, минут.
Если при выполнении отдельных последовательных операций имеющиеся параллельные рабочие места, то продолжительность операционного цикла будет определяться по формуле (5):
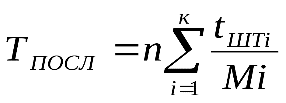
где Ми - количество рабочих мест, занятых изготовлением партии деталей на каждой операции.
При последовательном виде движения деталей (изделий) отсутствуют перерывы в работе оборудования и рабочего на каждой операции, возможная высокая загрузка оборудования на протяжении изменения, но производственный цикл имеет наибольшую величину, которая уменьшает обращение оборотных средств.
Параллельный вид движения характеризуется передачей деталей (изделий) на следующую операцию немедленно после выполнения предыдущей операции независимо от готовности других деталей (изделий) в партии. Детали передаются из операции на операцию или поштучно операционными партиями. Процесс происходит беспрерывно, если достигнутая кратность выполнения операций во времени. Это характерно для поточных линий, такт которых исчисляется и подчинено правилу (6):

где r - такт поточной линии, минут.
Параллельный вид движения деталей (изделий) есть наиболее эффективным, но возможности его применения ограниченные, так как обязательным условием такого движения есть, как уже отмечалось, кратность продолжительности выполнения операций. В противоположном случае неминуемыми есть потери (перерыва) в работе оборудования и рабочего.
Операционный цикл партии обрабатываемых параллельно деталей определяется по формуле (7):
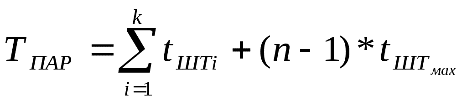
где tшTmax - время выполнения наиболее продолжительной в технологическом процессе операции, минут.
При передаче деталей (изделий) операционными партиями расчет операционного цикла осуществляется за формулой (8):
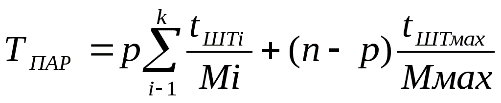
где р - размер операционной партии, в штуках.
Параллельно-последовательный (смешанный)
вид движения заключается в том, что изготовление деталей (изделий) на следующей операции начинается к истечению изготовления всей партии на предыдущей операции с таким расчетом, чтобы работа на каждой операции по обработке партии деталей (изделий) осуществлялась без перерывов. В отличие от параллельного вида движения здесь происходит лишь частичное соединение во времени выполнения сопредельных операций.
На практике существует два вида соединения сопредельных операций при условиях, когда:
- время выполнения следующей операции больше времени выполнения предыдущей операции;
- время выполнения следующей операции меньше времени выполнения предыдущей операции.
В первом случае целесообразно применять параллельный вид движения деталей и полностью загрузить рабочие места.
Во втором случае приемлемым есть параллельно-последовательный вид движения с максимально возможным соединением во времени выполнения обеих операций. Максимально соединенные операции при этом отличаются на время изготовления последней детали (последней ли операционной партии) на следующей операции.
Таким образом, продолжительность операционного цикла партии обрабатываемых параллельно-последовательным (смешанным) способом деталей определяется по формуле (9

где tшт кор и - время выполнения кратчайшей из сопредельных в технологическом процессе операций, минут.
При передаче деталей операционными партиями (р) расчет продолжительности операционного цикла осуществляется за формулой (10):

Параллельно-последовательный вид движения деталей (изделий) обеспечивает работу оборудования и рабочего без перерывов. Продолжительность производственного цикла при этом виде движения длинная в сравнении с параллельным, но меньшая, чем при последовательном.
Производственный цикл изделия (ТцВ) может быть рассчитанный за формулой (11):

где Тцд - производственный цикл изготовления ведущей детали;
ТцР - производственный цикл сборочных работ.
При определении продолжительности производственных циклов для разных видов движения обрабатываемых деталей (изделий) не были учтены перерывы. Итак, с учетом перерывов формула для определения продолжительности операционного цикла видоизменяется. Например, при последовательном движении (в календарных днях) она принимает вид (12):

где Тзм- продолжительность изменения, минут;
Пзм- количество изменений;
Кпер- переводной коэффициент (способ переведения рабочих дней в календарные);
Тмо - время межоперационных перерывов, минут;
Тпр - время естественных процессов, минут.
Сокращение производственного цикла имеет большое экономическое значение:
-
сокращается оборачиваемость оборотных средств за счет сокращения объемов незавершенного производства; -
увеличивается фондоотдача основных производственных фондов; -
снижается себестоимость изделий за счет сокращения условно-постоянной части издержек на одно изделие и т.д.
Длительность производственного цикла зависит от двух важнейших групп факторов:
-
технического уровня производства; -
организации производства.
Эти обе группы факторов взаимообуславливают и дополняют друг друга.
Основными направлениями снижения производственного цикла являются:
-
совершенствование технологии; -
применение более производительных оборудования, инструментов, средств технологического оснащения; -
автоматизация производственных процессов и применение гибких интегрированных процессов; -
специализация и кооперирование производства; -
организация поточного производства; -
гибкость (многофункциональность) персонала; -
многие другие факторы, влияющие на длительность производственного цикла.
Поточное производство является наиболее эффективной формой организации производственного процесса.
Признаки поточного производства:
-
закрепление одного или ограниченного числа наименований изделий за определенной группой рабочих мест; -
ритмическая повторяемость согласованных во времени технологических и вспомогательных операций; -
специализация рабочих мест; -
расположение оборудования и рабочих мест по ходу технологического процесса; -
применение специальных транспортных средств для межоперационной передачи изделий.
При поточном производстве реализуются принципы:
-
специализации; -
параллельности; -
пропорциональности; -
прямоточности; -
непрерывности; -
ритмичности.
Поточное производство обеспечивает самую высокую производительность труда, низкую себестоимость продукции, наиболее короткий производственный цикл.
Основой (первичным звеном) поточного производства является поточная линия.
Расположение поточных линий (планировка) должна обеспечить:
-
прямоточность и кратчайший путь движения изделия; -
рациональное использование производственных площадей; -
условия для транспортировки материалов и деталей к рабочим местам; -
удобство подходов для ремонта и обслуживания; -
достаточность площадей и оргоснастки для хранения требуемых запасов материалов и готовых деталей; -
возможность легкого удаления отходов производства.
-
Направления сокращения производственного цикла.
Одной из актуальных задач всех предприятия является разработка мероприятий, связанных с сокращением длительности производственного цикла. Ее сокращают одновременно по двум направлениям: уменьшают рабочий период цикла и полностью ликвидируют или сводят к минимуму различные перерывы.
Все практические мероприятия по сокращению производственного цикла вытекают из принципов построения производственного процесса, в первую очередь из принципов пропорциональности, параллельности и непрерывности. Чем быстрее совершается производственный процесс (чем меньше длительность производственного цикла), являющийся одним из элементов кругооборота оборотных средств, тем больше будет и скорость их оборачиваемости, тем большее число оборотов они совершают в течение года, тем меньшая будет потребность в них для выполнения заданной производственной программы.
В результате происходит высвобождение денежных ресурсов, которые могут быть использованы для расширения производства на данном предприятии.
По этой же причине происходит сокращение объема незавершенного производства. А это означает высвобождение оборотных средств в их вещественной форме, т.е. в форме конкретных материальных ресурсов. Производственная мощность предприятия или цеха прямо зависит от длительности производственного цикла. Под производственной мощностью понимается максимально возможный выпуск продукции в плановом периоде. И поэтому ясно, что чем меньше затрачивается времени на производство одного изделия, тем большее их число может быть изготовлено за тот же период времени.
Путями сокращения длительности производственного цикла являются:
а) технический прогресс производства;
б) совершенствование организации труда;
в) производства и управления.
Эти группы факторов дополняют друг друга.
Обобщая вышесказанное, отметим основные направления снижения производственного цикла:
а) совершенствование технологий;
б) применение более производительных оборудования, инструментов, средств технологического оснащения;
в) автоматизация производственных процессов;
г) специализация и кооперирование производства;
д) организация поточного производства;
е) гибкость (многофункциональность) персонала.
Мероприятия по сокращению длительности производственного цикла дают комплексный экономический эффект. Они создают предпосылки улучшения использования производственных мощностей, снижения удельного веса накладных расходов в себестоимости единицы продукции.
Таким образом, сокращение длительности производственного цикла - один из важных источников интенсификации и повышения эффективности производства.
Сокращение длительности производственного цикла представляет собой одну из наиболее важных задач организации производства на предприятии, от надлежащего решения, которой в большой мере зависит его эффективная, рентабельная работа.
Технологическое время и время перерывов существенно сокращается в итоге совершенствования конструкций выпускаемой продукции, увеличения уровня ее технологичности, внедрения более оптимальных высокоэффективных технологических процессов, увеличения уровня механизации и автоматизации, внедрения робототехники. Сокращение трудозатратности технологических операций достигается методом использования более совершенного оборудования, подмены металла пластмассами, внедрения действенной специальной и универсальной оснастки.
Для совершенствования процессов контроля, транспортировки и складирования деталей целенаправленно их совмещение по времени с технологическим циклом, как это происходит, к примеру, на роторных автоматических линиях. Внедрение статистических способов контроля свойства продукции и регулирование технологических процессов позволяет перейти от сплошного контроля к выборочному, снижая тем время контрольных операций.
Сокращение времени транспортных и складских операций достигается с их помощью механизации и автоматизации, поэтому не только лишь ускоряется их выполнение, да и создается высочайшая степень надежности обслуживания производственного процесса.