Файл: Проектирование производственного участка сборки и сварки двутавровой балки.docx
Добавлен: 08.11.2023
Просмотров: 869
Скачиваний: 28
ВНИМАНИЕ! Если данный файл нарушает Ваши авторские права, то обязательно сообщите нам.
Контроль качества сварки состоит в следующем:
– проверяют последовательность и режим сварки узла или конструкции согласно заданному технологическому процессу;
– проверяют качество сварных швов и их размеры соответственно чертежу наружным осмотром, шаблонами и другими способами, указанными в технологическом процессе.
Контроль сварных швов внешним осмотром выполняют пооперационно:
- швы должны иметь гладкую или равномерно-чашуйчатую поверхность без наплывов, прожогов, сужений и перерывов и не иметь резкого перехода к основному металлу.
- угловые швы должны выполняться с плавным переходом к основному металлу и не иметь несплавлений по кромкам;
- наплавленный металл должен быть плотным по всей длине шва и не иметь трещин;
- подрезы основного металла допускаются глубиной не более 1 мм;
- все кратеры должны быть заварены.
- выявляют отклонения от прямолинейности сваренных узлов и изделий в пределах допусков.
Визуально измерительный контроль производится с помощью лупы 4-х-10-ти кратного увеличения и измерительных инструментов: шаблонов и катетомеров.
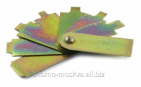
Рис 2. 9 Набор катетомеров сварщика кмс-3-16.
Измерительный контроль является более совершенным, т.к. осуществляется с помощью разнообразных технических средств контроля.
Проверка размеров разделки кромок производится специальными шаблонами, а исправление – при помощи повторной или дополнительной механической обработки.
Контроль размеров зазоров производится специальными шаблонами – щупами.
Предлагаю проверять с помощью визуального контроля 100% длины швов.
Рентгенографический контроль
Предлагаю проверять рентгенографическим контролем – 20% суммы длины швов. Рентгеновские лучи проникают сквозь металл и понижают свою интенсивность вследствие поглощения их металлом. Лучи ослабляются сильнее в тех случаях, когда они встречают на своём пути более плотный металл. Имеющиеся в сварном шве шлаковые включения, газовые поры, трещины или другие дефекты будут в большей степени пропускать рентгеновские лучи, чем плотный металл шва. Рентгеновские лучи оказывают такое же действие на рентгеновскую плёнку, как и световые, лучи. При рентгеновском просвечивании сварного шва в местах его пороков на негативе получаются более темные пятна и полосы, имеющие форму порока, вследствие более интенсивного прохождения лучей через эти дефектные места. На снимках дефектные места видны в виде светлых пятен и полос такой же формы.
Рентгеновское просвечивание стальных элементов целесообразно производить при толщине детали до 100 мм.
По каждому рентгеновскому снимку составляется длина просвеченного участка шва в мм, характер дефектов, их размеры в мм, и количество дефектов на этом участке.
По характеру распределения дефекты объединяются в следующие группы (ГОСТ 7512-82):
Группа А – отдельные дефекты
Группа Б – цепочка дефектов
Группа В-скопление дефектов
Оценка качества шва по рентгеновским снимкам устанавливается путём сравнения с другими снимками, принятыми за эталоны для данного типа конструкции.
Она состоит из следующих операций:
-
разметка изделия для выделения участков сварных швов подлежащих просвечиванию; -
выбор режима просвечивания/по таблицам и графикам; -
установка рентгеновской трубки и кассеты с пленкой; -
облучение шва; -
фотообработка пленки; -
определение качества снимка по чувствительности, вычисляемой с помощью эталонов; -
оценки качества шва.
Кассеты для рентгеносъемки изготавливают из черной бумаги, резины,
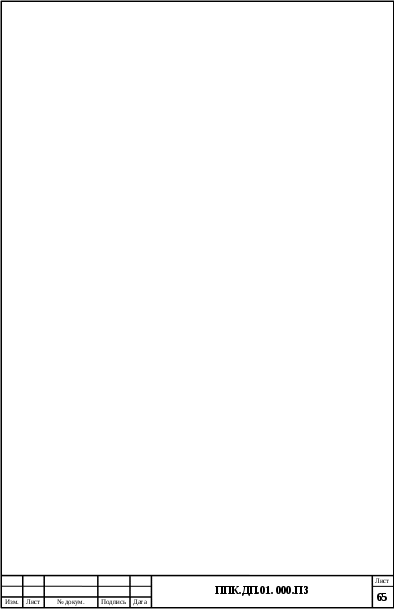
В зависимости от толщины контролируемого металла применяется один из четырех типов эталонов, регламентируемых ГОСТ 7512-82 и представляющих собой пластинки из того же материала, что и просвечиваемое изделие, с канавками разной глубины.
Сварные соединения следует просвечивать по схеме (рис. 2), рекомендуемой ГОСТ 7512–82.

Рис.2.10. Схема просвечивания таврового соединения. 1 – источник излучения; 2 – кассета с радиографической пленкой.
- 1 2 3 4 5 6 7
Разработка маршрутной технологии сборки и сварки
Маршрутная карта оформляется в соответствии с ГОСТ 3.1118-82 и применяется при разработке технологических процессов изготовления или ремонта изделий в основном и вспомогательном производствах. Маршрутная карта (МК) является составной и неотъемлемой частью комплекта технологических документов. Формы МК являются унифицированными, и их следует применять независимо от типа и характера производства и степени детализации описания технологических процессов.
При маршрутном и маршрутно-операционном описании технологического процесса МК является одним из основных документов, в котором описывается весь процесс в технологической последовательности выполнения операций.
При операционном описании технологического процесса МК выполняет роль сводного документа, в котором указывается адресная информация (номер цеха, участка, рабочего места, операции), наименование операции, перечень документов, применяемых при выполнении операции, технологическое оборудование и трудозатраты.
Оформление форм, бланков и документов осуществляется по ГОСТ 3.1130-93.
Обе операции – сборка и сварка – излагаются подробно в одном документе, чередуясь в том порядке, какой требуется для изготовления изделия.
Схема сборки и сварки двутавровой балки представлена на рис.2.10
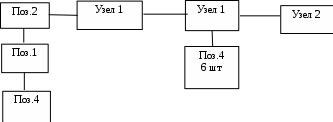
Рисунок 2.10. Схема сборки и сварки двутавровой балки.
Маршрутная технология сборки и сварки двутавровой балки включает в себя следующие операции (таблица 2.6).
Таблица 2.6. Операции сборки и сварки двутавровой балки (рис.1.1)
№ операции | Наименование операции Содержание перехода |
1 | 2 |
005 | Подготовка |
| 1) Скомплектовать детали согласно чертежу и спецификации; |
2) Проверить геометрические размеры заготовок по чертежу; | |
3) Зачистить места соединений под сварку до чистого металла на ширину 20 мм. | |
010 | Узел 1 Сборка |
| 1) Установить на опорную балку стенку поз. 4 |
2) Установить верхнюю полку поз. 1 и нижнюю полку поз. 2 – вдоль балок на опорные винты | |
3) Поджать стенку поз. 4, верхнюю полку поз. 1 и нижнюю полку поз. 2 пневмоприжимами | |
4) Прихватить полуавтоматической сваркой в среде углекислого газа стенку поз. 3 с верхней полкой поз. 1 и нижней полкой поз. 2 тавровыми двусторонними швами, L пр.= 50–60 мм, количество - 2. | |
5) Включить портал, передвинуть к месту следующей прихватки, на шаг прихватки 350–400 мм | |
6) Прихватить полуавтоматической сваркой в среде углекислого газа стенку поз. 4 с верхней полкой поз. 1 и нижней полкой поз. 2 тавровыми двусторонними швами, L пр.= 50–60 мм, количество -2. | |
7) Повторить переходы 5,6 – 19 раз. | |
8) Отвести портал; | |
9). Отжать прижимы; | |
10). Проверить качество сборки внешним осмотром; | |
11) Сдать ОТК – ВИК-100%. | |
12). Передать на сварку | |
015 | Узел 1 Сварка |
| 1) Установить узел 1 на цепной кантователь прихватками вниз; |
2) Сварить автоматической сваркой под флюсом в нижнем положении угловые швы тавровых соединений Т3-Δ6 без разделки кромок однопроходным швом. | |
3) Кантовать узел на 180º; | |
4) Повторить переход 3. | |
5). Проверить качество сварки внешним осмотром; | |
6) Сдать ОТК – ВИК-100% и 20% сварных швов контролировать рентгенографическим способом. | |
7). Передать на сборку | |
020 | Узел 2. Сборка |
| 1).Установить узел 1 на сборочно-сварочную плиту; |
2).Разметить под установку ребер жесткости поз. 3 – 6 шт. стенку поз. 4, верхнюю полку поз. 1 и нижнюю полку поз.2. | |
3).Пристыковать ребро жесткости поз. 3 по разметке к стенке поз. 3, верхней полке поз. 1 и нижней полке с помощью угольника поверочного; | |
4).Прихватить полуавтоматической сваркой в среде углекислого газа ребро поз. 3 со стенкой поз. 4, верхней полкой поэ.1 и нижней полкой поз. 2 тавровыми двухсторонними швами Т3- Δ6, L пр.= 20–30 мм, по две на стык стенки с ребром и по одной на стыки верхней полкой поэ.1 и нижней полкой поз. 2 с ребром, общее количество прихваток – 8. | |
5) Повторить переходы 3,4 – 6 раз. | |
6) Проверить качество сборки внешним осмотром; | |
7) Зачистить сварные швы и околошовную зону от брызг после сварки; | |
8) Проверить качество сборки внешним осмотром; | |
9) Сдать ОТК – ВИК-100%. | |
025 | Узел 2. Сварка |
| 1) Сварить полуавтоматической сваркой в среде углекислого газа ребра жесткости поз. 3 к стенке поз. 4 с верхней полкой поэ.1 и нижней полкой поз. 2 тавровым однопроходным швом Т3-Δ6 |
3) Сдать ОТК – ВИК-100%.; рентгенографический контроль – 20% суммарной длины швов | |
030 | Правка грибовидности |
035 | Фрезерование торцов балки. |
Заполненная маршрутная карта на технологический процесс сборки и сварки двутавровой балки размещена в приложении 1.
-
Расчетная часть-
Нормирование сварных работ
-
Нормирование сборочных работ
Операция 010. Сборка Узел1
Нормирование произведем по укрупненным нормативам [14].

Подберем нормы штучного времени по таблицам.
где tуст - время на установку одной позиции, tуст =1,5-2 мин;
nпоз - число позиций, из которых собирается узел;
tфикс - время на фиксацию одной позиции, tфикс=1,0-1,5 мин;
nфикс - число фиксаций на собираемый узел, nфикс =2;
Lшв - суммарная длина швов собираемого узла, м;
tприхв - время на одну прихватку, tприхв =0,5 мин;
lшаг - шаг прихваток, lшаг =0,5 м;
tкант - время на один полный поворот при кантовке изделия,
tкант= 0мин;
nкант - число кантовок на узел;
tп.св - время на один переход сварщика в процессе сборки узла,
tп.св =0,1 мин;
nп.св – число переходов сварщика, nп.св=Lшв/2lшаг ;
tвсп - вспомогательное время, tвсп =2,5 мин/изд;

Операция 015. Сварка Узел1
Используем расчетно-аналитический метод [1].
Расчет штучного времени автоматической сварки производится по формуле, мин:


где То – основное время, Твш – вспомогательное время, зависящее от длины шва, мин/пог. м, Тви
– вспомогательное время, связанное с изделием и работой оборудования, мин, К1 – коэффициент, учитывающий затраты времени на обслуживание рабочего места, отдых и на естественные надобности сварщика, по таблице 89 [1] К1 = 1,12.
Рассчитаем норму штучного времени на сварку узла 1.
Основное время сварки одного погонного метра однопроходного шва определяется по формулам, мин, автоматической сварки:

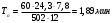
Твш рассчитываем по таблице 85 [1]:
- зачистка и осмотр свариваемых кромок (без скоса) – 0,30 мин/пог.м;
- корректировка электрода относительно оси шва с перемещением автомата вручную – 0,15 мин/пог.м;
- возврат сварочного трактора в исходное положение – 0,10 мин/пог.м;
- сбор флюса со шва и ссыпка его в бункер – 0,40 мин/пог.м;
- очистка шва от шлака и промер шва – 0,40 мин/пог.м.
Твш = 0,30+0,15+0,10+0,40+0,40 = 1,35 мин/пог.м.
Тви рассчитывается по таблице 87 [1]:
- время на установку изделия – 4,7мин;
- время на поворот кантователем– 0,35 мин;
- время на снятие – 3,1 мин;
- время установку трактора – 2,7 мин;
- время на установку головки трактора – 1,0 мин;
- время на засыпку флюса в бункер, установку электродной проволоки, опускание проволоки – 1,6 мин.
Тви = 4,7+0,35+3,1+2,7+1,0+1,6 = 11,85 мин.
Длина шва lш = 12∙4 = 48м.
Тогда
Тш = [(1,89+1,35)48+11,85] ∙1,12 = 187,5мин = 3,13час.
Операция 020. Сборка Узел 2.
Производим нормирование по укрупненным нормативам [14].
Тп.з = 10 мин.= 0,17 час
Тш = (1,93 + 0,08) ∙1,1 = 2,01∙1,1 = 2,22час
Тшк.= 2,22 + 0,17 = 2,39 час
Операция 025. Сварка Узел 2.
Применим укрупненные нормативы времени [13].
Тш = [(То + tв.ш) ∙Lш + t в.и] ∙К2 , мин
Подберем нормы штучного времени по таблицам.
То = 5,7 мин.