Файл: Содержание. Введение. Основная часть. Технологическая часть.docx
Добавлен: 08.11.2023
Просмотров: 64
Скачиваний: 1
ВНИМАНИЕ! Если данный файл нарушает Ваши авторские права, то обязательно сообщите нам.
СОДЕРЖАНИЕ.
1. Введение.
2. Основная часть.
2.1. Технологическая часть.
2.1.1. Характеристика металла конструкции.
2.1.2. Подготовка металла к сварке.
2.1.3. Технология ручной дуговой сварки покрытыми
электродами.
2.1.4. Основные характеристики сварочных материалов,
оборудования и приспособлений.
2.1.5. Выбор режима сварки.
2.1.6. Техника ручной дуговой сварки покрытыми электродами.
2.1.7. Контроль качества сварки, возможные дефекты и
способы их исправления.
2.2. Творческая часть.
2.2.1. Характеристика материала конструкции.
2.2.2. Подготовка металла к сварке.
2.2.3. Основные характеристики сварочных материалов,
оборудования и приспособлений.
2.2.4. Выбор режима сварки.
2.2.5. Техника ручной дуговой сварки покрытыми электродами.
2.2.6. Контроль качества сварки.
2.3. Графическая часть.
2.4. Требования охраны труда и организация рабочего места.
3. Заключение.
4. Список использованной литературы.
5. Приложения.
1. ВВЕДЕНИЕ.
Современный мир полностью держится на металле. Без него нельзя построить высокие здания, машины, корабли. Металл применяется повсеместно: в быту, в промышленности, в строительстве. Поэтому, специалист по металлу, соединяющий металлические детали в сложные конструкции при помощи электрической сварки, будет нужен всегда. Сварщик — профессия ответственная, почти виртуозная, от качества работы которого зависит многое — долговечность и устойчивость строительных конструкций, работа и срок службы различной техники.
ИСТОРИЯ ПРОФЕССИИ. (возникновение профессии, история развития профессии)
Временем возникновения профессии сварщик можно считать 1802 год, когда В. Петров открыл эффект электрической дуги, при возникновении которой между двумя угольными электродами, создаётся высокая температура. Эта температура настолько высока, что позволяет расплавлять металлы. С момента этого открытия и до его промышленного применения прошёл немалый период времени. Но спустя десятилетия, метод соединения металлов электродуговым способом произвёл революцию в различных отраслях промышленности, строительства и стал массовой технологией соединения материалов.…
СОЦИАЛЬНАЯ ЗНАЧИМОСТЬ ПРОФЕССИИ В ОБЩЕСТВЕ. (значение профессии, важность профессии, потребность в профессии, востребованность профессии)
Сварочные работы применяются во многих отраслях промышленности. Сварщики трудятся на стройплощадках, создавая конструкции и системы различных коммуникаций, в промышленности, где применяют свой опыт и навыки в машиностроении, кораблестроении и в других областях, таких как, энергетика, нефтеперерабатывающая промышленность, сельское хозяйство. Трудно назвать такой сегмент производства, где не применялся бы труд сварщика.
МАССОВОСТЬ И УНИКАЛЬНОСТЬ ПРОФЕССИИ. (требования к профессии, перспективы)
Сварщик, как профессия, подразделяется на несколько специализаций: сварщик ручной дуговой сварки, газосварщик, оператор автоматических сварочных аппаратов. Рабочие всех этих специальностей занимаются одним делом — соединением металлических конструкций, сложных аппаратов, деталей, узлов методом сплавления металлов. От мастерства сварщиков зависит качество сварочных швов. Любые ошибки, небрежность, допускаемые в работе, могут привести к катастрофическим последствиям. Сварщик — профессионал должен знать электротехнику, технологию плавления металлов, свойства газов, применяемых для антиокисления, методы и принципы действия используемых агрегатов и оборудования. Большое значение имеет соблюдение техники безопасности и производственной санитарии.
2. ОСНОВНАЯ ЧАСТЬ.
2.1. ТЕХНОЛОГИЧЕСКАЯ ЧАСТЬ.
2.1.1. ХАРАКТЕРИСТИКА МАТЕРИАЛА КОНСТРУКЦИИ.
Наиболее распространённым материалом для изготовления сварных конструкций является сталь.
Сталь — это сплав железа с углеродом и другими элементами. В зависимости от химического состава сталь бывает углеродистая и легированная. Углеродистая сталь делится на низкоуглеродистую (содержание углерода до 0,25%), среднеуглеродистую (от 0,25 до 0,6%С) и высокоуглеродистую (от 0,6 до 2,0%С). Сталь, в составе которой кроме углерода имеются легирующие компоненты (хром, никель, вольфрам, ванадий и т. д.), называется легированной. Различают легированные стали: низколегированные (суммарное содержание легирующих компонентов, кроме углерода, менее 2,5%), среднелегированные (от 2,5 до 10%), высоколегированные (более 10%). Легирующие компоненты, вводимые в состав сталей, улучшают их качество: повышаются механические свойства, снижается порог хладноломкости, в результате чего создается возможность снизить массу конструкций.
По микроструктуре различают стали перлитного, мартенситного, аустенитного, ферритного и карбидного классов.
По способу производства различают стали:
А) обыкновенного качества;
Б) качественная;
В) высококачественная.
По назначению стали бывают строительные, машиностроительные (конструкционные), инструментальные и стали с особыми физическими свойствами.
Рассмотренные выше стали имеют хорошую свариваемость. Технология ручной дуговой сварки таких сталей должна обеспечивать конкретный комплекс требований, к которым прежде всего относятся:
-обеспечение надежности и долговечности конструкций и особенно из термически упрочняемых сталей, как правило, используемых при изготовлении ответственных конструкций;
-обеспечение равнопрочное сварного соединения с основным металлом и отсутствие дефектов в сварном шве, поэтому механические свойства металла шва и околошовной зоны должны быть не ниже нижнего предела соответствующих свойств основного металла.
2.1.2. ПОДГОТОВКА МЕТАЛЛА К СВАРКЕ.
Подготовка металла под сварку заключается в правке, очистке, разметке, резке и сборке.
Правкой устраняют деформацию прокатной стали. Листовой и сортовой металл правят в холодном состоянии на листоправйльных и углоправйльных вальцах и прессах. Сильно деформированный металл правят в горячем состоянии.
Перенос размеров детали в натуральную величину с чертежа на металл называют разметкой. При этом пользуются инструментом: рулеткой, линейкой, угольником и чертилкой. Проще и быстрее разметка выполняется шаблоном, изготовляемым из тонкого металлического листа. При разметке заготовок учитывается укорачивание их в процессе сварки конструкции. Поэтому предусматривается припуск из расчета 1 мм на каждый поперечный стык и 0,1—0,2 мм на 1 м продольного шва.
При подготовке деталей к сварке применяют преимущественно термическую резку. Механическую резку целесообразно выполнять при заготовке однотипных деталей, главным образом с прямоугольным сечением. Часто кислородную резку, особенно машинную, сочетают со снятием угла скоса кромок. После термической резки иногда проводят механическую обработку по кромкам для удаления науглероженного металла.
Перед сборкой под сварку требуется в соответствии с ГОСТом подготовить кромки свариваемых деталей.
К элементам геометрической формы подготовки кромок под сварку (см.рис.) относятся угол разделки кромок a, притупление кромок S, длина скоса листа L при наличии разности толщин металла, смещение кромок относительно друг друга б, зазор между стыкуемыми кромками а; геометрические размеры шва: в-ширина шва,
h-высота шва, К-катет шва.
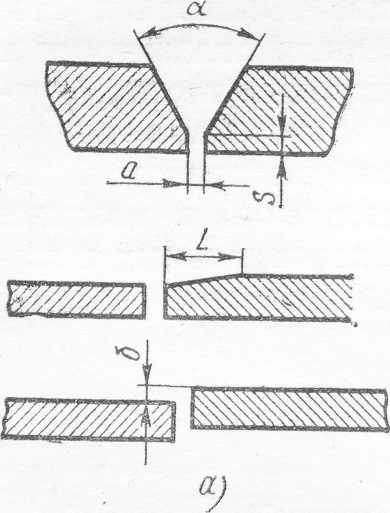
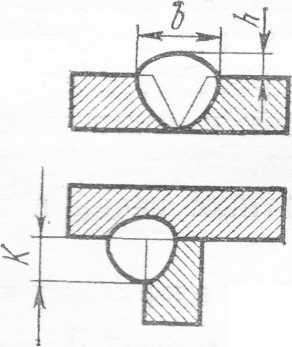
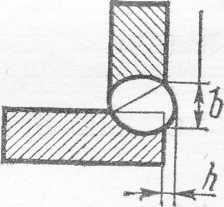
СБОРКА ИЗДЕЛИЙ ПОД СВАРКУ.
Трудоемкость сборки деталей под сварку составляет около 30% от общей трудоемкости изготовления изделия. Она зависит от ряда условий (серийности производства, типа изделий и др.). Для уменьшения времени сборки, а также для повышения ее точности применяют различные приспособления. Приспособления могут быть предназначены только для сборки деталей под сварку или только для сварки уже собранного изделия (например, для выполнения швов в изделии только в нижнем положении) или пользуются комбинированными сборочно-сварочными приспособлениями.
Основным назначением сборочного оборудования является фиксация и закрепление собираемого сварного узла в заданном положении. Для этой цели применяются специальные узлы и установки. Установочные и закрепляющие элементы сборочного оборудования. К первым относятся упоры, опоры, призмы, фиксаторы, шаблоны и домкраты. Закрепляющими элементами являются прижимы, которые могут быть ручными и механизированными. В качестве привода механизированных прижимов чаще всего применяются пневматические и гидравлические системы. В некоторых случаях прижим объединяют с упором или фиксатором и выполняют в виде комплексного узла. Установочные и зажимные элементы могут быть съемными и регулируемыми. Из отдельных элементов могут быть собраны приспособления и установки, в частности кондукторы и стенды. Указанные установки применяют для сборки плосколистовых и коробчатых конструкций, а также цилиндрических обечаек. При сборке осуществляют следующие операции: устанавливают все необходимые элементы конструкции на соответствующих местах с заданными зазорами и закрепляют их, совмещают кромки свариваемых элементов, при необходимости производят прихватки. В результате получают конструкцию, готовую для сварки. Для обеспечения необходимой точности сборки, сокращения времени на
разметку и проверку собранной конструкции, а также облегчения процесса сварки (возможность выполнения швов в нижнем положении) целесообразно использовать при изготовлении конструкций специальный кондуктор.
На рисунке показаны различные виды сборочно-сварочных приспособлений.
Р
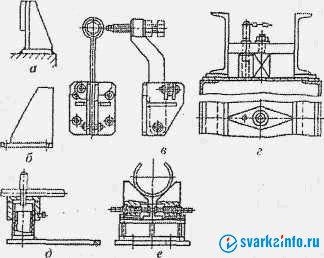
Изделия чаще всего собирают на сварочных прихватках. Сварочные прихватки представляют собой неполноценные короткие швы с поперечным сечением до 1/3 сечения полного шва. Длина прихватки от 20 до 100 мм в зависимости от толщины свариваемых листов и длины шва; расстояние между прихватками в зависимости от различных условий достигает 1м. Прихватки придают изделию жесткость и препятствуют перемещению деталей, что может привести к трещинам в прихватках при их охлаждении. Чем больше толщина свариваемых листов, тем больше растягивающая усадочная сила в прихватках и больше возможность образования трещин. Поэтому сборку на сварочных прихватках применяют для конструкций из листов небольшой толщины (до 6 — 8 мм). При значительной толщине листов необходимо обеспечить податливость деталей и сборку изделия выполняют на механических приспособлениях.
Точность сборки проверяют с помощью специального инструмента.
Р
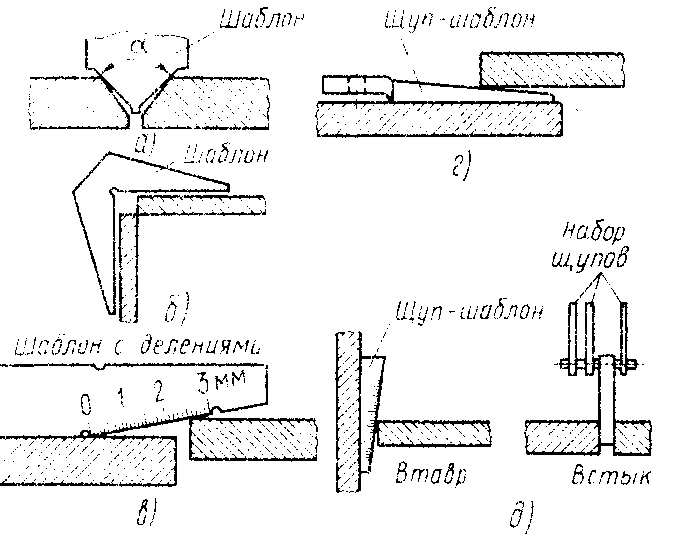
2.1.3.ТЕХНОЛОГИЯ РУЧНОЙ ДУГОВОЙ СВАРКИ ПОКРЫТЫМИ ЭЛЕКТРОДАМИ.
При ручной дуговой сварке покрытыми металлическими электродами, сварочная дуга горит с электрода на изделие, оплавляя кромки свариваемого изделия и расплавляя металл электродного стержня и покрытие электрода (рисунок). Кристаллизация основного металла и металла электродного стержня образует сварной шов.
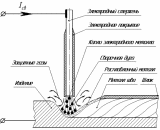
Достоинства способа:
простота оборудования;
возможность сварки во всех пространственных положениях;