Файл: Информация о предприятии 6 2 Правила эксплуатации линейной части магистрального газопровода 8.docx
Добавлен: 25.10.2023
Просмотров: 468
Скачиваний: 3
ВНИМАНИЕ! Если данный файл нарушает Ваши авторские права, то обязательно сообщите нам.
СОДЕРЖАНИЕ
2 Правила эксплуатации линейной части магистрального газопровода
3 Физическая сущность, классификация и характеристика способов и видов сварки
3.1 Физическая сущность и основные способы сварки
3.2. Виды сварных соединений и швов
4 Типы сварки, применяемых при строительстве газопроводов
4.2 Автоматическая дуговая сварка
5.4 Сооружение временных дорог
5.6 Подготовка труб к сборке и сварке
6 Организация подготовительных работпри ремонте магистрального газопровода
6.2 Технология и организация выполнения работ при ремонте
7.2 Контроль качества сварных соединений
8.1 Техника безопасности при сварочных работах
8.2 Охрана труда на предприятии и промышленная санитария
На основе результатов обследования участка ремонтируемого газопровода составляют акт, в котором приводят конкретные данные по протяженности участка, количеству плетей, метраж годных, отбракованных и подлежащих ремонту труб, о характере повреждений (глубина, протяженность и площадь коррозионного повреждения). К акту прилагают профиль трассы и журнал обследования.
Сварочно-восстановительные работы на газопроводе должны проводиться после производства работ по отбраковке уложенного на лежки газопровода. К сварочно-восстановительным работам при капремонте трубопровода относятся следующие: зашлифовка дефектов; заварка дефектов; вварка заплат; установка уплотнительных муфт; замена катушек, замена участков с временными муфтами из различных материалов (металлических, композиционных).
Заварка поврежденных участков должна выполняться ручной дуговой сваркой.
Участки газопровода с недопустимыми дефектами подлежат вырезке, а на их место врезают технологические катушки или трубы.
При производстве сварочно-восстановительных работ для сварки неповоротных стыков применяют самоходные сварочные установки типа АДД-4005 УРАЛ и АДД-2х2501ВУ1(Рисунок 14, 15), источник тока инверторный DC250.
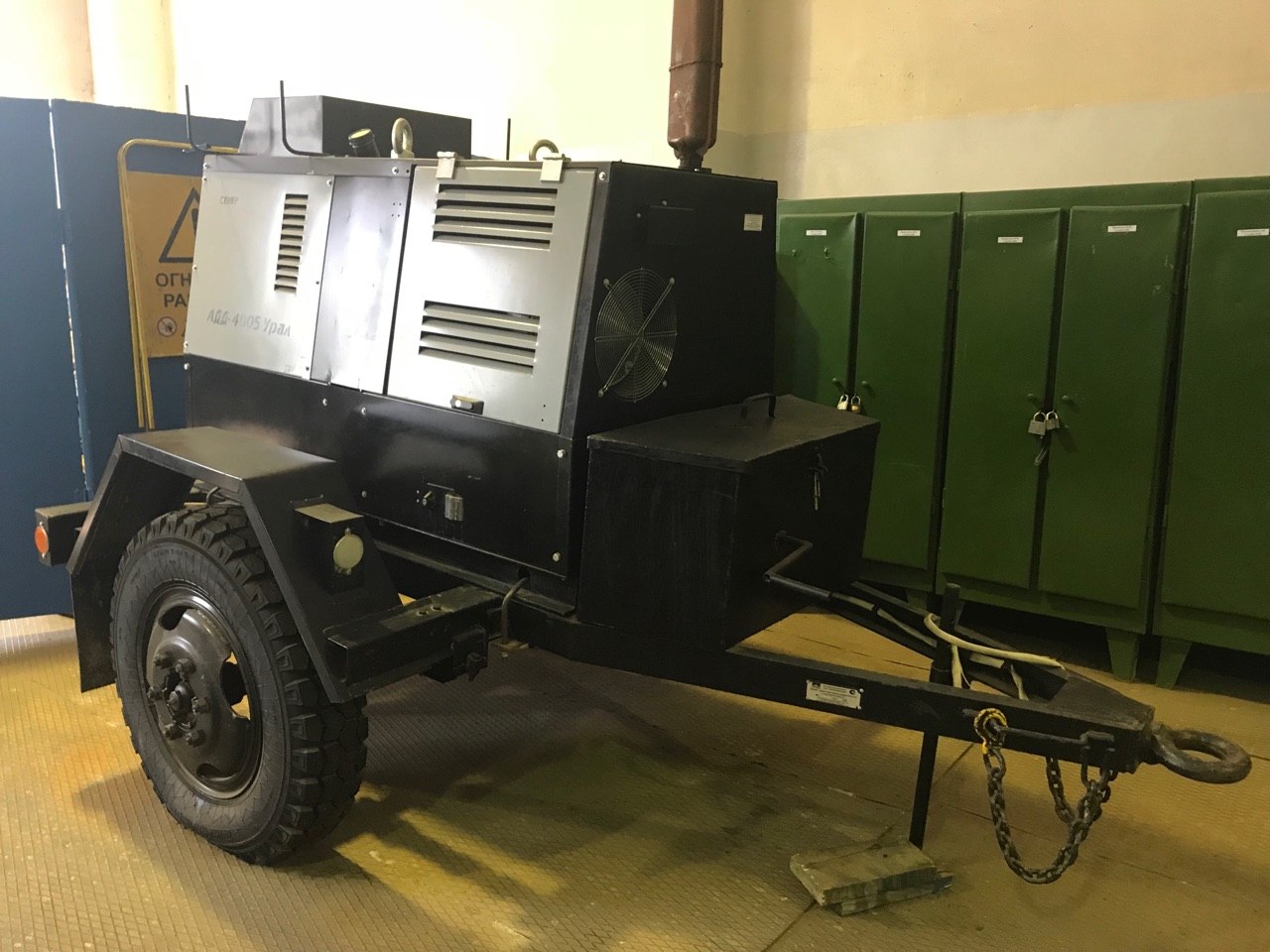
Рисунок 14 АДД-4005 УРАЛ
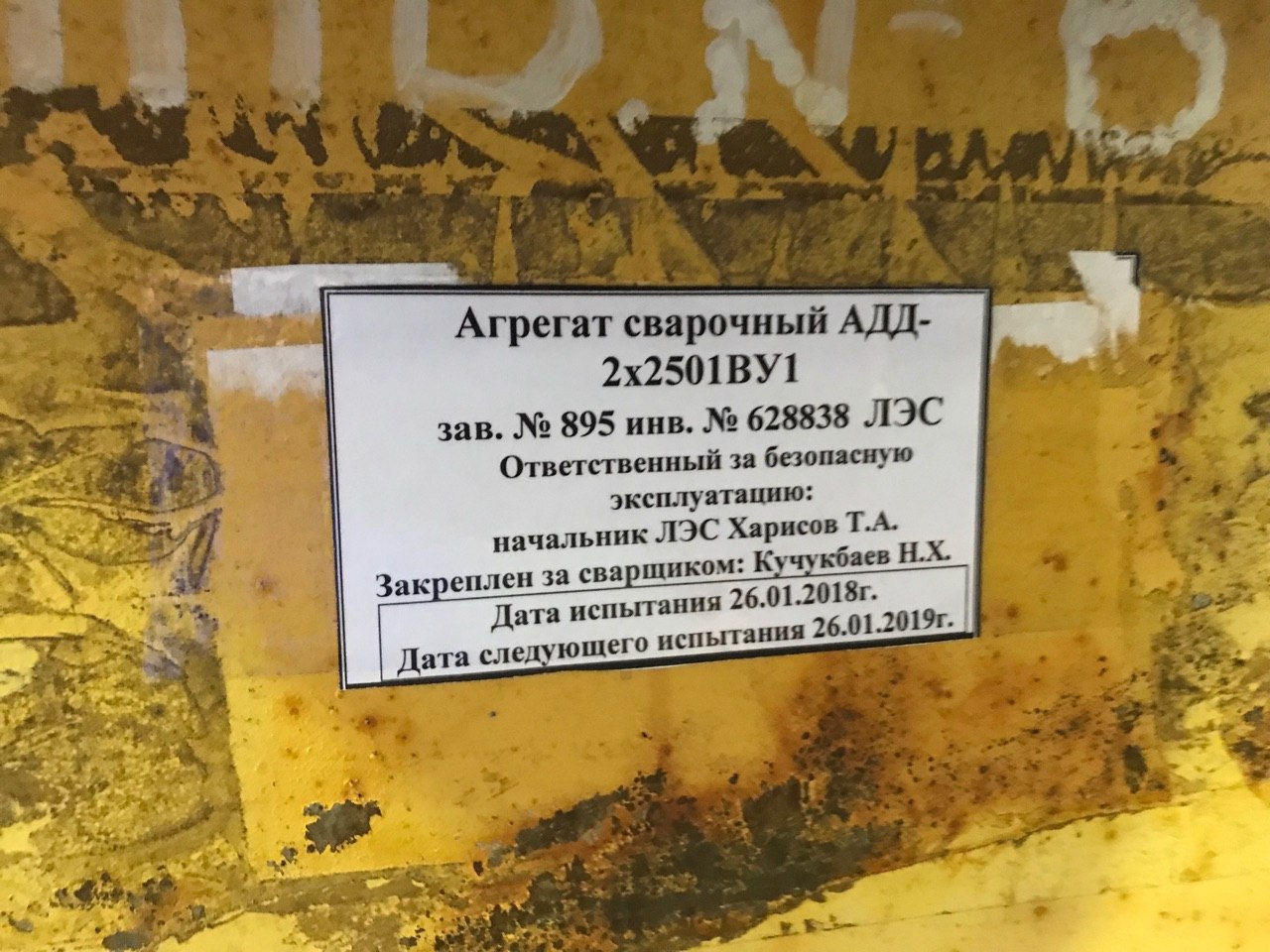
Рисунок 15 АДД-2х2501ВУ1
7 Контроль качества
7.1 Контроль качества работ
Контроль и оценку качества работ при сооружении магистрального трубопровода заваркой в соответствии с требованиями следующих нормативных документов:
-
СП 48.13330.2001. Организация строительства; -
СНиП 3.04.03-85. Защита строительных конструкций и сооружений от коррозии; -
СНиП 2.03.11-85. Защита строительных конструкций от коррозии; -
СНиП III-42-80*. Магистральные трубопроводы; -
ГОСТ Р 51164-98. Трубопроводы стальные магистральные. Общие требования к защите от коррозии.
Контроль качества строительно-монтажных работ осуществляется прорабом или мастером с привлечением аккредитованной Производственно-испытательной лаборатории оснащенной техническими средствами, обеспечивающими необходимую достоверность и полноту контроля.
Производственный контроль качества работ должен включать входной контроль рабочей документации и поступающих материалов, а также качество выполненных предшествующих работ, операционный контроль отдельных строительных процессов или технологических операций и приемочный контроль выполненных работ с оценкой соответствия.
7.2 Контроль качества сварных соединений
Контроль качества сварных соединений стальных трубопроводов включает:
-
пооперационный контроль; -
визуальный и измерительный контроль; -
контроль неразрушающими методами (ультразвуковой, радиографический); -
механические испытания; -
гидравлические или пневматические испытания.
Пооперационный контроль предусматривает: проверку качества и соответствия труб, деталей трубопроводов и сварочных материалов требованиям стандартов и технических условий на изготовление и поставку; проверку качества подготовки концов труб и деталей трубопроводов под сварку и качества сборки стыков (угол скоса кромок, совпадение кромок, зазор в стыке перед сваркой, правильность центровки труб, расположение и число прихваток, отсутствие трещин в прихватках); проверку температуры предварительного подогрева; проверку качества и технологии сварки (режима сварки, порядка наложения швов, качества послойной зачистки шлака);
Пооперационный контроль должен проводиться инженерно-техническим работником, ответственным за сварку, или под его наблюдением, а самоконтроль исполнителями работ.
Визуальному и измерительному контролю подлежат все (100%) сварных соединений после их очистки от шлака, окалины, брызг металла и загрязнений на ширине не менее 20 мм по обе стороны от шва.
В выполненном сварном соединении (наплавке) визуально следует контролировать: отсутствие (наличие) поверхностных трещин всех видов и направлений; отсутствие (наличие) на поверхности сварных соединений и наплавок дефектов (пор, включений, скоплений пор и включений, отслоений,прожогов, свищей, наплывов, усадочных раковин, подрезов, непроваров, брызг расплавленного металла, западаний между валиками, грубой чешуйчатости, прижогов металла, а также мест касания сварочной дугой поверхности основного материала); наличие зачистки металла в местах приварки временных технологических креплений, гребенок индуктора и бобышек крепления термоэлектрических преобразователей (термопар), а также отсутствие поверхностных дефектов в местах зачистки; наличие зачистки поверхности сварного соединения изделия (сварного шва и прилегающих участков основного металла) под последующий контроль неразрушающими методами; наличие маркировки (клеймения) шва (наплавки) и правильность ее выполнения.
В выполненном сварном соединении измерениями необходимо контролировать: размеры поверхностных дефектов (пор, включений),выявленных при визуальном контроле; высоту и ширину шва, а также вогнутость и выпуклость обратной стороны шва в случае доступности обратной стороны шва для контроля; высоту (глубину) углублений между валиками (западания межваликовые) и чешуйчатость поверхности шва; подрезы основного металла; несплавления (непровары) с наружной и внутренней стороны шва.
Визуальный и измерительный контроль качества сварных соединений должен выполняться в соответствии с требованиями РД 03-606-03. По результатам визуального осмотра и измерений сварные швы должны удовлетворять требованиям соответствующей «Технологической карты визуального и измерительного контроля».
Сварные соединения после визуального и измерительного контроля и устранения обнаруженных при этом недопустимых дефектов подвергают контролю физическими методами.
Контроль стыков радиографическим методом следует проводить по ГОСТ 7512-82, ультразвуковым по ГОСТ 14782-86, магнитографический по ГОСТ 25225-82.
Сварные соединения, в которых по результатам контроля обнаружены недопустимые дефекты (признанные «негодными), подлежат удалению или ремонту с последующим повторным контролем в соответствии с установленными требованиями.
Дополнительному (дублирующему) ультразвуковому контролю подвергают стыки через трое суток после окончания сварки (термообработки).
В случае, если по результатам неразрушающего контроля имеет место массовое появление недопустимых дефектов, по требованию Заказчика дальнейшее выполнение сварных кольцевых соединений данным сварщиком(сварщиками) запрещается. Разрешение на выполнение работ данным сварщиком (сварщиками) может быть выдано только после выявления и устранения причин неудовлетворительных результатов контроля и проведения повторных аттестационных испытаний сварщика(ов).
Испытания механических свойств сварных соединений выполняются при проведении аттестации технологических процессов сварки и аттестационных испытаниях сварщиков.
В процессе сооружения промысловых трубопроводов Заказчик имеет право подвергнуть дополнительном неразрушающему контролю или испытанию образцов для определения механических свойств любое кольцевое сварное соединение.
Все законченные строительством промысловые трубопроводы до ввода в эксплуатацию должны подвергаться очистке полости, испытанию на прочность и проверке на герметичность.
Испытание трубопроводов на прочность и проверка на герметичность производится после полной готовности участка или всего трубопровода.
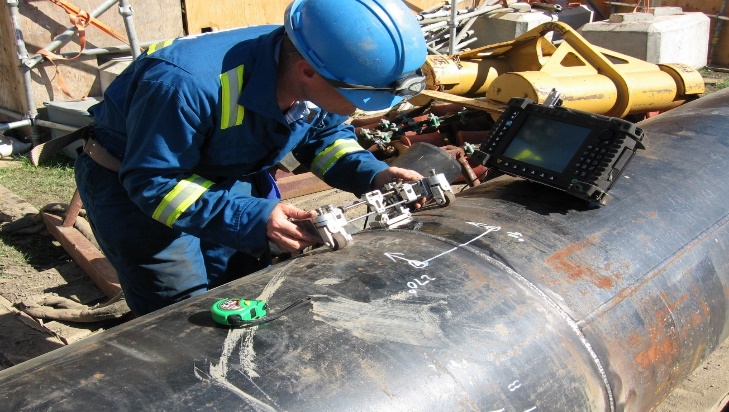
Рисунок 16 Контроль качества сварных соединений
8 Охрана труда
8.1 Техника безопасности при сварочных работах
Все сварочные работы должны выполняться в соответствии с требованиями «Правил безопасности при работе с инструментом и приспособлениями».
К электросварочным и газосварочным работам допускаются лица не моложе 18 лет, прошедшие специальную подготовку и проверку теоретических знаний, практических навыков, знаний по технике безопасности и имеющих удостоверение сварщиков. Все сварщики должны проходить проверку знаний инструкции по охране труда.
Проходы между источниками сварочного тока должны быть не менее 0,8 м. Проходы между группами сварочных трансформаторов должны иметь ширину не менее 1 м. Запрещается установка сварочного трансформатора над регулятором тока.
Запрещается производство электросварочных работ во время дождя и снегопада, при отсутствии навесов на электросварочным оборудованием и рабочим местом. При электросварочных работах в сырых местах сварщик должен находиться на настиле из сухих досок или на диэлектрическом ковре.
При любых отлучках с места работы сварщик обязан отключить сварочный аппарат. При электросварочных работах сварщик должен пользоваться индивидуальными средствами защиты: щиток, служащий для защиты лица и глаз, рукавицы для защиты рук. Одежда должна быть из несгораемого материала с низкой электропроводностью, кожаные ботинки.
При газосварочной работе запрещается хранить баллоны с кислородом в одном помещении с баллонами для горючих газов, а также с карбидом кальция, красками и маслами (жирами). Баллоны необходимо перемещать на специальных тележках, контейнерах и других устройствах, обеспечивающих устойчивое положение баллонов. Запрещается переноска баллонов на плечах и руках. Баллон с утечкой газа не должен применяться для работы или транспортирования.
Запрещается подогревать баллоны для увеличения давления. При проведении газосварочных работ запрещается курить и пользоваться открытым огнем на расстоянии менее 10 метров от баллонов с газом. Общая длинна шлангов должна быть не более 30 м. До присоединения шланга к горелке, его необходимо продуть рабочим газом. Каждые пять лет баллон для газа должен проходить освидетельствование. По окончанию работы вентили баллонов должны быть закрыты.