Файл: подготовка газа к транспорту. Выбор оборудования подготовки газа к транспорту.docx
ВУЗ: Не указан
Категория: Не указан
Дисциплина: Не указана
Добавлен: 25.10.2023
Просмотров: 170
Скачиваний: 7
ВНИМАНИЕ! Если данный файл нарушает Ваши авторские права, то обязательно сообщите нам.
СОДЕРЖАНИЕ
1.ПРИРОДНЫЙ ГАЗ. СОСТАВ И ФИЗИЧЕСКИЕ СВОЙСТВА ПРИРОДНОГО ГАЗА
2. ОБОРУДОВАНИЕ ДЛЯ ПОДГОТОВКИ ДОБЫВАЕМОГО ГАЗА.
2.1 Абсорбционная очистка газов
2.3 Расчет основных размеров абсорберов
2.4 Очистка газа от механических примесей
3. МОДЕРНИЗАЦИЯ СИСТЕМЫ СБОРА И ПОДГОТОВКИ ПОПУТНОГО НЕФТЯНОГО ГАЗА
3.1 Анализ эффективности осушки газа
3.2 Расчет абсорбера, оснащенного регулярной насадкой ДОАО ЦКБН
До обработки органическим абсорбентом из отбросных газов необходимо удалить дисперсные примеси. Иначе абсорбент быстро загрязняется и становится отходом, практически не поддающимся очистке.
Органические абсорбенты должны иметь низкое давление насыщенных паров при температуре процесса. Растворители с недостаточно низкой

На интенсивность перехода загрязнителя из газовой фазы в жидкую большое влияние оказывают температура и давление процесса, а также способ организации контакта фаз.
С ростом давления и снижением температуры скорость абсорбции увеличивается. Абсорбенты, работающие при отрицательных (по Цельсию) температурах, принято называть хладоносителями, а процесс абсорбции, протекающий в таких условиях - контактной конденсацией.
Абсорбционную очистку выбросов в атмосферу применяют как для извлечения ценного компонента из газа, так и для санитарной очистки газа. Считают, что целесообразно применять абсорбцию, если концентрация данного компонента в газовом потоке составляет свыше 1 %.
Сочетая абсорбцию с десорбцией, можно многократно использовать почти без потерь жидкий поглотитель (абсорбент) в замкнутом контуре аппаратов: абсорбер-десорбер-абсорбер (круговой процесс), выделяя поглощенный компонент в чистом виде.
Различают физическую абсорбцию и хемосорбцию. При физической абсорбции растворение газа в жидкости не сопровождается химической реакцией или, по крайней мере, влиянием этой реакции на скорость процесса можно пренебречь. Вследствие этого физическая абсорбция не сопровождается тепловым эффектом. Если в этом случае начальные потоки газа и жидкости незначительно различаются по температуре, то такую абсорбцию можно рассматривать как изотермическую.
На рисунке 2.1 представлена принципиальная схема установки для абсорбции определенного компонента из газовой среды и последующего его выделения из абсорбента (десорбции).
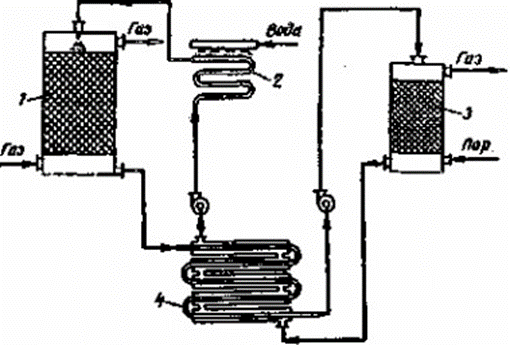

Рисунок 2.1 - Принципиальная схема установки для абсорбционно- десорбционного улавливания определенного компонента из газовой смеси:
1 - абсорбер; 2 - холодильник; 3 - десорбер; 4 – теплообменник
Газовая смесь, содержащая извлекаемый из нее компонент, поступает в абсорбер, где происходит контакт с абсорбентом, который поглощает данный компонент. Газ, очищенный от компонента, удаляется (очищенный воздух может быть выброшен в атмосферу), а раствор поглотителя, содержащий абсорбированный компонент, поступает в теплообменник, где нагревается. Нагретый раствор насосом подается в десорбер, где из него выделяется (десорбируется) поглощенный компонент путем испарения в результате нагревания поглотителя паром. Поглотитель, освобожденный от компонента, поступает в теплообменник, где отдает теплоту абсорбенту при его противоточном движении в десорбер, а затем направляется в холодильник, пройдя который, снова поступает в абсорбер. Круг замкнулся. По такому циклу работает установка для абсорбционно-десорбционного улавливания определенных паров и газов из газовой смеси (из воздуха).
2.2 Методы расчета абсорберов
Атмосферные загрязнители в отходящих газах обычно присутствуют в низких концентрациях. В связи с этим при проектировании абсорберов прежде всего учитывают необходимость обработки газовых потоков с

Поскольку конечная концентрация загрязнителя в газовой фазе всегда
выше равновесной с растворенным в жидкой фазе, абсорберы проектируют
для противоточной схемы движения поглотителя и обрабатываемых газов. При этом степень извлечения загрязнителя значительно зависит от факторов, влияющих на величину парциального давления загрязнителя над жидкостью: температуры поглотителя, начального содержания в нем загрязнителя и его растворимости.
Газовые и жидкие потоки в абсорберах слабоконцентрированы, что позволяет ввести ряд упрощений: оперируют моделью идеального раствора, подчиняющегося законам Генри и Рауля; пренебрегают неизотермичностью процесса, теплотами фазовых переходов растворения и химических реакций, рядом других факторов.
Большинство расчетных зависимостей относится к концентрационным диапазонам, характерным для химической технологии.
Они не распространяются на область значений концентраций, в которой работают системы защиты атмосферы, а лишь соприкасаются с ней: выходные (сбросные) концентрации технологических устройств, в том числе и абсорберов, являются начальными, т.е. входными для очистных аппаратов.

Расчеты абсорбционных аппаратов упрощают не только по причине низкой концентрации поглощаемых веществ. Множество упрощений вводится на том основании, что они уменьшают объем расчетов без заметного снижения точности результата. В соответствии с этим поглотитель обычно рассматривают как индивидуальное вещество, а многокомпонентные газовые смеси - как бинарные, состоящие из одного улавливаемого и одного инертного компонента.
Технологический расчет абсорбционной установки выполняют в несколько этапов.
На первом этапе производят материальные и энергетические расчеты и
устанавливают условия линию, находят число равновесия, строят линию равновесия и рабочую теоретических ступеней изменения концентрации, определяют необходимость циркуляции раствора, расход энергии на циркуляцию, устанавливают необходимую степень регенерации раствора, расход энергии на регенерацию и потери раствора при регенерации.
На втором этапе выбирают конструкции аппаратов, рассчитывают массо- и теплопередачу, гидродинамику и габариты аппаратов.
На третьем этапе уточняют технологические параметры и осуществляют оптимизацию процесса.
При проектировании абсорбера необходимо определить: диаметр аппарата и его высоту, размеры внутренних частей (размеры и тип насадки, конструкцию тарелок, число тарелок, устройства для ввода и распределения жидкости), оптимальную скорость жидкости в абсорбере.
2.3 Расчет основных размеров абсорберов
Все массообменные колонные аппараты можно условно разделить нa две группы: с непрерывно и со ступенчато изменяющейся концентрацией веществ, участвующих в процессе массообмена. Целью расчета таких колонн
является определение их диаметра и высоты. Диаметр колонны определяется объемным расходом и режимом движения сплошной фазы:
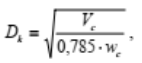
где V0 = Gc / ρ c — объемный расход сплошной фазы;
Gс, ρ с — соответственно массовый расход и плотность сплошной фазы;

Скорость движения сплошной фазы wс зависит от режима работы и конструктивных особенностей массообменного аппарата. Высоту массообменной части аппарата с непрерывно изменяющейся по его высоте концентрацией вещества можно рассчитать:
-
по основному уравнению массопередачи:

2) по числу единиц переноса (Nox или Noy) и высоте единицы переноса (hox или hoy):

3) по числу теоретических ступеней изменения концентраций (числу теоретических тарелок) Nт и высоте массообменной части аппарата, эквивалентной одной теоретической тарелке hэкв:
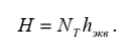
Теоретической тарелкой называют однократный контакт взаимодействующих потоков, завершающийся достижением фазового равновесия.
Высоту массообменной части аппарата со ступенчатым изменением концентрации веществ, участвующих в процессе массообмена, можно рассчитать по числу действительных ступеней изменения концентраций (числу действительных тарелок) Nд и расстоянию между тарелками h:


Общая высота колонного аппарата составляет:

где Hв - расстояние от верхнего ряда контактных элементов до крышки
колонны, м;
Нн - расстояние от нижнего ряда контактных элементов до днища колонны, м.
Расстояние Нн обычно определяется минимальным объемом жидкости, необходимым для обеспечения стабильности процесса парообразования и равномерного распределения газа (пара) по поперечному сечению колонны.
Это расстояние принимают равным (1,0... 1,5) Dк.
Расстояние Hв зависит от размеров распределительного устройства для орошения колонны жидкостью и от высоты сепарационного пространства, в котором устанавливают отбойные устройства для предотвращения брызгоуноса из колонны.
В зависимости от диаметра колонны Dк можно рекомендовать следующие высоты верхней Hв и нижней Нн частей колонны:
