Файл: 1 Технологическая часть 1 Описание конструкции и назначения детали 6.doc
Добавлен: 23.11.2023
Просмотров: 113
Скачиваний: 2
ВНИМАНИЕ! Если данный файл нарушает Ваши авторские права, то обязательно сообщите нам.
∑ ∙ Ky = 0,045 ∙ 0,03 ≈ 0
Данные заносим в графу 4.
Таблица 5 - межоперационный и общий припуски и диаметральный размер поверхности заготовки.
Погрешность установки заготовок (графа 5) в пневмотиски с призматическими губками при сверлении ε
у1=200мкм [5. табл. П 1.3.]; при растачивании без переустановки - εу2=0мкм; при шлифовании в пневмотисках с призматическими губками εу3=35мкм.
Расчет минимального припуска (графа 6) при обработке отверстия
производится по формуле:
для сверления:
2Zimin=2(200+300+√152+2002)=2(500+√225+40000)=2(500+200,56)=1401,12 мкм.
для чистового растачивания:
2Zi min=2(100+70+√0,92+02)=2(170+0,81)=341,8мкм.
для шлифования:
2Zi min=2(6,3+15+√0,0452+352)=2(21,3+35,00002)=112,6001мкм.
Расчет промежуточных минимальных диаметров по переходам проводится в порядке, обратном ходу технологического процесса обработки этой поверхности, т.е. от размера готовой детали к размеру заготовки, путем
последовательного вычитания к наименьшему предельному размеру готовой
поверхности детали минимального припуска 2Zi min. Результаты заносятся в
графу 7.
В графу 10 записываются размеры по всем технологическим переходам,
округляя их увеличением до того же знака десятичной дроби, с каким задан
допуск на размер для каждого перехода.
Наибольшие предельные размеры (графа 9) определяются путем
прибавления допуска к округленному минимальному предельному размеру.
Предельные размеры припусков Zi max (графа 11) определяются как
разность предельных максимальных размеров и Zi min (графа 12) – как
разность предельных минимальных размеров предшествующего и выполняемого переходов.
2.2 Расчет режимов резания
Расчет режимов резания на наружную цилиндрическую поверхность диаметром 80. Шероховатость Ra = 0,63 мкм.
Исходные данные: деталь «Втулка» из стали ХВГ. Заготовка- «прокат». Обработка производится на токарном станке. Режущий инструмент – резец с пластинами из твердого сплава Т15К6.
1. Глубина резания –t, мм
t = 1,39 мм (данные берутся из расчета припусков).
2. Подача-S мм/об
S = 0,6 мм/об [5. табл. П 2.7.].
3. Скорость резания – Vм/мин
. (5)
По [5. табл. П 2.11.] выписываем значения Сυ и показатели степеней хυ, уυ, m.
σв = 750 МПа
Сυ = 350
х = 0,15
у = 0,35
m = 0,20
Период стойкости инструмента – T = 120 мин
Находим поправочные коэффициенты
Кυ = Кмυ · Кпυ · Киυ , (6)
[5. табл. П.2.11.] (7)
где Кмυ - поправочный коэффициент на скорость резания, зависящий от материала заготовки,
Кпυ – поправочный коэффициент на скорость резания, зависящий от состояния обрабатываемой поверхности,
Кпυ = 1 [5. табл. П 2.5.],
Киυ - поправочный коэффициент на скорость резания, зависящий от режущего инструмента,
Киυ = 1 [5. табл. П 2.6],
пυ= 1 [5. табл. П 2.2.],
Кr = 1 [5. табл. П 2.2.].
4. Определяем частоту вращения шпинделя - n, об/мин
об/мин (8)
5. Уточняем частоту вращения шпинделя по паспорту и корректируем ее в ближайшую меньшую сторону.
Принимаем n = 500 об/мин.
6. Пересчитываем скорость резания,VФ.
Vф – фактическая скорость резания, м/мин:
(9)
1.Глубина резания –t, мм
t = 0,44 мм (данные берутся из расчета припусков).
2. Подача - S мм/об
S =0,144 мм/об. [5. табл. П 2.10.].
3.Рассчитываем скорость резания – Vм/мин
По [5. табл. П 2.11] выписываем значения Сυ и показатели степеней хυ, уυ, m.
Сυ =420,
х =0,15,
у = 0,20,
m = 0,20.
Период стойкости инструмента - Т = 120 мин
Находим поправочные коэффициенты
Кпυ = 1[5. табл. П 2.5.].
Киυ = 1 [5. табл. П 2.6.].
пυ = 1; Кr = 1 [5. табл. П 2.2.].
Кυ = 1
4. Определяем частоту вращения шпинделя - n, об/мин
об/мин.
5.Уточняем частоту вращения шпинделя по паспорту и корректируем ее в ближайшую меньшую сторону.
Принимаем n = 1000 об/мин.
6.Пересчитываем скорость резания,Vф.
Vф – фактическая скорость резания:
.
Расчет режимов резания на наружную цилиндрическую поверхность диаметром 50. Шероховатость Ra = 0,63 мкм.
Исходные данные: деталь «Втулка» из стали ХВГ. Заготовка- «прокат». Обработка производится на токарном станке. Режущий инструмент – резец с пластинами из твердого сплава Т15К6.
1. Глубина резания –t, мм
t = 1,39 мм (данные берутся из расчета припусков).
2. Подача-S мм/об
S = 0,6 мм/об [5. табл. П 2.7.].
3. Скорость резания – Vм/мин
По [5. табл. П 2.11.]. выписываем значения Сυ и показатели степеней хυ, уυ, m.
σв = 750 МПа
Сυ = 350
х = 0,15
у = 0,35
m = 0,20
Период стойкости инструмента – T = 120 мин
Находим поправочные коэффициенты
Кпυ = 1 [5. табл. П 2.5.],
Киυ - поправочный коэффициент на скорость резания, зависящий от режущего инструмента,
Киυ = 1 [5. табл. П 2.6.],
пυ= 1 [5. табл. П 2.2.],
Кr = 1 [5. табл. П 2.2.].
4. Определяем частоту вращения шпинделя - n, об/мин
об/мин
5. Уточняем частоту вращения шпинделя по паспорту и корректируем ее в ближайшую меньшую сторону.
Принимаем n = 800 об/мин.
6. Пересчитываем скорость резания,VФ.
Vф – фактическая скорость резания, м/мин:
1.Глубина резания –t, мм
t = 0,44 мм (данные берутся из расчета припусков).
2. Подача - S мм/об
S =0,144 мм/об. [5. табл. П 2.10.].
3.Рассчитываем скорость резания – Vм/мин
По [5. табл. П 2.11.]. выписываем значения Сυ и показатели степеней хυ, уυ, m.
Сυ =420,
х =0,15,
у = 0,20,
m = 0,20.
Период стойкости инструмента - Т = 120 мин
Находим поправочные коэффициенты
Кпυ = 1 [5. табл. П 2.5)
Киυ = 1 [5. табл. П 2.6.].
пυ = 1; Кr = 1 [5. табл. П 2.2.].
Кυ = 1
4. Определяем частоту вращения шпинделя - n, об/мин
об/мин.
5.Уточняем частоту вращения шпинделя по паспорту и корректируем ее в ближайшую меньшую сторону.
Принимаем n = 1600 об/мин.
6.Пересчитываем скорость резания,Vф.
Vф – фактическая скорость резания:
Расчет режимов резания на отверстие диаметром 40+0,025. Шероховатость Ra = 6,3 мкм. Исходные данные: деталь «втулка» из стали ХВГ. Заготовка – «прокат». Обработка производится на вертикально-сверлильном станке. Режущий инструмент – сверло спиральное, зенкер, развертка. Инструментальный материал – быстрорежущая сталь Р6М5
Операция «Сверлильная».
Переход 1. Сверлить отверстие 1.
1.Глубина резания
, мм
, мм (данные берутся из расчета припусков).
2. Находим подачу S, мм/об [5. табл. П 2.16.].
S=0,28 – 0,33мм/об принимаем S = 0,29 мм/об.
Т – период стойкости, мин [5. табл. П 2.21]
Т = 45 мин.
Находим неизвестные [5. табл. П 2.19.].
Сv = 9,8,
q = 0,40,
y = 0,5,
m = 0,2.
Находим поправочные коэффициенты:
,
КMV-коэффициент на обрабатываемый материал [5. табл. П 2.1-П 2.4.].
Данные заносим в графу 4.
Таблица 5 - межоперационный и общий припуски и диаметральный размер поверхности заготовки.
Маршрут обработки поверхности | Элементы припуска, мкм | Расчетный припуск, мкм | Расчетный размер, мкм | Допуск по переходам, в мм | Предельный размер, мм | Предельные припуски, мм | |||||
Rzi-1 | Ti-1 | ρi-1 | εi | max мм | min мм | max мм | min мм | ||||
1 | 2 | 3 | 4 | 5 | 6 | 7 | 8 | 9 | 10 | 11 | 12 |
Внутренняя поверхность 40Н7 | | | | | | | | | | | |
Прокат | 200 | 300 | 15 | - | - | 38,1695 | 620 | 38,17 | 37,55 | - | - |
Сверление | 100 | 70 | 0,9 | 200 | 1401,12 | 39,5706 | 250 | 39,57 | 39,32 | 1,77 | 1,4 |
растачивание чистовое | 6,3 | 15 | 0,045 | 0 | 341,8 | 39,9124 | 100 | 39,9 | 39,8 | 0,48 | 0,33 |
шлифование | 3,2 | 15 | 0 | 35 | 112,6001 | 40,025 | 25 | 40,025 | 40 | 0,2 | 0,125 |
Погрешность установки заготовок (графа 5) в пневмотиски с призматическими губками при сверлении ε
у1=200мкм [5. табл. П 1.3.]; при растачивании без переустановки - εу2=0мкм; при шлифовании в пневмотисках с призматическими губками εу3=35мкм.
Расчет минимального припуска (графа 6) при обработке отверстия
производится по формуле:
для сверления:
2Zimin=2(200+300+√152+2002)=2(500+√225+40000)=2(500+200,56)=1401,12 мкм.
для чистового растачивания:
2Zi min=2(100+70+√0,92+02)=2(170+0,81)=341,8мкм.
для шлифования:
2Zi min=2(6,3+15+√0,0452+352)=2(21,3+35,00002)=112,6001мкм.
Расчет промежуточных минимальных диаметров по переходам проводится в порядке, обратном ходу технологического процесса обработки этой поверхности, т.е. от размера готовой детали к размеру заготовки, путем
последовательного вычитания к наименьшему предельному размеру готовой
поверхности детали минимального припуска 2Zi min. Результаты заносятся в
графу 7.
В графу 10 записываются размеры по всем технологическим переходам,
округляя их увеличением до того же знака десятичной дроби, с каким задан
допуск на размер для каждого перехода.
Наибольшие предельные размеры (графа 9) определяются путем
прибавления допуска к округленному минимальному предельному размеру.
Предельные размеры припусков Zi max (графа 11) определяются как
разность предельных максимальных размеров и Zi min (графа 12) – как
разность предельных минимальных размеров предшествующего и выполняемого переходов.
2.2 Расчет режимов резания
Расчет режимов резания на наружную цилиндрическую поверхность диаметром 80. Шероховатость Ra = 0,63 мкм.
Исходные данные: деталь «Втулка» из стали ХВГ. Заготовка- «прокат». Обработка производится на токарном станке. Режущий инструмент – резец с пластинами из твердого сплава Т15К6.
Операция «Токарная».
Переход 1. Точить поверхность 1 предварительно.
1. Глубина резания –t, мм
t = 1,39 мм (данные берутся из расчета припусков).
2. Подача-S мм/об
S = 0,6 мм/об [5. табл. П 2.7.].
3. Скорость резания – Vм/мин
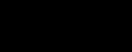
По [5. табл. П 2.11.] выписываем значения Сυ и показатели степеней хυ, уυ, m.
σв = 750 МПа
Сυ = 350
х = 0,15
у = 0,35
m = 0,20
Период стойкости инструмента – T = 120 мин
Находим поправочные коэффициенты
Кυ = Кмυ · Кпυ · Киυ , (6)
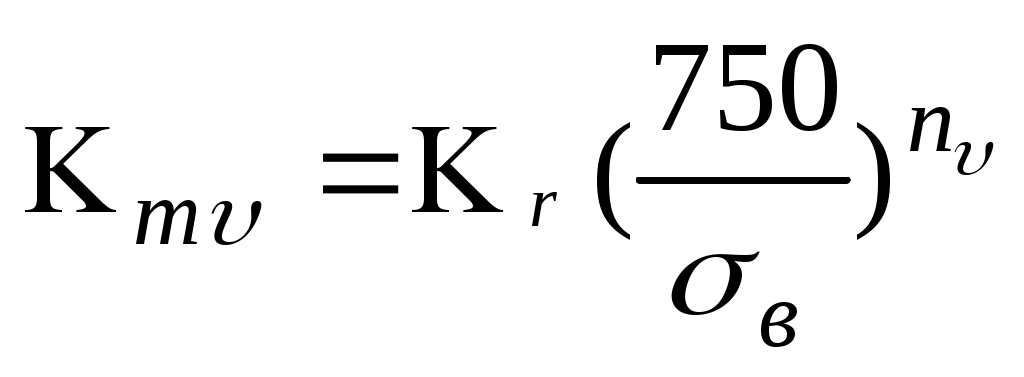
где Кмυ - поправочный коэффициент на скорость резания, зависящий от материала заготовки,
Кпυ – поправочный коэффициент на скорость резания, зависящий от состояния обрабатываемой поверхности,
Кпυ = 1 [5. табл. П 2.5.],
Киυ - поправочный коэффициент на скорость резания, зависящий от режущего инструмента,
Киυ = 1 [5. табл. П 2.6],
пυ= 1 [5. табл. П 2.2.],
Кr = 1 [5. табл. П 2.2.].
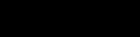

4. Определяем частоту вращения шпинделя - n, об/мин
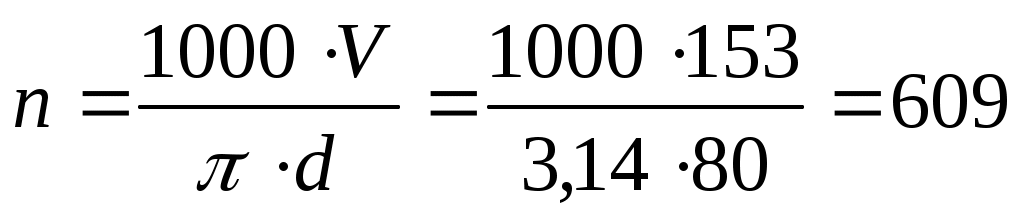
5. Уточняем частоту вращения шпинделя по паспорту и корректируем ее в ближайшую меньшую сторону.
Принимаем n = 500 об/мин.
6. Пересчитываем скорость резания,VФ.
Vф – фактическая скорость резания, м/мин:

Переход 2. Точить поверхность 1 окончательно
1.Глубина резания –t, мм
t = 0,44 мм (данные берутся из расчета припусков).
2. Подача - S мм/об
S =0,144 мм/об. [5. табл. П 2.10.].
3.Рассчитываем скорость резания – Vм/мин
По [5. табл. П 2.11] выписываем значения Сυ и показатели степеней хυ, уυ, m.
Сυ =420,
х =0,15,
у = 0,20,
m = 0,20.
Период стойкости инструмента - Т = 120 мин
Находим поправочные коэффициенты
Кпυ = 1[5. табл. П 2.5.].
Киυ = 1 [5. табл. П 2.6.].
пυ = 1; Кr = 1 [5. табл. П 2.2.].
Кυ = 1

4. Определяем частоту вращения шпинделя - n, об/мин
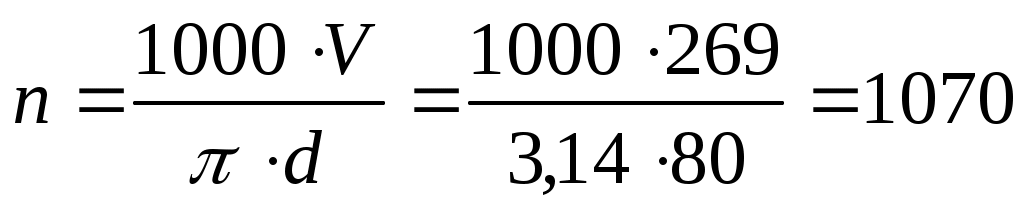
5.Уточняем частоту вращения шпинделя по паспорту и корректируем ее в ближайшую меньшую сторону.
Принимаем n = 1000 об/мин.
6.Пересчитываем скорость резания,Vф.
Vф – фактическая скорость резания:

Расчет режимов резания на наружную цилиндрическую поверхность диаметром 50. Шероховатость Ra = 0,63 мкм.
Исходные данные: деталь «Втулка» из стали ХВГ. Заготовка- «прокат». Обработка производится на токарном станке. Режущий инструмент – резец с пластинами из твердого сплава Т15К6.
Операция «Токарная».
Переход 1. Точить поверхность 1 предварительно.
1. Глубина резания –t, мм
t = 1,39 мм (данные берутся из расчета припусков).
2. Подача-S мм/об
S = 0,6 мм/об [5. табл. П 2.7.].
3. Скорость резания – Vм/мин
По [5. табл. П 2.11.]. выписываем значения Сυ и показатели степеней хυ, уυ, m.
σв = 750 МПа
Сυ = 350
х = 0,15
у = 0,35
m = 0,20
Период стойкости инструмента – T = 120 мин
Находим поправочные коэффициенты
Кпυ = 1 [5. табл. П 2.5.],
Киυ - поправочный коэффициент на скорость резания, зависящий от режущего инструмента,
Киυ = 1 [5. табл. П 2.6.],
пυ= 1 [5. табл. П 2.2.],
Кr = 1 [5. табл. П 2.2.].


4. Определяем частоту вращения шпинделя - n, об/мин
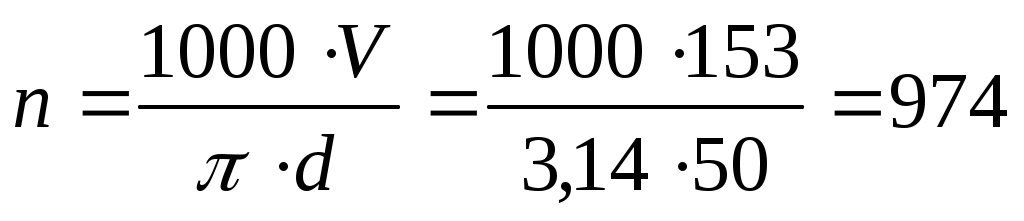
5. Уточняем частоту вращения шпинделя по паспорту и корректируем ее в ближайшую меньшую сторону.
Принимаем n = 800 об/мин.
6. Пересчитываем скорость резания,VФ.
Vф – фактическая скорость резания, м/мин:

Переход 2. Точить поверхность 1 окончательно
1.Глубина резания –t, мм
t = 0,44 мм (данные берутся из расчета припусков).
2. Подача - S мм/об
S =0,144 мм/об. [5. табл. П 2.10.].
3.Рассчитываем скорость резания – Vм/мин
По [5. табл. П 2.11.]. выписываем значения Сυ и показатели степеней хυ, уυ, m.
Сυ =420,
х =0,15,
у = 0,20,
m = 0,20.
Период стойкости инструмента - Т = 120 мин
Находим поправочные коэффициенты
Кпυ = 1 [5. табл. П 2.5)
Киυ = 1 [5. табл. П 2.6.].
пυ = 1; Кr = 1 [5. табл. П 2.2.].
Кυ = 1

4. Определяем частоту вращения шпинделя - n, об/мин
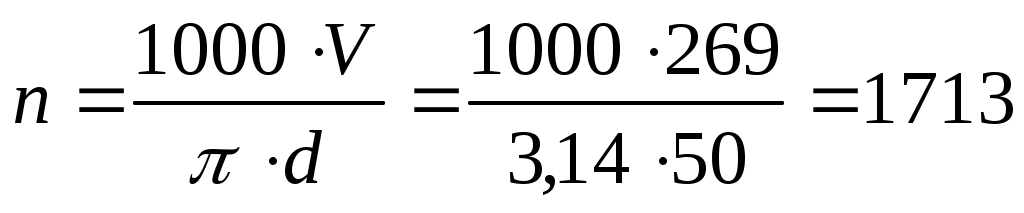
5.Уточняем частоту вращения шпинделя по паспорту и корректируем ее в ближайшую меньшую сторону.
Принимаем n = 1600 об/мин.
6.Пересчитываем скорость резания,Vф.
Vф – фактическая скорость резания:

Расчет режимов резания на отверстие диаметром 40+0,025. Шероховатость Ra = 6,3 мкм. Исходные данные: деталь «втулка» из стали ХВГ. Заготовка – «прокат». Обработка производится на вертикально-сверлильном станке. Режущий инструмент – сверло спиральное, зенкер, развертка. Инструментальный материал – быстрорежущая сталь Р6М5
Операция «Сверлильная».
Переход 1. Сверлить отверстие 1.
1.Глубина резания
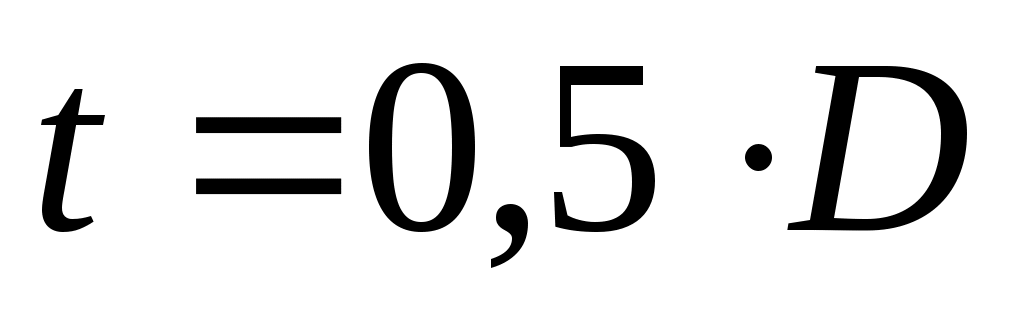

2. Находим подачу S, мм/об [5. табл. П 2.16.].
S=0,28 – 0,33мм/об принимаем S = 0,29 мм/об.
-
Рассчитываем скорость резания Vм/мин -
. (10)
Т – период стойкости, мин [5. табл. П 2.21]
Т = 45 мин.
Находим неизвестные [5. табл. П 2.19.].
Сv = 9,8,
q = 0,40,
y = 0,5,
m = 0,2.
Находим поправочные коэффициенты:

КMV-коэффициент на обрабатываемый материал [5. табл. П 2.1-П 2.4.].
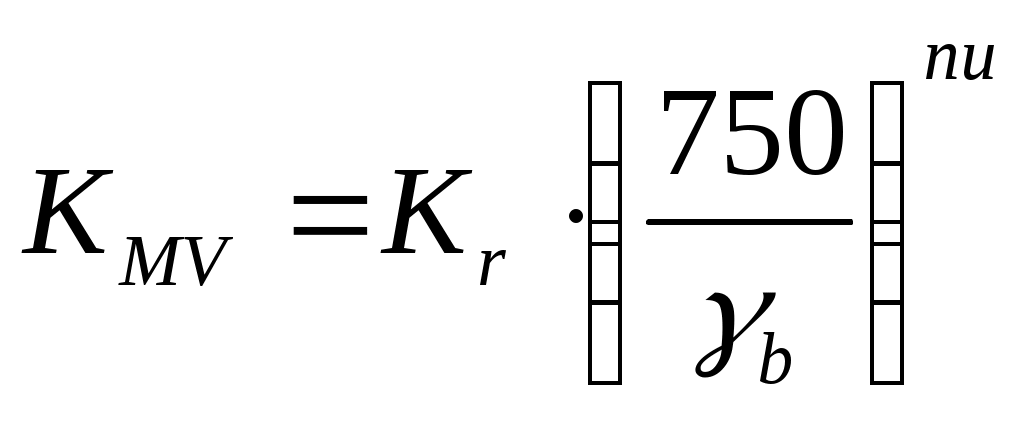