Файл: Практическое задание 2 Расчет цилиндрической передачи.docx
ВУЗ: Не указан
Категория: Не указан
Дисциплина: Не указана
Добавлен: 24.10.2023
Просмотров: 121
Скачиваний: 3
ВНИМАНИЕ! Если данный файл нарушает Ваши авторские права, то обязательно сообщите нам.
М
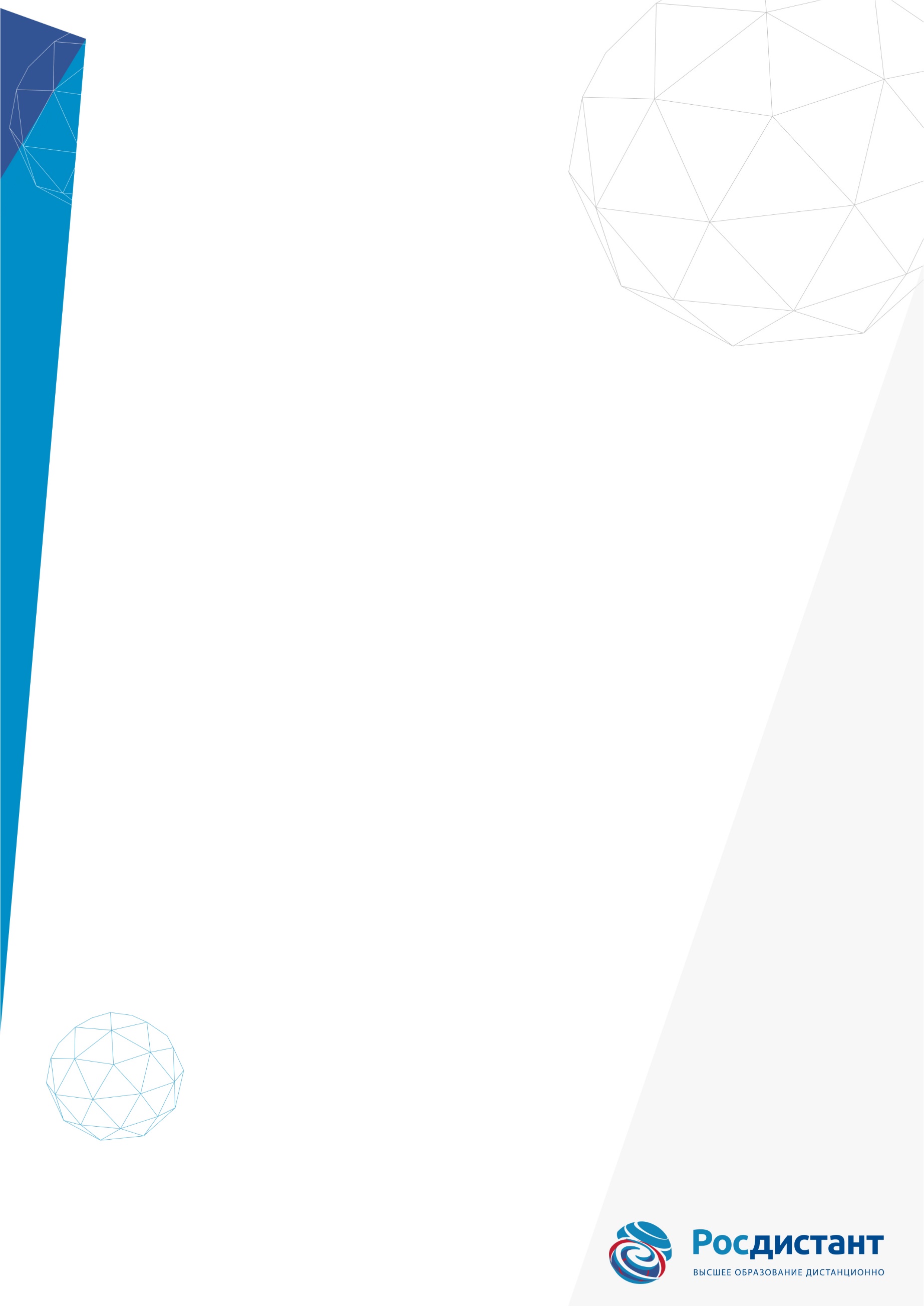
федеральное государственное бюджетное образовательное учреждение
высшего образования
«Тольяттинский государственный университет»
Институт машиностроения
(наименование института полностью)
Сварка, обработка материалов давлением и родственные процессы
(наименование кафедры/департамента/центра полностью)
15.03.01 Машиностроение
(код и наименование направления подготовки, специальности)
Технологии сварочного производства и инженерия поверхностей
(направленность (профиль) / специализация)
Практическое задание № 2
по учебному курсу « Механика 4 »
(наименование учебного курса)
Вариант 2
Студент | | |
| (И.О. Фамилия) | |
Группа | | |
| | |
Преподаватель | | |
| (И.О. Фамилия) | |
Тольятти 2023
Практическое задание 2
«Расчет цилиндрической передачи»
Задание
Рассчитать косозубую цилиндрическую зубчатую передачу с симметричным расположением колес, представленную на схеме (рис. 2.1).
Исходные данные:
![]() | ![]() |
Рис. 2.1. Схема редуктора | Рис. 2.2. Циклограмма нагружения |
Зубчатые колеса выполнены без смещения. Коэффициенты смещения шестерни и колеса
x1,2 = 0.
Нагрузка постоянная, передача нереверсивная.
u= 4 - передаточное число.
Срок службы 5 лет.
Коэффициент перегрузки определяется по циклограмме нагружения – рис. 2.2.
Первая буква фамилии | Вари-ант | Мощность на выходном валу Nвых, кВт | Частота вращения шестерни n1, об/мин | Коэффициент суточного использования Ксут | Коэффициент годового использования Кгод | Коэффициент перегрузки Кпер = Тmax/Тном |
Б | 2 | 3,8 | 1500 | 0,6 | 1 | 1,75 |
2.1. Проектировочный расчет
По заданию, исходя из указанных выше факторов, выбираем материалы и термообработку зубчатых колес.
Выбор материалов и способов термообработки зубчатых колес рекомендуется производить в зависимости от заданной мощности на выходе (NВЫХ).
1. Так как NВЫХ = 4…8 кВт, то:
Материал зубчатых колес – сталь 40Х, 40ХН.
Термообработка:
– шестерни – закалка, твердость Н1 = (40…60) HRC;
– колеса – улучшение, твердость Н2 = (269…302) НВ.
Минимальное число зубьев зубчатых колес, выполненных без смещения, для предотвращения подрезания принимается равным zmin = 17. Выбираем коэффициент ширины зуба:


Коэффициент ширины зуба по диаметру определяем по формуле




Расчет на контактную выносливость зубьев служит для предотвращения усталостного выкрашивания активных поверхностей зубьев. Но следует отметить, что после проектировочного расчета необходимо выполнить уточненные проверочные расчеты.
Определяем межосевое расстояние из условия контактной выносливости активных поверхностей зубьев по формуле, мм:
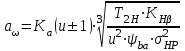
где «+» – для внешнего зацепления, «–» – для внутреннего зацепления;
Ka – вспомогательный коэффициент. Вспомогательный коэффициент Ka принимают по табл. 2.4.
Ka

T2H – вращающий момент на валу колеса, Н· м;

u – передаточное число;







Вспомогательный коэффициент Ka принимают по табл. 2.4.
Ka

Допускаемые контактные напряжения


где

SH – коэффициент запаса прочности;
ZN – коэффициент долговечности;
ZR – коэффициент, учитывающий шероховатость сопряженных поверхностей зубьев;

ZL – коэффициент, учитывающий влияние вязкости масла;
ZX – коэффициент, учитывающий размер зубчатого колеса.
В проектировочном расчете
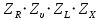


В качестве допускаемого контактного напряжения




При этом должно выполняться условие





Условие


Предел контактной выносливости





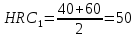
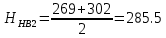




При отсутствии необходимых фактических данных можно применить следующие минимальные коэффициенты запаса прочности SH:
– для зубчатых колес, выполненных из материала однородной структуры, принимаем SHmin = 1,1,
– для колес с поверхностным упрочнением зубьев SHmin = 1,2;
Коэффициент долговечности ZN принимают в зависимости от отношения суммарного и базового чисел циклов перемены напряжений в зубьях NK и NHlim по следующим формулам:
ZN =


но не более 2,6 для однородной структуры материала и 1,8 для поверхностного упрочнения;
ZN =


но не менее 0,75,
где NHlim – базовое число циклов перемены напряжений;
NК – суммарное число циклов перемены напряжений.
Суммарное число циклов перемены напряжений NК при постоянной нагрузке определяется следующим образом (определяется и для шестерни, и для колеса):

где с – число зубчатых колес, сцепляющихся с рассчитываемым зубчатым колесом (в данном задании с = 1);
n – частота вращения рассчитываемого зубчатого колеса, об/мин;
t – срок службы передачи, в часах.


Если не задано конкретное число часов работы передачи, а задан срок работы передачи в годах, то t определятся по формуле

где L – срок службы в годах;
КГОД, КСУТ– коэффициенты использования передачи в течение года и суток соответственно.

Базовое число циклов перемены напряжений

