Файл: Информация о предприятии 6 2 Правила эксплуатации линейной части магистрального газопровода 8.docx
Добавлен: 25.10.2023
Просмотров: 466
Скачиваний: 3
ВНИМАНИЕ! Если данный файл нарушает Ваши авторские права, то обязательно сообщите нам.
СОДЕРЖАНИЕ
2 Правила эксплуатации линейной части магистрального газопровода
3 Физическая сущность, классификация и характеристика способов и видов сварки
3.1 Физическая сущность и основные способы сварки
3.2. Виды сварных соединений и швов
4 Типы сварки, применяемых при строительстве газопроводов
4.2 Автоматическая дуговая сварка
5.4 Сооружение временных дорог
5.6 Подготовка труб к сборке и сварке
6 Организация подготовительных работпри ремонте магистрального газопровода
6.2 Технология и организация выполнения работ при ремонте
7.2 Контроль качества сварных соединений
8.1 Техника безопасности при сварочных работах
8.2 Охрана труда на предприятии и промышленная санитария
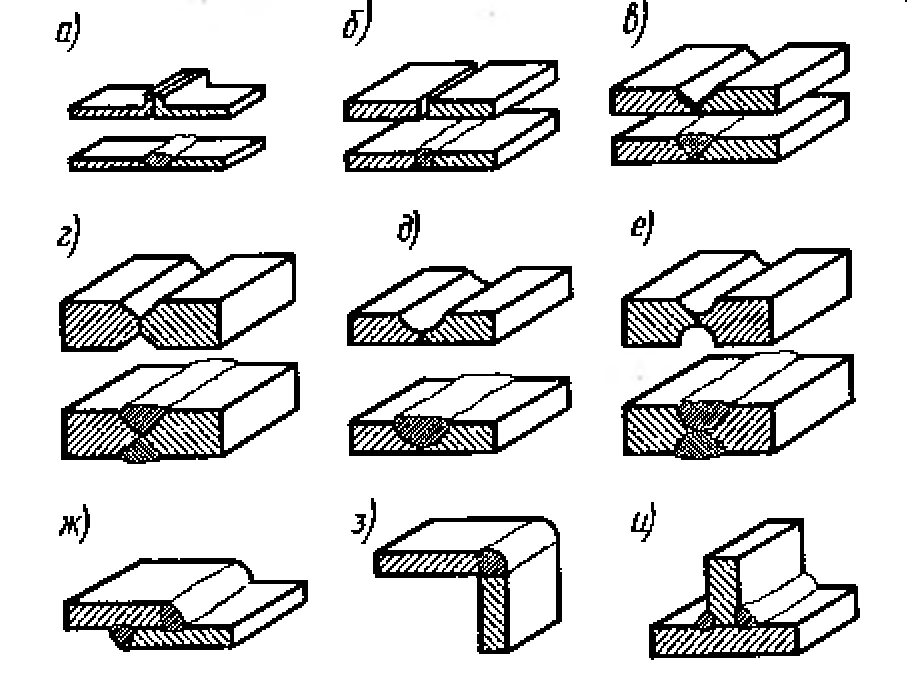
Рисунок 5 Виды сварных соединений
Соединения внахлестку (рисунок 5 - ж) выполняют угловыми швами, величина нахлестки равна трех-пятикратной толщине свариваемых элементов.
Угловые соединения (рисунок 5 - з) производят без скоса и со скосом кромок.
Тавровые соединения выполняют приваркой одного элемента изделия к другому (рисунок 5 - и). Без скоса кромок сваривают конструкции с малой нагрузкой. При изготовлении ответственных конструкций с элементами толщиной 10 - 20 мм применяют односторонний скос, а при толщине более 20 мм - двусторонний. Подготовка кромок для ручной сварки регламентируется ГОСТ 5264 - 69; для автоматической - ГОСТ 8713 - 70.
По положению в пространстве швы могут быть нижние и горизонтальные (рисунок 6 - а, б), вертикальные (рисунок 6 - в) и потолочные (рисунок 6 - г).
Наиболее легко выполнять нижние швы; их можно располагать на нижней горизонтальной плоскости в любом направлении. Вертикальные швы располагают на вертикальной плоскости в любом направлении. Наиболее трудны для выполнения потолочные швы; они располагаются в любом направлении на верхней горизонтальной плоскости.
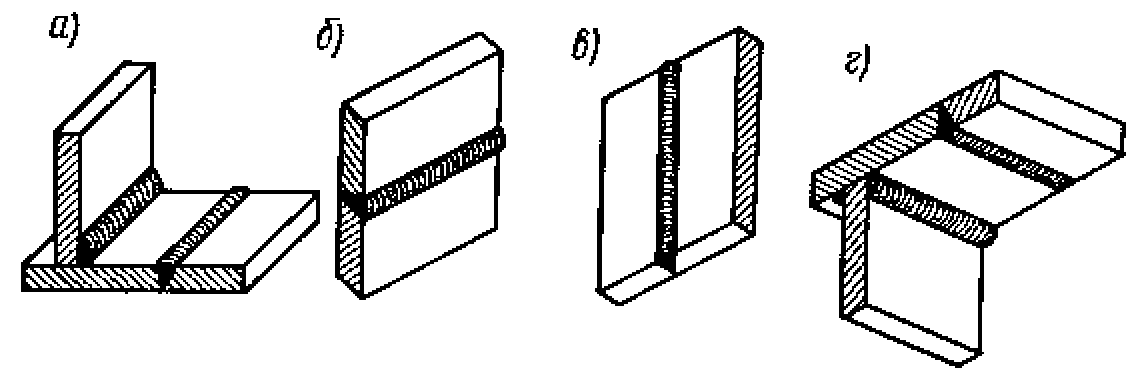
Рисунок 6 Типы швов при различном положении в пространстве:
а – нижние; б – горизонтальные; в – вертикальные; г – потолочные
Строение сварного шва после затвердевания и распределения температуры малоуглеродистой стали показаны на рисунке 7. Наплавленный металл 2 получается в результате перевода присадочного и частично основного металлов в жидкое состояние, образования жидкой ванночки и последующего затвердевания, в процессе которого расплавленный металл соединяется с основным 1. В узкой зоне сплавления 3 кристаллизуются зерна, принадлежащие основному и наплавленному металлу. Во всяком сварном шве образуется зона термического влияния 4, которая располагается в толще основного металла. В этой зоне под влиянием быстрого нагрева и охлаждения в процессе сварки изменяется лишь структура металла, а его химический состав остается неизменным.
Свойства металла в зоне шва определяются условиями плавления, металлургической обработки основного и присадочного металлов и кристаллизации металла шва при охлаждении. Свойства сварного соединения в целом определяются характером теплового воздействия на металл в околошовных зонах.
Во время плавления основной и присадочный металлы сильно перегреваются иногда до температур, близких к температуре кипения. Это приводит к испарению металла и изменению химического состава сплава. Наличие газовой атмосферы вокруг плавящегося металла приводит в ряде случаев к окислению, взаимодействию металла с азотом и растворению в металле газов. Все это изменяет химический состав наплавленного металла, создает в нем окислы и другие неметаллические включения, поры и трещины. Чем чище наплавленный металл, тем выше механические свойства сварного шва.
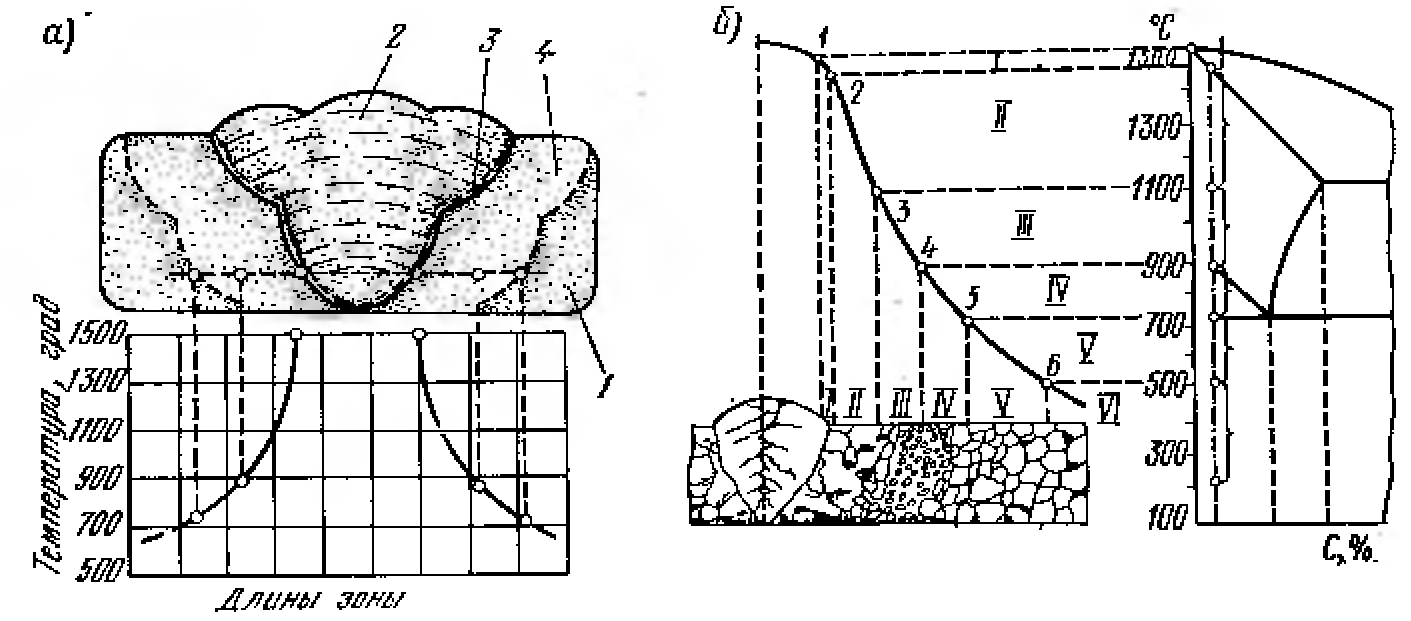
Рисунок 7 Строение сварочного шва (а) и структурные превращения малоуглеродистой стали в зоне термического влияния (б)
С целью повышения качества наплавленного металла вокруг жидкого металла создают специальную газовую атмосферу, защищающую его от воздействия воздуха, раскисляют и прикрывают жидкую ванночку специальными шлаками.
Строение сварного шва после затвердевания и распределения температуры в малоуглеродистой стали показаны на рисунке 7 - б. Зона I примыкает непосредственно к металлу шва. Основной металл на этом участке в процессе сварки частично расплавляется и представляет собой смесь твердой и жидкой фаз.
Наплавленный металл имеет столбчатое (дендритное) крупнозернистое строение, характерное для литой стали. Если наплавленный металл или соседний с ним участок был сильно перегрет, то при охлаждении на этом участке (зона II) зерна основного металла (малоуглеродистой стали) образуют грубоигольчатую так называемую видманштеттовую структуру.
Металл этой зоны обладает наибольшей хрупкостью и является самым слабым местом сварного соединения. В зоне III температура металла не превышает 1100 °С. Здесь наблюдается структура нормализованной стали с характерным и мелкозернистым строением. Металл в этой зоне имеет более высокие механические свойства (в сравнении с металлом первых двух зон).
В зоне IV происходит неполная перекристаллизация стали, нагретой до температуры, лежащей между критическими точками Ас1и Ac3. На этом участке после охлаждения наряду с крупными зернами феррита образуются мелкие зерна феррита и перлита.
В зоне V структурных изменений в стали не происходит, если сталь перед сваркой не подвергалась пластической деформации. В противном случае на этом участке наблюдается рекристаллизация.
В зоне VI сталь не претерпевает видимых структурных изменений. Однако на этом участке наблюдается резкое падение ударной вязкости (синеломкость).
Структурные изменения основного металла в зоне термического влияния незначительно отражаются на механических свойствах малоуглеродистой стали при сварке ее любыми способами. Однако при сварке некоторых конструкционных сталей в зоне термического влияния возможно образование закалочных структур, которые резко снижают пластические свойства сварных соединений и часто являются причиной образования трещин.
Размеры зоны термического влияния зависят от способа и технологии сварки и рода свариваемого металла. Так, при ручной дуговой сварке стали тонкообмазанными электродами (обмазку применяют в виде покрытия для защиты сварного шва от воздействия внешней среды) и при автоматической сварке стали под слоем флюса размеры зоны термического влияния минимальны (2 — 2,5 мм); при сварке электродами с толстой обмазкой протяженность этой зоны равна 4 — 10 мм, а при газовой сварке — 20 — 25 мм.
4 Типы сварки, применяемых при строительстве газопроводов
4.1 Дуговая сварка
Дуговая сварка (Рисунок 8) – это наиболее часто используемый метод для соединения труб магистральных газопроводов. Она основана на принципе возникновении электрической дуги между свариваемой деталью и электродом. При их соприкосновении происходит замыкание. В следствии этого, возникающая большая плотность тока, которая проходит через точку контакта, обеспечивает высокую температуру (более 5000 градусов по Цельсию). На поверхности электрода образуется расплавленный металл, который переходит на свариваемую деталь и смешивается с ее расплавленным материалом.
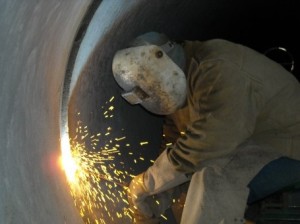
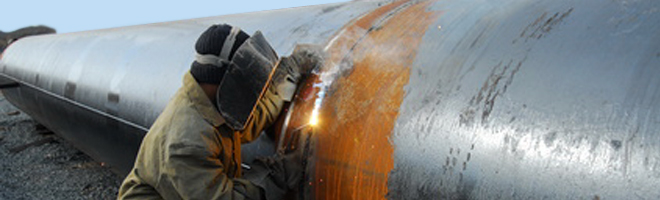
Рисунок 8 Дуговая сварка, труба 1420 мм
Толщину слоя металла свариваемого изделия, который перешел в расплавленное состояние, специалисты называют глубиной провара. Она достигает одного-двух миллиметров при ручной сварке. Но автоматическая сварка может обеспечить глубину проварки гораздо больше.
Стоит контролировать температуру плавления. Ведь, если разогрев металла будет недостаточным, то соединения не произойдет. Это приведет к неприятным последствиям – непровару, а, следовательно, снижению качества всего соединения. В случае чрезмерного нагрева возможно проникновение воздуха внутрь шва и его выгорание, что также сильно повлияет на прочность стали. Исправить эти огрехи можно только проведя весь процесс подготовки трубы и ее сварки с самого начала и в соответствии с требованиями, которые выдвигаются эксплуатационной и технической документацией.
Достаточное напряжение при зажигании сварочной дуги составляет пятьдесят Вольт. В дальнейшем оно снижается до шестнадцати-двадцати пяти Вольт. Сила тока выбирается в зависимости от толщины свариваемых элементов и может равняться от ста пятидесяти до пятисот ампер. При использовании тока из электрической сети используют агрегаты (генераторы и прочее), которые обеспечивают его преобразование до нужной силы и напряжения. Если придерживаться всех требований к проведению дуговой сварки, то можно получить качественный и надежный сварной шов.
4.2 Автоматическая дуговая сварка
Дуговая сварка бывает также автоматической и полуавтоматической (Рисунок 9).
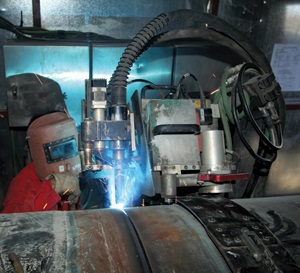
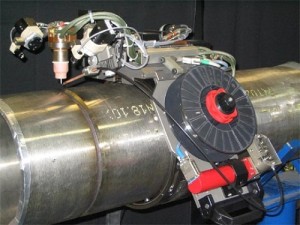
Рисунок 9 Автоматическая и полуавтоматическая сварка трубы
Для автоматической сварки нужен комплекс машин и механизмов, составляющих единую установку. При этом методе используются не электроды, а проволока из специального материала, которая автоматически подается в зону плавления по мере необходимости.
Автоматическая сварка имеет несколько основных преимуществ. Например, длина дуги остается постоянной. Также, возможно применение высокой плотности тока без перегрева проволоки. Все это значительно влияет на итоговое качество сварного шва.
Самый распространенный метод автоматического процесса – это сварка под флюсом. Сущность процесса заключается в применении сварочной проволоки и гранулированного флюса. Он насыпается слоем толщиной тридцать -пятьдесят миллиметров перед дугой. Сварка под флюсом получила широкое применение. Для многих отраслей промышленности она является одним из ведущих технологических процессов при производстве сложных конструкций из стали. Столь широкое распространение она получила благодаря обеспечению достаточно крепких сварных соединений без особых временных и финансовых затрат. Но стоит заметить, что требования к ее применению достаточно серьезные.
Целесообразно применять автоматическую сварку под флюсом в массовом и серийном производствах, а также для проварки швов протяженностью более восьмидесяти сантиметров. Для этого необходимо использовать агрегаты со свободным входом и выходом сварочной головки для начала и конца шва. Толщина свариваемого металла может быть в диапазоне от трех до ста миллиметров.
Основными преимуществами автоматической сварки под флюсом являются:
-
высокая производительность; -
высокое качество и хороший внешний вид сварочных соединений; -
снижение расхода электроэнергии и электродного металла.
Но, как любой процесс, автоматическая сварка под флюсом обладает некоторыми недостатками:
-
необходимость более тщательной подготовки кромок; -
возможность сварки только в горизонтальном положении на полу; -
невозможность сварки стыковых швов для вертикально расположенных деталей.