Файл: Технологическая оснастка является переменной частью технологического оснащения.docx
ВУЗ: Не указан
Категория: Не указан
Дисциплина: Не указана
Добавлен: 26.10.2023
Просмотров: 64
Скачиваний: 2
ВНИМАНИЕ! Если данный файл нарушает Ваши авторские права, то обязательно сообщите нам.
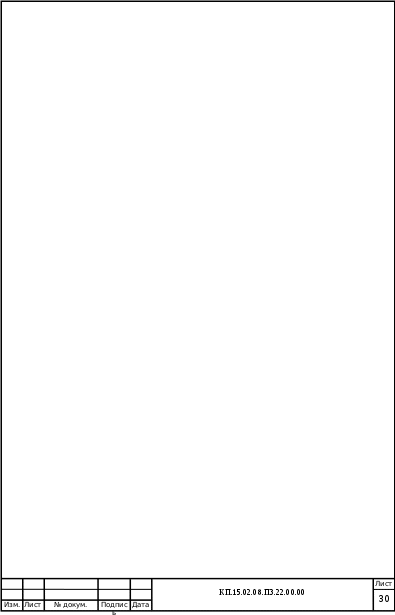
ВВЕДЕНИЕ
Технологическая оснастка предусматривает собой совокупность рабочего, измерительного инструмента и приспособлений, используемых для базирования, закрепления и контроля обрабатываемых деталей на различном технологическом оборудовании: метало, деревообрабатывающих станках, прессах, измерительных машинах и др.
Технологическая оснастка является переменной частью технологического оснащения. Назначение технологической оснастки – обеспечивать, менять и расширять технологические возможности оборудования, поэтому срок её службы на один порядок и более ниже срока службы оборудования.
В массовом производстве приоритетным является применение специальной неразборной и безналадочной технологической оснастки; в серийном производстве - специализированной и унифицированной технологической оснастки, обладающей свойством обратимости; в единичном производстве – специальной неразборной и универсально-наладочной технологической оснастки.
Приспособление должно обеспечивать заданной точности инструмента или заготовки. Основные требования к инструментам – точность режущих кромок и прилегающая поверхность резания.
Заготовка – предмет производства, из которого изменяются формы, размеры, шероховатость поверхности и свойства изготовления деталей. Она характеризуется заданной точностью и стабильностью материала.
Станочные приспособления должны быть удобными в эксплуатации и экономичными в изготовлении, безопасными в работе, быстродействующими, точными, жесткими, виброустойчивыми, износостойкими. Приспособления, используемые для оснащения станков определенной группы (токарных, фрезерных и т.д.) называются целевыми. Для оснащения станков нескольких групп применяются многоцелевые приспособления: столы, стойки, тиски, центры, некоторые планшайбы, оправки, патроны.
Станочные приспособления позволяют: существенно уменьшить время работы заготовки; повысить точность резания; обеспечить условия для обслуживания нескольких станков одним рабочим; облегчить труд рабочего; снизить себестоимость.
Благодаря применению станочных приспособлений выполняется условие, при котором ожидаемая погрешность обработки не превышает допуска на получаемый размер. На машиностроительных предприятиях используются десятки миллионов приспособлений, причем ежегодно на их изготовление расходуется до 1 млн. тонн металла.
В данном курсовом проекте рассматривается приспособление «Патрон поводковый», которая предназначена для чистовой и получистовой скоростной обточки деталей класса валов. На рисунке 1.1.1 представлен общий вид приспособления «Патрон поводковый».
1.1 Эскиз общего вида приспособления
Рисунок 1.1.1 Патрон Поводковый
1.2 Служебное назначение приспособления
Основными деталями оправки являются: корпус 1, втулка 2, центр 3, цанга 4, поводок 6, пружина 10.
Обрабатываемая деталь устанавливается на центр 3 оправки и вращающийся центр задней бабки. При нажатии центром задней бабки плавающий центр 3 вдвигается внутрь корпуса 1 и торец вала, упираясь в зубцы поводка 6, перемещает втулку 2 и цангу 4, закрепляя плавающий центр. После этого поворотом маховика задней бабки достигается врезание зубцов поводка 6 в торец вала. При этом поводок самоустанавливается относительно торца вала благодаря наличию опорной сферической поверхности. Врезание зубцов в торец вала обеспечивает передачу вращения и предотвращает поворачивание вала в процессе обработки.
Поводковая оправка позволяет обтачивать вал на проход, обеспечивая достаточную жесткость крепления, правильное центрирование, а также установку и снятие детали небольшого веса при вращении шпинделя станка.
Для деталей, имеющих внутреннюю цилиндрическую поверхность, в качестве установочных элементов применяют оправки. Конструктивно оправки делят на жесткие и разжимные.
Жесткие оправки могут быть: конические, цилиндрические для посадки заготовок с гарантированным зазором или натягом.
На станке оправки устанавливают в центрах, с помощью конусного хвостовика или фланца. Центровые оправки имеют центровые отверстия. Для того чтобы сообщить оправке вращательное движение, на ее левом конце делают квадрат, лыски или устанавливают поводок.
Конусные оправки обеспечивают высокую точность центрирования. Конусность рабочей части оправки принимается равной 1/1500 …1/2000. В таблице 1.2.1 указывается характеристика всех деталей приспособления.
Таблица 1.2.1 - Характеристика деталей приспособления
№ детали | Наименование | Кол-во | Материал | Обозначение | Термообработка |
1 | Корпус | 1 | Сталь 45 | | Закалка ![]() |
2 | Гайка M14X1,5 | 2 | Ст. 3 | | |
3 | Шарикоподшипник | 1 | - | № 203 | |
4 | Гайка М64Х2 | 1 | Сталь 45 | ГОСТ 3105-46 | |
| Шарикоподшипник | 1 | - | № 8205 | |
6 | Кольцо | 1 | Сталь 45 | | |
7 | Шарикоподшипник | 1 | - | | |
8 | Фланец | 3 | Сталь 45 | | Закалка ![]() |
9 | Пробка 1М16Х1,5 | 6 | Ст. 3 | | |
10 | Палец | 3 | Сталь 45 | | Закалка ![]() |
11 | Ось | 3 | Сталь 45 | | Закалка ![]() |
12 | Пружина 10Х2Х15 | 3 | 65Г | | Закалка ![]() |
13 | Кулачок сменный | 3 | 65Г | | |
14 | Пружина 10Х2Х15 | 3 | 65Г | | |
15 | Шарик Ø12,7 | 3 | | ГОСТ 3725-47 | |
16 | Винт М4Х10 | 3 | Ст. 3 | ГОСТ 1473-42 | |
17 | Крышка | 1 | Ст. 3 | | |
18 | Винт М5 Спец. | 3 | Сталь 45 | | Закалка ![]() |
19 | Штырь | 3 | Ст. 3 | | |
20 | Кольцо | 1 | Сталь 45 | | |
21 | Винт М8Х25 | 3 | Ст.3 | | |
22 | Кольцо плавающее | 1 | Сталь 45 | | |
23 | Центр | 1 | У8А | | Закалка ![]() |
| | | | | |
1.3 Характеристика и описание станка, на котором применяется данное приспособление
Назначение и область применения токарного патронно-центрового станка с ЧПУ 16К20Ф3.
Назначение: Токарная обработка деталей типа тел вращения в замкнутом полуавтоматическом цикле.
Токарно-винторезный станок 16А20Ф3 предназначен для обработки внутренних и наружных поверхностей деталей, имеющих криволинейный либо ступенчатый профиль в сечении оси.
Область применения: Мелкосерийное серийное производство.
Класс точности П по ГОСТ 8—82.
Вид климатического исполнения по ГОСТ 15150—69: УХЛ4.
Станки могут выпускаться с различными устройствами ЧПУ (УЧПУ), в исполнении для встраивания в гибкие производственные модули (ГПМ), а также в специальном и специализированном исполнении при оснащении наладками по согласованию с заказчиком.
Токарно-винторезный станок 16А20Ф3 с устройством ЧПУ 2Р22 оснащен главным приводом «КЕМРОН» и приводом подач «КЕМТОК» по оси Z и X. Он предназначен для токарной обработки в автоматическом режиме наружных и внутренних поверхностей деталей типа тел вращения со ступенчатым и криволинейным профилем различной сложности по заранее составленной управляющей программе. Отклонение от цилиндричности 7мкм, конусности 20мкм на длине 300мм, отклонение от прямолинейности торцевой поверхности на диаметре 300мм - 16мкм. Область применения станка: мелкосерийное и серийное производство. Станки 16А20Ф3 с системой ЧПУ 2Р22 имеют правильное название 16А20Ф3С32, согласно системе обозначений завода производителя.
Особенности конструкции:
1. Высокопрочная станина, выполненная литьем из чугуна марки СЧ20 с термообработанными, шлифованными направляющими обеспечивают длительный срок службы и повышенную точность обработки;
2. Привод главного движения, включающий главный двигатель 11кВт и шпиндельную бабку обеспечивает наибольший крутящий момент до 800Нм;
3. Высокоточный шпиндель с отверстием 55мм (по заказу 64мм), позволяющий обрабатывать детали из пруткового материала зона обработки может быть оснащена как линейной наладкой, так и револьверной головкой, в зависимости от требований покупателя;
4. Надежная защита шарико-винтовых пар обеспечивает долговечность работы механизмов, перемещения по координатам X и Z. Станок оснащается системами ЧПУ и электроприводами, как отечественного производства, так и производства зарубежных фирм. На рисунках 1.3.1 и 1.3.2 показано: общий вид токарного станка и его устройство.
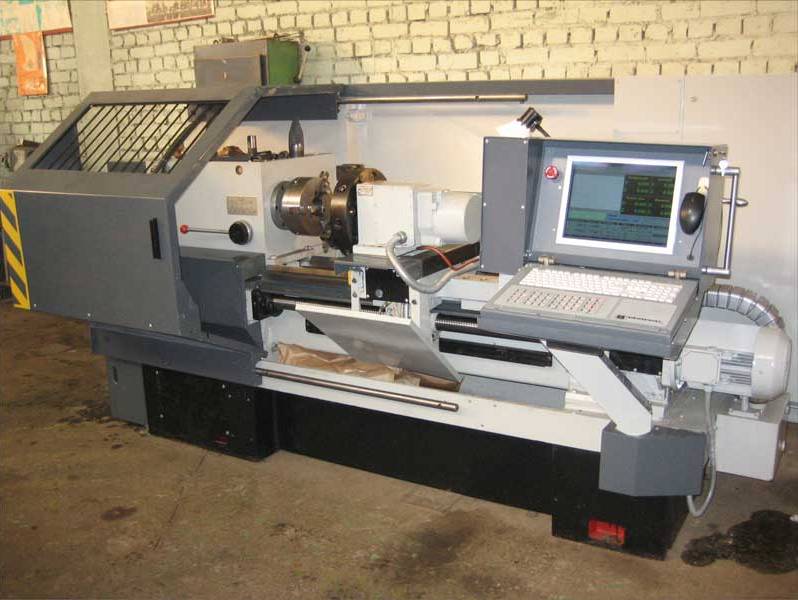
Рисунок 1.3.1 Общий вид токарного станка 16А20Ф3
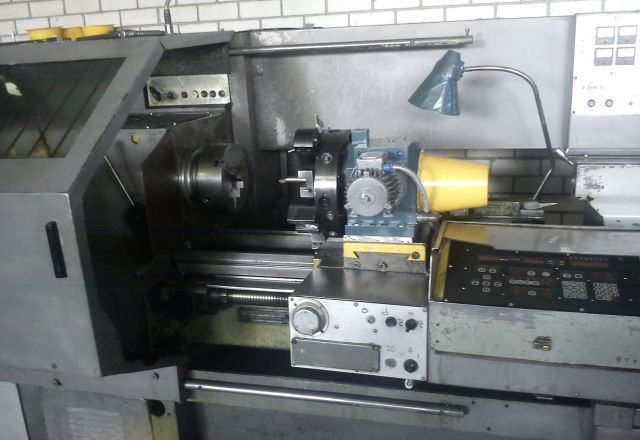
Рисунок 1.3.2 Устройство токарного станка 16А20Ф3
Особенности кинематики устройства главного движения станка:
Шпиндельная бабка, монтируемая на агрегат, характеризуется тремя диапазонами, соотношения которых могут быть следующими:
- 1:2;
- 1,25:1;
- 1:5,8.
Все они переключаются вручную.
Положение оси бабки регулируется также в ручном режиме при помощи двух винтов. Смазка бабки выполняется от установленной на основании агрегата специальной станции смазки, имеющей собственный электродвигатель. Имеющийся датчик нарезания резьбы позволяет производить на шпиндельной бабке процесс резьбонарезания.
Шпиндель установки размещается в однорядном и двухрядном коническом подшипниках. В процессе использования станка их регулировку выполнять нет необходимости, так как данная процедура осуществляется на комбинате-производителе.
Приводом движения (главного) в описываемом нами токарном агрегате выступает асинхронный частотно-регулируемый двигатель. Передача вращения от него на шпиндельную бабку (а именно на ее передний вал) обеспечивается ремнем поликлинового типа 2240Л20, передаточное отношение его составляет 115:257.
На основании станка, которое является, по сути, жесткой отливкой, монтируется электродвигатель, станина, станции смазки бабки и направляющих каретки. Имеются агрегаты с основаниями двух разных видов:
-
Без окна для удаления стружки: такой вариант основания представляет собой отсек, разделенный в средней своей части вертикальной сплошной перегородкой. В данном случае отделение в правой нижней части выполняет функцию резервуара стружки, в средней части – сборника стружки; Справа (сзади от основания) монтируется насос. -
С окном, по которому стружка сходит. При такой конструкции с правой стороны монтируется транспортер для удаления стружки.
Конструкция приводов продольного и поперечного перемещения:
Привод перемещения деталей в поперечном направлении состоит из:
- Опоры винта;
- Передачи шарикового принципа действия;
- Датчика связи (он посредством муфт соединяется с винтом);
- Винт-гайки качения;
- Двигателя (он может быть асинхронным либо постоянного тока).
Если станок работает с асинхронным двигателем, в его конструкции имеется возможность добавочной передачи на валик управления суппортом при консервации и проведении обслуживающих работ агрегата, находящегося в выключенном состоянии. В остальных случаях суппорт передвигается за головку винта с применением ключа.