Файл: Технология сборки и сварки коптильни из листового металла.docx
ВУЗ: Не указан
Категория: Не указан
Дисциплина: Не указана
Добавлен: 26.10.2023
Просмотров: 321
Скачиваний: 7
ВНИМАНИЕ! Если данный файл нарушает Ваши авторские права, то обязательно сообщите нам.

Внешний осмотр сварных швов на легированных сталях с целью выявления трещин выполняют дважды: сразу же после сварки и спустя 15—30 дней. Это объясняется тем, что структурные изменения в легированных сталях происходят медленно, и трещины могут появиться после того, как изделие уже осмотрено. Для получения сварного соединения хорошего качества необходимо осуществлять контроль, начиная с проверки качества подготовки шва и кончая проверкой полученного сварного соединения. Качество основного металла, электродной проволоки, присадочного металла, флюса и других материалов проверяют по сертификатам и заводским документам. Маркировка и качество должны соответствовать установленным техническим условиям и технологическому процессу сварки. Сборку под сварку и разделку шва проверяют по стандартам и техническим условиям. Сварное соединение проверяется внешним осмотром, металлографическими исследованиями, химическим анализом, механическими испытаниями, просвечиванием рентгеновскими и гамма-лучами, магнитными методами и с помощью ультразвука. Предварительно сварное соединение очищают от шлака, окалины и металлических брызг. Внешним осмотром выявляют наружные дефекты шва. Осмотр производят невооруженным глазом или с помощью лупы с десятикратным увеличением. Размеры сварных швов проверяют шаблонами и мерительным инструментом. Металлографические исследования Заключаются в следующем: сверлят отверстие, проходящее через шов и основной металл. Поверхность отверстия протравливают 10%-иым водным раствором двойной соли хлорной меди и аммония в течение 1...3 мин. Осадок меди удаляют водой. Протравленную поверхность осматривают невооруженным глазом или с помощью лупы. При этом выявляют качество провара и наличие внутренних дефектов. Для ответственных сварных конструкций производят более полные металлографические исследования макро - и микрошлифов из специально сваренных контрольных пластин или из пластин, вырезанных из сварных соединений. Химическим анализом определяют сослав основного и наплавленного металлов и электродов, а также их соответствие установленным техническим условиям на изготовление сварного изделия. Методы отбора проб для химического и спектрального анализов предусмотрены ГОСТ 7122—81. Механические испытания проводят либо специально сваренных контрольных образцов, либо образцов, вырезанных из сварного соединения. Определяют предел прочности на растяжение, ударную вязкость, твердость и угол загиба. Рентгенодефектоскопия основана на различном поглощении рентгеновских лучей различными веществами. Этим методом обнаруживают поры, Микротрещины, непровары, неметаллические включения. Рентгеновские лучи направляют на сварной шов, а с обратной стороны, прикладывают фотопленку.
3 Дефекты сварных соединений
Дефекты бывают нескольких видов - наружные и внутренние. Наружными являются дефекты, которые можно обнаружить визуально при осмотре сварочного шва. Внутренние дефекты, наоборот, находятся внутри сварочных соединений и их можно увидеть лишь после дефектоскопии, включая рентген и механическую обработку. Дефекты бывают допустимыми и не допустимыми, в зависимости от требований, предъявляемых к сварочным соединениям и конструкции в целом. Однако, исходя из самого определения, любые дефекты являются дефектами и требуют их полного устранения либо сведения к минимуму их количества и размеров. Так как дефекты сварных швов являются причиной, в результате которой есть риск поставить под угрозу стабильность соединения и функциональность сварной конструкции, есть ряд операций, чтобы их устранить. Чтобы свести к минимуму вероятность появления дефектов следует обязательно учитывать:
-
1) Технологию сварки и квалификацию сварщика -
2) Присадочный материал и свариваемый металл -
3) Подготовку поверхности под сварку и защитный газ -
4) Режимы и применяемое сварочное оборудование
-
Наружные дефекты
-
К наружным дефектам относятся нарушения геометрических размеров (подрезы, наплывы), непровары и прожоги, незаваренные кратеры.
-
Непровар -
Основной причиной непроваров является -
недостаточный сварочный ток, так как он в большей степени влияет на проникновение в металл. Устранение дефектов этого вида обычно происходит путем повышения мощности сварочной дуги, уменьшением длины дуги и увеличением её динамики. Также причиной непроваров может быть большая скорость сварки или недостаточная подготовка кромок сварного соединения.
Непровары могут быть нескольких видов:
-
- когда сварочный шов проникает не на всю толщину металла при односторонней сварке (см. верхнюю часть на рисунке) -
- при двусторонней сварке встык швы не стыкуются друг с другом, образуя несплавление между собой (см. нижнюю часть на рисунке) -
- при сварке в тавр сварочный шов не проникает вглубь, а лишь цепляется за свариваемые кромки
Также причиной непроваров может быть большая скорость сварки или недостаточная подготовка кромок сварного соединения.
-
Подрез
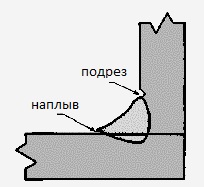
Подрезом называется дефект в виде канавки в основном металле по краям сварочного шва.Это наиболее распространенный дефект при сварке тавровых или нахлесточных соединений, но может также возникнуть и при сварке стыковых соединений. Этот вид дефекта обычно вызван неправильно подобранными параметрами, особенно скоростью сварки и напряжением на дуге. При угловой сварке (например при сварке длинных швов при сварке балок) подрезы часто возникают из за того, что сварочная дуга направлена больше на вертикальную поверхность. Расплавленный металл стекает на нижнюю кромку и его не хватает для заполнения канавки. При слишком высокой скорости сварки и повышенном напряжении, сварной шов образуется «горбатым». Из-за быстрого затвердевания сварочной ванны, в этом случае также образуются подрезы. Уменьшение скорости сварки постепенно сокращает размер подреза и в конечном итоге устраняет этот дефект. На подрезы влияет также длина сварочной дуги. При слишком длинной сварочной дуге ширина шва увеличивается, тем самым увеличивая количество расплавленного основного металла. Так как при увеличении длины дуги тепловложение остается прежним, его не хватает на весь сварочный шов, кромки быстро остывают, образуя подрезы. Уменьшение длины дуги не только избавляет от подрезов, но и увеличивает проплавление и устраняет такие дефекты, как непровар.
-
Наплыв Данный дефект появляется в результате натекания присадочного материала на основной металл без образования сплавления с ним. Обычно причиной этого дефекта является неправильно подобранные режимы сварки и окалина на свариваемой поверхности. Подбор правильного режима (соответствие сварочного тока со скоростью подачи присадочного материала, повышение напряжения на дуге) и предварительная очистка кромок устраняют появления наплывов. -
Прожог Данный дефект – отверстие насквозь в сварочном шве. В основном причинами прожога являются большой ток, медленная скорость сварки или большой зазор между кромками сварного соединения. В результате происходит прожог металла и утечка сварочной ванны. Понижение сварочного тока, увеличение скорости сварки и соответствующая подготовка геометрии кромок позволяют устранить прожоги. Прожоги являются очень частым дефектом при сварке алюминия, из его низкой температуры плавления и высокой теплопроводности.
-
Кратер Кратер появляется в конце сварочного шва в результате резкого обрыва дуги. Выглядит он в виде воронки в середине сварочного шва при его окончании. Современное сварочное оборудование имеет специальные программы для заварки кратера. Они позволяют проводить окончание сварки на пониженных токах, в результате чего кратер заваривается.
Внутренние дефекты
К внутренним основным дефектам сварных швов относят трещины (холодные и горячие) и поры.
-
Горячие трещины Горячие трещины появляются в то время, когда металл сварного шва находится в состоянии между температурами его плавления и затвердевания. Они могут быть в двух направлениях – вдоль и поперек сварного шва. Горячие трещины обычно являются результатом использования неправильного присадочного материала (в частности, алюминиевых и CrNi сплавов) и его химического состава (например, высокое содержание в составе углерода, кремния, никеля и др.) Горячие трещины могут появиться в результате неправильной заварки кратера, в результате резкого прекращения сварки.
-
Холодные трещины Трещины, которые возникают после того, как сварочный шов полностью остывает и затвердевает, называются холодными трещины. Эти дефекты также появляются тогда, когда сварочный шов не соответствует действующим на него нагрузкам и разрушается.
-
Поры
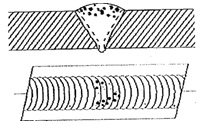
Пористость является одним из основных дефектов сварки, с которыми сталкиваются все сварщики при всех сварочных процессах. Пористость может быть вызвана загрязнением, плохой защитой ванны потоком сварочного газа, маслом, краской, сваркой несовместимых сплавов или даже ржавчиной и окислением металла. Поры могут различаться по размеру и, как правило, распределяются в случайном порядке по сварочному шву. Они могут находиться как внутри шва, так и на его поверхности.
Основные причины появления пористости:
1) Недостаточный поток защитного сварочного газа
2) Чрезмерный поток защитного газа. Это может вызвать подсос воздуха в поток газа.
3) Сквозняк в зоне сварки. Он может сдувать защитный газ.
- 1 2 3 4 5 6
4 Охрана труда на рабочем месте
К работе по профессии электрогазосварщика допускаются лица не моложе 18 лет, про шедшие медицинский осмотр, обучение и проверку знаний по данной профессии и по безопасной труда с присвоением II группы по электробезопасности и получившие соответствующее удостоверение.
Электрогазосварщик ежегодно, 1 раз в год, должен проходить периодическую проверь знаний по безопасности труда с подтверждением группы по электробезопасности комиссией, назначаемой приказом руководителя предприятия. При приеме на работу электрогазосварщик должен пройти вводный инструктаж, а в первый день выхода на работу - первичный инструктаж на рабочем месте. Получив вводный инструктаж по безопасности труда, электрогазосварщик должен расписаться в журнале регистрации вводного инструктажа и в личной карточке после того, как лицо, проводившее инструктаж, сделает запись о его проведении и распишется.
После обучения и проверки знаний по безопасности труда электрогазосварщик в течение первых 3 - 6 смен выполняет работу под наблюдением руководителя работ, после чего оформляет" допуск электрогазосварщика к самостоятельной работе в журнале регистрации инструктажа на рабочем месте и личной карточке. Электрогазосварщик не реже 1 раза в 3 месяца должен проходить повторный инструктажа. При изменении условий и требований безопасности труда (изменение технологического процесса, замена или модернизация оборудования, приспособлений и инструмента, изменение других факторов, влияющих на безопасность труда), при нарушении требований безопасности труда, которые привели или могут привести к травме, аварии, пожару или взрыву, а также при перерывах более чем и 30 календарных дней, электрогазосварщик должен пройти внеплановый инструктаж. При регистрации внепланового инструктажа указывается причина его проведения. После каждого вида инструктажа электрогазосварщик должен пройти проверку усвоении им знаний при инструктаже, которую осуществляет лицо, проводившее инструктажа Электрогазосварщик, не усвоивший инструктаж и показавший при проверке знаний по безопасности труда неудовлетворительные знания, к самостоятельной работе не допускается и обязан вновь пройти инструктаж и проверку знаний. Во время работы электрогазосварщик обязан пользоваться находящимися в “исправно” состоянии средствами индивидуальной защиты, выданными ему в соответствии с типовыми отраслевыми нормами. Электрогазосварщик обязан знать в необходимом для него объеме и соблюдать Правила пожарной безопасности и Правила техники безопасности при эксплуатации электроустановок потребителей.