ВУЗ: Не указан
Категория: Не указан
Дисциплина: Не указана
Добавлен: 29.10.2023
Просмотров: 176
Скачиваний: 1
ВНИМАНИЕ! Если данный файл нарушает Ваши авторские права, то обязательно сообщите нам.
необходимо снять щиты и кожухи, разобрать и снять системы пневматического управления и смазки, детали ленточного тормоза, цепи с зубчатых колес.
Лебедку разбирают на следующие узлы: подъемный и трансмиссионный валы, вал трансмиссии ротора, гидравлический тормоз и бак гидравлического тормоза. После демонтажа каждый узел очищают от остатков масла, промывают и направляют на разборку.
Подъемный вал разбирают на гидравлическом прессе; для этого вал укладывают на специальных стойках пресса.
Подъемный вал разбирается в следующем порядке: снимают детали пневмоуправления, разбирают болтовые соединения и снимают диск и шинно-пневматическую муфту ШПМ-1070, снимают при помощи пресса ступицу, затем отвинчивают гайки и вынимают болты; легкими ударами молотка снимают барабан муфты ШПМ-1070 и звездочку, отсоединяют крышки подшипников ступицы и при помощи винтового съемника стягивают с вала ступицу с роликовыми подшипниками. Последним с левой стороны барабана снимают коренной подшипник, для чего сначала отсоединяют от корпуса подшипника крышку, снимают корпус, а затем при помощи пресса снимают подшипник.
После этого вал поворачивают на 180° и разбирают другой конец вала (со стороны кулачковой муфты включения гидравлического тормоза). Демонтируют при помощи пресса кулачковую муфту и звездочку, отсоединяют крышку от корпуса коренного подшипника, снимают корпус, при помощи пресса снимают коренной подшипник, затем распорную втулку, отвинчивают болты и легкими ударами молотка снимают звездочку, последней снимают кулачковую муфту.
После того как с обоих концов вала сняты детали, снимают тормозные шкивы барабана, для чего отвинчивают гайки и выбивают болты, а затем ударами кувалды сбивают шкивы. После этого при помощи пресса выпрессовывают из барабана вал.
После разборки подъемного вала все его детали промываются и поступают на контроль. При контроле детали проверяют в соответствии с техническими условиями на выбраковку и сортируют на годные детали, детали, подлежащие восстановлению и негодные.
Разборка трансмиссионного вала производится в следующем порядке: снимают детали пневмоуправления, диск и шинно-пневматические муфты ШПМ-700, отсоединяют крышки подшипников,
снимают при помощи винтового съемника ступицу с роликовыми подшипниками. Последними с этого конца вала снимают при помощи винтового съемника спаренную звездочку с роликовыми подшипниками.
Ремонт вала
Ремонт проводится путем внедрения методов наплавки и металлизации при обработке подъемного вала буровой лебедки агрегата А – 50.
Основные конструктивные и технико-эксплуатационные показатели:
Металлизация - расплавленный металл распыляется струей сжатого воздуха, при том мелкие частицы металла с большой скоростью ударяются, о предварительно подготовленную поверхность детали сцепляется с ней, а последующие частицы сцепляются с предыдущим слоем частиц.
Метод восстановления наплавкой заключается в наращивании изношенных поверхностей путем расплавления присадочного металла к наплавляемой поверхности с последующей ее механической обработки. Степень внедрения: подъемный агрегат для капитального ремонта скважин А – 50.
Основной причиной выхода деталей из строя является износ. В большинстве случаев изношенные детали могут быть восстановлены и повторно использованы.
Подъемный вал изготавливают из стали 30ХНМА ГОСТ 4543-71.
Шейки валов буровых лебедок рекомендуется наращивать металлизацией.
Изношенные шпоночные пазы обычно наплавляют смятые кромки или шпоночный паз полностью, и фрезеруют новый паз на месте наплавки.
Шейки вала, работающего в подшипниках скольжения, обычно вырабатываются неравномерно и в продольном сечении принимают форму конуса, в поперечном - эллипса. Шейки вала, работающего в подшипниках качения, изнашиваются при протачивании внутренней обоймы подшипника на валу вследствие послабления при изготовлении или выработке посадочных мест в процессе эксплуатации буровой лебедки.
В зависимости от износа посадочных мест валов применяют следующие методы восстановления: хромирование при износе посадочных мест до 0,3 мм; осталивание (железнение) с последующим шлифованием при износе посадочных мест до 0,8 мм; наплавку при износе посадочных мест более 0,8 мм.
В ремонтном производстве для восстановления валов и роторов часто применяют электродуговую наплавку под слоем флюса, в среде диоксида углерода, в струе охлаждающей жидкости, с комбинированной защитой дуги, порошковой лентой и др. Автоматическую электродуговую наплавку под слоем флюса широко применяют для наплавки валов и роторов, изготовленных из нормализованных и закаленных среднеуглеродистых и низколегированных сталей, а также из малоуглеродистых сталей, не подвергающихся термической обработке, имеющих износ от 0,3 до 4,0 мм при однослойной наплавке и свыше 4 мм - при многослойной. Производительность процесса очень высока. Валы диаметром до 50 мм этим способом восстанавливать сложно, так как шлак, не успев затвердеть, стекает с наплавляемого изделия.
Электродуговая наплавка в среде диоксида углерода широко распространена в ремонтном производстве для восстановления валов диаметром до 40 мм.
Автоматическая наплавка порошковой проволокой, которая позволяет наносить слой металла любого химического состава и получать закалочные структуры различной твердости, получила широкое распространение в последнее время.
Автоматическая наплавка ленточным электродом и порошковой лентой в 2-3 раза производительнее, чем обычной электродной проволокой, и дает возможность за один ход аппарата наносить слой металла шириной до 100 мм, толщиной 2-8 мм. Этим способом нельзя наплавлять валы малого диаметра. Тугоплавкие сплавы наплавляют плазменным способом, который производительнее других способов.
В последние годы разработаны новые способы наплавки с комбинированной защитой дуги и сварочной ванны для устранения отдельных недостатков того или иного способа восстановления.
При восстановлении посадочных мест вала и ротора ручной электродуговой наплавкой поврежденное место вала и ротора протачивают на станке на величину наиболее глубоких повреждений. Затем наплавляют вал до нужных размеров с учетом последующей проточки и шлифовки.
Наиболее ответственная операция - наплавка вала. Кроме ручной применяют автоматическую электродуговую наплавку вибрирующим электродом. Восстановление валов вибродуговой наплавкой показано на рисунке 2.
При наплавке лентой от проплавления основного металла зависит степень его перемешивания с наплавленным. Благодаря постоянному перемещению дуги глубина проплавления основного металла при наплавке лентой меньше, чем при наплавке проволокой.
Наибольшее влияние на глубину проплавления и перемешивания основного металла с наплавленным оказывает скорость наплавки с ее ростом увеличивается глубина проплавления, уменьшаются ширина и толщина наплавляемого валика.
При малых скоростях наплавки снижается проплавление основного металла. Для наплавки холоднокатаной электродной лентой используют сварочные аппараты АДС-1000-2, А-384, А-874, TC-3.S, сварочные преобразователи постоянного тока ПС-500, ПТС-500, ПС-1000, ПСМ-1000-4 и выпрямители ВС-600, ВС-1000, ВКСМ-1000, ВКСМ-2000. Наплавку осуществляют лентами из стали 08кп и коррозионно-стойких сталей. Широкое применение получили металлокерамические ленты ЛМ-70ХЗНМ, ЛМ-20ХЮПОТ, ЛМ-1Х14НЗ, ЛМ-5Х4ВЗФС, разработанные в Институте электросварки им. Е. О. Патона.
1 - рабочие колеса; 2 - вал; 3 - головка для наплавки
Рисунок 2 - Восстановление валов автоматической электродуговой наплавкой вибрирующим электродом
Наплавку металлокерамическими лентами ведут постоянным током обратной полярности плотность тока на электроде 10-20 А/мм², напряжение дуги 28-32 В, скорость наплавки 0.16-0.55м/с, скорость подачи ленты 15-150м/ч. Сила тока в зависимости от ширины следующая:
Восстановление деталей контактным элекроипульсным покрытием заключается в приварке металлической ленты под воздействием сварочных импульсов. Чтобы исключить нагрев детали и улучшить условия закалки приварного слоя, в зону сварка подают охлаждающую жидкость.
При приварке ленты толщиной 0,3 - 0,4 мм рекомендуемая емкость батареи конденсаторов 6400 мкФ. Напряжение заряда конденсаторов регулируют в пределах 260 - 425 В. Ленту приваривают при напряжении 325 - 380 В.
Чем больше диаметр восстанавливаемой детали и толщина привариваемой ленты, тем выше требуемое напряжение заряда конденсаторов.
Свариваемость ленты с основным материалом в зависимости от амплитуды и длительности импульса тока определяют по глубине вмятин сварной точки, числу пор на поверхности деталей, прошлифованных до номинального размера, и шелушению приварного слоя толщиной 0,15 - 0,02 мм.
Правка подъемного вала буровой лебедки рекомендуется править с нагревом. Вал закрепляют вогнутой стороной вниз. Вогнутый участок обкладывают мокрым асбестом и закрепляют его на валу проволокой. Выпуклый открытый участок нагревают газовой горелкой до температуры 500-550 0С, после нагретый участок накрывают листовым асбестом и дают валу полностью остыть. В результате такой обработки вал выпрямляется. Качество правки проверяют индикатором.
Отремонтированный подъемный вал должен быть проверен магнитной дефектоскопией или другим методом на отсутствие внутренних трещин.
3.5 Основные требования к отремонтированным лебедкам
К отремонтированным лебедкам предъявляют следующие основные требования.
11. Радиальный зазор между колодками и шкивами шинно-пневматических муфт должен быть одинаковым по окружности в пределах 2,5-4 мм.
12. Пневматическая система после сборки должна быть испытана сжатым воздухом на прочность и плотность при давлении 1 МПа в течение 5 мин. Утечка воздуха не допускается. Шланги на штуцерах должны быть закреплены с помощью хомутиков свинтами.
Лебедку разбирают на следующие узлы: подъемный и трансмиссионный валы, вал трансмиссии ротора, гидравлический тормоз и бак гидравлического тормоза. После демонтажа каждый узел очищают от остатков масла, промывают и направляют на разборку.
Подъемный вал разбирают на гидравлическом прессе; для этого вал укладывают на специальных стойках пресса.
Подъемный вал разбирается в следующем порядке: снимают детали пневмоуправления, разбирают болтовые соединения и снимают диск и шинно-пневматическую муфту ШПМ-1070, снимают при помощи пресса ступицу, затем отвинчивают гайки и вынимают болты; легкими ударами молотка снимают барабан муфты ШПМ-1070 и звездочку, отсоединяют крышки подшипников ступицы и при помощи винтового съемника стягивают с вала ступицу с роликовыми подшипниками. Последним с левой стороны барабана снимают коренной подшипник, для чего сначала отсоединяют от корпуса подшипника крышку, снимают корпус, а затем при помощи пресса снимают подшипник.
После этого вал поворачивают на 180° и разбирают другой конец вала (со стороны кулачковой муфты включения гидравлического тормоза). Демонтируют при помощи пресса кулачковую муфту и звездочку, отсоединяют крышку от корпуса коренного подшипника, снимают корпус, при помощи пресса снимают коренной подшипник, затем распорную втулку, отвинчивают болты и легкими ударами молотка снимают звездочку, последней снимают кулачковую муфту.
После того как с обоих концов вала сняты детали, снимают тормозные шкивы барабана, для чего отвинчивают гайки и выбивают болты, а затем ударами кувалды сбивают шкивы. После этого при помощи пресса выпрессовывают из барабана вал.
После разборки подъемного вала все его детали промываются и поступают на контроль. При контроле детали проверяют в соответствии с техническими условиями на выбраковку и сортируют на годные детали, детали, подлежащие восстановлению и негодные.
Разборка трансмиссионного вала производится в следующем порядке: снимают детали пневмоуправления, диск и шинно-пневматические муфты ШПМ-700, отсоединяют крышки подшипников,
снимают при помощи винтового съемника ступицу с роликовыми подшипниками. Последними с этого конца вала снимают при помощи винтового съемника спаренную звездочку с роликовыми подшипниками.
Ремонт вала
Ремонт проводится путем внедрения методов наплавки и металлизации при обработке подъемного вала буровой лебедки агрегата А – 50.
Основные конструктивные и технико-эксплуатационные показатели:
Металлизация - расплавленный металл распыляется струей сжатого воздуха, при том мелкие частицы металла с большой скоростью ударяются, о предварительно подготовленную поверхность детали сцепляется с ней, а последующие частицы сцепляются с предыдущим слоем частиц.
Метод восстановления наплавкой заключается в наращивании изношенных поверхностей путем расплавления присадочного металла к наплавляемой поверхности с последующей ее механической обработки. Степень внедрения: подъемный агрегат для капитального ремонта скважин А – 50.
Основной причиной выхода деталей из строя является износ. В большинстве случаев изношенные детали могут быть восстановлены и повторно использованы.
Подъемный вал изготавливают из стали 30ХНМА ГОСТ 4543-71.
Шейки валов буровых лебедок рекомендуется наращивать металлизацией.
Изношенные шпоночные пазы обычно наплавляют смятые кромки или шпоночный паз полностью, и фрезеруют новый паз на месте наплавки.
Шейки вала, работающего в подшипниках скольжения, обычно вырабатываются неравномерно и в продольном сечении принимают форму конуса, в поперечном - эллипса. Шейки вала, работающего в подшипниках качения, изнашиваются при протачивании внутренней обоймы подшипника на валу вследствие послабления при изготовлении или выработке посадочных мест в процессе эксплуатации буровой лебедки.
В зависимости от износа посадочных мест валов применяют следующие методы восстановления: хромирование при износе посадочных мест до 0,3 мм; осталивание (железнение) с последующим шлифованием при износе посадочных мест до 0,8 мм; наплавку при износе посадочных мест более 0,8 мм.
В ремонтном производстве для восстановления валов и роторов часто применяют электродуговую наплавку под слоем флюса, в среде диоксида углерода, в струе охлаждающей жидкости, с комбинированной защитой дуги, порошковой лентой и др. Автоматическую электродуговую наплавку под слоем флюса широко применяют для наплавки валов и роторов, изготовленных из нормализованных и закаленных среднеуглеродистых и низколегированных сталей, а также из малоуглеродистых сталей, не подвергающихся термической обработке, имеющих износ от 0,3 до 4,0 мм при однослойной наплавке и свыше 4 мм - при многослойной. Производительность процесса очень высока. Валы диаметром до 50 мм этим способом восстанавливать сложно, так как шлак, не успев затвердеть, стекает с наплавляемого изделия.
Электродуговая наплавка в среде диоксида углерода широко распространена в ремонтном производстве для восстановления валов диаметром до 40 мм.
Автоматическая наплавка порошковой проволокой, которая позволяет наносить слой металла любого химического состава и получать закалочные структуры различной твердости, получила широкое распространение в последнее время.
Автоматическая наплавка ленточным электродом и порошковой лентой в 2-3 раза производительнее, чем обычной электродной проволокой, и дает возможность за один ход аппарата наносить слой металла шириной до 100 мм, толщиной 2-8 мм. Этим способом нельзя наплавлять валы малого диаметра. Тугоплавкие сплавы наплавляют плазменным способом, который производительнее других способов.
В последние годы разработаны новые способы наплавки с комбинированной защитой дуги и сварочной ванны для устранения отдельных недостатков того или иного способа восстановления.
При восстановлении посадочных мест вала и ротора ручной электродуговой наплавкой поврежденное место вала и ротора протачивают на станке на величину наиболее глубоких повреждений. Затем наплавляют вал до нужных размеров с учетом последующей проточки и шлифовки.
Наиболее ответственная операция - наплавка вала. Кроме ручной применяют автоматическую электродуговую наплавку вибрирующим электродом. Восстановление валов вибродуговой наплавкой показано на рисунке 2.
При наплавке лентой от проплавления основного металла зависит степень его перемешивания с наплавленным. Благодаря постоянному перемещению дуги глубина проплавления основного металла при наплавке лентой меньше, чем при наплавке проволокой.
Наибольшее влияние на глубину проплавления и перемешивания основного металла с наплавленным оказывает скорость наплавки с ее ростом увеличивается глубина проплавления, уменьшаются ширина и толщина наплавляемого валика.
При малых скоростях наплавки снижается проплавление основного металла. Для наплавки холоднокатаной электродной лентой используют сварочные аппараты АДС-1000-2, А-384, А-874, TC-3.S, сварочные преобразователи постоянного тока ПС-500, ПТС-500, ПС-1000, ПСМ-1000-4 и выпрямители ВС-600, ВС-1000, ВКСМ-1000, ВКСМ-2000. Наплавку осуществляют лентами из стали 08кп и коррозионно-стойких сталей. Широкое применение получили металлокерамические ленты ЛМ-70ХЗНМ, ЛМ-20ХЮПОТ, ЛМ-1Х14НЗ, ЛМ-5Х4ВЗФС, разработанные в Институте электросварки им. Е. О. Патона.
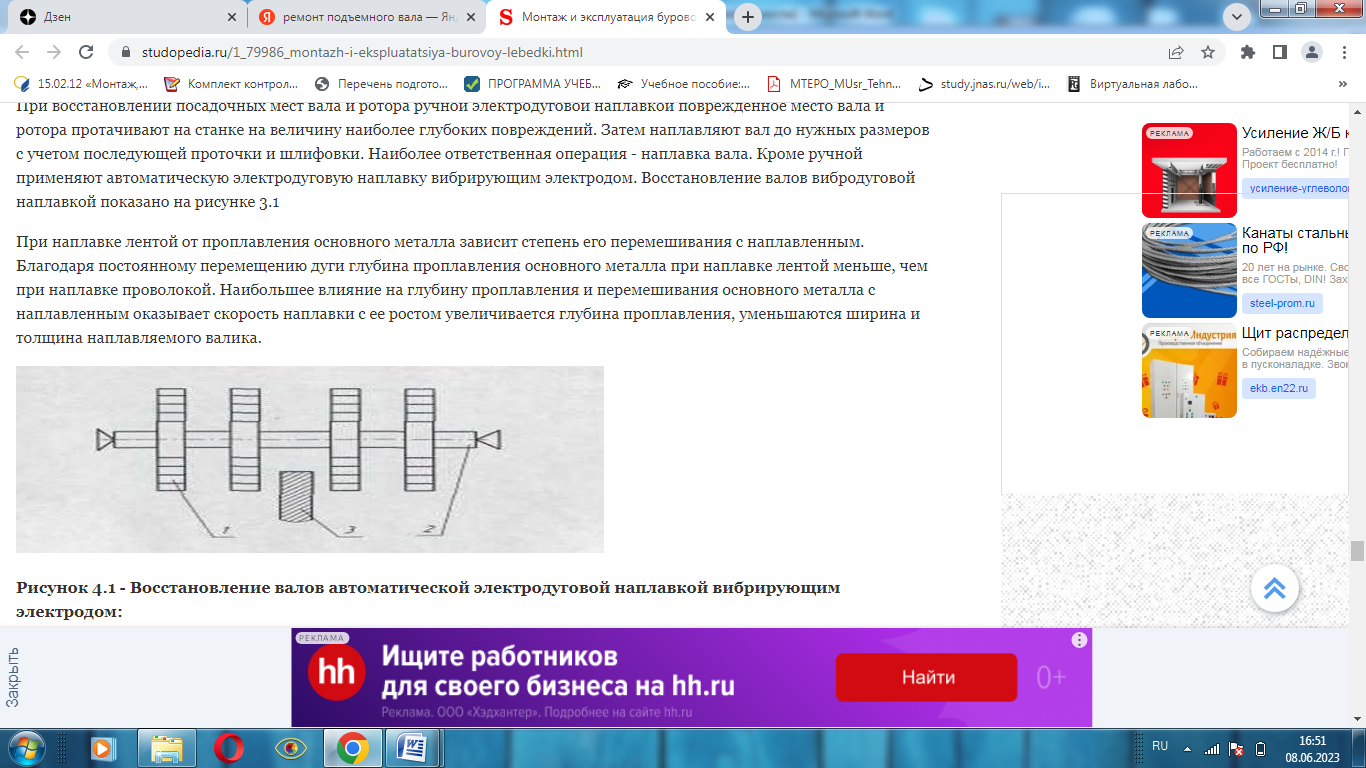
1 - рабочие колеса; 2 - вал; 3 - головка для наплавки
Рисунок 2 - Восстановление валов автоматической электродуговой наплавкой вибрирующим электродом
Наплавку металлокерамическими лентами ведут постоянным током обратной полярности плотность тока на электроде 10-20 А/мм², напряжение дуги 28-32 В, скорость наплавки 0.16-0.55м/с, скорость подачи ленты 15-150м/ч. Сила тока в зависимости от ширины следующая:
Восстановление деталей контактным элекроипульсным покрытием заключается в приварке металлической ленты под воздействием сварочных импульсов. Чтобы исключить нагрев детали и улучшить условия закалки приварного слоя, в зону сварка подают охлаждающую жидкость.
При приварке ленты толщиной 0,3 - 0,4 мм рекомендуемая емкость батареи конденсаторов 6400 мкФ. Напряжение заряда конденсаторов регулируют в пределах 260 - 425 В. Ленту приваривают при напряжении 325 - 380 В.
Чем больше диаметр восстанавливаемой детали и толщина привариваемой ленты, тем выше требуемое напряжение заряда конденсаторов.
Свариваемость ленты с основным материалом в зависимости от амплитуды и длительности импульса тока определяют по глубине вмятин сварной точки, числу пор на поверхности деталей, прошлифованных до номинального размера, и шелушению приварного слоя толщиной 0,15 - 0,02 мм.
Правка подъемного вала буровой лебедки рекомендуется править с нагревом. Вал закрепляют вогнутой стороной вниз. Вогнутый участок обкладывают мокрым асбестом и закрепляют его на валу проволокой. Выпуклый открытый участок нагревают газовой горелкой до температуры 500-550 0С, после нагретый участок накрывают листовым асбестом и дают валу полностью остыть. В результате такой обработки вал выпрямляется. Качество правки проверяют индикатором.
Отремонтированный подъемный вал должен быть проверен магнитной дефектоскопией или другим методом на отсутствие внутренних трещин.
3.5 Основные требования к отремонтированным лебедкам
К отремонтированным лебедкам предъявляют следующие основные требования.
-
Все детали и узлы лебедки должны быть изготовлены или
отремонтированы в полном соответствии с действующими чертежами и техническими условиями. Износ деталей, применяемых повторно, не должен превышать предельных размеров, установленных техническими условиями на выбраковку деталей при ремонте. -
Допустимое отклонение па непараллельность установленных на раме лебедки валов не должно превышать 2 мм на длине 2000 мм, а допустимое отклонение расстояния между валами должно быть не более 5 мм. -
Валы в подшипниках должны вращаться плавно, без заеданий, усилием одного рабочего. -
Парноработающие цепные колеса должны находиться в одной плоскости. -
У цепных колес и кулачковых муфт рабочие поверхности кулачков должны быть пригнаны друг к другу с зазором не более 0,25 мм. -
Тормозные шкивы должны иметь клеймо завода-изготовителя с указанием номера плавки и марки стали. Тормозные шкивы не должны иметь трещин, раковин и других дефектов. Минимальная допустимая толщина шкива 15-20 мм. -
Пальцы шарнирных соединений тормозной системы должны иметь шайбы и быть надежно зашплинтованными с зазором, обеспечивающим осевой лифт пальцев 2-3 мм. -
У цепных колес и кулачковых муфт рабочие поверхности кулачков должны быть пригнаны друг к другу с зазором не более 0,25 мм. -
Тормозные шкивы должны иметь клеймо завода-изготовителя с указанием номера плавки и марки стали. Тормозные шкивы не должны иметь трещин, раковин и других дефектов. Минимальная допустимая толщина шкива 15-20 мм. -
Пальцы шарнирных соединений тормозной системы должны иметь шайбы и быть надежно зашплинтованными с зазором, обеспечивающим осевой лифт пальцев 2-3 мм.
11. Радиальный зазор между колодками и шкивами шинно-пневматических муфт должен быть одинаковым по окружности в пределах 2,5-4 мм.
12. Пневматическая система после сборки должна быть испытана сжатым воздухом на прочность и плотность при давлении 1 МПа в течение 5 мин. Утечка воздуха не допускается. Шланги на штуцерах должны быть закреплены с помощью хомутиков свинтами.
-
Включение и выключение кулачковых муфт должно быть плавным, без заеданий, от усилия на рукоятку не более 250 Н. -
Подшипники и все маслоподводящие каналы должны быть промыты и заполнены свежей смазкой. -
Щиты ограждений должны быть из листовой стали толщиной не менее 4-5 мм и надежно закреплены. -
Все обработанные поверхности деталей и щиты лебедки должны быть покрашены стойкой краской.