Файл: Анализ хозяйственной деятельности обогатительной фабрики Айхальского гок ак алроса.docx
Добавлен: 08.11.2023
Просмотров: 224
Скачиваний: 4
ВНИМАНИЕ! Если данный файл нарушает Ваши авторские права, то обязательно сообщите нам.
По правому борту хвостохранилища расположен руслоотводный канал длиной 2120 метров.
Хвосты обогатительной фабрики поступают в хвостохранилище самотеком по магистральному футерованному пульповоду диаметром 700 мм и длиной 1000 мм.
Расчетный срок эксплуатации 20 лет.
Вместимость хвостохранилища 61 млн.м3.
Занимаемая площадь 330 гектар.
Система оборотного водоснабжения фабрики практически полностью замкнута за исключением минимального (до 90 м3/ч) забора чистой воды для технологических нужд. В связи с малой длиной пляжа исключается возможность пылевого загрязнения атмосферы. Другие факторы негативного влияния хвостохранилища отсутствуют. Таким образом, при проектном режиме эксплуатации хвостохранилища исключается возможность загрязнения окружающей среды и сооружения являются экологически безопасными.
Насосные станции - один из важнейших элементов систем водоснабжения. С помощью насосов и связанных с ними всасывающих труб и напорных водоводов насосные станции обеспечивают транспортирование воды от сооружения к сооружению и потребителям.
По расположению в схеме водоснабжения и назначению насосные станции разделяются на станции I подъема, II подъема, повысительные и циркуляционные. Насосные станции I подъема подают воду из источника водоснабжения на очистные сооружения или, если не требуется очистки воды, непосредственно в распределительную сеть, водонапорные башни и другие сооружения. Насосные станции II подъема служат для подачи воды от резервуаров чистой воды, расположенных после очистных сооружений, в распределительную сеть и водонапорные башни. Повысительные насосные станции предназначаются для повышения напора в водопроводной сети. Циркуляционные насосные станции устраиваются в промышленных системах оборотного водоснабжения для подачи отработанной воды на очистные и охлаждающие устройства и возврата этой воды на предприятие.
Производительность насосных станций определяется по количеству воды, потребляемой объектом водоснабжения, с учетом режима водопотребления и размеров регулирующих емкостей. Напор, который должны создавать насосные станции, зависит от необходимого свободного напора и рельефа местности.
При выборе типа насосов и количества рабочих агрегатов следует учитывать совместную работу насосов и водоводов или водопроводной сети.
В зависимости от надежности действия насосные станции разделяют на три класса: I - не допускается перерыв в работе насосов; II - допускается перерыв в работе насосов на время, необходимое для включения резервных агрегатов; III - допускается перерыв в подаче воды потребителям на время ликвидации аварии. Для обеспечения требуемой надежности действия насосных станций их оборудуют кроме рабочих агрегатов резервными, количество которых следует принимать по данным таблица 1.1.
Таблица 1.1
Количество резервных агрегатов, устанавливаемых на насосных станциях.
Количество рабочих агрегатов | Количество резервных агрегатов на станциях класса | ||
I | II | III | |
1 | 2 | 1 | 1 |
2-3 | 2 | 1 | 1 |
4-6 | 2 | 2 | 1 |
7-9 | 3 | 3 | 2 |
Для удобства монтажа и эксплуатации и ремонта оборудования на насосных станциях целесообразно применять однотипные насосы с одинаковой производительностью. Насосные агрегаты в зданиях насосных станций располагаются по следующим схемам: в один ряд с параллельным расположением осей (рисунок 1); в один ряд с расположением осей по одной прямой; в два ряда с параллельным расположением осей в каждом ряду; в два ряда с расположением в каждом ряду по одной прямой (рисунок 1.1).
Рисунок 1.1
Схема насосной станции с однорядным расположением агрегатов.
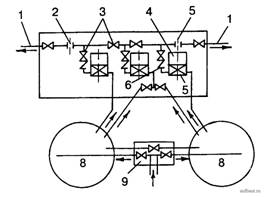
1 - напорные трубопроводы; 2 - водомеры; 3 - задвижки; 4 - электродвигатель; 5 - насос; 6 - обратный клапан; 7 - всасывающие линии; 8 - резервуары; 9 - камера переключения.
При выборе схемы расположения агрегатов в здании необходимо учитывать конкретные условия проектирования, количество и размеры агрегатов, заглубление насосной станции в грунт и способы производства работ, количество всасывающих камер водоприемного колодца и их размер по фронту (для насосных станций I подъема), количество и размеры резервуаров чистой воды (для насосных станций I подъема), арматуру, которой оборудуются напорные трубопроводы, и т. д. Принятая схема расположения агрегатов должна обеспечивать минимальные размеры здания насосной станции, удобство монтажа и демонтажа насосных агрегатов и простоту эксплуатации насосной станции.
Рисунок 1.2
Схема насосной станции с двухрядным расположением агрегатов.
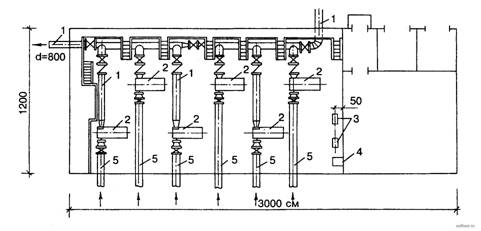
1 - напорные трубопроводы; 2 - центробежный насос с электродвигателем; 3 - вакуум-насос; 4 - дренажный насос; 5 - всасывающие линии
2. ТЕХНОЛОГИЧЕСКИЙ РАСЧЕТ
2.1 Технология ремонта насосного оборудования
Надежная и безотказная работа насосного оборудования обеспечивается только из-за надлежащего надзора за ним и своевременного ремонтных работ.
К текущему ремонтным работам центробежных насосов относятся: замена уплотнительных колец, набивка сальников, замена прокладок, предотвращение разбега ротора, центровка насоса, замена подшипников, масляная покраска насосного агрегата и трубопроводов. Длительность этапа между текущими ремонтами составляет не более трех месяцев или по мере необходимости.
Капитальный ремонт предусматривает: полную проверку насоса с чисткой, разборкой, регулированием и сменой частей; балансировку рабочего колеса; правку вала обточкой; замену вала; шлифовку шеек вала и уплотняющих колец; перезаливку либо замену вкладышей подшипников; смену рабочих колес и уплотнений; срезку либо наращивание рабочих колес насоса. Периодичность работ по капитальному ремонту центробежных насосов насосных станций составляет 1,5…3 года.
Вид ремонтных работ насоса определяют при его разборке, при этом в то же время составляют дефектировочную карту на узлы и детали насоса.
Основные неисправности насоса и методы их устранения приведены в таблице 1.1.
Таблица 2.1
Основные неисправности насоса и методы их устранения.
Наименование неисправности | Вероятная причина | Способ устранения | |||
1. Насос не подает жидкость | а)стрелки приборов сильно колеблются. | - насос не залит или недостаточно залит жидкостью; - велика высота всасывания; | - залить насос и трубопровод жидкостью; | ||
б)манова-куумметр показывает разрежение выше требуемого. | - происходит подсос воздуха в местах соединения во всасывающем трубопроводе или через сальник; - закрыта задвижка на всасывающем трубопроводе. | -привести сопротивление всасывающей линии в соответствие с характеристикой насоса; - устранить неплотность соединений, обеспечить нормальную работу сальника; - открыть задвижку. | |||
2. Подача меньше требуемой по характеристике | - обратное вращение вала; - низкая частота вращения; - велико сопротивление всасывающего или напорного трубопровода; - происходит подсос воздуха в местах соединения во всасывающем трубопроводе или через сальник; - высота всасывания превышает допустимую при заданной температуре; - засорены всасывающий трубопровод и насос; - сильный износ уплотняющего кольца. | - переключить фазы электродвигателя; - параметры энергопитания довести до нормального; - привести сопротивление всасывающей или напорной линии в соответствие с характеристикой насоса; - устранить неплотность соединений, обеспечить нормальную работу сальника; - уменьшить допустимую высоту всасывания; - очистить трубопровод и насос; - заменить уплотняющие кольца. | |||
3. «Горит» сальник | - износилась набивка сальника; - слишком затянуты гайки крышки сальника; - в сальник не поступает затворная и охлаждающая жидкость. | - заменить набивку сальника; - ослабить затяжку гаек крышки сальника; - подать в сальник затворную и охлаждающую жидкость. | |||
4. Температура нагрева подшипников превышает температуру помещения более чем на 40…50К (40…50°С) | - недостаточно смазки; - нарушена сносность валов; - загрязнена смазка; - износ подшипников. | - добавить смазки; - отцентровать валы насоса и двигателя; - сменить смазку; - заменить подшипники. | |||
5. Завышена потребляемая мощность, двигатель нагревается | - неправильная сборка насоса, вал не проворачивается вручную; - в насос попал песок или другие абразивные вещества; - насос работает за пределами рабочего интервала подач. - отрегулировать | - отрегулировать торцевые зазоры рабочего колеса, устранить перекосы; - разобрать насос и прочистить его. | |||
6. Ненормальный шум внутри насоса (в насосе происходит явление кавитации) | - велика подача; - велико сопротивление на всасывании; - высокая температура перекачиваемой жидкости. | - уменьшить подачу; - уменьшить температуру. | |||
7. Повышенная вибрация насоса | - нарушена сносность насоса и двигателя; - насос не закреплен на раме. | - произвести центрование валов; - закрепить насос на раме. |
При разборке насоса первоначально снимают ограждение муфты, а далее пальцы упругой муфты и буксы сальников; отсоединяют торцевые крышки подшипников; освобождают шпильки согласно разъему корпуса, отжимными винтами подрывают крышку насоса и снимают ее, снимают ротор и укладывают его на козлы; снимают полумуфты, уплотняющие кольца, шарикоподшипники и рабочее колесо.
Сальниковые камеры центробежных насосов заполняются сальниковыми набивками (ГОСТ 5152—84) квадратного или круглого сечения. Размеры сечения набивок контролируют штангенциркулем или толщиномером. Внешний вид их проверяют визуально: поверхность набивок не должна иметь местных утолщений, неровностей, повреждений оплетки, выступающих оборванных ниток.
Для набивки сальников насоса рекомендовано применят пропитанные набивки, из-за чего сухие вызывают быстрое изнашивание втулок вала и выгорают из-за трения.
Перед тем как применить набивку ХБС заранее проваривают в техническом жиру.
Сальниковую набивку необходимо менять на новую через каждые 300-500 отработанных часов зависимости от температуры воды, наличия механических примесей и др.
Реконструкция сальниковых уплотнений состоит в том, что подвод воды на них демонтируется. Отверстие Б глушат пробкой. Снимают три внутренних кольца набивки и гидрозатворное кольцо, а на их место устанавливают изготовленную стальную втулку и три кольца сальниковой набивки, между которыми размещают фторопластовые или паронитовые прокладки толщиной 2-3 мм.3
При правильной сборке сальникового уплотнения ротор свободно поворачивается на валу, а величина утечки воды находится в пределах 5… 10 л/ч.
Рисунок 2.1
Реконструкция сальниковых уплотнений насосов типа «Д», работающих
под давлением
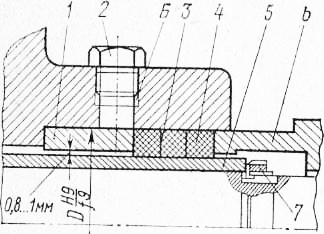
1 - втулка дистанционная (чугун, сталь, бронза, фторопласт); 2 - пробка (сталь, чугун, пластмасса); 3 - прокладка (фторопласт листовой 6-2…3 мм); 4 - набивка сальниковая; 5 - втулка защитная (чугун СЧ20, сталь 45 или 20X13 HRC 40…30); 6 - букса (втулка нажимная); 7 - гайка круглая.
Сборку насоса производят в обратной последовательности.
Перед тем как начать сборку посадочные поверхности смазывают маслом.
С целью уменьшения объемных потерь на рабочее колесо в центробежных насосах жестко устанавливают уплотнение, а в корпусе насоса запрессовывают неподвижное уплотнение. По мере износа уплотнение на рабочем колесе заменяют новым.