Добавлен: 08.11.2023
Просмотров: 270
Скачиваний: 4
ВНИМАНИЕ! Если данный файл нарушает Ваши авторские права, то обязательно сообщите нам.
, узлы механизма, тяговый хомут и детали, передающие нагрузку на раму вагона, необходимо изготовлять из соответствующих углеродистой и низколегированной сталей.
Механические свойства металла при этом могут несколько различаться для разных деталей. Так, металл корпуса автосцепки и тягового хомута должен иметь предел прочности 52—55 кгс/мм2 при пределе текучести не менее 30 кгс/мм2, относительном удлинении не менее 18% и ударной вязкости при —60° С не менее 2,5 кгс-м/см2. Металл деталей механизма сцепления и деталей, передающих нагрузку на раму вагона, должен иметь предел прочности не менее 45 кгс/мм2, предел текучести не менее 25 кгс/мм2, ударную вязкость при 20° С не менее 5 кгс м/см2 и т. д.
Все перечисленные детали автосцепного устройства подвержены весьма интенсивному износу в эксплуатации, поэтому нуждаются в периодическом ремонте для восстановления изношенных мест наплавкой электродами. По этой причине содержание углерода в стали для них ограничено 0,27%. Если в металле этих деталей углерода содержится более 0,25%, то на них ставят знак в виде буквы С, указывающий на необходимость при заварке дефектов или наплавке изношенных поверхностей подогревать ремонтируемую деталь до температуры 250—300° С.
В качестве материала для деталей поглощающего пружинно-фрикционного аппарата применяют углеродистую сталь с повышенным содержанием углерода или легированную сталь. В конструкции гидравлических, гидропневматических, резинометалли-ческих и других аппаратов помимо сталей используют и другие материалы: бронзу, резину, пластмассы и т. п. Корпус пружинно-фрикционного поглощающего аппарата отливают из стали 32Х06Л или ЗОГСЛ (ГОСТ 977—75) и подвергают закалке и отпуску до твердости НВ 207—277. Клинья и корпус аппарата изготовляют штамповкой из стали 30 (ГОСТ 1050—74) и подвергают нитроце-ментации или цементации с последующей закалкой и отпуском до твердости HRC 50—64. Допускается изготовлять клинья и конусы из стали 38ХС (ГОСТ 4543—71) с закалкой до твердости НВ 341—477. Клин или валик тягового хомута, а также упорную плиту и подвески центрирующего прибора рекомендуется изготовлять штамповкой из стали 38ХС с последующей закалкой и отпуском до твердости НВ 255—321.
В конструкции магистральных вагонов в зависимости от их типа применяют несколько разновидностей автосцепных устройств. Основную разновидность автосцепного устройства (ГОСТ 3475—62) применяют на четырехосных грузовых вагонах. Характерной особенностью этого устройства является применение типовой автосцепки СА-3 и поглощающего аппарата Ш-1-Тм, устанавливаемого в проем между упорами, равный 625 мм. Ход аппарата 70 мм. Корпус автосцепки опирается на центрирующий прибор без подпружинивания (см. рис. 44).
В пассажирских вагонах (в том числе электропоездов и дизель-поездов) применяют автосцепное устройство, отличающееся от предыдущего типом поглощающего аппарата и центрирующего прибора. В этом устройстве применен резинометаллический поглощающий аппарат Р-2П.
В шести- и восьмиосных вагонах применяют так называемое модернизированное автосцепное устройство (рис. 45), которое существенно отличается от автосцепного устройства четырехосных вагонов по конструкции корпуса автосцепки 1, хомута 3, узла 2 соединения корпуса с хомутом и центрирующего прибора 4. Узел соединения корпуса автосцепки с тяговым хомутом выполнен в отличие от соответствующего узла типового автосцепного устройства не с клином, а с валиком и сферическим вкладышем. Модернизированное автосцепное устройство допускает использование поглощающих аппаратов с ходом до 110 мм при стандартном расстоянии между упорами 625 мм. В модернизированном автосцепном устройстве использован центрирующий прибор с подпружиненной опорой для хвостовика автосцепки.
Автосцепные устройства восьмиосных вагонов, имеющих значительную длину консолей, оборудованы специальным приспособлением для принудительного отклонения автосцепки в кривых участках пути (внутрь кривой) с целью облегчения при этом сцепляемости вагонов. Такое приспособление в виде Л-образного рычага (торсиона) крепят в кронштейнах на хребтовой балке вагона и соединяют одним плечом с соединительной балкой четырехосной тележки, а другим — с центрирующей балочкой автосцепки.
Железнодорожный подвижной состав должен быть оборудован автосцепкой. Высота оси автосцепки над уровнем верха головок рельсов должна быть:
у локомотивов, пассажирских и грузовых порожних вагонов — не более 1080 мм;
у локомотивов и пассажирских вагонов с людьми — не менее 980 мм;
у грузовых вагонов (груженых) — не менее 950 мм;
у специального подвижного состава:
в порожнем состоянии — не более 1080 мм;
в груженом — не менее 980 мм.
Для железнодорожного подвижного состава, выпускаемого из ремонта, высота оси автосцепки над уровнем верха головок рельсов должна соответствовать нормам и правилам и обеспечена в эксплуатации при наибольших износах и нагрузках. Разница по высоте между продольными осями автосцепок допускается не более:
в грузовом поезде — 100 мм;
между локомотивом и первым груженым вагоном грузового поезда — 110 мм;
в пассажирском поезде ….. до 120 км/ч, — 70 мм;
в пассажирском поезде…… 121 — 140 км/ч, — 50 мм;
между локомотивом и первым вагоном пассажирского поезда — 100 мм;
между локомотивом и подвижными единицами специального подвижного состава — 100 мм.
Автосцепка пассажирских вагонов должна иметь ограничители вертикальных перемещений.Автосцепка специального подвижного состава, работающего по технологии совместно в сцепе, должна иметь ограничитель вертикальных перемещений.
20. Ответственным за техническое состояние автосцепных устройств и правильное сцепление вагонов в составе поезда является осмотрщик вагонов, выполняющий техническое обслуживание состава поезда перед отправлением.При прицепке вагонов к поезду на железнодорожных станциях, где нет осмотрщиков вагонов, а также при маневровой работе ответственным за правильное сцепление вагонов является работник, непосредственно руководящий действиями всех лиц, участвующих в маневрах, без указания которого машинист локомотива, специального самоходного подвижного состава, производящий маневры, не имеет права приводить локомотив, специальный самоходный подвижной состав в движение (далее — руководитель маневров). За правильное сцепление локомотива или специального самоходного подвижного состава, используемого в качестве локомотива, соответственно с первым вагоном поезда или другим специальным подвижным составом ответственным является машинист локомотива или специального самоходного подвижного состава, используемого в качестве локомотива. Отцепка поездного локомотива от состава и прицепка к составу (в том числе разъединение, соединение и подвешивание тормозных рукавов, открытие и закрытие концевых кранов) должны производиться работниками локомотивной бригады. Отцепка поездного локомотива от пассажирского состава, оборудованного электрическим отоплением, производится работником локомотивной бригады, а при обслуживании локомотива одним машинистом — осмотрщиком вагонов только после разъединения поездным электромехаником высоковольтных междувагонных электрических соединителей. Разъединение электрических цепей отопления производится при опущенном токоприемнике. Выполнение операций по прицепке поездного локомотива к железнодорожному составу и отцепке его от железнодорожного состава грузового и пассажирского поезда при обслуживании локомотива одним машинистом возлагается на осмотрщика вагонов, а на железнодорожных станциях, где не предусмотрены осмотрщики вагонов, и на перегонах: в пассажирском поезде — на начальника (механика-бригадира) пассажирского поезда; в грузовом поезде — на машиниста локомотива.
1.4 Автосцепное устройство и его неисправности.
Безопасность на железной дороге реализуется с помощью различных мероприятий и устройств. Надежность вагонов и локомотивов и их безопасное использование во многом зависят от исправности ударно-тяговых приборов — автосцепных устройств.
Исправное автосцепное устройство вагонов обеспечивает:
Любая неисправность автосцепного устройства может привести к порче вагонов и повысить аварийность на железной дороге. Часто встречающиеся последствия несвоевременного ремонта:
Что может сломаться:
К счастью, все поломки и износ можно вовремя заметить и устранить. Для этого на железной дороге регулярно проводят профилактические мероприятия, осматривают составы каждый раз перед тем, как выпустить их на пути. При обнаружения неисправностей автосцепного устройства вагонов можно починить или заменить изношенные части или всю автосцепку целиком.
Автосцепное устройство вагонов состоит из множества элементов, которые могут потребовать замены из-за износа, поломки или некорректной установки.
В процессе эксплуатации могут возникнуть следующие поломки поглощающего аппарата:
Все эти неисправности могут привести к разрыву хомута или всей автосцепки вагона. Это приостановит движение на участке пути на неопределенный срок, что повлияет на весь график движения других составов.
Основные признаки износа:
Такая неисправность автосцепного устройства вагонов очень похожа на трещину в корпусе, поэтому определением причины поломки должны заниматься опытные профессионалы, которые оценят не только яркость блеска на хомуте и хвостовике, но и место сбора клиньев (при износе).
При потере упругости энергоемкость аппарата упадет более чем в 10 раз. Это произойдет потому, что поглощающий аппарат будет работать только на пружинах. Диагностируется выявлением смещения автосцепки внутрь вагона и обратно. В случае подозрений на потерю упругости осматривают упорную плиту — именно она может сломаться при такой неисправности автосцепного устройства вагонов.
Трещина исключает трение при давлении на стенки, заставляя все автосцепное устройство вагонов работать на одних пружинах.
Такая неисправность выявляется с помощью оценки металлического блеска: он должен быть характерно ярким как на хвостовике, так и на хомуте. Благодаря этому методу выявляют:
Основная проблема: при излишнем натяжении цепи валик может расцепиться. Слишком длинная цепь также может повлиять на безопасность движения состава.
Основные виды неисправности корпуса автосцепного устройства вагонов:
При проведении профилактических работ также следят за тем, чтобы в корпусе не было посторонних предметов, а зимой — обледенения.
Механические свойства металла при этом могут несколько различаться для разных деталей. Так, металл корпуса автосцепки и тягового хомута должен иметь предел прочности 52—55 кгс/мм2 при пределе текучести не менее 30 кгс/мм2, относительном удлинении не менее 18% и ударной вязкости при —60° С не менее 2,5 кгс-м/см2. Металл деталей механизма сцепления и деталей, передающих нагрузку на раму вагона, должен иметь предел прочности не менее 45 кгс/мм2, предел текучести не менее 25 кгс/мм2, ударную вязкость при 20° С не менее 5 кгс м/см2 и т. д.
Все перечисленные детали автосцепного устройства подвержены весьма интенсивному износу в эксплуатации, поэтому нуждаются в периодическом ремонте для восстановления изношенных мест наплавкой электродами. По этой причине содержание углерода в стали для них ограничено 0,27%. Если в металле этих деталей углерода содержится более 0,25%, то на них ставят знак в виде буквы С, указывающий на необходимость при заварке дефектов или наплавке изношенных поверхностей подогревать ремонтируемую деталь до температуры 250—300° С.
В качестве материала для деталей поглощающего пружинно-фрикционного аппарата применяют углеродистую сталь с повышенным содержанием углерода или легированную сталь. В конструкции гидравлических, гидропневматических, резинометалли-ческих и других аппаратов помимо сталей используют и другие материалы: бронзу, резину, пластмассы и т. п. Корпус пружинно-фрикционного поглощающего аппарата отливают из стали 32Х06Л или ЗОГСЛ (ГОСТ 977—75) и подвергают закалке и отпуску до твердости НВ 207—277. Клинья и корпус аппарата изготовляют штамповкой из стали 30 (ГОСТ 1050—74) и подвергают нитроце-ментации или цементации с последующей закалкой и отпуском до твердости HRC 50—64. Допускается изготовлять клинья и конусы из стали 38ХС (ГОСТ 4543—71) с закалкой до твердости НВ 341—477. Клин или валик тягового хомута, а также упорную плиту и подвески центрирующего прибора рекомендуется изготовлять штамповкой из стали 38ХС с последующей закалкой и отпуском до твердости НВ 255—321.
В конструкции магистральных вагонов в зависимости от их типа применяют несколько разновидностей автосцепных устройств. Основную разновидность автосцепного устройства (ГОСТ 3475—62) применяют на четырехосных грузовых вагонах. Характерной особенностью этого устройства является применение типовой автосцепки СА-3 и поглощающего аппарата Ш-1-Тм, устанавливаемого в проем между упорами, равный 625 мм. Ход аппарата 70 мм. Корпус автосцепки опирается на центрирующий прибор без подпружинивания (см. рис. 44).
В пассажирских вагонах (в том числе электропоездов и дизель-поездов) применяют автосцепное устройство, отличающееся от предыдущего типом поглощающего аппарата и центрирующего прибора. В этом устройстве применен резинометаллический поглощающий аппарат Р-2П.
В шести- и восьмиосных вагонах применяют так называемое модернизированное автосцепное устройство (рис. 45), которое существенно отличается от автосцепного устройства четырехосных вагонов по конструкции корпуса автосцепки 1, хомута 3, узла 2 соединения корпуса с хомутом и центрирующего прибора 4. Узел соединения корпуса автосцепки с тяговым хомутом выполнен в отличие от соответствующего узла типового автосцепного устройства не с клином, а с валиком и сферическим вкладышем. Модернизированное автосцепное устройство допускает использование поглощающих аппаратов с ходом до 110 мм при стандартном расстоянии между упорами 625 мм. В модернизированном автосцепном устройстве использован центрирующий прибор с подпружиненной опорой для хвостовика автосцепки.
Автосцепные устройства восьмиосных вагонов, имеющих значительную длину консолей, оборудованы специальным приспособлением для принудительного отклонения автосцепки в кривых участках пути (внутрь кривой) с целью облегчения при этом сцепляемости вагонов. Такое приспособление в виде Л-образного рычага (торсиона) крепят в кронштейнах на хребтовой балке вагона и соединяют одним плечом с соединительной балкой четырехосной тележки, а другим — с центрирующей балочкой автосцепки.
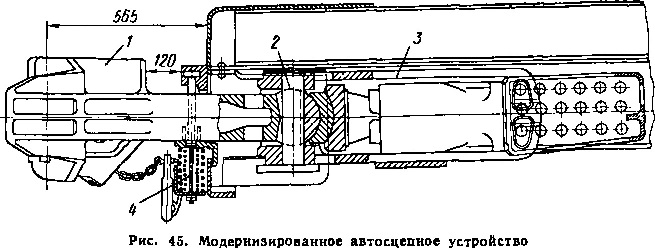
Железнодорожный подвижной состав должен быть оборудован автосцепкой. Высота оси автосцепки над уровнем верха головок рельсов должна быть:
у локомотивов, пассажирских и грузовых порожних вагонов — не более 1080 мм;
у локомотивов и пассажирских вагонов с людьми — не менее 980 мм;
у грузовых вагонов (груженых) — не менее 950 мм;
у специального подвижного состава:
в порожнем состоянии — не более 1080 мм;
в груженом — не менее 980 мм.
Для железнодорожного подвижного состава, выпускаемого из ремонта, высота оси автосцепки над уровнем верха головок рельсов должна соответствовать нормам и правилам и обеспечена в эксплуатации при наибольших износах и нагрузках. Разница по высоте между продольными осями автосцепок допускается не более:
в грузовом поезде — 100 мм;
между локомотивом и первым груженым вагоном грузового поезда — 110 мм;
в пассажирском поезде ….. до 120 км/ч, — 70 мм;
в пассажирском поезде…… 121 — 140 км/ч, — 50 мм;
между локомотивом и первым вагоном пассажирского поезда — 100 мм;
между локомотивом и подвижными единицами специального подвижного состава — 100 мм.
Автосцепка пассажирских вагонов должна иметь ограничители вертикальных перемещений.Автосцепка специального подвижного состава, работающего по технологии совместно в сцепе, должна иметь ограничитель вертикальных перемещений.
20. Ответственным за техническое состояние автосцепных устройств и правильное сцепление вагонов в составе поезда является осмотрщик вагонов, выполняющий техническое обслуживание состава поезда перед отправлением.При прицепке вагонов к поезду на железнодорожных станциях, где нет осмотрщиков вагонов, а также при маневровой работе ответственным за правильное сцепление вагонов является работник, непосредственно руководящий действиями всех лиц, участвующих в маневрах, без указания которого машинист локомотива, специального самоходного подвижного состава, производящий маневры, не имеет права приводить локомотив, специальный самоходный подвижной состав в движение (далее — руководитель маневров). За правильное сцепление локомотива или специального самоходного подвижного состава, используемого в качестве локомотива, соответственно с первым вагоном поезда или другим специальным подвижным составом ответственным является машинист локомотива или специального самоходного подвижного состава, используемого в качестве локомотива. Отцепка поездного локомотива от состава и прицепка к составу (в том числе разъединение, соединение и подвешивание тормозных рукавов, открытие и закрытие концевых кранов) должны производиться работниками локомотивной бригады. Отцепка поездного локомотива от пассажирского состава, оборудованного электрическим отоплением, производится работником локомотивной бригады, а при обслуживании локомотива одним машинистом — осмотрщиком вагонов только после разъединения поездным электромехаником высоковольтных междувагонных электрических соединителей. Разъединение электрических цепей отопления производится при опущенном токоприемнике. Выполнение операций по прицепке поездного локомотива к железнодорожному составу и отцепке его от железнодорожного состава грузового и пассажирского поезда при обслуживании локомотива одним машинистом возлагается на осмотрщика вагонов, а на железнодорожных станциях, где не предусмотрены осмотрщики вагонов, и на перегонах: в пассажирском поезде — на начальника (механика-бригадира) пассажирского поезда; в грузовом поезде — на машиниста локомотива.
1.4 Автосцепное устройство и его неисправности.
Безопасность на железной дороге реализуется с помощью различных мероприятий и устройств. Надежность вагонов и локомотивов и их безопасное использование во многом зависят от исправности ударно-тяговых приборов — автосцепных устройств.
Исправное автосцепное устройство вагонов обеспечивает:
-
свободный проход по кривым участкам пути; -
безопасный проход по горбам сортировочных горок; -
плавный разгон и торможение.
Любая неисправность автосцепного устройства может привести к порче вагонов и повысить аварийность на железной дороге. Часто встречающиеся последствия несвоевременного ремонта:
-
внезапное расцепление; -
неполное сцепление; -
разрыв тягового хомута.
Что может сломаться:
-
предохранитель; -
замок или замкодержатель; -
корпус; -
привод; -
валик подъемника; -
поглощающий аппарат.
К счастью, все поломки и износ можно вовремя заметить и устранить. Для этого на железной дороге регулярно проводят профилактические мероприятия, осматривают составы каждый раз перед тем, как выпустить их на пути. При обнаружения неисправностей автосцепного устройства вагонов можно починить или заменить изношенные части или всю автосцепку целиком.
Виды неисправностей
Автосцепное устройство вагонов состоит из множества элементов, которые могут потребовать замены из-за износа, поломки или некорректной установки.
Поглощающий аппарат
В процессе эксплуатации могут возникнуть следующие поломки поглощающего аппарата:
-
трещины на корпусе; -
износ; -
потеря упругости.
Все эти неисправности могут привести к разрыву хомута или всей автосцепки вагона. Это приостановит движение на участке пути на неопределенный срок, что повлияет на весь график движения других составов.
Износ
Основные признаки износа:
-
нет давления на стенки; -
задействованы исключительно пружины.
Такая неисправность автосцепного устройства вагонов очень похожа на трещину в корпусе, поэтому определением причины поломки должны заниматься опытные профессионалы, которые оценят не только яркость блеска на хомуте и хвостовике, но и место сбора клиньев (при износе).
Потеря упругости
При потере упругости энергоемкость аппарата упадет более чем в 10 раз. Это произойдет потому, что поглощающий аппарат будет работать только на пружинах. Диагностируется выявлением смещения автосцепки внутрь вагона и обратно. В случае подозрений на потерю упругости осматривают упорную плиту — именно она может сломаться при такой неисправности автосцепного устройства вагонов.
Трещины в корпусе
Трещина исключает трение при давлении на стенки, заставляя все автосцепное устройство вагонов работать на одних пружинах.
Такая неисправность выявляется с помощью оценки металлического блеска: он должен быть характерно ярким как на хвостовике, так и на хомуте. Благодаря этому методу выявляют:
-
просадку и деформацию пружин; -
трещину и износ корпуса и клиньев.
Расцепной привод
Основная проблема: при излишнем натяжении цепи валик может расцепиться. Слишком длинная цепь также может повлиять на безопасность движения состава.
Корпус
Основные виды неисправности корпуса автосцепного устройства вагонов:
-
уширение зева; -
износ шипа; -
изгиб полочки.
При проведении профилактических работ также следят за тем, чтобы в корпусе не было посторонних предметов, а зимой — обледенения.