ВУЗ: Не указан
Категория: Не указан
Дисциплина: Не указана
Добавлен: 09.11.2023
Просмотров: 232
Скачиваний: 2
ВНИМАНИЕ! Если данный файл нарушает Ваши авторские права, то обязательно сообщите нам.
Этот вид контроля отличается от других видов неразрушающего контроля границами спектральной области электромагнитного излучения, используемого для получения информации об объекте. Видимое излучение (свет) - излучение, которое может непосредственно вызывать зрительное ощущение. И действительно, визуальный контроль - это единственный неразрушающий метод контроля, который может выполняться и часто выполняется без какого-либо оборудования и проводится с использованием простейших измерительных средств.
Ввиду того, что некоторые технические средства визуального и измерительного контроля доступны каждому, а сама процедура контроля кажется, достаточно простой, предполагают, что проведение контроля этим методом может быть простым и быстрым. Фактически же, визуальный и измерительный контроль является таким же современным сложным видом контроля, как радиационный и ультразвуковой НК.
Главным недостатком данного метода является невозможность обнаружения внутренних дефектов, поэтому целесообразно его использование с другим методом.
Наибольшее применение для обнаружения внутренних дефектов получили методы радиационного и акустического контроля.
Визуальный и измерительный метод контроль – это методов НК для оценки качества продукции, материалов, сырья и т. д. Он характеризуется следующими стадиями технологического процесса:
-
входного контроля; -
изготовления деталей, сборочных единиц и изделий; -
подготовки деталей и сборочных единиц к сборке; -
подготовки деталей и сборочных единиц к сварке; -
сборки деталей и сборочных единиц под сварку; -
процесса сварки; -
контроля готовых сварных соединений и наплавок; -
исправления дефектных участков в материале и сварных соединениях (наплавках); -
оценки состояния материала и сварных соединений в процессе эксплуатации технических устройств и сооружений, в том числе по истечении установленного срока их эксплуатации.
Для технических устройств и сооружений, применяемых и эксплуатируемых на опасных производственных объектах, подконтрольных Ростехнадзору России в настоящее время ВИК проводится в соответствии с «Инструкций по визуальному и измерительному контролю» (РД 03-606-03) (в дальнейшем Инструкция).
Настоящая Инструкция устанавливает порядок проведения визуального и измерительного контроля основного материала (далее — материал) и сварных соединений (наплавок) при изготовлении, строительстве, монтаже, ремонте, реконструкции, эксплуатации, техническом диагностировании (освидетельствовании) технических устройств и сооружений, применяемых и эксплуатируемых на опасных производственных объектах, подконтрольных Росртехнадзору России. В Инструкции приведены обязательные требования к организации и порядку проведения работ, включая требования к подготовке персонала, средствам контроля и фиксации его результатов. Согласно Инструкции специалисты, осуществляющие визуальный и измерительный контроль, должны быть аттестованы в соответствии с Правилами аттестации персонала в области неразрушающего контроля (ПБ 03-440-02). Такие специалисты получают удостоверение установленной формы. Минимальный стаж работы при этом должен быть не менее трех месяцев для аттестации на I уровень и 6 месяцев на II уровень квалификации. Все специалисты осуществляющие работы по ВИК контролю, кроме аттестации должны проходить аттестацию на знание правил, норм и инструкций по безопасному ведению работ на объектах, подконтрольных Ростехнадзору России.
Основные термины и определения при ВИК
Термин | Определение |
ОБЩИЕ ПОНЯТИЯ | |
Визуальный контроль | Органолептический контроль, осуществляемый органами зрения |
Органолептический контроль | Контроль, при котором первичная информация воспринимается органами чувств |
Измерительный контроль | Контроль, осуществляемый с применением средств измерений |
Дефект | Каждое отдельное несоответствие продукции требованиям, установленным нормативной документацией |
Брак | Объект контроля, содержащий недопустимый дефект |
СВАРНЫЕ СОЕДИНЕНИЯ И ШВЫ | |
Сварная конструкция | Металлическая конструкция, изготовленная сваркой отдельных деталей |
Сварной узел | Часть конструкции, в которой сварены примыкающие друг к другу элементы |
Сборочная единица | Часть свариваемого изделия, содержащая один или несколько сварных соединений |
Сварное соединение | Неразъемное соединение деталей, выполненное сваркой и включающее в себя шов и зону термического влияния |
Стыковое соединение | Сварное соединение двух элементов, примыкающих друг к другу торцовыми поверхностями. ![]() |
Угловое соединение | Сварное соединение двух элементов, расположенных под углом и сваренных в месте примыкания их краев. ![]() |
Нахлесточное соединение | Сварное соединение, в котором сваренные элементы расположены параллельно и частично перекрывают друг друга. ![]() |
Тавровое соединение | Сварное соединение, в котором торец одного элемента примыкает под углом и приварен к боковой поверхности другого элемента. ![]() |
Торцовое соединение | Сварное соединение, в котором боковые поверхности сваренных элементов примыкают друг к другу. ![]() |
Сварной шов | Участок сварного соединения, образовавшийся в результате кристаллизации расплавленного металла или в результате пластической деформации при сварке давлением или сочетания кристаллизации и деформации |
Стыковой шов | Сварной шов стыкового соединения |
Угловой шов | Сварной шов углового, нахлесточного или таврового соединения |
Точечный шов | Сварной шов, в котором связь между сваренными частями осуществляется сварными точками |
Непрерывный шов | Сварной шов без промежутков по длине |
Прерывистый шов | Сварной шов с промежутками по длине |
Цепной прерывистый шов | Двухсторонний прерывистый шов, у которого промежутки расположены по обеим сторонам стенки один против другого. ![]() |
Шахматный прерывистый шов | Двухсторонний прерывистый шов, у которого промежутки на одной стороне стенки расположены против сваренных участков шва с другой ее стороны. ![]() |
Многослойный шов | Сварной шов деталей, выполненный в несколько слоев по высоте |
Подварочный шов | Меньшая часть двухстороннего шва, выполняемая предварительно для предотвращения прожогов при последующей сварке или выполняемая в последнюю очередь в корне шва после его зачистки (выборки) |
Корень шва | Часть сварного шва, наиболее удаленная от его лицевой поверхности. ![]() |
Валик | Металл сварного шва, наплавленный или переплавленный за один проход |
Слой сварного шва | Часть металла сварного шва, которая состоит из одного или нескольких валиков, располагающихся на одном уровне поперечного сечения шва |
Прихватка | Короткий сварной шов для фиксации взаимного расположения подлежащих сварке деталей |
Выпуклость сварного шва | Расстояние между плоскостью, проходящей через видимые линии границы сварного шва с основным металлом и поверхностью сварного шва, измеренное в любом поперечном сечении по длине шва (определяется по максимальной высоте расположения поверхности шва под плоскостью). ![]() |
Вогнутость сварного шва | Максимальное расстояние между плоскостью, проходящей через видимые линии границы сварного шва с основным металлом и поверхностью шва, измеренное в любом поперечном сечении по длине шва. ![]() |
Номинальная толщина сваренных деталей | Указанная в чертеже (без учета допусков) толщина основного металла деталей в зоне, примыкающей к сварному шву |
Толщина углового шва | Наибольшее расстояние от поверхности углового шва до точки максимального проплавления основного металла. ![]() |
Расчетная высота углового шва | Указанный в рисунке размер перпендикуляра, опущенного из точки сопряжения сваренных деталей (точка о) на прямую линию, соединяющую края поверхности шва водном поперечном сечении, или на параллельную указанной линии касательную к поверхности сварного шва (при вогнутом угловом шве). ![]() |
Катет углового шва | Кратчайшее расстояние от поверхности одной из свариваемых частей до границы углового шва на поверхности второй свариваемой части. ![]() |
Ширина сварного шва | Расстояние между линиями сплавления на лицевой стороне сварного шва в одном поперечном сечении. ![]() |
Основной металл | Металл деталей, соединяемых сваркой |
Разделка кромки | Придание кромкам деталей, подлежащих сварке, необходимой формы |
Скос кромок | Прямолинейный наклонный срез кромки детали, подлежащей сварке. ![]() |
Притупление кромки | Нескошенная часть торца кромки детали, подлежащей сварке. ![]() |
Угол скоса кромки | Острый угол между плоскостью скоса кромки и плоскостью торца детали или торцовая поверхность детали после механической обработки до заданных чертежом размеров. ![]() |
Угол разделки кромок | Угол между скошенными кромками свариваемых деталей. ![]() |
Смешение кромок | Несовпадение уровней расположения внутренних и наружных поверхностей свариваемых (сваренных) деталей в стыковых сварных соединениях. ![]() |
Зазор в соединении | Расстояние между собранными под сварку деталями в поперечном сечении их кромок. ![]() |
Конструктивный непровар (зазор) | Непровар (зазор) в сварном соединении, предусмотренный конструкторской документацией на сварной узел. ![]() |
Подкладка. Остающаяся подкладная пластина (кольцо) | Стальная пластина или кольцо заданной формы, ширины и толщины, устанавливаемое при сварке плавлением под кромки свариваемых деталей. ![]() |
Расплавляемая вставка | Стальная проволочная вставка заданной формы, ширины и толщины, устанавливаемая между кромками свариваемых деталей и расплавляемая при сварке. ![]() |
Провар | Сплошная металлическая связь между поверхностями основного металла, слоями и валиками сварного шва |
Зона сплавления при сварке. Зона сплавления | Зона частично оплавившихся зерен на границе основного металла и металла шва |
Зона термического влияния при сварке. Зона термического влияния | Участок основного металла от линии сплавления до зоны, в которой происходит изменение структуры и свойств металла в результате нагрева при сварке или наплавке |
ВИК подразделяется на следующие стадии технологического процесса:
-
Визуальный и измерительный контроль материалов на стадии входного контроля выполняют при поступлении материала (полуфабрикатов, заготовок, деталей) в организацию с целью подтверждения его соответствия требованиям стандартов, технических условий (далее — ТУ), конструкторской документации и Правил. Проводят данный контроль с целью выявления деформаций, поверхностных трещин, расслоений, закатов, забоин, рисок, раковин и других несплошностей; проверки геометрических размеров заготовок, полуфабрикатов и деталей; проверки допустимости выявленных деформаций и поверхностных несплошностей. -
Визуальный и измерительный контроль изготовления деталей и сборочных единиц, подготовки их к сборке и сварке выполняют с целью подтверждения соответствия качества их изготовления и подготовки требованиям рабочих чертежей, технологии изготовления (технологии сборки, гиба) и прочей производственно-технологической документации (далее — ПТД), требованиям нормативной технической документации (далее — НД), ТУ на изготовление и Правил. Проводят данный контроль с целью выявления и проверки обеспечения допустимых размеров зазоров, смещений кромок, формы и размеров кромок и геометрического положения (излома или перпендикулярности) осей и поверхностей собранных элементов. -
Визуальный и измерительный контроль качества сварных соединений и наплавок в процессе сварки (наплавки) и готового сварного соединения или наплавки выполняют с целью подтверждения их соответствия требованиям конструкторской документации, ПТД и (или) НД и Правил. Проводят данный контроль с целью выявления деформаций, поверхностных трещин, подрезов, прожогов, наплывов, кратеров, свищей, пор, раковин и других несплошностей и дефектов формы швов; проверки геометрических размеров сварных швов и допустимости выявленных деформаций, поверхностных несплошностей и дефектов формы сварных швов. -
Визуальный и измерительный контроль качества исправления дефектных участков в материале, сварных соединениях и наплавках выполняют с целью подтверждения полноты удаления дефекта, проверки соответствия формы и размеров выборки дефектного участка и качества заварки выборок (в случаях, когда выборка подлежит заварке) требованиям ПТД, НД и Правил. -
Визуальный и измерительный контроль технических устройств и сооружений в процессе эксплуатации проводят с целью выявления изменений их формы, поверхностных дефектов в материале и сварных соединениях (наплавках), образовавшихся в процессе эксплуатации (трещин, коррозионных и эрозионных повреждений, деформаций и пр.).
ВИК контроль выполняют в соответствии с требованиями Технологической карты контроля и Карт (схем) операционного контроля.
В указанных картах приводятся контролируемые параметры, последовательность контроля, объемы контроля, средства контроля, схемы выполнения замеров контролируемых параметров и нормы оценки результатов контроля. Технологические карты и карты операционного контроля разрабатываются организацией, выполняющей контроль, либо специализированной организацией, выполняющей проектно-технологическую подготовку производства работ по контролю.
ВИК контроль проводят невооруженным глазом и (или) с применением визуально-оптических приборов до 20-кратного увеличения (луп, микроскопов, эндоскопов, зеркал и др.). При контроле материала и сварных соединений и наплавок используют лупы с 2–7-кратным увеличением, а при оценке состояния технических устройств и сооружений в процессе их эксплуатации — лупы до 20-кратного увеличения. Существует универсальный набор ВИК рис 6.1 он состоит из следующих компонентов:
-
Универсальный шаблон сварщика УШС-3 предназначен для контроля элементов разделки под сварной шов, электродов и элементов сварного шва. -
Лупа ЛП-3,5 с подсветкой для просмотра деталей, мелких предметов. -
Лупа ЛП-7 асферическая для просмотра деталей, мелких предметов и т.д. -
Лупа ЛП-4 складная для просмотра деталей, мелких предметов и т.д. -
Лупа измерительная ЛИ-10 (десятикратная) для измерения линейных размеров плоских предметов с помощью шкалы, выполненной на стеклянной пластине. -
Штангенциркуль ШЦ-1-125-0,1 с глубиномером. -
Линейка металлическая Л-150. -
Набор радиусных шаблонов для оценки радиусов выпуклых и вогнутых поверхностей № 1 (R=1 ...6мм) и № 3 (R=7...25мм) . -
Набор щупов для контроля зазоров № 4 (0.1 ...1мм). -
Угольник металлический 160х250 мм Угол-90. -
Фонарик миниатюрный.
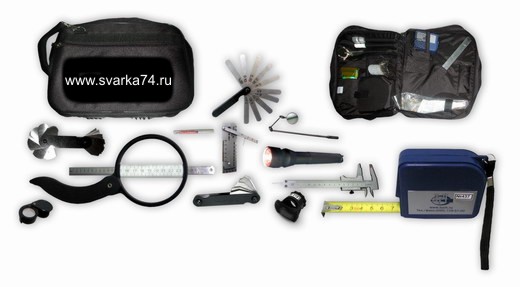
Рис. 6.1 Набор ВИК.
Для осуществления ВИК в труднодоступных местах используют жесткие и гибкие эндоскопы, зеркальные зонды, смотровые устройства с освещением, бинокулярные лупы, а также рабочие станции с визуализацией на экране ноутбука по средствам видеозахвата изображений с последуещей архивировацией изображений на ноутбуке, а также с возможностью созданием отчетов с распечаткой изображения на принтер.
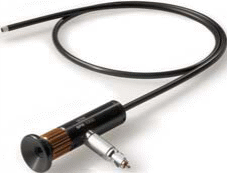
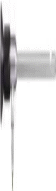
Рис 6.2. Гибкий и жесткий эндоскоп
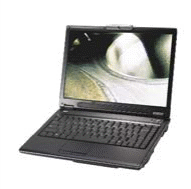
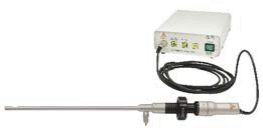

1 2 3
Рис 6.3. Пример рабочий станции:
1. Ноутбук с USB устройством для видеозахвата изображений;
2. Жесткий или гибкий эндоскоп с камерой A-Cam с адаптером;
3. Видеопринтер. Публикация с последующим предоставлением документа о повреждениях
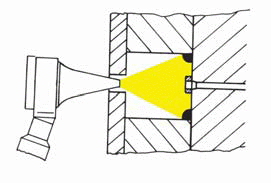
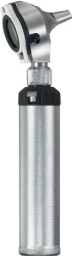
Рис. 6.4. Смотровые зонды
ВИК контроль выполняют до проведения контроля другими методами, а также после устранения дефектов.
Поверхности материалов и сварных соединений (наплавок) перед контролем очищаются от влаги, шлака, брызг металла, ржавчины и других загрязнений, препятствующих проведению контроля.
Дефекты, выявленные при ВИК контроле, должны быть устранены до выполнения последующей технологической операции или до приемки объекта контроля. Устранение выявленных дефектов должно выполняться в соответствии с требованиями ПТД. Если дефекты, выявленные при визуальном и измерительном контроле, не препятствуют дальнейшему применению других видов (методов) неразрушающего контроля, эти дефекты могут быть устранены после завершения контроля другими видами (методами) контроля.
Измерения проводят после визуального контроля или одновременно с ним. Измерения деталей, подготовленных под сварку, проводятся до их сборки.
При подготовке деталей под сварку необходимо контролировать:
-
наличие маркировки и документации, подтверждающей приемку полуфабрикатов, деталей, сборочных единиц и изделий при входном контроле; -
наличие маркировки изготовителя материала на деталях, подготовленных под сварку; -
наличие удаления механическим путем зоны термического влияния в месте термической резки заготовок; -
геометрическую форму обработанных кромок; -
геометрическую форму обработанных внутренних поверхностей кольцевых деталей; -
форму подкладных пластин (колец) и расплавляемых вставок; -
наличие заварки разъема подкладной пластины (кольца), качество шва заварки подкладной пластины (кольца), а также наличие зачистки шва заварки разъема подкладной пластины (кольца); -
отсутствие визуально наблюдаемых загрязнений, пыли, продуктов коррозии, влаги, масла и. т.п. в зоне подлежащей сварке (наплавке) кромок и прилегающих к ним поверхностей, а также подлежащих неразрушающему контролю участков материала.