ВУЗ: Не указан
Категория: Не указан
Дисциплина: Не указана
Добавлен: 09.11.2023
Просмотров: 234
Скачиваний: 2
ВНИМАНИЕ! Если данный файл нарушает Ваши авторские права, то обязательно сообщите нам.
Оценку качества материала изготовленных деталей, подготовки кромок деталей, сборки деталей под сварку, выполненного сварного соединения (наплавки) и конструкций в целом, швов заварки дефектных участков по результатам визуального и измерительного контроля проводят по нормам, согласованным с нормативной документацией.
Результаты визуального и измерительного контроля фиксируются в журнале учета работ по визуальному и измерительному контролю с оформлением актов, заключений, протоколов согластно Инструкции (РД 03-606-03) .
В случаях, предусмотренных технологической документацией, на поверхности проконтролированных материалов и готовых сварных соединений контролером по завершении каждого этапа работ по визуальному и измерительному контролю ставится клеймо, подтверждающее положительные результаты контроля.
Дефекты сварных соединений и поверхности основного материала приведены ниже в таблице.
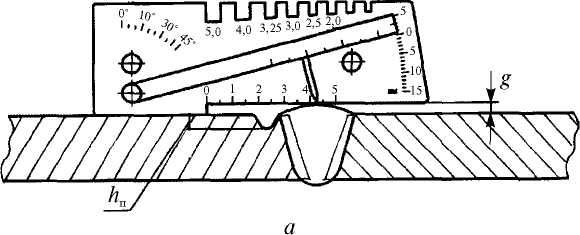
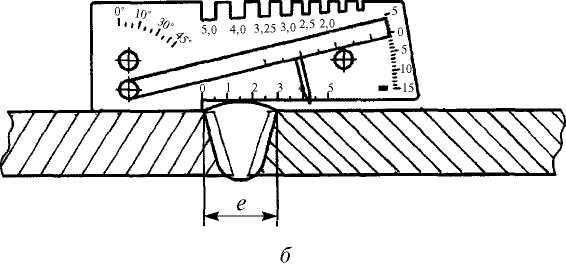
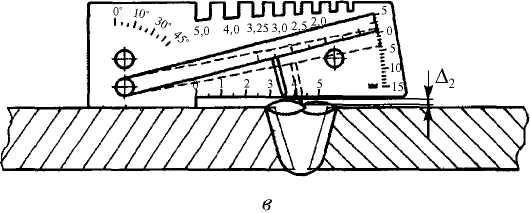
Рис. 16. Измерения с помощью шаблона УШС размеров сварного шва:
а — измерение высоты шва (g) и глубины подреза (hп); б — измерение
ширины шва (e); в — измерение западаний между валиками (Л )
Термины | Определения | |
ДЕФЕКТЫ СВАРНЫХ СОЕДИНЕНИЙ ПРИ ВИЗУАЛЬНОМ И ИЗМЕРИТЕЛЬНОМ КОНТРОЛЕ | ||
Несплошность | Обобщенное наименование трещин, отслоений, прожогов, свищей, пор, непроваров и включений. | |
Трещина сварного соединения. Трещина | Дефект сварного соединения в виде разрыва металла в сварном шве и (или) прилегающих к нему зонах сварного соединения и основного металла | |
Продольная трещина сварного соединения. Продольная трещина | Трещина сварного соединения, ориентированная вдоль оси сварного шва. ![]() | |
Поперечная трещина сварного соединения. Поперечная трещина | Трещина сварного соединения, ориентированная поперек оси сварного шва. ![]() | |
Разветвленная трещина сварного соединения. Разветвленная трещина | Трещина сварного соединения, имеющая ответвления в различных направлениях, или группа соединенных трещин, отходящих от одной общей трещины. ![]() | |
Радиальная трещина | Несколько трещин разного направления, исходящих из одной точки (могут располагаться в металле сварного шва, в зоне термического влияния, в основном металле) Примечание. Маленькие трещины этого типа известны как звездообразные трещины. ![]() | |
Кратерная трещина. Трещина в кратере | Трещина (продольная, поперечная, разветвленная) в кратере валика (слоя) сварного шва. ![]() | |
Включение | Полость в металле, заполненная газом, шлаком или инородным металлом; обобщенное наименование пор, шлаковых и вольфрамовых включений | |
Шлаковое включение сварного шва. Шлаковое включение | Полость в металле, в том числе сварном шве, заполненная шлаком | |
Флюсовое включение | Полость в металле сварного шва, заполненная нерасплавившимся флюсом, попавшим в металл шва во время затвердевания | |
Вольфрамовое включение | Внедрившаяся в металл шва нерасплавленная частица (осколок) неплавящегося вольфрамового электрода | |
Окисное включение | Окисел металла, попавший в металл шва во время затвердевания | |
Пора | Заполненная газом полость округлой формы | |
Отслоение | Дефект в виде нарушения сплошности сплавления наплавленного металла с основным металлом. ![]() | |
Кратер. Усадочная раковина сварного шва | Дефект в виде полости или впадины, образовавшийся при усадке расплавленного металла при затвердевании (располагается, как правило, в местах обрыва дуги или окончания сварки). ![]() | |
Свищ в сварном шве | Дефект в виде воронкообразного или трубчатого углубления в сварном шве. Примечание. Обычно свищи группируются в скопления и распределяются елочкой ![]() | |
Подрез | Острые конусообразные углубления на границе поверхности сварного шва с основным металлом. ![]() | |
Брызги металла | Дефект в виде затвердевших капель расплавленного металла на поверхности сваренных или наплавленных деталей с образованием или без образования кристаллической связи с основным металлом | |
Непровар. Неполный провар | Дефект в виде несплавления в сварном соединении вследствие неполного расплавления кромок основного металла или поверхностей ранее выполненных валиков сварного шва. ![]() | |
Углубление (западание) между валиками шва | Продольная впадина между двумя соседними валиками (слоями) шва (оценивается по максимальной глубине). ![]() | |
Чешуйчатость сварного шва | Поперечные или округлые (при автоматической сварке под флюсом - удлиненно-округлые) углубления на поверхности валика, образовавшиеся вследствие неравномерности затвердевания металла сварочной ванны (оценивается по максимальной глубине). ![]() | |
Выпуклость (превышение проплавления) корня шва | Часть одностороннего сварного шва со стороны его корня, выступающая над уровнем расположения поверхностей сваренных деталей (оценивается по максимальной высоте расположения поверхности корня шва над указанным уровнем). ![]() | |
Вогнутость корня шва | Дефект в виде углубления на поверхности обратной стороны сварного одностороннего шва (оценивается по максимальной глубине расположения поверхности корня шва от уровня расположения поверхностей сваренных деталей). ![]() | |
Максимальный размер включения Максимальная ширина включения | Наибольшее расстояние а между точками внешнего контура включения. Наибольшее расстояние b между двумя точками внешнего контура включения, измеренное в направлении, перпендикулярном максимальному размеру включения. ![]() | |
Включение одиночное | Включение, минимальное расстояние l от края которого до края любого соседнего включения - не менее максимальной ширины каждого из двух рассматриваемых включений, но не менее трехкратного максимального размера включения с меньшим значением этого показателя (из двух рассматриваемых). ![]() | |
Скопление включений | Два или несколько включений (пор, шлаковых и прочих включений), минимальное расстояние между краями которых менее установленных для одиночных включений, но не менее максимальной ширины каждого из любых двух рассматриваемых соседних включений. ![]() | |
Цепочка пор. Линейная пористость | Группа пор в сварном шве, расположенная в линию, параллельно оси сварного шва. ![]() | |
Превышение усиления сварного шва | Избыток наплавленного металла на лицевой стороне (сторонах) стыкового шва. ![]() Правильно Неправильно | |
Превышение выпуклости | Избыток наплавленного металла на лицевой стороне углового шва. ![]() | |
Местное превышение проплава | Местный избыточный проплав (с внутренней стороны одностороннего шва) | |
Неправильный профиль сварного шва | Слишком малый угол (а) между поверхностью основного металла и плоскостью касательной к поверхности сварного шва. ![]() Правильно Неправильно | |
Наплыв | Дефект в виде металла, натекшего в процессе сварки (наплавки) на поверхность сваренных (наплавленных) деталей или ранее выполненных валиков и несплавившегося с ними. ![]() | |
Перелом осей деталей. Угловое смешение | Смешение между двумя свариваемыми деталями, при котором их плоские поверхности непараллельны (или не направлены под определенным углом). ![]() | |
Прожог сварного шва | Дефект в виде сквозного отверстия в сварном шве, образовавшийся вследствие вытекания части жидкого металла сварочной ванны в процессе выполнения сварки | |
Не полностью заполненная разделка кромок | Продольная непрерывная или прерывистая вогнутость на поверхности сварного шва из-за недостаточности присадочного металла. ![]() | |
Асимметрия углового шва | Несоответствие фактического значения катета шва проектному значению. ![]() | |
Неравномерная ширина шва | Чрезмерное колебание ширины шва | |
Неравномерная поверхность шва | Чрезмерная неровность наружной поверхности шва | |
Плохое возобновление шва | Местная неровность поверхности в месте возобновления сварки. ![]() | |
ДЕФЕКТЫ ПОВЕРХНОСТИ ОСНОВНОГО МЕТАЛЛА | ||
Случайное оплавление основного металла в результате зажигания или гашения дуги | Местное повреждение поверхности основного металла, примыкающего к сварному шву, возникшее в результате случайного и (или) преднамеренного возбуждения дуги вне разделки соединения | |
Задир поверхности основного металла | Повреждение поверхности, вызванное удалением путем отрыва временного технологического крепления | |
Утонение металла | Уменьшение толщины металла вследствие чрезмерного его удаления при обработке абразивным инструментом | |
Остатки поджога от резки | Темное пятно, отличающееся по травимости от основного металла, или углубление, частично заполненное расплавленным металлом и шлаком, образовавшееся при резке на анодно-механических станках | |
Дефект рубки металла | Трещины или рваные вязкие изломы | |
Пузыри в поверхностных слоях металла | Полости, имеющие в поперечном сечении округлую форму, а в продольном сечении - форму капсулы, ориентированной перпендикулярно оси слитка. При выходе пузырей на поверхность слитка имеют вид отверстий округлой формы | |
Завороты корки | Завернувшиеся корки металла, окислившиеся заливины и брызги, расположенные у поверхности слитков. В деформированном металле дефект представляет собой или разрывы, или частичное отслоение, образовавшееся в результате раскатки завернувшихся корок или брызг | |
Загрязнения и волосовины | Загрязнения поверхности слитков, прутков и других изделий неметаллическими включениями (шлаком, огнеупорами, утепляющими смесями, оксидами и др.). Имеют вид пристывших или частично залитых металлом кусков или мелких частиц светло-серого, темно-серого или коричневого цвета | |
Трещины горячие (кристаллизационные) | Извилистый окисленный разрыв металла, более широкий у поверхности и сужающийся вглубь, образовавшийся в период кристаллизации металла вследствие растягивающихся напряжений, превышающих прочность наружных слоев слитка | |
Дефект от вдавливания в слиток кернов клещей крана | Углубления на блюмах и слябах, образовавшиеся от вдавливания острых кернов клещей крана в горячие слитки при их транспортировке. По виду дефект напоминает единичную чечевицеобразную, широко открытую, сравнительно короткую трещину | |
Трещина напряжения | Направленный в глубь металла разрыв, часто под прямым углом к поверхности, образовавшийся вследствие объемных изменений, связанных со структурными превращениями или с нагревом и охлаждением металла | |
Трещина шлифовочная | Сетка паутинообразных разрывов или отдельных произвольно направленных поверхностных разрывов, образовавшихся при шлифовке металла. Очень тонкие, извилистые и проникающие в глубь металла зигзагами или ступеньками с ответвлениями | |
Трещины травильные | Разрывы, образовавшиеся при травлении металла с внутренними напряжениями, вызванными структурными превращениями или деформацией. Травильные трещины иногда образуют поверхностную сетку, подобную сетке шлифовочных трещин, но значительно более грубую | |
Рванины | Раскрытые разрывы, расположенные перпендикулярно или под углом к направлению наибольшей вытяжки металла | |
Прокатные плены | Отслоения металла языкообразной формы, соединенные с основным металлом и образованные вследствие раскатки или расковки рванин | |
Чешуйчатость | Отслоения или разрывы в виде сетки, образовавшиеся при прокатке из-за перегрева (пережога) или пониженной пластичности металла периферийной зоны | |
Прижоги | Дефекты, образующиеся при локальном перегреве металла (шлифование, электрохимическое клеймение, спектральный анализ и др.), являющиеся структурными концетраторами напряжений, в зоне которых может возникнуть растрескивание | |
Ус | Продольный выступ с одной стороны прутка или с двух диаметрально противоположных его сторон | |
Подрез | Продольное углубление по всей длине прутка или на отдельных участках его поверхности, образовавшееся из-за неправильной настройки валковой арматуры или одностороннего перекрытия калибра. Прокатный подрез может иметь волнистый или зазубренный край | |
Морщины | Группа чередующихся продольных углублений и выступов | |
Риска | Прямоугольное продольное углубление с закругленным или плоским дном, образовавшееся из-за царапания поверхности металла наварами и другими выступами | |
Отпечатки | Углубления или выступы, расположенные по всей поверхности металла или на отдельных его участках | |
Рябизна | Углубление от вдавленной окалины, образовавшееся при ковке, прокатке или правке металла с толстым слоем окалины | |
Заусенец | Острый в виде гребня выступ на конце прутка, образовавшийся при резке металла | |
Остатки окалины | Окалина, не удаленная с отдельных участков прутков | |
Перетрав | Местное или общее разъедание поверхности металла при травлении | |
Царапина | Канавка неправильной формы и произвольного направления, образовавшаяся в результате механических повреждений, в том числе при складировании и транспортировке металла | |
Раковины от вдавленной окалины | Отдельные углубления, иногда частично вытянутые вдоль направления прокатки, образующиеся при выпадании и вытравливании вкатанной окалины | |
Вкатанный кусок металла | Приварившийся кусок инородного металла к металлу основного материала |
1 ... 5 6 7 8 9 10 11 12 13
25. РАДИАЦИОННЫЙ КОНТРОЛЬ СВАРНЫХ СОЕДИНЕНИЙ
Радиационный неразрушающий контроль - это вид неразрушающего контроля, основанный на регистрации и анализе ионизирующего излучения после его взаимодействия с объектом контроля. Этот вид контроля играл и продолжает играть важную роль при определении качества материалов и изделий и поиске оружия и взрывных устройств в тех или иных конкретных ситуациях.
Это один из старейших и достаточно универсальных видов неразрушающего контроля. Кроме того, различные радиационные методы хорошо разработаны и подробно описаны в стандартах, справочниках и монографиях.
Радиационный неразрушающий контроль в основном использует фотонное, нейтронное и электронное излучения.
Он активно применяется при контроле:
-
качества материалов (выявление дефектов в слитках, литых изделиях, сварных и паяных соединениях); -
качества функционирования узлов и механизмов; -
контейнеров, багажа, почтовых отправлений (выявление оружия, недозволенных вложений); -
продуктов (выявление инородных тел); -
произведений искусства (обнаружение подделок); -
в судебной практике (обнаружение подделок); -
в научных исследованиях (регистрация быстро протекающих процессов, физических явлений в непрозрачных средах); -
в сельском хозяйстве (определение качества посевного материала, регистрация распределения зерен при посеве).
В данном разделе мы рассмотрим радиационный контроль сварных соединений.
Радиационный неразрушающий контроль представляет собой обязательное использование трех основных элементов:
-
источника ионизирующего излучения, -
объекта контроля, -
устройства, регистрирующего дефектоскопическую информацию (детектора).
Сущность радиационных методов контроля заключается в просвечивании объекта контроля ионизирующим излучением и фиксирование выходящего пучка на детектор. Ионизирующее излучение, проходя через изделие (вещество), взаимодействует с атомными ядрами и электронными оболочками, поглощаясь и рассеиваясь, и вследствие этого испытывает ослабление. При этом у каждого вещества своя степень поглощения и ослабления излучения. Наличие в объекте контроля дефектов приводит к резкому изменению энергии или интенсивности излучения выходящего пучка. Поэтому зафиксированный детектором пучок излучения несет в себе информацию о наличии и размерах дефектов (рис. 6.5). Степень ослабления зависит от толщины и плотности


где




Рис. 6.5. Схема контроля радиационными методами с картиной распределения интенсивности рентгеновского излучения. 1 – Источник рентгеновского излучения; 2 – Контролируемый образец (сварной шов, металл); 3 – Дефект (пора, шлаковые включения, наличие воздушной прослойки); 4 – Дефект (включение вольфрама,); 5 – Подрез; 6 – Рентгеновская пленка
Методы радиационного контроля различают по детекторам и источникам ионизирующих излучений. По детекторам радиационные методы контроля подразделяют на:
-
радиографический, -
радиоскопический, -
радиометрический.
Радиографические методы радиационного неразрушающего контроля основаны на преобразовании радиационного изображения контролируемого объекта в радиографический снимок или запись этого изображения на запоминающем устройстве с последующим преобразованием в световое изображение. На практике этот метод наиболее широко распространен в связи с его простотой и документным подтверждением полученных результатов. В зависимости от используемых детекторов различают пленочную радиографию и ксерора-диографию (электрорадиографию). В первом случае детектором скрытого изображения и регистратором статического видимого изображения служит фоточувствительная пленка, во втором - полупроводниковая пластина, а в качестве регистратора используют обычную бумагу.
В зависимости от используемого излучения различают несколько разновидностей промышленной радиографии: рентгенографию, гамма-графию, ускорительную и нейтронную радиографию. Каждый из перечисленных методов имеет свою сферу использования. Этими методами можно просвечивать стальные изделия толщиной 1.. .700 мм.
Радиоскопический метод (радиационная интроскопия) - метод основанный на преобразовании радиационного изображения контролируемого объекта в световое изображение на выходном экране радиационно-оптического преобразователя, причем полученное изображение анализируется в процессе контроля.
Чувствительность этого метода несколько меньше, чем радиографии, но его преимуществами являются повышенная достоверность получаемых результатов благодаря возможности стереоскопического видения дефектов и рассмотрения изделий под разными углами; экспрессность и непрерывность контроля.
Радиометрическая дефектоскопия - метод получения информации о внутреннем состоянии контролируемого изделия, просвечиваемого ионизирующим излучением, в виде электрических сигналов (различных величины, длительности или количества).
Этот метод обеспечивает наибольшие возможности автоматизации процесса контроля и осуществления автоматической обратной связи контроля и технологического процесса изготовления изделия. Преимуществом метода является возможность непрерывного высокопроизводительного контроля качества изделия, обусловленная высоким быстродействием применения аппаратуры. По чувствительности этот метод не уступает радиографии.
По источникам ионизирующих излучений радиационные методы контроля различают на:
-
рентгеновские - генерирующие рентгеновское излучение; -
гамма методы - при которых генерируются радиоизотопными источниками гамма излучения; -
методы, в которых применяют специальные ускорители электронов для получения рентгеновского излучения большой мощности.
Имеются и другие источники ионизирующих излучений, которые не нашли широкого применения в дефектоскопии.
Физические основы метода.
Рентгеновское и гамма-излучения (



В связи с вышеперечисленным, обладая большой энергией, рентгеновское и -излучение легко проникают через металл, теряя при этом часть энергии в зависимости от толщины и плотности этого металла.
Рентгеновские лучи возникают тогда, когда поток быстролетящих электронов встречает на своем пути материю. При резком торможении часть энергии летящих электронов переходит в энергию рентгеновских лучей. Все эти процессы осуществляются в специальных вакуумных приборах, называемых рентгеновскими трубками.
В современной рентгенотехнике используются высоковакуумные (порядка

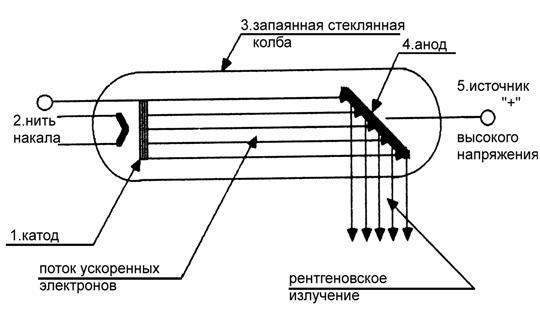
Рис. 2.1. Схема рентгеновской трубки: 1 – катод; 2 – нить накала катода; 3 – стеклянный колба; 4 – анод; 5 – источник высокого напряжения
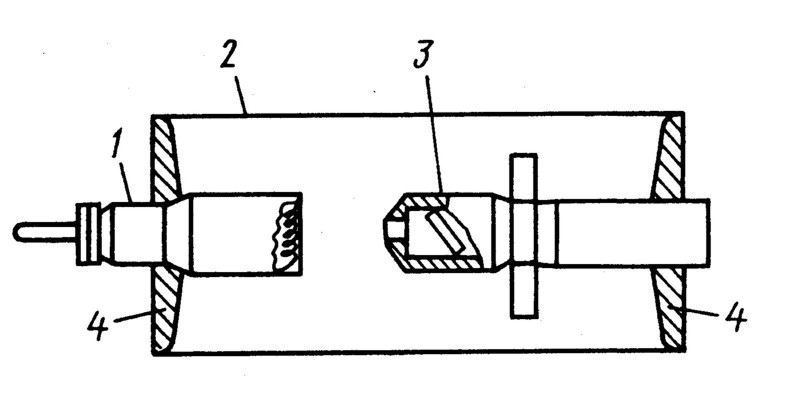
Рис. 2.2. Схема металлокерамической рентгеновской трубки:
1 – катодный узел; 2 – металлический цилиндр; 3 – анодный узел; 4 – керамический диски
Катодный узел (катод) включает вольфрамовую нить накала, закрученную, как правило, в спираль и окруженную металлическим электродом, создающим вокруг нее такую конфигурацию электрического поля, при которой электроны, выходящие из катода, движутся к аноду в виде узкого электронного пучка. Нить обычно питается переменным током (50 Гц) от отдельного регулируемого трансформатора. Ток нити накала находится в пределах 1 ... 10 А. Ток трубки лежит в диапазоне несколько десятков микроампер, у микрофокусных трубок - до 20 мА.