ВУЗ: Не указан
Категория: Не указан
Дисциплина: Не указана
Добавлен: 09.11.2023
Просмотров: 231
Скачиваний: 2
ВНИМАНИЕ! Если данный файл нарушает Ваши авторские права, то обязательно сообщите нам.
При сборке деталей под сварку визуально необходимо контролировать:
-
правильность установки подкладных пластин (колец); -
правильность установки временных технологических креплений; -
правильность сборки и крепления деталей в сборочных приспособлениях; -
правильность расположения и количество прихваток и их качество; -
правильность установки приспособлений для поддува защитного газа; -
правильность нанесения активирующего флюса и защитной флюс-пасты; -
наличие защитного покрытия от брызг расплавленного металла на поверхности деталей из аустенитных сталей, свариваемых ручной дуговой и полуавтоматической (автоматической) сваркой плавящимся электродом в среде защитного газа; -
чистоту кромок и прилегающих к ним поверхностей деталей.
Контролируемые параметры при измерительном контроле при подготовке деталей под сварку приведены на Рис. 6.2.
Контролируемые параметры при измерительном контроле соединений, собранных под сварку приведены Рис. 6.3.
Визуальному и измерительному контролю подготовки и сборки деталей под сварку подлежат не менее 20 % деталей и соединений из числа представленных к приемке.
Объем выборочного контроля качества подготовки и сборки деталей под сварку может быть увеличен или уменьшен в зависимости от требований НД, ПТД и ПКД или по требованию Заказчика.
При выявлении отклонений от требований рабочих чертежей и (или) ПТД, которые могут привести к ухудшению качества сварных соединений, объем выборочного контроля должен быть увеличен вдвое для группы однотипных деталей (соединений). Если при дополнительном контроле вторично будут выявлены отклонения оттребований конструкторской документации и (или) ПТД, то объем контроля для группы деталей, подготовленных к приемке, должен быть увеличен до 100 %.
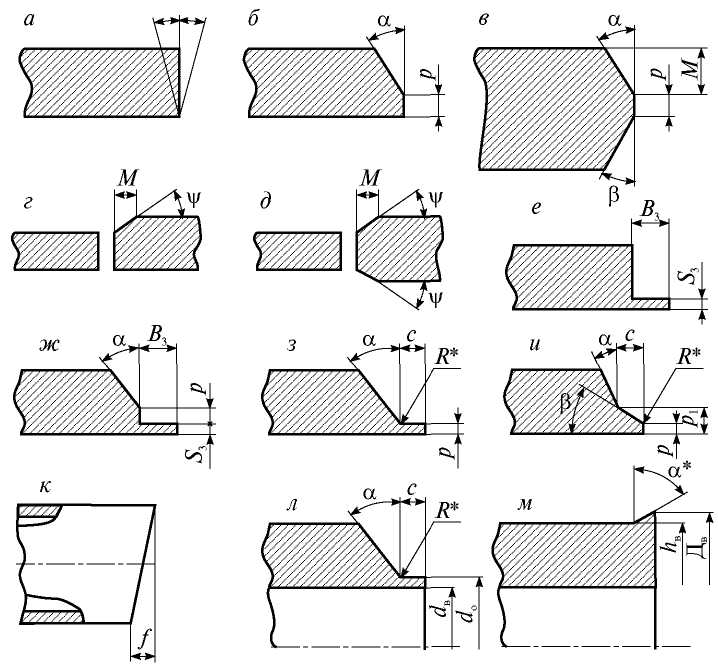
* Размер измерению не подлежит, обеспечивается режущим инструментом и оценивается визуально.
Рис. 6.2. Размеры, контролируемые измерением
при подготовке деталей под сварку (начало):
а — I-образная разделка кромки (без скоса кромки); б — V-образная односторонняя разделка кромки; в — V-образная двухсторонняя разделка кромки; г, д — подготовка к сварке стыкового соединения деталей, значительно отличающихся по толщине; е, ж — подготовка к сварке замкового соединения
; з — У-образная разделка кромки;
и — V-образная двухскосная разделка кромки; к — отклонение от перпендикулярности торца трубы; л — подготовка кромок штуцера
Ду 10–65; м — I-образная разделка с присадочным выступом
Детали, забракованные при контроле, подлежат исправлению. Собранные под сварку соединения деталей, забракованные при контроле, подлежат разборке с последующей повторной сборкой после устранения причин, вызвавших их первоначальную некачественную сборку.
Визуальный контроль удаления материала, подвергнутого термическому влиянию во время резки термическими способами (газовая, воздушно-дуговая, газофлюсовая, плазменная и др.), проводится на каждой детали, подвергавшейся резке.
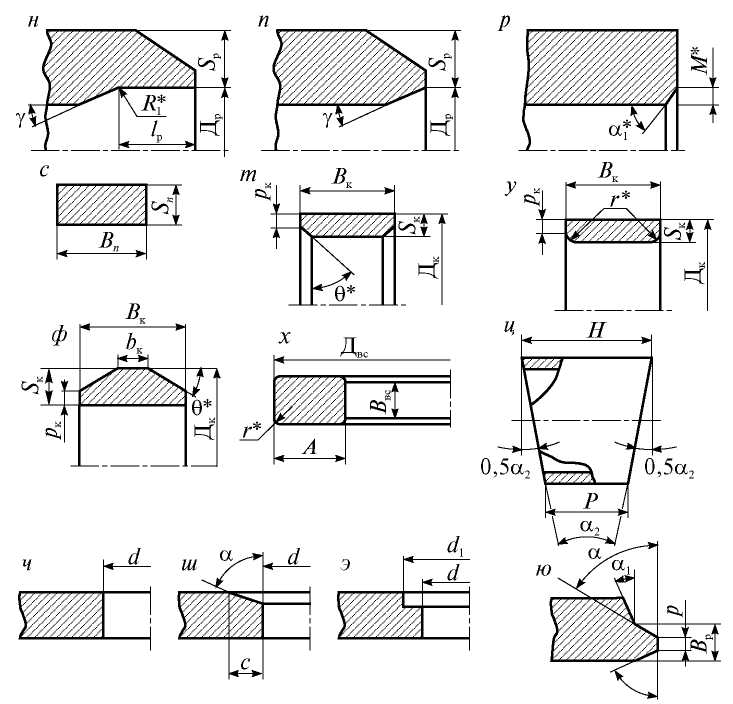
* Размер измерению не подлежит, обеспечивается режущим инструментом и оценивается визуально.
Рис. 6.2. Окончание:
н — цилиндрическая расточка (раздача) концов труб по внутреннему диаметру; п — коническая расточка труб по внутреннему диаметру; р — притупление
внутренней кромки трубы; с — подкладная остающаяся пластина;
т,у — подкладное стальное остающееся кольцо; ф — подкладное стальное
остающееся кольцо; х — расплавляемая проволочная вставка; ц — сектор
отвода; ч,ш,э — рассверловка отверстия под штуцер (патрубок) в корпусе
(трубе, коллекторе); ю — разделка кромок под автоматическую сварку в среде
защитных газов
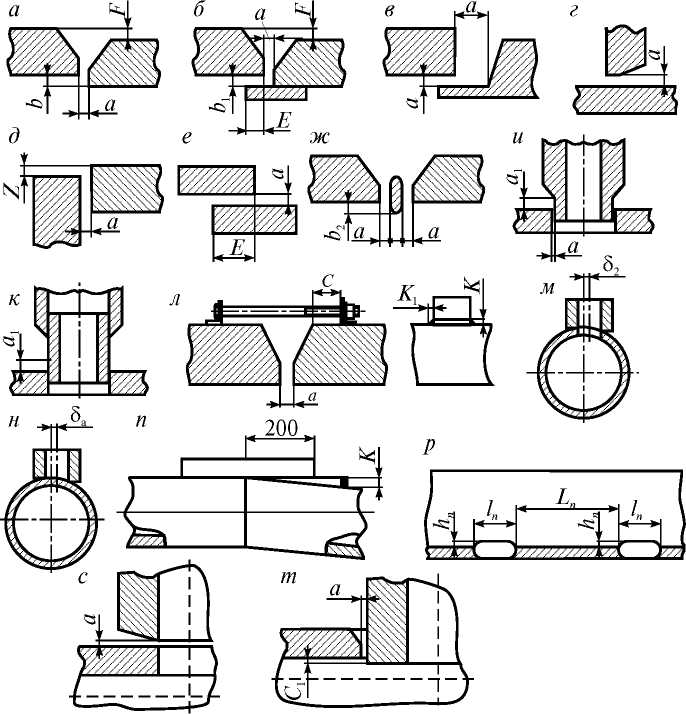
Рис. 6.3. Размеры, контролируемые при сборке соединения под сварку:
а — стыковое соединение; б — стыковое соединение с остающейся
подкладной пластиной (кольцом); в — стыковое замковое соединение;
г — тавровое соединение; д — угловое соединение; е — нахлесточное
соединение; ж — стыковое соединение с расплавляемой вставкой;
и, к — угловые соединения штуцеров; л — соединение с приварными
элементами временных креплений; м —
соединение с несоосностью
осей штуцера и корпуса; н — соединение с несоосностью осей в угловых
соединениях труб; п — соединение с переломом осей цилиндрических
деталей;р — прихватки соединения; с, т — тройниковое (угловое)
соединение
На кромках разделки не должно быть следов резки (для деталей из низкоуглеродистых, марганцовистых и кремнемарганцовистых сталей) и следов разметки (кернение), нанесенной на наружной поверхности деталей после резки.
Требования к выполнению измерительного контроля при подготовке деталей под сборку и сварку приведены Инструкции (РД 03-606-03).
Схемы измерения отдельных размеров подготовки деталей под сборку и сборки соединений под сварку с помощью шаблона универсального типа УШС приведены на рис. 6.4. Допускается применение шаблонов конструкций В.Э. Ушерова-Маршака и А.И. Красовского (рис. 6.5. и 6.6.).
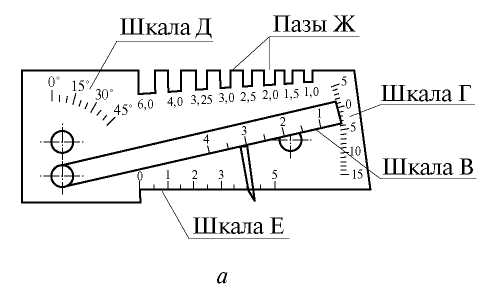
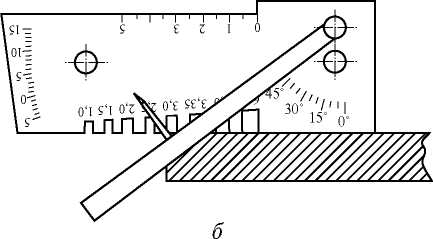
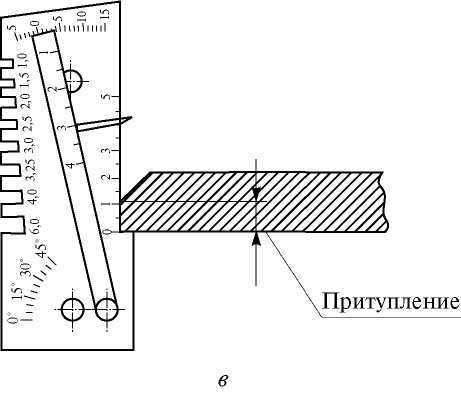
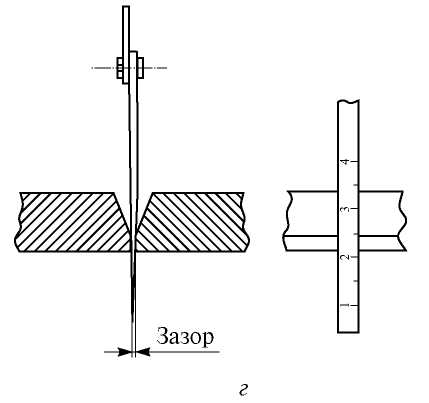
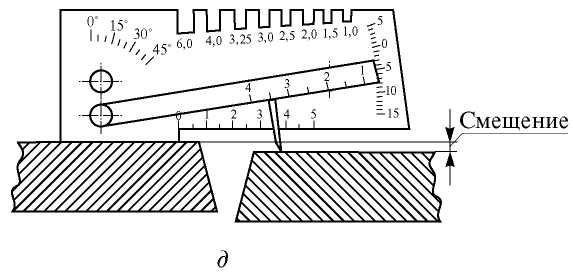
Рис. 6.4. Контроль универсальным шаблоном сварщика УШС (начало): а — общий вид шаблона УШС; б — измерение угла скоса разделки; в — измерение размера притупления кромкир; г — измерение зазора в соединении а; д — измерение смещения наружных кромок деталей
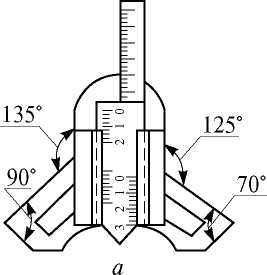
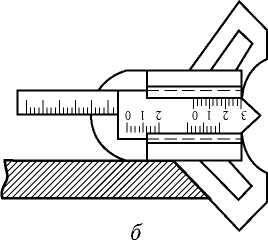
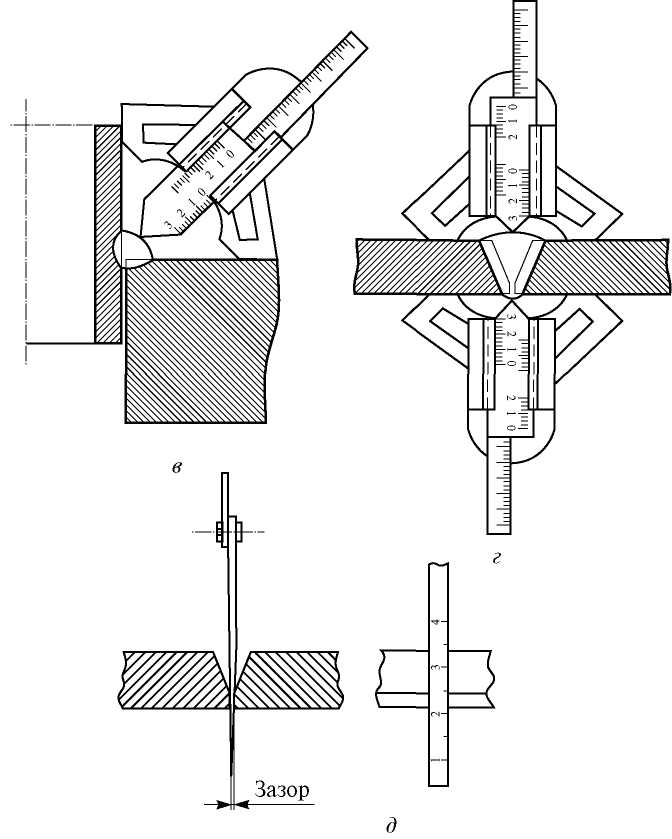
Рис. 6.5. Контроль шаблоном конструкции В.Э. Ушерова-Маршака (начало): а — общий вид шаблона; б — измерение угла скоса разделки
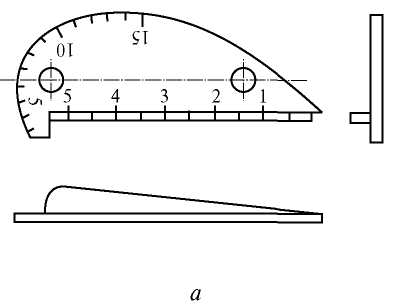
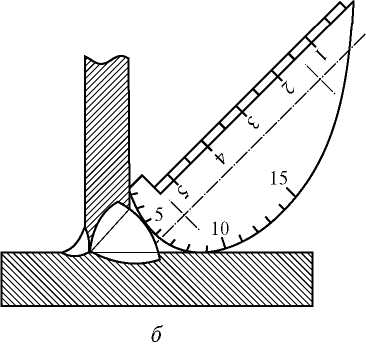
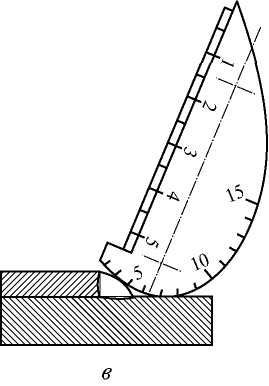
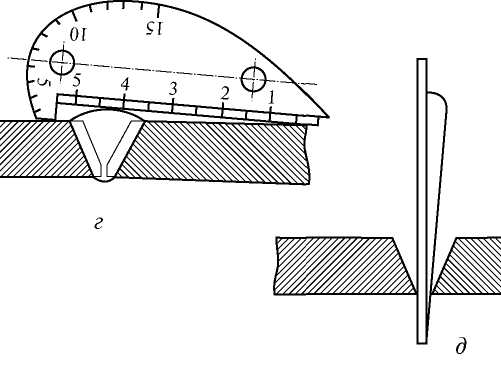
Рис. 7. Контроль шаблоном конструкции А.И. Красовского (начало): а — общий вид шаблона; б, в — контроль тавровых и нахлесточных сварных соединений; г — контроль стыковых сварных соединений; д — измерение зазора между кромками
Визуальный и измерительный контроль сварных соединений (наплавок) выполняется при производстве сварочных (наплавочных) работ и на стадии приемосдаточного контроля готовых сварных соединений. В случае если контролируется многослойное сварное соединение, визуальный контроль и регистрация его результатов могут проводиться после выполнения каждого слоя (послойный визуальный контроль в процессе сварки).
Послойный визуальный контроль в процессе сварки выполняется в случае невозможности проведения ультразвукового или радиационного контроля, а также по требованию Заказчика или в соответствии с ПТД.
Послойный визуальный контроль в процессе сварки выполняется с целью выявления недопустимых поверхностных дефектов (трещин, пор, включений, прожогов, свищей, усадочных раковин, несплавлений, грубой чешуйчатости, западаний между валиками, наплывов) в каждом слое (валике) шва. Выявленные при контроле дефекты подлежат исправлению перед началом сварки последующего слоя (валика) шва. По требованию Заказчика или в соответствии с ПТД сварные соединения, выполненные с послойным визуальным контролем, подлежат дополнительно контролю капиллярной или магнитопорошковой дефектоскопией на доступных участках.
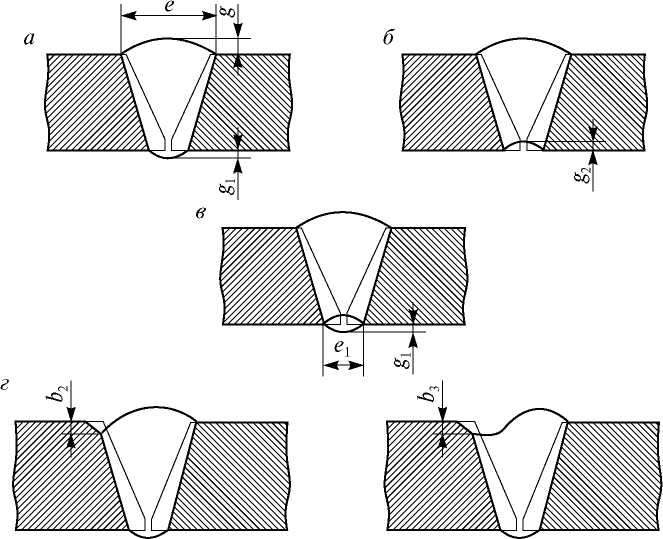
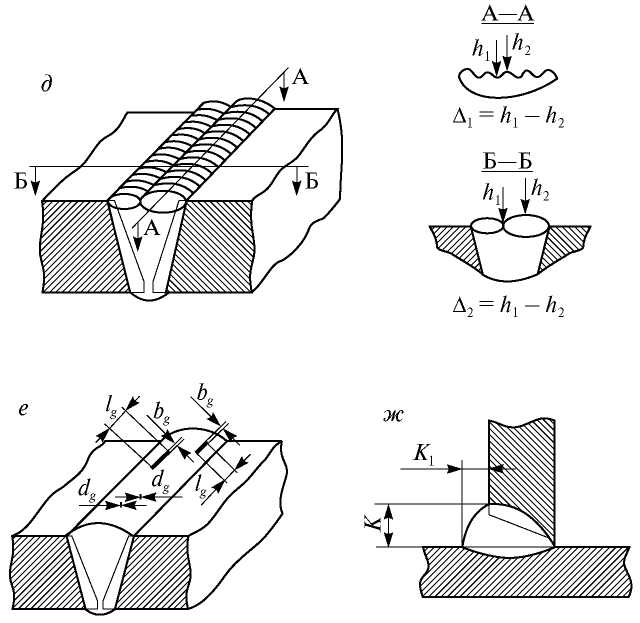
Рис. 8. Конструктивные элементы и дефекты сварного шва,подлежащие измерительному контролю (начало): а, б — размеры (ширина, высота) стыкового одностороннего шва с наружной и внутренней стороны; в — то же двухстороннего сварного шва; г —
подрез и неполное заполнение разделки кромок; д — чешуйчатость (Л^ шва и западание между валиками шва (Л2); е — размеры поверхностных включений (диаметр — d; длина — l; ширина — b включения); ж — размеры катета шва углового(таврового, нахлесточного) соединения
В выполненном сварном соединении визуально следует контролировать:
отсутствие (наличие) поверхностных трещин всех видов и направлений;
отсутствие (наличие) на поверхности сварных соединений дефектов (пор, включений, скоплений пор и включений, отслоений, прожогов, свищей, наплывов, усадочных раковин, подрезов, непроваров, брызг расплавленного металла, западаний между валиками, грубой чешуйчатости, а также мест касания сварочной дугой поверхности основного материала);
качество зачистки металла в местах приварки временных технологических креплений, гребенок индуктора и бобышек крепления термоэлектрических преобразователей (термопар), а также отсутствие поверхностных дефектов в местах зачистки;
наличие маркировки (клеймения) шва и правильность ее выполнения.
В выполненном сварном соединении измерениями необходимо контролировать:
размеры поверхностных дефектов (поры, включения и др.), выявленных при визуальном контроле;
высоту и ширину шва, а также вогнутость и выпуклость обратной стороны шва в случае доступности обратной стороны шва для контроля;
высоту (глубину) углублений между валиками (западания межваликовые) и чешуйчатости поверхности шва;
подрезы (глубину и длину) основного металла;
отсутствие непроваров (за исключением конструктивных непроваров) с наружной и внутренней стороны шва;
размеры катета углового шва;
отсутствие переломов осей сваренных цилиндрических элементов.
Измеряемые параметры и требования к выполнению измерительного контроля сварных швов приведены на рис. 8.
Измерительный контроль геометрических размеров сварного соединения (конструктивных элементов сварных швов, геометрического положения осей или поверхностей сваренных деталей, углублений между валиками и чешуйчатости поверхности шва, выпуклости и вогнутости корня односторонних швов и т.д.) следует проводить в местах, указанных в рабочих чертежах, НД, ПТД или ПДК, а также в местах, где допустимость указанных показателей вызывает сомнения по результатам визуального контроля.
Измерения отдельных размеров сварного соединения с помощью универсального шаблона типа УШС приведены на рис. 16.