Файл: Портландцемент (цемент). История изобретения. Гост 3051597.docx
ВУЗ: Не указан
Категория: Не указан
Дисциплина: Не указана
Добавлен: 09.11.2023
Просмотров: 60
Скачиваний: 1
ВНИМАНИЕ! Если данный файл нарушает Ваши авторские права, то обязательно сообщите нам.
Портландцемент (цемент). История изобретения. ГОСТ 30515-97
Цемент. Порошкообразный строительный вяжущий материал, который обладает гидравлическими свойствами, состоит из клинкера и при необходимости гипса или его производных и добавок.
Портландцемент. Цемент, полученный на основе портландцементного клинкера.
Портландцементом называют гидравлическое вяжущее вещество, получаемое тонким измельчением портландцементного клинкера с гипсом, а иногда со специальными добавками.
Портландцементом называют гидравлическое вяжущее вещество, в составе которого преобладают силикаты кальция (70-80 %).
Портландцемент – продукт тонкого измельчения клинкера с добавкой гипса (3-5 %). Гипс регулирует сроки схватывания портландцемента.
А.А. Акимов, В.В. Воронин «Технология производства неметаллических строительных изделий и конструкций».
Для производства портландцемента имеются неограниченные сырьевые ресурсы в виде побочных продуктов в промышленности (шлаков, зол, шамотов и распространенных карбонатов и глинистых горных пород).
История развития производства вяжущих веществ
Примерно за 4-3 тыс. лет до н.э. появились вяжущие вещества, получаемые искусственным путем обжига. Первым из них был, по-видимому, строительный гипс, получаемый обжигом гипсового камня при сравнительно невысокой температуре 140-1900С. Вслед за гипсом появилась воздушная известь, изготовляемая путем обжига известняка при более высокой температуре. При возведении пирамид и др. монументальных сооружений египтяне применяли гипс, а также растворы из смеси гипса с известью. При возведении некоторых пирамид использовали известковый раствор. В Китае при возведении ряда участков Великой Китайской стены применяли известь еще 200 лет до н.э..
В начале нашей эры римлян не удовлетворяли известные в то время воздушные вяжущие вещества, какими являлись строительный гипс и известь. Развивающееся городское хозяйство и дорожное строительство требовали водостойких вяжущих веществ с более высокой прочностью. Поэтому римляне строили водопроводы, каналы и аналогичные сооружения на известковых растворах, к которым примешивали толченый бой кирпича или гончарных изделий, а также измельченную пуццолану.
в Италии, стране с большим числом действующих и потухших вулканов, имелись громадные запасы трасов, туфов и др. продуктов вулканических извержений, известных под общим названием «пуццоланы» по месту залежей вблизи итальянского города Пуццуолли.
В 1756 г. англичанин Д. Смит применил при строительстве Эдисонского маяка продукт, полученный обжигом известняка содержащего глинистые примеси. Это вяжущее обладало гидравлическими свойствами, и поэтому впоследствии было названо гидравлической известью.
В 1796 г. англичанин Д. Паркер предъявил патент на производство из мергеля, негасящегося вяжущего материала, требующего после обжига помола и твердеющего под водой. Этот продукт напоминал цветом древние римские смеси из извести и пуццоланы и поэтому был назван романцементом (римским цементом).
В России вяжущие материалы стали применять в Х-ХI в.в. при возведении городских стен, башен, церквей и т.п. Развитие производства вяжущих материалов было вызвано строительством древних русских городов – Киева, Новгорода, Ростова, Суздаля, Владимира, Москвы и др.
После Отечественной войны 1812 г. в Москве развернулись большие строительные работы, прежде всего по восстановлению разрушенного Наполеоном Кремля. Егор Герасимович Челиев, начальник московской военно-рабочей бригады мастерских команд, производивших строительные работы в Москве, обобщил накопленный русскими строителями опыт и описал способ производства гидравлического вяжущего в книге «Полное наставление как приготовлять дешевый и лучший мергель или цемент весьма прочный для подводных строений как-то: каналов, мостов, бассейнов, плотин, подвалов, погребов и штукатурки каменных и деревянных строений». В этой книге Е.Г.Челиев описывает производство вяжущего вещества из искусственной сырьевой смеси, состоящей из одной части извести, обожженной из известняка и одной части глины. Эти материалы смешивали друг с другом в присутствии воды и формовали в кирпичи, которые обжигались в горне на сухих дровах добела (примерно при t0 1100-12000С). Продукт обжига Челиев предлагал измельчать на жерновах и просеивать через решета и грохоты, а затем упаковывать в бочки. Он считал необходимым брать гашеную известь, а не молотый известняк, т.к. последний нельзя было измолоть на существовавших в то время аппаратах до такой тонкости, которую имеет гашеная известь. Уже тогда Челиев предлагал добавлять гипс к полученному им цементу для повышения прочности и атмосфероустойчивости, а также для активизации лежащего без употребления в течение длительного времени продукта.
В 1824 г. англичанином Джозефом Аспдином был заявлен патент на производство вяжущего вещества, названного им портландцементом, т.к. оно в затвердевшем виде по цвету и прочности сильно походило на портландцементный камень, добываемый вблизи города Портленда (полуостров на юге Великобритании – Роrtland). Получали портландцемент путем обжига искусственной смеси известняка с глиной до полного удаления углекислоты при 900-10000С и последующего измельчения обожженного материала в порошок. Хотя название «портландцемент» и сохранилось, однако полученный Аспдином цемент не был портландцементом в современном смысле этого слова, а представлял собой разновидность искусственного романцемента вследствие недостаточной температуры обжига (не доведенного до спекания).
Заводское производство романцемента в России было организовано в Петербурге в 1839 г., а затем были построены заводы по производству романцемента в Усть-Ижоре в 1848 г, в Подольске в 1849 г. и в ряде других мест.
Производство портландцемента: сырьевые материалы, приготовление смеси по «сухому», «мокрому» и комбинированному способами.
Производство портландцемента включает в себя следующие основные этапы:
а) добычу в карьере и доставку на завод сырьевых материалов;
б) приготовление сырьевой смеси;
в) обжиг сырьевой смеси до спекания – получение клинкера;
г) помол клинкера с добавкой гипса – получение портландцемента.
Сырьевыми материалами для производства клинкера служат известняки с высоким содержанием СаСО3 (мел, известь, мергели и др.) и глинистые породы (глина, глинистые сланцы), содержащие SiO2, Al2O3, Fe2O3. Примерное соотношение между карбонатной и глинистой составляющими сырьевой смеси 3 : 1 (75-78% известняка и 25-22% глины). В сырьевую смесь вводят добавки, корректирующие химический состав, регулируя температуру спекания смеси и кристаллизацию минералов клинкера.
Приготовление сырьевой смеси состоит в тонком измельчении и смешении необходимого количества компонентов. Смесь приготовляют сухим, мокрым и комбинированными способами.
Обжиг сырьевой смеси как при сухом, так и при мокром способе осуществляется в основном во вращающихся печах (рис. 9.1), которые представляют собой длинный
, расположенный слегка наклонно цилиндр (барабан), сваренный из листовой стали с огнеупорной футеровкой внутри. Длина печей от 95 до 230 м, диаметр 5-7 м.
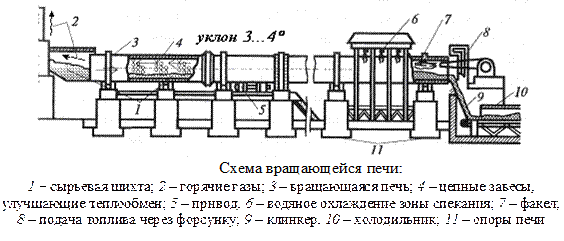
Сырье, подготовленное в виде порошка (сухой способ) или шлама (мокрый способ) подается автоматическим питателем в печь со стороны ее верхнего (холодного) конца, а со стороны нижнего (горячего) конца вдувается топливо (природный газ, мазут, воздушно-угольная смесь), сгорающее в виде 20…30 метрового факела. Сырье занимает только часть поперечного сечения печи и при ее вращении (скорость 1…2 об/мин) медленно движется к нижнему концу навстречу горячим газам, проходя 6 температурных зон: испарения (зона сушки), подогрева, декарбонизации, экзотермических реакций, спекания, охлаждения.
1.Зона испарения (зона сушки), в ней происходит высушивание сырьевой смеси при постепенном повышении температуры с 70 до 200 °С. Подсушенный материал комкуется, при перекатывании комья распадаются на более мелкие гранулы.
2.Зона подогрева – здесь при постепенном нагревании сырья с 200 до 700 °С сгорают находящиеся в нем органические примеси, из глины удаляется кристаллохимическая вода (при 500 °С) и образуется безводный каолинит Al2O3×2SiO2.
Подготовительные зоны (испарения и подогрева) при мокром способе занимают 50 – 60 % длины печи, при сухом же способе подготовка сырья сокращается за счет зоны испарения.
3.Зона декарбонизации (20% длины печи) – здесь температура материала поднимается с 700 до 1100 °С, завершается процесс разложения карбонатов кальция и магния с выделением большого количества СаО, что сопровождается большим поглощением теплоты. В этой же зоне происходит распад глинистых минералов на оксиды Al2O3, SiO2 и Fe2O3, которые вступают в химическое взаимодействие с СаО и в результате образуются минералы 3СаО×Al2O3 и частично 2СаО×SiO2.
4.Зона экзотермических реакций (5-7 % длины печи, температура 1100 –1250°С) – в этой зоне проходят реакции образования 3СаО×Al2O3, целита и белита; эти экзотермические реакции сопровождаются выделением большого количества теплоты и интенсивным повышением температуры материала.
5.Зона спекания – (10-15 % длины печи), здесь при температуре с 1300°С до 1450°С образуется расплав из легкоплавких минералов, в которых растворяются белит и СаО, из которых в расплаве происходит образование алита 3СаО×SiO2, идущее почти до полного связывания СаО. При вращении печи частично расплавленный материал непрерывно перекатывается, мелкие частицы слипаются в гранулы. Понижение температуры с 1450 до 1300°С вызывает кристаллизацию 3СаО×Al
2O3, целита и MgO, которая заканчивается в зоне охлаждения.
6.Зона охлаждения – температура клинкера понижается с 1300 до 1000°С; здесь полностью формируется его структура и состав, включающий алит, белит, C3A, C4AF, MgO (периклаз), стекловидную фазу и второстепенные составляющие.
Цементный клинкер выходит из вращающейся печи в виде мелких зерен – гранул. На выходе из печи клинкер интенсивно охлаждается воздухом с 1000°С до 100…200 °С в колосниковых и других холодильниках. После этого клинкер выдерживается на складе 1-2 недели.
Помол клинкера производится при помощи трубной мельницы, представляющей собой барабан, облицованный внутри стальными броневыми плитами и разделенный дырчатыми перегородками на 2-4 камеры. Материал измельчается под действием загруженных в барабан стальных шаров или цилиндров.
При помоле к клинкеру добавляется гипс (так чтобы общее содержание SO3 в цементе не превышало 3,5%), который регулирует сроки схватывания портландцемента.
Готовый портландцемент – очень мелкий порошок темно-серого или зеленовато-серого цвета; на выходе из мельницы он имеет высокую температуру (80-120 °С) и направляется пневмотранспортом на хранение в силосы, где он выдерживается до окончательного охлаждения и гашения влагой воздуха остатков свободного СаО. Из силосов портландцемент поступает в специальный транспорт, а также на расфасовку в мешки.
Производство п.ц. в основном осуществляется в два этапа – производстве клинкера и его переработки в цемент.
Клинкером называется продукт обожженной до спекания сырьевой смеси надлежащего состава (известняк 75-78 % и глина 22-25 %) обеспечивающей получение высокоосновных силикатов кальция.
Портландцемент получают тремя способами «мокрым», «сухим» и комбинированным.
«Мокрый» способ
Для приготовления сырьевой смеси применяют мягкое сырье, которое имеет значительную влажность (мел, глины, мягкий мергель). Сырьевые материалы, доставляемые на завод в кусках, подвергают предварительному измельчению (до размеров не более 5 мм). Твердые породы измельчают в дробилках, а более мягкие (глина, мел) перемешивают в дробилках-болтушках с водой. Для более тонкого совместного измельчения известняка, глины и корректирующих добавок (например, пиритных огарков, содержащих Fе