Файл: Портландцемент (цемент). История изобретения. Гост 3051597.docx
ВУЗ: Не указан
Категория: Не указан
Дисциплина: Не указана
Добавлен: 09.11.2023
Просмотров: 63
Скачиваний: 1
ВНИМАНИЕ! Если данный файл нарушает Ваши авторские права, то обязательно сообщите нам.
2О3) используют шаровые мельницы, обеспечивающие тщательное смешение исходных материалов и получение однородной смеси.
Помол сырья производят до остатка на сите 008 не более 8-10%, следовательно более 90% частиц смеси имеет размер менее 80 мкм.
Из мельниц известково-глиняный шлам (сметанообразная масса с содержанием воды от 35 до 45 %) перекачивают насосами в вертикальные или горизонтальные резервуары (шламбассейны), где окончательно корректируется и усредняется химический состав шлама. Во избежание расслоения шлам в бассейне перемешивают сжатым воздухом. Для снижения влажности шлама применяют разжижители (коагуляторы).
Данный процесс производства цементного клинкера энергоемкий. Из бассейна шлам равномерно подается на обжиг во вращающиеся печи.
«Сухой» способ
производства портландцемента применяют, когда сырье имеет невысокую влажность (8-10%). Сущность технологических операций не меняется, однако они осуществляются иными приемами. Производство «сухим» способом проще чем «мокрым» - отсутствует процесс образования шлама, можно совместить помол сырьевых материалов с подсушкой.
Таким образом, сырьевые материалы дробят, сушат, измельчают, поэтому сырьевая смесь получается в виде минерального порошка, называемого сырьевой мукой. Тонкое совместное измельчение известняка и глины осуществляют в трубных (шаровых) мельницах. Выходящая из мельниц сырьевая мука имеет влажность 1-2%. Сырьевую муку направляют в силосы, в них корректируется состав сырья и создается запас необходимый для бесперебойной работы печей.
Затем сухой порошок гранулируют или формуют в брикеты. Гранулы обжигают в циклонных теплообменниках, вращающихся печах; брикеты в шахтных печах.
Комбинированный способ
Подготовку сырья осуществляют по схеме мокрого способа, затем полученный шлам до поступления в печь частично обезвоживают на специальных установках, приготовляют из него гранулы и обжигают по схеме сухого способа.
Обжиг сырьевых смесей. Образование клинкера
Обжиг сырьевой смеси осуществляется в основном во вращающихся печах, которые представляют собой цилиндр (барабан) из листовой стали, стенки которого внутри футерованы огнеупорным материалом. Длина печи 95-185-230 м., диаметр от 5 до 7 м.
1. Вращающаяся печь; 2. Головка печи; 3. Горячая камера; 4. Холодильник;
5. Пылеосадитель
Данные печи при монтаже устанавливают под небольшим углом к горизонту (3-40) в сторону передвижения сырьевой смеси в процессе ее обжига. Для улучшения теплообмена внутри печей ближе к верхнему (холодному) концу устраивают цепные завесы, устанавливают теплообменники различной конструкции. Вращающиеся печи работают по принципу противотока. Сырье подается автоматическим питателем в печь со стороны ее верхнего холодного конца, а со стороны нижнего (горячего) вдувается топливо (природный газ и др.). Сырье занимает только часть печи по поперечному сечению, и при ее вращении медленно движется к нижнему концу, проходя различные температурные зоны (всего условно подразделяют 6 зон).
I. Испарение свободной воды при t0 70-800С (зона сушки).
II. Удаление химически связанной воды, т.е дегидратация глинистых минералов с образованием каолинитового ангидрита Аl2О3
и других подобных соединений при t0 200-7000С (зона подогрева).
III. Декарбонизация карбонатов кальция и магния СаСО3 = СаО+ СО2;
МgСО3 = МgО+СО2 и разложение глинистых компонентов на оксиды (SiO2, Аl2О3; Fе2О3) (зона кальцинирования) t0 – 700-11000C.
IV. Зона экзотермических реакций. ей при t0 – 1100-12500С продолжают образовываться соединения оксидов, определяющих состав клинкера.
V.Зона спекания. Здесь при t0 – 1300-14500С окончательно образуются соединения оксидов, и происходит спекание клинкера.
VI. Зона охлаждения до t0 10000С, при этом формируется структура и состав клинкера.
Клинкер представляет собой зерна серовато-зеленого цвета, твердые, размером до 25 мм (твердость 6-7 по шкале Мооса)
Раскаленный клинкер поступает в холодильник, где охлаждается до
80-1000С холодным воздухом.
Маганизирование клинкера
(хранение)
Выходящий из холодильника клинкер поступает на склад в течение
(3-4) недель. За это время снижается твердость зерен, что в дальнейшем облегчает помол.
Назначение складов двоякое:
1- создать запас клинкера;
2 – в клинкере происходит ряд физико-химических процессов, улучшающих его свойства.
Кроме клинкера в складах хранятся добавки, которые впоследствии подвергаются помолу вместе с клинкером.
Помол
Для получения портландцемента клинкер в тонкий порошок размалывают в трубных (рис.а) или шаровых мельницах (рис.б) с гипсом или другими добавками.
Трубные мельницы работают как по открытому, так и по закрытому циклу (помол, сепарация и снова помол крупных частиц). Открытый – однократный помол. Во время помола через мельницу продувается сжатый воздух. Свойства портландцемента зависят от минералогического состава и тонкости помола. Из мельниц цемент сжатым воздухом транспортируется на цементный склад. Хранят его в ж/б цилиндрах диаметром 8-14 м, высотой
25-30 м. Силосы оборудованы пневматическими устройствами для продувания цемента, аналогичными устройствами и в складах сырьевой муки.
Рис.а Рис.б
Цемент доставляется к потребителю в специализированных вагонах, автомобилях-цементовозах или упакованными в многослойные бумажные или полиэтиленовые мешки.
Хранить цемент следует в закрытых складах с плотной крышей, стенами и деревянным полом, возвышающимся над землей. При этом следует учитывать, что при хранении даже в самых благоприятных условиях активность цемента снижается в результате частичной гидратации и карбонизации. При хранении 3 мес. активность цемента снижается на
15-20%, а через 6 мес. на 20-30 %.
Химический и минералогический состав клинкера влияет на свойства.
Для получения хорошего и однородного по качеству портландцемента необходимо чтобы его химический состав, а следовательно состав сырья имел небольшие колебания.
Химический состав
Клинкер состоит из:
СаО – 63-67 %; SiО2 – 21-24 %; Аl2О3 – 4-7 %; Fе2О3 – 2-3 %
Это основные оксиды портландцементного клинкера.
Кроме основных могут присутствовать и другие: МgО; К2О; Nа2О; ТiО2; Сr2О5; SО3, которые снижают качество цемента.
Химический состав выражают при помощи модуля и коэффициента.
Основной или гидравлический модуль
Обязательно подсчитывают коэффициент насыщения (КН), который показывает отношение количества извести, остающейся после полного насыщения глинозема, оксида железа и серного ангидрита к тому количеству извести, которое необходимо для полного насыщения кремнезема.
Наилучшим являлся бы цемент, КН которого был бы = 1.
В действительности такого нет, но надо стремиться. Для обычного цемента КН = 0,82-0,95. По значениям модулей и КН можно судить о свойствах цемента.
Минералогический состав клинкера
Определяется основными минералами клинкера:
Алит – трехкальциевый силикат
(С3S) – самый важный минерал, который определяет быстроту твердения, прочность и др. свойства портландцемента, интенсивно выделяет тепло. Представляет собой твердый раствор трехкальциевого силиката и небольшого количества (2…4%) MgO, Al2O3, P2O5, Cr2O3 и других примесей, которые могут существенно влиять на структуру и свойства минерала. (содержится в количестве 45-65 %)
Белит – двухкальциевый силикат
(С2S) – медленно твердеет, но достигает высокой прочности при длительном твердении
п.ц. (20-30%). Второй по важности силикатный минерал клинкера, обладает малым тепловыделением. Представляет собой твердый раствор двухкальциевого силиката (С2S) и небольшого количества (1…3%) Al2O3, Fe2O3, MgO, Cr2O3.
Целит – трехкальциевый алюминат
(С3А) – быстро взаимодействует с водой, является причиной сульфатной коррозии (4-12 %). и при благоприятных условиях обжига получается в виде кубических кристаллов размером до 10-15 мкм; образует твердые растворы сложного состава. Он очень быстро гидратируется и твердеет, но имеет небольшую прочность и наибольшую интенсивность тепловыделения. Является причиной сульфатной коррозии бетона, поэтому в сульфатостойком портландцементе содержание С
3А ограничено 5%.
Браунмиллирит– четырехкальциевый алюмоферрит
(С4АF) по тепловыделению и быстроте твердения занимает промежуточное положение между С2S и С3S (10-20%).
Алюмоферритная фаза промежуточного вещества клинкера представляет собой твердый раствор алюмоферритов кальция разного состава.
Помол сырья производят до остатка на сите 008 не более 8-10%, следовательно более 90% частиц смеси имеет размер менее 80 мкм.
Из мельниц известково-глиняный шлам (сметанообразная масса с содержанием воды от 35 до 45 %) перекачивают насосами в вертикальные или горизонтальные резервуары (шламбассейны), где окончательно корректируется и усредняется химический состав шлама. Во избежание расслоения шлам в бассейне перемешивают сжатым воздухом. Для снижения влажности шлама применяют разжижители (коагуляторы).
Данный процесс производства цементного клинкера энергоемкий. Из бассейна шлам равномерно подается на обжиг во вращающиеся печи.
«Сухой» способ
производства портландцемента применяют, когда сырье имеет невысокую влажность (8-10%). Сущность технологических операций не меняется, однако они осуществляются иными приемами. Производство «сухим» способом проще чем «мокрым» - отсутствует процесс образования шлама, можно совместить помол сырьевых материалов с подсушкой.
Таким образом, сырьевые материалы дробят, сушат, измельчают, поэтому сырьевая смесь получается в виде минерального порошка, называемого сырьевой мукой. Тонкое совместное измельчение известняка и глины осуществляют в трубных (шаровых) мельницах. Выходящая из мельниц сырьевая мука имеет влажность 1-2%. Сырьевую муку направляют в силосы, в них корректируется состав сырья и создается запас необходимый для бесперебойной работы печей.
Затем сухой порошок гранулируют или формуют в брикеты. Гранулы обжигают в циклонных теплообменниках, вращающихся печах; брикеты в шахтных печах.
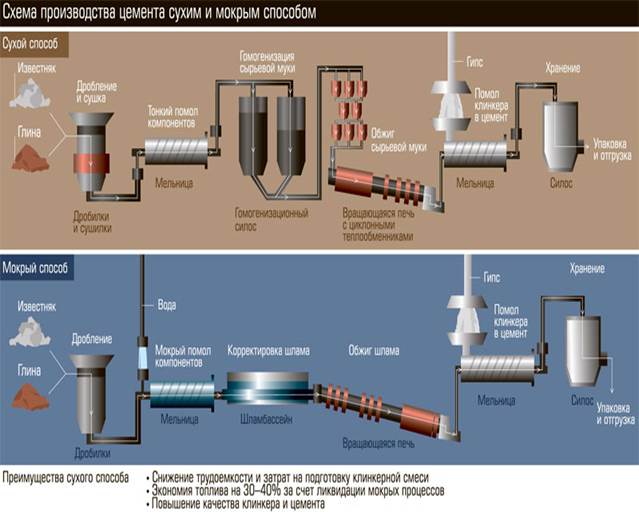
Комбинированный способ
Подготовку сырья осуществляют по схеме мокрого способа, затем полученный шлам до поступления в печь частично обезвоживают на специальных установках, приготовляют из него гранулы и обжигают по схеме сухого способа.
Обжиг сырьевых смесей. Образование клинкера
Обжиг сырьевой смеси осуществляется в основном во вращающихся печах, которые представляют собой цилиндр (барабан) из листовой стали, стенки которого внутри футерованы огнеупорным материалом. Длина печи 95-185-230 м., диаметр от 5 до 7 м.
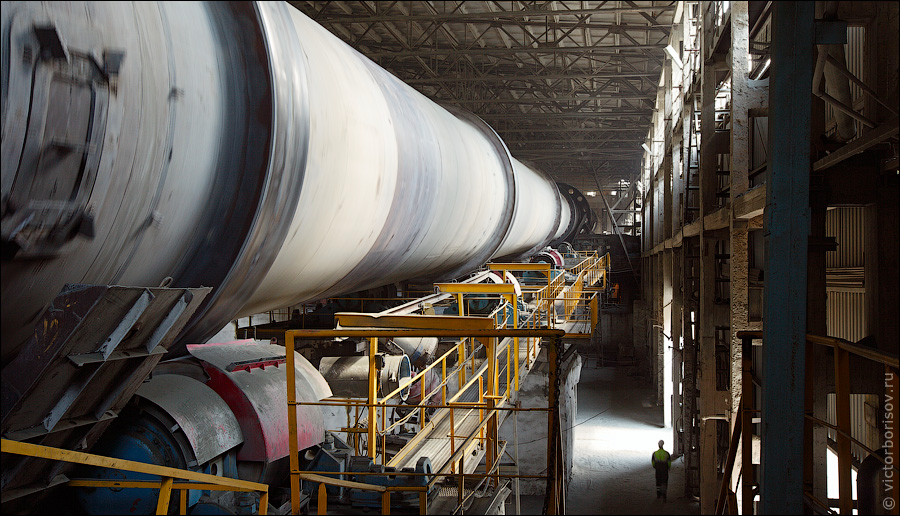

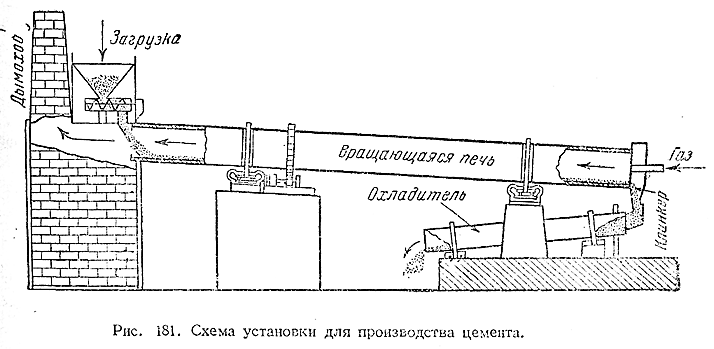
1. Вращающаяся печь; 2. Головка печи; 3. Горячая камера; 4. Холодильник;
5. Пылеосадитель
Данные печи при монтаже устанавливают под небольшим углом к горизонту (3-40) в сторону передвижения сырьевой смеси в процессе ее обжига. Для улучшения теплообмена внутри печей ближе к верхнему (холодному) концу устраивают цепные завесы, устанавливают теплообменники различной конструкции. Вращающиеся печи работают по принципу противотока. Сырье подается автоматическим питателем в печь со стороны ее верхнего холодного конца, а со стороны нижнего (горячего) вдувается топливо (природный газ и др.). Сырье занимает только часть печи по поперечному сечению, и при ее вращении медленно движется к нижнему концу, проходя различные температурные зоны (всего условно подразделяют 6 зон).
I. Испарение свободной воды при t0 70-800С (зона сушки).
II. Удаление химически связанной воды, т.е дегидратация глинистых минералов с образованием каолинитового ангидрита Аl2О3

III. Декарбонизация карбонатов кальция и магния СаСО3 = СаО+ СО2;
МgСО3 = МgО+СО2 и разложение глинистых компонентов на оксиды (SiO2, Аl2О3; Fе2О3) (зона кальцинирования) t0 – 700-11000C.
IV. Зона экзотермических реакций. ей при t0 – 1100-12500С продолжают образовываться соединения оксидов, определяющих состав клинкера.
V.Зона спекания. Здесь при t0 – 1300-14500С окончательно образуются соединения оксидов, и происходит спекание клинкера.
VI. Зона охлаждения до t0 10000С, при этом формируется структура и состав клинкера.
Клинкер представляет собой зерна серовато-зеленого цвета, твердые, размером до 25 мм (твердость 6-7 по шкале Мооса)
Раскаленный клинкер поступает в холодильник, где охлаждается до
80-1000С холодным воздухом.
Маганизирование клинкера
(хранение)
Выходящий из холодильника клинкер поступает на склад в течение
(3-4) недель. За это время снижается твердость зерен, что в дальнейшем облегчает помол.
Назначение складов двоякое:
1- создать запас клинкера;
2 – в клинкере происходит ряд физико-химических процессов, улучшающих его свойства.
Кроме клинкера в складах хранятся добавки, которые впоследствии подвергаются помолу вместе с клинкером.
Помол
Для получения портландцемента клинкер в тонкий порошок размалывают в трубных (рис.а) или шаровых мельницах (рис.б) с гипсом или другими добавками.
Трубные мельницы работают как по открытому, так и по закрытому циклу (помол, сепарация и снова помол крупных частиц). Открытый – однократный помол. Во время помола через мельницу продувается сжатый воздух. Свойства портландцемента зависят от минералогического состава и тонкости помола. Из мельниц цемент сжатым воздухом транспортируется на цементный склад. Хранят его в ж/б цилиндрах диаметром 8-14 м, высотой
25-30 м. Силосы оборудованы пневматическими устройствами для продувания цемента, аналогичными устройствами и в складах сырьевой муки.
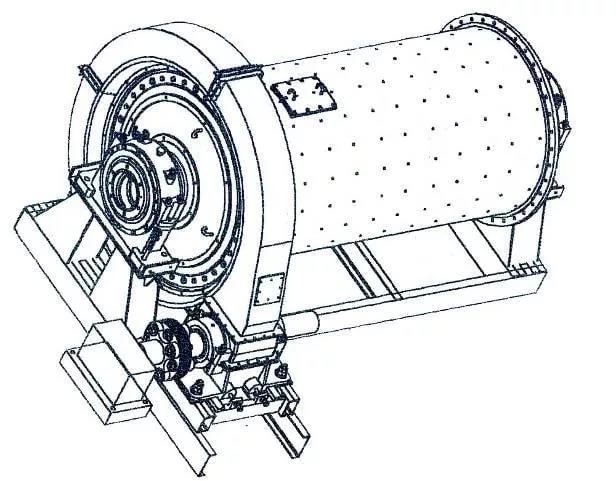
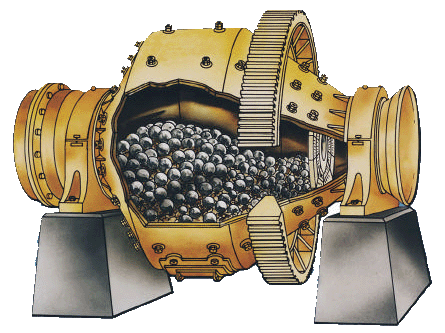
Рис.а Рис.б
Цемент доставляется к потребителю в специализированных вагонах, автомобилях-цементовозах или упакованными в многослойные бумажные или полиэтиленовые мешки.
Хранить цемент следует в закрытых складах с плотной крышей, стенами и деревянным полом, возвышающимся над землей. При этом следует учитывать, что при хранении даже в самых благоприятных условиях активность цемента снижается в результате частичной гидратации и карбонизации. При хранении 3 мес. активность цемента снижается на
15-20%, а через 6 мес. на 20-30 %.
Химический и минералогический состав клинкера влияет на свойства.
Для получения хорошего и однородного по качеству портландцемента необходимо чтобы его химический состав, а следовательно состав сырья имел небольшие колебания.
Химический состав
Клинкер состоит из:
СаО – 63-67 %; SiО2 – 21-24 %; Аl2О3 – 4-7 %; Fе2О3 – 2-3 %
Это основные оксиды портландцементного клинкера.
Кроме основных могут присутствовать и другие: МgО; К2О; Nа2О; ТiО2; Сr2О5; SО3, которые снижают качество цемента.
Химический состав выражают при помощи модуля и коэффициента.
Основной или гидравлический модуль

Обязательно подсчитывают коэффициент насыщения (КН), который показывает отношение количества извести, остающейся после полного насыщения глинозема, оксида железа и серного ангидрита к тому количеству извести, которое необходимо для полного насыщения кремнезема.

Наилучшим являлся бы цемент, КН которого был бы = 1.
В действительности такого нет, но надо стремиться. Для обычного цемента КН = 0,82-0,95. По значениям модулей и КН можно судить о свойствах цемента.
Минералогический состав клинкера
Определяется основными минералами клинкера:
Алит – трехкальциевый силикат
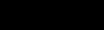
Белит – двухкальциевый силикат
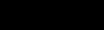
п.ц. (20-30%). Второй по важности силикатный минерал клинкера, обладает малым тепловыделением. Представляет собой твердый раствор двухкальциевого силиката (С2S) и небольшого количества (1…3%) Al2O3, Fe2O3, MgO, Cr2O3.
Целит – трехкальциевый алюминат
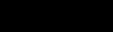
3А ограничено 5%.
Браунмиллирит– четырехкальциевый алюмоферрит

Алюмоферритная фаза промежуточного вещества клинкера представляет собой твердый раствор алюмоферритов кальция разного состава.