Файл: Российской федерации федеральное государственное бюджетное образовательное.docx
Добавлен: 10.11.2023
Просмотров: 89
Скачиваний: 3
ВНИМАНИЕ! Если данный файл нарушает Ваши авторские права, то обязательно сообщите нам.
Расширенное определение процессам смешения компонентов композита таково: это совокупность процессов направленного формирования гетерогенной системы, целью которых является обеспечение максимально возможного проявления обусловленных составом ценных свойств материала при наименьших экономических затратах. Разработка состава композиции представляет два взаимосвязанных этапа - разработку качественного состава, т.е. выбор наилучших исходных компонентов, и разработку количественного состава - нахождение оптимальных соотношений компонентов. Именно на данном этапе в будущий материал закладываются определенные полезные свойства, степень проявления которых зависит от эффективности процесса смешения. Создание принципов разработки составов композиций представляет собой особую область исследований. В дальнейшем будем считать тот или иной состав композиций, выбранный в качестве объекта исследования, оптимальным. Способы и средства подготовки компонентов определяются типом полимерной матрицы и наполнителя. Тип компонентов, варьирование соотношением компонентов, их агрегатное состояние и геометрическая форма наполнителя требуют достаточно различных технологических приемов совмещения компонентов как при получении конечного, так и промежуточного продуктов.
Исходя из этого, следует разделить технологии получения дис-персно-наполненных смесей и волокнистых композитов, которые имеют принципиальное различие.
Производство композиционных материалов может происходить двумя способами:
- за один технологический цикл, например, «мокрая» намотка, где совмещение армирующего наполнителя и формирования изделия происходит одновременно;.
- поэтапно, например «сухая» намотка или намотка препрегом, где совмещение компонента и формирование изделия происходит на различных этапах и оборудовании.
Следует более подробно рассмотреть понятия о промежуточных (совмещенных, но не сформированных) продуктах. Пресс-порошки - полимерные материалы с порошкообразным наполнителем требуемой дозировки и распределения по объему матричного материала, содержащие все необходимые компоненты, обеспечивающие возможность переработки в композит методом как компрессионного, так и трансферного прессования в соответствующих пресс-формах.
Гранулят - сыпучий материал, состоящий из однородных по размеру частиц с наполнителем в виде порошка (дисперсные) или волокна. Применяется во всех видах прессования, стабилизирует режим функционирования перерабатывающего оборудования, облегчает дозировку сырья, повышает производительность и качество готового изделия.
Премиксы - термореактивная формовочная композиция, армированная дисперсным или волокнистым наполнителем. В отличие от пресс-порошков изготовление заканчивается после смешения всех компонентов, и они не нуждаются в дальнейшем отверждении, сушке или других технологических операциях и готовы для переработки на литьевом прессе. Препреги - материалы рулонного типа в виде пропитанных полимерным связующим нитей, жгутов, лент, тканей, матов.
Препреги имеют более высокие прочностные показатели, чем премиксы. Применяются для изготовления крупногабаритных изделий средней сложности и изделий, имеющих контур тел вращения.
Слопреги - слоистые препреги, выложенные по определенной схеме армирования.
При «мокром» способе формования наполнитель пропитывается жидким связующим непосредственно перед формованием, т.е. пропитка технологически совмещена с формообразованием изделия. При сухом способе пропитка выделена в самостоятельную операцию, в результате которой из волокон и связующего получают препреги. Чтобы добиться высокого качества пропитки, в связующее обычно добавляют растворители, которые обеспечивают низкую технологическую вязкость. После пропитки препреги подсушивают и частично отверждают. В частично отвержденном состоянии препреги могут находиться от нескольких дней до нескольких месяцев, в зависимости от связующего и способа хранения.
«Сухой» способ формирования более технологичен, чем «мокрый». Так, при формовании методом намотки использование препреговой технологии позволяет увеличить натяжение до 25% от разрывной нагрузки по сравнению с «мокрой» намоткой, где натяжение составляет 10 - 15%. Преимущества «сухого» способа выражаются в использовании широкой номенклатуры связующих, в возможности получения препрегов с заданной степенью армирования, к сведению до минимума отходов материалов и возможности полной автоматизации процесса (например, использование выкладочных центров). В конечном счете применение препрегов повышает качество изделий и культуру их производства. Основные недостатки «сухого» способа - ограниченный срок хранения, повышенная стоимость материала по сравнению с «мокрым» способом, в некоторых случаях необходимость применения специальной технологической оснастки для подогрева препрега.
Поперечная прочность однонаправленного препрега должна быть достаточной для того, чтобы с ним можно было работать на машине или вручную. Готовый препрег или сразу, или по прошествии срока, гарантирующего жизнеспособность препрега, подвергается раскрою требуемой конфигурации и размера и последующей выкладке (изготовлению пакета). Иногда обе операции совмещаются и автоматизируются.
Так как технология изготовления препрегов в первую очередь предусматривает совмещение двух компонентов - термореактивной матрицы и волокнистого наполнителя, следует остановиться подробнее на каждом из компонентов и их подготовке к процессу совмещения. Хорошая пропитка волокон достигается при использовании низковязких расплавов связующих, однако повышение температуры, требуемое для таких пропитывающих композиций, может привести к преждевременному гелеобразованию и неконтролируемому их отверждению. В таком случае предпочитают применять растворители, хотя из-за пористости волокон возникают затруднения при удалении растворителя из препрега при его сушке. Традиционные методы сушки связаны с подводом теплоты от периферии материала к наполнителю, закрытому слоем нанесенного связующего. При этом происходит обеднение периферийного слоя связующего растворителем и образование плотной корки смолы, препятствующей массопереносу растворителя из внутренних слоев материала, и особенно из пор. Это заставляет проводить процесс сушки в мягких условиях (например, увеличение времени пребывания в зоне сушки при более низких температурах), что существенно уменьшает производительность технологического оборудования.
Использование активных растворителей, способных химически взаимодействовать с полимером в процессе отверждения, затруднено из-за избирательной сорбции (поглощения) подобных растворителей волокнами. В таких пластиках возможно протекание процессов внутренней пластификации полимерной матрицы. При подготовке армирующего наполнителя к пропитке большое значение приобретают вопросы сорбции-десорбции влаги, так как важно, чтобы перед пропиткой поры волокон были свободны от паров влаги, которая может явиться причиной парообразования при формовании пластика. Кроме того, адсорбированная влага, блокируя активные центры поверхности волокна, снижает его адгезию к связующему.
Исследование кинетики процесса удаления влаги при сушке волокон показало, что повторное насыщение влагой высушенных волокон проходит довольно интенсивно. Таким образом, сушку нужно проводить непосредственно перед операцией совмещения волокна со связующим. Процесс сушки должен быть быстрым и эффективным, чтобы при включении в общую технологическую линию он не снижал производительности оборудования. Операция совмещения осуществляется методом пропитки. Под пропиткой понимается введение в структуру волокнистого наполнителя полимерного связующего и образование в ней плотной монолитной матрицы. В зависимости от физико-химической природы компонентов связующего, их исходного состояния, получения жидкой фазы связующей композиции, необходимой для качественной пропитки, технологические варианты пропитки подразделяют на пропитку в растворе и пропитку в расплаве. Эти варианты различаются как технологической схемой пропитки, так и физической сущностью процесса.
Наиболее широкое распространение в производстве препрегов нашел метод пропитки армирующих наполнителей растворами связующих в органических растворителях.
Пропитку можно проводить как ручным, так и машинным способом. Ручной способ имеет ограниченное применение, используется обычно при разработке новых рецептур связующих, когда технологию получения пластика отрабатывают на небольших количествах растворов, или когда изделие не требует достаточной точности дозировки связующего и наполнителя, имеет несерийный выпуск, и все операции производятся вручную, например, изготовление корпуса спортивной яхты из пропитанной ткани.
Изготовление препрегов машинным способом на пропиточных машинах позволяет получать полуфабрикат с требуемыми характеристиками. Для получения качественного препрега важно в процессе переработки сохранить исходную прочность наполнителя и провести его полную равномерную и бездефектную пропитку. Наиболее трудно обеспечить это требование для жестких волокон, например, для углеродных. Особенностью углеродных волокон, влияющей на технологию их переработки, является низкая деформируемость (0,5 - 1,5%) и повышенная хрупкость волокна. Это влечет за собой трудности при пропитке углеродных волокон машинным методом, так как в этом процессе необходимо исключить их многократные перегибы и невозможно использование традиционных узлов отжима связующего. Узлы пропиточной машины должны обеспечивать повышенную точность и чистоту обработки, равномерное натяжение углеродных волокон без их механического повреждения. Препреги обычно изготавливают на горизонтальных или вертикальных пропиточно-сушильных машинах.
Вертикальные машины более широко распространены, так как занимают меньшую площадь (более компактны), в них легче регулируется тепловой поток сушильной камеры и удаление из рабочей зоны летучих (как правило, токсичных) выделений (рис. 1).
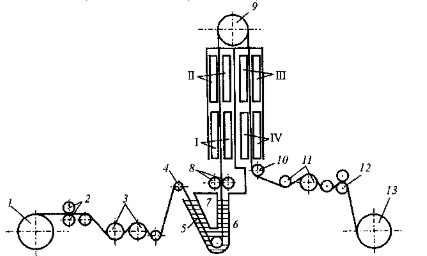
Рис. 1. Схема непрерывно действующей вертикальной пропиточно-сушильной машины с автоматическим управлением: Арматура 2 сматывается со шпулярника 1 и, проходя через систему направляющих и обогреваемых валков 3-4, поступает в пропиточную ванну 5 с раствором связующего, нагретым до необходимой температуры нагревателем 7. Выходящий из ванны 5 пропитанный материал направляется в зазор между двумя отжимными валками 8 и затем для удаления растворителя поступает в сушильную камеру, имеющую четыре зоны (I - IV) с различной температурой. Общая длина сушильной камеры может достигать 20 м. Высушенный препрег, огибая охлаждающие и направляющие валки 9- 12, сматывается в рулон 13.