Файл: Российской федерации федеральное государственное бюджетное образовательное.docx
Добавлен: 10.11.2023
Просмотров: 90
Скачиваний: 3
ВНИМАНИЕ! Если данный файл нарушает Ваши авторские права, то обязательно сообщите нам.
8. Демонтаж вакуумного мешка, снятие изделия с формы и передача на следующие технологические операции: - обрезка припуска - контроль - испытание - зачистка - грунтовка - окраска - оформление технологического паспорта.
Вакуумное формование. Сущность: использование внешнего атмосферного давления величиной до 1 атмосферы для получения из препрега монолитного материала.
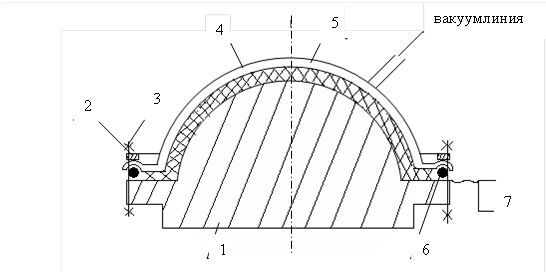
Рис. 9 Технологический пакет для формования 1. – форма. 2. – прижим. 3. – зажимное устройство (механическое или гидравлическое). 4. – формуемое изделие. 5. – вакуумный мешок. 6. – уплотнительный жгут. 7. – термопара.
Давление формования достигается отсасыванием воздуха, содержащегося в объеме между формующей поверхностью препрега и вакуумным мешком, прилегающим к форме. Для этой цели используются вакуумные насосы. Для отверждения в этом случае обычно используют печь, хотя можно использовать и нагреваемую форму. Все зависит от условий. Этот метод особенно эффективен, так как не требует дорогостоящих автоклавов, гидроклавов, и прессов, но качество формуемых изделий из-за низкого давления формования существенно ниже, чем при гидроклавном, автоклавном и пресс-камерном формовании.
Волоконная технология
Волоконная технология основана на получении препрегов в виде тканых полуфабрикатов, состоящих из армирующих (неплавких) и матричных (плавких) волокон с регулируемой структурой.
Использование связующего в виде волокон позволило реализовать различные текстильные структуры и формы в виде технических тканей, нетканых иглопробивных материалов, плетеных шнуров, трикотажа. Полученные по волоконной технологии композиционные материалы характеризуются широким разнообразием состава, текстурных и геометрических характеристик.
К недостаткам волоконной технологии можно отнести:
– отсутствие выпуска плавких волокон в Российской Федерации (имеется производство только волокон из полиамида-6 и опытное производство из полипропилена);
– технология получения тканых полуфабрикатов разработана только для органопластиков на основе полиамида-6 и армирующих волокон на основе СВМ, терлона и фенилона.
Из перечисленных способов только растворная и волоконная технологии обеспечивают качественную пропитку наполнителя связующим и высокий уровень механических свойств композиционного материала. Однако использование растворителей требует создания громоздких и дорогостоящих рекуперационных устройств, а пропитка проводится в 2–3 этапа. Кроме того, не все термопластичные связующие можно растворить в каком-либо растворителе и не все термопласты склонны к волокнообразованию.
Низкие механические свойства КТМ при использовании разных способов совмещения связаны, как правило, с плохим качеством пропитки наполнителя высоковязким расплавом связующего. Последующее прессование пластика практически не сказывается на глубине пропитки наполнителя связующим: волоконца остаются сухими, не связанными между собой. Только если перед совмещением со связующим наполнитель обработать аппретом или пропитать промежуточный слой, то, независимо от технологии совмещения, прочностные характеристики КТМ будут аналогичны свойствам КТМ, полученного по растворной технологии.
-
Технологические свойства и методы определения свойств препрегов
В связи с изменением состояния полимера на каждой стадии технологического процесса особенно важное значение имеют те его свойства, которые определяют поведение полимера на данной стадии и, следовательно, учитываются при выборе параметров переработки. Так, на стадии нагревания полимера определяющая роль принадлежит теплофизическим свойствам - температуре перехода полимера в вязкотекучее состояние, его теплоемкости и теплопроводности. На стадии подачи расплава в формующий инструмент большое значение имеют вязкостные, то есть реологические свойства расплава.
При охлаждении отформованного изделия важную роль играют как теплофизические свойства, так и процессы кристаллизации и усадки. Таким образом, поведение полимера при переработке определяется целым комплексом свойств, на основе которых выбираются параметры переработки. Эти свойства связаны с физическим состоянием термопласта - стеклообразным, высокоэластическим и вязкотекучим. В процессе переработки полимер последовательно находится в каждом из них и поэтому знание закономерностей перехода одного состояния в другое и структурных особенностей полимера необходимо для управления процессом переработки. Выбор метода переработки термопластов и расчет оптимальных технологических параметров проводится с учетом таких технологических характеристик, как показатель текучести расплава, термостабильность, усадка и др. Знание этих характеристик дает возможность правильно выбрать температуру и давление при переработке, рассчитать размер формы. Все это обеспечивает необходимое качество готовых изделий, а следовательно, их эксплуатационные свойства. Текучесть является важнейшей технологической характеристикой полимерных материалов и определяется ее обратной величиной - вязкостью. В области вязкотекучего состояния термопласты обладают малым сопротивлением деформации, происходит скольжение макромолекул относительно друг друга, т.е. течение полимера. Главной реологической особенностью расплавов термопластов является зависимость их вязкости от скорости течения. Исходя из этого для переработки термопластов область вязкотекучего состояния играет основную роль.
Поэтому знание основных закономерностей течения расплавов термопластов приобретает особое значение для правильного выбора параметров переработки материалов с термопластичной матрицей. Из практики известно, что чем выше интенсивность механического воздействия на полимеры, тем в большей степени они разжижаются, тем меньше их вязкость. В то время как вязкость низкомолекулярной жидкости остается постоянной, вязкость расплава уменьшается с увеличением скорости сдвига. Такое поведение расплавов полимеров при их течении объясняется особенностями молекулярной структуры:. - длинные молекулы полимера ориентируются при течении вдоль потока, ослабляя сопротивление течению;. - при увеличении напряжения сдвигу разрушаются структурные агрегаты молекул, уменьшая тем самым сопротивление течению, или вязкость системы;. - вязкость полимеров быстро увеличивается с возрастанием молекулярной массы;. - чем больше степень полимеризации, тем более затрудненным становится перемещение макромолекулы;. - вязкость расплава полимера зависит от температуры: чем выше температура, тем выше подвижность макромолекул и, соответственно, меньше вязкость. Текучесть - способность полимерных материалов к вязкому течению под действием тепла и давления, на практике оценивается показателем текучести расплава (ПТР) методом капиллярной вискозиметрии при стандартных условиях. Следующей важной характеристикой, связанной с температурой текучести, является термостабильностъ (термостойкость) - способность полимерного материала не разлагаться и не изменять внешнего вида при повышенных температурах без нагрузки. Формование изделий проводят при заданной температуре в течение определенного времени.
Следовательно, термостабильность дает возможность определить верхний температурный предел переработки термопластов. Термостабильностъ определяют методами термогравиометрии и дифференциального термического анализа. Количественной характеристикой термостабильности является температура Т , при которой начинается интенсивная потеря массы образца, или температура Т при которой потеря массы составляет определенную долю от исходной массы образца. Термостабильность также зависит от продолжительности выдержки полимера при повышенной температуре. Поэтому более полную характеристику термостабильности можно получить с помощью изотермической термогравиометрии, при которой определяют изменение массы во времени при постоянной температуре. Такие измерения в широких интервалах температур и различной продолжительности их действия позволяют оценить термостойкость в любом температурновременном режиме. Дифференциальный термический анализ основан на том, что химические превращения полимера сопровождаются тепловыми эффектами, следовательно, он позволяет более точно определить температуру начала интенсивных химических реакций, протекающих в полимере. При определении термостойкости большое значение имеет среда, в которой находится полимер (например, присутствие кислорода ускоряет деструкцию).
Для определения временной термостойкости применяют дериватограф, который позволяет фиксировать изменение массы образ. Среди приведенных полимеров наименее термостабильным является поливинилхлорид. Для повышения термостойкости таких полимеров в них вводят стабилизаторы, которые замедляют термическую и термоокислительную деструкцию. Процесс переработки -это не только придание конкретной формы изделию, но и создание определенной структуры материала. И то и другое напрямую связано с возможной усадкой термопласта. Усадка полимерных материалов характеризует уменьшение размеров отформованного изделия при его охлаждении. Усадка происходит в результате изменении структуры, разупорядочивания ориентированного полимера, т.е. обуславливается, главным образом, релаксационными явлениями в материале. Усадка термопластов зависит в основном от технологии их переработки. Например, при получении изделий методом литья под давлением она связана с интенсивным охлаждением расплава в литьевой форме. Усадка в форме происходит в две стадии: на первой - объем материала уменьшается вследствие понижения его температуры и увеличения плотности; на второй - усадка кристаллизующихся полимеров определяется скоростью и полнотой кристаллизации, а у аморфных полимеров - уменьшением объема только в результате понижения температуры.
Таблица 4. Термостабильность некоторых термопластов
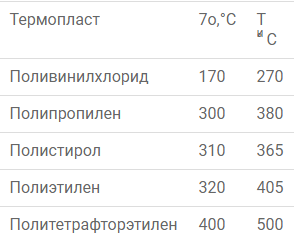
Заключение
В первой части курсовой работы рассмотрены