Файл: Министерство науки и высшего образования российской федерации выксунский филиал.docx
ВУЗ: Не указан
Категория: Не указан
Дисциплина: Не указана
Добавлен: 22.11.2023
Просмотров: 162
Скачиваний: 3
ВНИМАНИЕ! Если данный файл нарушает Ваши авторские права, то обязательно сообщите нам.
Требования к охлаждающей воде используемой во внутреннем контуре.
Таблица 9 – Рекомендованные параметры охлаждающей воды во внутреннем контуре
Параметр | Значение | Единица |
Максимальный общий расход воды | 200 | м3/ч |
Давление | 5,5 | бар |
Температура на входе не более | 38 | °С |
Температура на выходе не более зависит от получаемого слитка | 48 | °С |
Качество воды | Техническая специально подготовленная смешанная с антикоррозионной добавкой | |
Значение рН | 7,6-8,5 | - |
Карбонатная жесткость | 3-6 | Моль/л |
Размер твердых частиц | Не более 500 | мкм |
Удельная электропроводность | 250-400 | мкСм/см |
Суммарное содержание взвешенных твердых частиц | Не более 10 | мг/л |
Железо Fe2+ без Fe3+ | Не более 0,03 | мг/л |
Маганец Mn2+ | Не более 0,03 | мг/л |
Хлорид Cl- | Не более 50 мг/л | |
Сульфат SO42- | Не более 50 | мг/л |
Нитрат + нитрит NO3- NO2- | Не более 10 | мг/л |
Аммоний NH4 | Не более 10 | мг/л |
Кислород О2 | 4-5 | мг/л |
Агрессивная угольная кислота Н2СО3 | 0 | мг/л |
Остаток при испарении | Не более 500 | мг/л |
Взвешенные твердые вещества | Не более 250 | мг/л |
Таблица 10 – Рекомендованные параметры охлаждающей воды во внешнем контуре
Параметр | Значение | Единица |
Расход | 200 | М3/ч |
Охлаждающая способность теплообменников | - | МВт |
Качество воды | Техническая специально подготовленная с антикоррозионной добавкой | |
Давление | 3-5 | бар |
Температура на входе не более | 30 | °С |
Температура на выходе не более (зависит от типа слитка) | 50 | °С |
Значение рН | 7,6-8,5 | |
Кальциевая жесткость | 3-6 | ммоль/л |
Размер твердых частиц | Не более 500 | мкм |
Удельная электропроводность | 600-1500 | мкСм/см |
Значение м | 2,5-3,5 | м/л |
Железо Fe2+ без Fe3+ | Не более 1 | мг/л |
Хлорид Cl- | Не более 100 | мг/л |
Сульфат SO42- | Не более 100 | мг/л |
Диоксид кремния SiO2 | Не более 50 | мг/л |
Взвешенные твердые вещества | Не более 10 | мг/л |
Смазка / масло | Не более 5 | млн-1 |
Общее содержание солей | 350-550 | млн -1 |
Размножение микроорганизмов | Не более 10000 | 1/ млн |
Таблица 10. – Рекомендованные параметры воды используемой как аварийной
Параметр | Значение | Единица |
Расход Качество воды | 40 Неочищенная питьевая или техническая. | м3/ч |
Давление | 3-5 | бар |
Температура на входе | 25-35 | °С |
Температура на выходе | 35-45 | °С |
После аварийной ситуации, когда была использована система аварийного водоохлаждения необходимо промыть внутренний контур водоохлаждения печи ЭШП.
Таблица 11. – Требования к средам (аргону)
Параметр | Значение | Единица |
Максимальный расход на каждую головку (только в процессе запуска и при замене электродов) | 100 | м3/ч при н.у. |
Расход на каждую головку печи в процессе плавления и продувки | 5 | м3/ч при н.у. |
Качество (чистота) | 99,999 | % |
Точка росы | 83,8 | |
Давление | Не более 12 | Бар |
Температура на входе | 20 | °С |
Таблица 12. – Требования к средам (азоту)
Параметр | значение | единица |
Расход | 114 | м3/ч при н.у. |
Максимальный расход на каждую головку (только в процессе запуска и при замене электродов) | 100 | м3/ч при н.у. |
Расход на каждую головку печи в процессе плавления и продувки | 5 | м3/ч при нормальных условиях |
Качество (чистота) | 99,999 | % |
Точка росы | 63,2 | |
Давление | Не более 12 | Бар |
Температура на входе | 20 | °С |
Подача рабочего воздуха | 12 | м3/ч при н.у. |
Таблица 13. – Требования к средам (сжатому воздуху)
Параметр | значение | единица |
Общая пропускная способность | 12 | м3/ч при н.у. |
Качество (чистота) | Сухой и чистый | |
Давление | 6 | Бар |
Температура на входе | 20 | °С |
Точка росы | 3 | °С |
Содержание воды | Не более 1 | г/м3 при н.у. |
Содержание масла | Не более 0,02 | г/м3 при н.у. |
Таблица 14. – Требования к системе пылеудаления
Параметр | значение | единица |
Общий объем вытяжки для установки | 350 | м3/ч при н.у. |
Давление на выходе фильтра | 2000 | Па |
Температура отходящего газа на вытяжной насадке Постоянная температура Максимальная температура | +60 +120 | °С °С |
Концентрация пыли (очищаемый газ) | 5 | мг/м3 при н.у. |
Содержание HF | Не более 0,5 | мг/м3 при н.у. |
Таблица 15. – Максимальные выбросы в процессе работы установки
Параметр | Значение | Единица |
Выброс отработавших газов ... концентрация пыли в чистом газе …содержание HF в чистом газе | <5 < 1 | мг/м3 при н.у. мг/м3 при н.у. |
Излучения шума | Компоненты установки, уровень шума которых > 75 дБ(А) либо помещаются в защитные кожухи, либо устанавливаются в отдельных комнатах. Общее допущение заключается в том, что средний уровень шума во время работы составляет 65 дБ(А). |
В цикле перед электрошлаковым переплавом для получения готовой продукции на участке ЦСЭМ установлена Вакуумная дуговая печь (ВДП-7). Печь вакуумного дугового переплава предназначена для получения слитков максимальной массой до 6 тонн.
3.2 Экологические характеристики производства ЭШП 9.8 на АО Русполимет
В электросталеплавильных цехах главным источником загрязнения атмосферы цеха и окружающей среды являются высокотемпературные пылегазовыделения, связанные с работой печей: выделения из печи во время плавки, при сливе металла и шлака, при загрузке печи. Основная часть пылегазовыде-лений – это выделения из печи при плавке, их удельное количество изменяется от 2,1 до 8–10м3/(т • мин), причем наибольшее количество газов выделяется в период плавления и при продувке ванны кислородом.
В разные периды плавки эти газы имеют температуру от 800 до 1400-1600 °С и содержат 4-68% СО, 30-79% N2, до 30 % СО2, до 21 % О2; токсичные оксиды азота и серы, цианиды, диоксины и фториды; кроме того, газы содержат дисперсную пыль (в основном оксиды железа) в количестве 5–30, а при продувке кислородом до 60–100 г на 1 м3 газа.
Чтобы уменьшить загрязнение окружающей природной среды в разных цехах улавливают ту или иную часть пылегазовыде-лений и перед выбросом в атмосферу очищают их от пыли. В некоторых старых цехах с малыми печами выделяющиеся газы отсасывают через зонт, установленный над сводом с электродами и отворачиваемый при загрузке печи. Устраивают также местные отсосы от неплотностей рабочего пространства печи, например, устанавливая зонты над рабочим окном и выпускным желобом (рис. 17, а) или над рабочим окном и электродными отверстиями (рис. 17, б). Такие зонты громоздки и не улавливают все газовыделения.
На всех современных печах организован отсос печных газов через выполняемое в своде четвертое отверстие и закрепленный над ним на своде изогнутый футерованный патрубок (см. рис. 17, в). В ряде цехов наряду с отводом печных газов через сводовое отверстие над печью под крышей цеха устанавливают зонт больших размеров (рис. 17, д) для улавливания газов, выделяющихся через неплотности рабочего пространства, при сливе металла и шлака и за грузке печи.
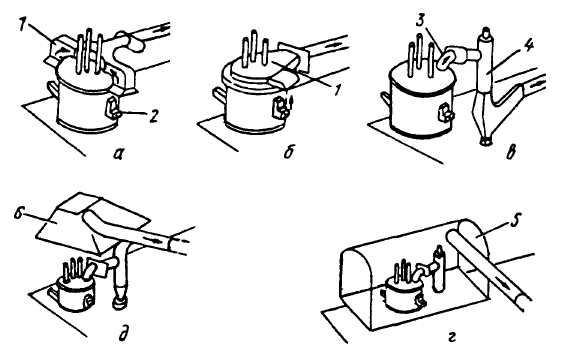
Рисунок 17 - Системы улавливания и отвода газов дуговых печей: 1 – зонт; 2 – рабочее окно; 3 – сводовый газоотводящий патрубок; 4 – газоочистка; 5 – дымошумоизолирующая камера; 6 – подкрышный зонт
Лучшим способом в настоящее время признан отвод печных газов через сводовое отверстие в сочетании с улавливанием всех остальных выделений с помощью сооружаемой вокруг печи герметичной шумодымоизолирующей камеры (рис. 17, г), которая вмещает также сталеразливочный ковш и чашу для слива шлака. Камера снабжена раздвижными дверями для подачи к печи загрузочной корзины, ковша и шлаковой чаши. Улавливаемые камерой газы так же, как и газы отводимые через свод, направляют на установку для очистки от пыли. Достоинством способа является то, что камера защищает персонал цеха от сильного шума электрических дуг.