Добавлен: 23.11.2023
Просмотров: 201
Скачиваний: 2
ВНИМАНИЕ! Если данный файл нарушает Ваши авторские права, то обязательно сообщите нам.
14,30 мм2/с; температура застывания (с обработкой) ниже минус 47 оС. Содержание парафина составило 0,50 %, температура его плавления 50 оС. Содержание серы 0,20%, азота 0,002, смол сернокислотных 7,00, силикагелевых 3,20%, асфальтенов следы. Коксуемость равна 0,90%, кислотное число – 1,38 мг КОН на 1 г нефти, выход фракций до 200 оС – 6,0%, до 300 оС – 30,0%.
Таблица 2.1 Характеристика мазутов и остатков
Разгонка нефтей по ГОСТу 2177–66 при н. к.–198
оС; при 200 оС 4%, при 220 оС 6%, при 240 оС 11%, при 260 оС 19%, при 280 оС 25%, при 300 оС 32%.
Элементный состав нефти следующий (%): С 86,11; Н 13,11; О 0,56; S 0,20; N 0,02.
Таблица 2.2 Характеристика сырья для деструктивных процессов
Основными продуктами гидрокрекинга являются бензиновые, керосиновые и дизельные фракции; в отдельных случаях — сжиженные газы С3—С4, и очищенные остаточные фракции — исходное сырье для пиролиза, каталитического крекинга, производства смазочных масел. Побочными продуктами являются сероводород и углеводороды С1—С2.
Дальнейшая переработка сероводорода осуществляется на установках производства серы или серной кислоты, углеводородные газы С1—С2 используются в качестве сырья для производства водорода или как топливо, сжиженные газы С3—С4 находят как техническое, так и бытовое применение. Легкий бензин с октановым числом до 85 (и.м. и м.м.) является высококачественным компонентом товарного автомобильного бензина.
Тяжелый бензин отличается высоким содержанием нафтеновых углеводородов и используется в качестве компонента сырья риформинга, обеспечивая получение автомобильного бензина с улучшенными антидетонационными характеристиками.
Керосиновые фракции отвечают требованиям на современные и перспективные реактивные топлива с повышенной плотностью, умеренным содержанием ароматических углеводородов, хорошими показателями по термической стабильности и низкотемпературным свойствам.
В процессе гидрокрекинга может быть получен весь ассортимент дизельных топлив от арктических до летних утяжеленных сортов. Дизельные топлива отличаются практическим отсутствием непредельных, сернистых и азотистых соединений и низким содержанием ароматических углеводородов, что обеспечивает им высокие эксплуатационные показатели.
Глубокоочищенная фракция 350—500 °С может быть использована как сырье для пиролиза; ее применение позволяет высвободить из производства этилена фракции бензина и дизельного топлива.
Остаточные фракции гидрокрекинга практически не содержат бн- и полициклических углеводородов и могут быть успешно использованы для получения масел с высоким индексом вязкости без применения стадии селективной очистки.
2.2. Выбор и обоснование схемы установки, режима осуществления процесса
В зависимости от состава исходного сырья, назначения процесса, применяемых катализаторов и инженерных решений технологические схемы гидрокрекинга могут быть разделены на три основных категории:
Технологические схемы принципиально схожи с установками гидроочистки - сырьё, смешанное с водородосодержащим газом (ВСГ), нагревается в печи, поступает в реактор со слоем катализатора, продукты из реактора отделяются от газов и поступают на ректификацию. Однако, реакции гидрокрекинга протекают с выделением тепла, поэтому технологической схемой предусматривается ввод в зону реакции холодного ВСГ, расходом которого регулируется температура. Гидрокрекинг - один из самых опасных процессов нефтепереработки, при выходе температурного режима из-под контроля, происходит резкий рост температуры, приводящий к взрыву реакторного блока.
Аппаратурное оформление и технологический режим установок гидрокрекинга различаются в зависимости от задач, обусловленных технологической схемой конкретного НПЗ, и используемого сырья. Например, для получения малосернистого вакуумного газойля и относительно небольшого количества светлых (лёгкий гидрокрекинг), процесс ведётся при давлении до 80 ат на одном реакторе при температуре около 350°С. Для максимального выхода светлых (до 90%, в том числе до 20% бензиновой фракции на сырье) процесс осуществляется на 2-х реакторах.
При этом, продукты после первого реактора поступают в ректификационную колонну, где отгоняются полученные в результате химических реакций светлые, а остаток поступает во второй реактор, где повторно подвергается гидрокрекингу. В данном случае, при гидрокрекинге вакуумного газойля давление составляет около 180 ат, а при гидрокрекинге мазута и гудрона - более 300. Температура процесса, соответственно, варьируется от 380 до 450°С и выше.
Совместное строительство установок гидрокрекинга и каталитического крекинга в рамках комплексов глубокой переработки нефти представляется наиболее эффективным для производства высокооктановых бензинов и высококачественных средних дистиллятов.
С разработкой эффективных аморфных и цеолитсодержащих алюмосиликатникельмолибденовых катализаторов, устойчивых к действию каталитических ядов, двухступенчатые схемы были заменены па одноступенчатые. При этом в случае производства среднедистиллятных продуктов (в основном, дизельного топлива) и сырья для пиролиза применяется одностадийная схема (процессы Эйч-Си Юнион фирмы UOP, гидрокрекинг фирмы Linde AG, гидрокрекинг фирмы BASF и Французского института нефти, гидрокрекинг фирмы British Petroleum International, изокрекинг фирмы Shevron Research, гидрокрекинг институтов ВНИИ НП — ВНИПИНефть).
На рис. 2.1. показана типовая технологическая схема одностадийного варианта процесса. Смесь свежего сырья, рециркулирующего остатка, циркулирующего и свежего водорода нагревается до температуры реакции и подается в реактор. Продукты, выходящие из реактора, отдают тепло сырьевой смеси и поступают в сепаратор высокого давления, где отделяется циркулирующий газ, возвращаемый в реактор. Жидкие продукты, покидающие сепаратор высокого давления, проходят последовательно сепаратор низкого давления, колонну дебутанизации и поступают в ректификационную колонну, где они разделяются на компоненты.
Двухстадийная схема используется для получения более широкого ассортимента продуктов: сжиженного газа, бензина, реактивного топлива, дизельного топлива и др. (процессы юникрекинг фирмы Union Oil of California, гидрокрекинг фирмы Houdry-Giilf, хайкрекинг фирмы Exxson Research and Engineering, гидрокрекинг фирмы BASF и Французского института нефти, гидрокрекинг институтов ВНИИ НП и ВНИПИНефть).
Рис 2.1. Одноступенчатая установка одностадийного гидрокрекинга
1 – реактор; 2 – сырьевая печь; 3 – компрессор добавочного водорода; 4 - циркуляционный компрессор; 5 – воздушный холодильник; 6 и 7 – газожидкостные сепараторы высокого и низкого давления; 8 – стабилизационная колонна; 9 – фракционирующая колонна; 10 – колонна вторичной перегонки бензина;
I – сырье; II – добавочный водород; III – вода; IV – кислые стоки; V – газ на очистку; VI – сжиженный нефтяной газ; VII – легкий бензин; VIII – тяжелый бензин; IX – лигроин; X – керосин; XI – газойль; XII – остаток.
В двухстадийном варианте процесса (рис. 2.2.) нагретое сырье и циркулирующий водородсодержащий газ смешивают и пропускают через реактор первой стадии для очистки от серы, азота и частично от ароматических углеводородов, после чего газосырьевая смесь вместе с рециркулирующим остатком и добавочным количеством водорода поступает во второй реактор для контакта с катализатором гидрокрекинга. Продукты, выходящие из второго реактора, отдают тепло сырьевой смеси и поступают в сепаратор высокого давления. Последующее движение продуктов реакции не отличается от предшествующей схемы.
Большинство промышленных установок гидрокрекинга работает под давлением 15—17 МПа сциркуляцией водородсодержащего газа, объемное содержание водорода о котором находится в пределах 80—85%. В отдельных случаях, например при производстве масел, давление поддерживается на уровне 20—25 МПа.
В последние годы получает распространение одностадийный процесс легкого гидрокрекинга вакуумного дистиллята при давлении 5—7 МПа с целью получения дизельного топлива и малосернистого сырья для каталитического крекинга.
Рис. 2.2. Одноступенчатая установка двухстадийного гидрокрекинга
1 – печь; 2 и 3 – первый и второй реакторы; 4 – газожидкостные сепараторы;
I – сырье; II – добавочный водород; III – циркулирующий водород; IV – газ на ГФУ; V – легкий бензин; VI – тяжелый бензин; VII – среднедистиллятное топливо; VIII – рециркулирующий остаток.
Кратность циркуляции водородсодержащего газа по отношению к перерабатываемому сырью принимается, в зависимости от назначения процесса, в пределах 800—2000 м3/м3 (указан объем газа при нормальных условиях).
Таблица 2.1 Характеристика мазутов и остатков
Продукт | Выход на нефть % | ![]() | ![]() | ![]() | ![]() | Температура, оС | Содержание серы, % | Коксуемость, % | |
застывания | вспышки | ||||||||
Мазут флотский: 5 12 | 73,0 61,0 | 0,8975 0,9004 | 4,89 11,38 | 2,14 2,91 | 1,50 1,73 | –27 –21 | 182 209 | 0,30 0,33 | 1,64 1,84 |
Мазут топочный 40 100 200 | 39,7 26,7 31,0 | 0,9062 0,9100 0,9085 | 32,05 79,01 61,00 | 8,00 15,15 13,00 | 3,72 8,25 6,50 | –10 0 –4 | 256 298 280 | 0,39 0,41 0,40 | 3,40 5,41 4,57 |
Остаток, % выше 350 выше 400 выше 450 выше 500 | 53,7 38,7 29,0 21,0 | 0,9018 0,9065 0,9102 0,9125 | 17,00 34,82 68,00 100,00 | 3,50 8,51 14,00 18,71 | 1,95 4,01 7,50 10,45 | –18 –9 –2 10 | 223 258 287 332 | 0,36 0,39 0,41 0,43 | 2,10 3,69 5,40 6,31 |
Разгонка нефтей по ГОСТу 2177–66 при н. к.–198
оС; при 200 оС 4%, при 220 оС 6%, при 240 оС 11%, при 260 оС 19%, при 280 оС 25%, при 300 оС 32%.
Элементный состав нефти следующий (%): С 86,11; Н 13,11; О 0,56; S 0,20; N 0,02.
Таблица 2.2 Характеристика сырья для деструктивных процессов
Остаток после отбора фракций до темп-ры, оС | Выход на нефть, % | ![]() | ![]() | Темп-ра застывания, оС | Содержание серы, % | Коксуемость, % |
350 450 500 | 53,7 29,0 21,0 | 0,9018 0,9102 0,9125 | 1,95 7,50 10,45 | –18 –2 10 | 0,36 0,41 0,43 | 2,10 5,40 6,31 |
Основными продуктами гидрокрекинга являются бензиновые, керосиновые и дизельные фракции; в отдельных случаях — сжиженные газы С3—С4, и очищенные остаточные фракции — исходное сырье для пиролиза, каталитического крекинга, производства смазочных масел. Побочными продуктами являются сероводород и углеводороды С1—С2.
Дальнейшая переработка сероводорода осуществляется на установках производства серы или серной кислоты, углеводородные газы С1—С2 используются в качестве сырья для производства водорода или как топливо, сжиженные газы С3—С4 находят как техническое, так и бытовое применение. Легкий бензин с октановым числом до 85 (и.м. и м.м.) является высококачественным компонентом товарного автомобильного бензина.
Тяжелый бензин отличается высоким содержанием нафтеновых углеводородов и используется в качестве компонента сырья риформинга, обеспечивая получение автомобильного бензина с улучшенными антидетонационными характеристиками.
Керосиновые фракции отвечают требованиям на современные и перспективные реактивные топлива с повышенной плотностью, умеренным содержанием ароматических углеводородов, хорошими показателями по термической стабильности и низкотемпературным свойствам.
В процессе гидрокрекинга может быть получен весь ассортимент дизельных топлив от арктических до летних утяжеленных сортов. Дизельные топлива отличаются практическим отсутствием непредельных, сернистых и азотистых соединений и низким содержанием ароматических углеводородов, что обеспечивает им высокие эксплуатационные показатели.
Глубокоочищенная фракция 350—500 °С может быть использована как сырье для пиролиза; ее применение позволяет высвободить из производства этилена фракции бензина и дизельного топлива.
Остаточные фракции гидрокрекинга практически не содержат бн- и полициклических углеводородов и могут быть успешно использованы для получения масел с высоким индексом вязкости без применения стадии селективной очистки.
2.2. Выбор и обоснование схемы установки, режима осуществления процесса
В зависимости от состава исходного сырья, назначения процесса, применяемых катализаторов и инженерных решений технологические схемы гидрокрекинга могут быть разделены на три основных категории:
-
одноступенчатая одностадийная; -
одноступенчатая двухстадийная; -
двухступенчатая.
Технологические схемы принципиально схожи с установками гидроочистки - сырьё, смешанное с водородосодержащим газом (ВСГ), нагревается в печи, поступает в реактор со слоем катализатора, продукты из реактора отделяются от газов и поступают на ректификацию. Однако, реакции гидрокрекинга протекают с выделением тепла, поэтому технологической схемой предусматривается ввод в зону реакции холодного ВСГ, расходом которого регулируется температура. Гидрокрекинг - один из самых опасных процессов нефтепереработки, при выходе температурного режима из-под контроля, происходит резкий рост температуры, приводящий к взрыву реакторного блока.
Аппаратурное оформление и технологический режим установок гидрокрекинга различаются в зависимости от задач, обусловленных технологической схемой конкретного НПЗ, и используемого сырья. Например, для получения малосернистого вакуумного газойля и относительно небольшого количества светлых (лёгкий гидрокрекинг), процесс ведётся при давлении до 80 ат на одном реакторе при температуре около 350°С. Для максимального выхода светлых (до 90%, в том числе до 20% бензиновой фракции на сырье) процесс осуществляется на 2-х реакторах.
При этом, продукты после первого реактора поступают в ректификационную колонну, где отгоняются полученные в результате химических реакций светлые, а остаток поступает во второй реактор, где повторно подвергается гидрокрекингу. В данном случае, при гидрокрекинге вакуумного газойля давление составляет около 180 ат, а при гидрокрекинге мазута и гудрона - более 300. Температура процесса, соответственно, варьируется от 380 до 450°С и выше.
Совместное строительство установок гидрокрекинга и каталитического крекинга в рамках комплексов глубокой переработки нефти представляется наиболее эффективным для производства высокооктановых бензинов и высококачественных средних дистиллятов.
С разработкой эффективных аморфных и цеолитсодержащих алюмосиликатникельмолибденовых катализаторов, устойчивых к действию каталитических ядов, двухступенчатые схемы были заменены па одноступенчатые. При этом в случае производства среднедистиллятных продуктов (в основном, дизельного топлива) и сырья для пиролиза применяется одностадийная схема (процессы Эйч-Си Юнион фирмы UOP, гидрокрекинг фирмы Linde AG, гидрокрекинг фирмы BASF и Французского института нефти, гидрокрекинг фирмы British Petroleum International, изокрекинг фирмы Shevron Research, гидрокрекинг институтов ВНИИ НП — ВНИПИНефть).
На рис. 2.1. показана типовая технологическая схема одностадийного варианта процесса. Смесь свежего сырья, рециркулирующего остатка, циркулирующего и свежего водорода нагревается до температуры реакции и подается в реактор. Продукты, выходящие из реактора, отдают тепло сырьевой смеси и поступают в сепаратор высокого давления, где отделяется циркулирующий газ, возвращаемый в реактор. Жидкие продукты, покидающие сепаратор высокого давления, проходят последовательно сепаратор низкого давления, колонну дебутанизации и поступают в ректификационную колонну, где они разделяются на компоненты.
Двухстадийная схема используется для получения более широкого ассортимента продуктов: сжиженного газа, бензина, реактивного топлива, дизельного топлива и др. (процессы юникрекинг фирмы Union Oil of California, гидрокрекинг фирмы Houdry-Giilf, хайкрекинг фирмы Exxson Research and Engineering, гидрокрекинг фирмы BASF и Французского института нефти, гидрокрекинг институтов ВНИИ НП и ВНИПИНефть).
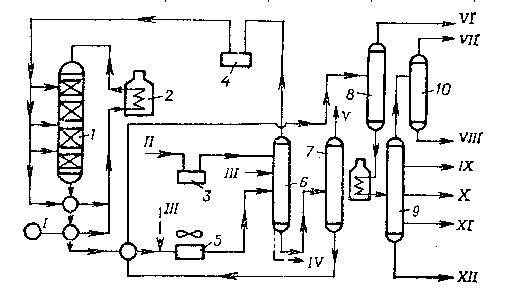
Рис 2.1. Одноступенчатая установка одностадийного гидрокрекинга
1 – реактор; 2 – сырьевая печь; 3 – компрессор добавочного водорода; 4 - циркуляционный компрессор; 5 – воздушный холодильник; 6 и 7 – газожидкостные сепараторы высокого и низкого давления; 8 – стабилизационная колонна; 9 – фракционирующая колонна; 10 – колонна вторичной перегонки бензина;
I – сырье; II – добавочный водород; III – вода; IV – кислые стоки; V – газ на очистку; VI – сжиженный нефтяной газ; VII – легкий бензин; VIII – тяжелый бензин; IX – лигроин; X – керосин; XI – газойль; XII – остаток.
В двухстадийном варианте процесса (рис. 2.2.) нагретое сырье и циркулирующий водородсодержащий газ смешивают и пропускают через реактор первой стадии для очистки от серы, азота и частично от ароматических углеводородов, после чего газосырьевая смесь вместе с рециркулирующим остатком и добавочным количеством водорода поступает во второй реактор для контакта с катализатором гидрокрекинга. Продукты, выходящие из второго реактора, отдают тепло сырьевой смеси и поступают в сепаратор высокого давления. Последующее движение продуктов реакции не отличается от предшествующей схемы.
Большинство промышленных установок гидрокрекинга работает под давлением 15—17 МПа сциркуляцией водородсодержащего газа, объемное содержание водорода о котором находится в пределах 80—85%. В отдельных случаях, например при производстве масел, давление поддерживается на уровне 20—25 МПа.
В последние годы получает распространение одностадийный процесс легкого гидрокрекинга вакуумного дистиллята при давлении 5—7 МПа с целью получения дизельного топлива и малосернистого сырья для каталитического крекинга.
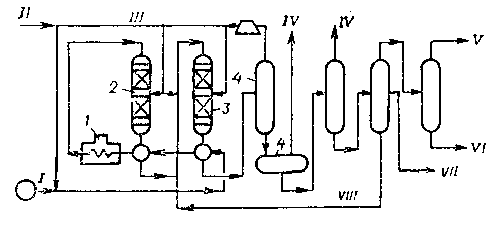
Рис. 2.2. Одноступенчатая установка двухстадийного гидрокрекинга
1 – печь; 2 и 3 – первый и второй реакторы; 4 – газожидкостные сепараторы;
I – сырье; II – добавочный водород; III – циркулирующий водород; IV – газ на ГФУ; V – легкий бензин; VI – тяжелый бензин; VII – среднедистиллятное топливо; VIII – рециркулирующий остаток.
Кратность циркуляции водородсодержащего газа по отношению к перерабатываемому сырью принимается, в зависимости от назначения процесса, в пределах 800—2000 м3/м3 (указан объем газа при нормальных условиях).