Файл: Тематический план по выполнению лабораторных работ и практических занятий по междисциплинарному курсу мдк 01. 04. Контроль качества сварных соединений.docx
ВУЗ: Не указан
Категория: Не указан
Дисциплина: Не указана
Добавлен: 23.11.2023
Просмотров: 192
Скачиваний: 1
ВНИМАНИЕ! Если данный файл нарушает Ваши авторские права, то обязательно сообщите нам.
2. Он основан на том же явлении капиллярности, что и контроль пенетрантами. К слову сказать, в некоторые пенетранты фирменного изготовления керосин входит в качестве составляющего компонента.
Проверка керосином сводится к ряду последовательных операций:
Негерметичность швов обнаруживает себя появлением темных полос или точек на меловом или каолиновом покрытии, которые с течением времени расплываются в более обширные пятна. Именно поэтому наблюдать за обратной стороной нужно сразу после нанесения керосина - чтобы зафиксировать первые проявления керосина, точно указывающие на место и форму дефекта. Проявляющиеся точки свидетельствуют о порах и свищах, полоски - о сквозных трещинах. Этот метод, при котором в качестве проникающего вещества используют керосин (керосиновая проба), получил широкое распространение благодаря своей простоте и сравнительно высокой чувствительности. С помощью керосина контролируют открытые изделия – емкости, элементы гидравлических и газовых систем. В ряде случаев этот метод используют и при испытаниях закрытых систем – топливных отсеков, баков, а также сварных соединений различных изделий. Высокая проникающая способность керосина обусловлена тем, что он не является полярно-активной жидкостью, имеет сравнительно низкую вязкость, хорошо растворяет пленки жира и устраняет пробки в неплотностях. В качестве индикатора течи используют меловую обмазку того же состава, что и при гидравлических испытаниях.
Различают четыре способа испытаний:
Контроль керосиновым способом выполняют следующим образом.
Чувствительность и порядок осмотра изделий при испытаниях керосиновым способом:
Иногда для повышения чувствительности контроля керосин окрашивают, растворяя в нем краски ярких цветов. Керосиновым способом могут быть выявлены течи диаметром до 0,1 мм в изделиях толщиной до 25 мм.
При керосинопневматическом способе контроля изделие после смачивания керосином обдувают струей сжатого воздуха под давлением 0,3...0,4 МПа, что повышает чувствительность контроля и ускоряет выявление дефектов.
Керосиновакуумный способ основан на применении переносных вакуумных камер, устанавливаемых на контролируемое изделие со стороны меловой обмазки. При этом так же, как и при керосинопневматическом способе, повышаются чувствительность и производительность контроля.
При керосиновибрационном способе на изделие, смоченное керосином, воздействуют ультразвуковыми колебаниями, что существенно ускоряет процесс проникновения керосина в неплотности и также повышает чувствительность и производительность контроля.
Чувствительность способов испытаний керосином существенно зависит от чистоты последнего. Примеси, растворяемые керосином, повышают его вязкость, что приводит к уменьшению потока через течь, которая при малых размерах может закупориться. Особое влияние на чувствительность
испытаний оказывают компоненты смазок, применяемых при сборке гидро- и газовых систем и вымываемых керосином из объектов в процессе контроля. Использование загрязненной проникающей жидкости может привести к невыявлению скрытых дефектов, которые в дальнейшем, при эксплуатации изделия, могут проявиться в виде значительных течей.
Испытание сжатым воздухом применяется только для закрытых сосудов. Для испытания в сосуд с предварительно заглушенными отверстиями подается сжатый воздух под давлением 1,0—2,0 атм. Снаружи все швы смачиваются мыльной водой, и сжатый воздух, выходя через неплотности, образует мыльные пузыри, по которым определяют пороки в швах и исправляют их.
Рис.1. Цистерна, подготовленная для проверки на герметичность с использованием керосина
Испытание воздухом
Необходимо отметить, что испытание воздухом при неправильной подготовке изделий или подаче воздуха без чувствительного манометра и предохранительного клапана представляет значительную опасность. Крышки и заглушки перед испытанием должны быть надежно закреплены.Применять сжатый воздух давлением свыше 2 атм не рекомендуется вследствие опасности разрушения конструкций.
Гидравлическое испытание
При гидравлическом испытании проверяется прочность и плотность различных сосудов, котлов и трубопроводов, работающих под давлением. При этом испытании сосуд с плотно закрытыми отверстиями наполняется водой. Воздух из него выходит через верхнее отверстие, которое после заполнения также заглушается. Затем давление доводится до необходимой величины, и сосуд подвергается тщательному осмотру. Швы, имеющие пороки, дают течь и потение, а слабые места даже разрушаются. После выдержки и осмотра давление в сосуде доводится до рабочего, и металл сосуда на расстоянии 15—20 мм от швов подвергается обстукиванию легкими ударами молотка (весом 0,4—1,5 кг) с круглым бойком для предупреждения образования вмятин. Величина давления при испытании устанавливается соответствующими инструкциями по контролю и правилами освидетельствования. Обычно испытательное давление на 25—100% больше рабочего. Рабочее место, где производится испытание, должно быть оборудовано в соответствии с правилами по технике безопасности.
II.Практическая часть.
1.Технологическая задача: Провести испытания на герметичность швов сварных конструкций. Данные контроля занести в таблицу.
2.Технологическая задача: Укажите способы контроля качества сварных швов емкости для хранения нефтепродуктов. Выберите наиболее эффективный. Обоснуйте ответ.
2. Тестовое задание.
1. Ржавчина, окалина, масло, краска, влага являются причиной образования дефектов, которые называют:
1) поры; 3) включения;
2) трещины; 4) несплавления.
2. Трещины, непровары, несплавления относят к группе дефектов, которую называют:
1) объемные; 3) случайные;
2) трещиноподобные; 4) аварийные.
3. Самые опасные дефекты в сварных швах:
1) поры; 3) трещины;
2) включения; 4) наплывы.
4. Самые опасные концентраторы напряжений в сварных швах:
1) поры; 3) наплывы;
2) включения; 4) трещины.
5. При удалении дефектных мест длина удаляемого участка должна равняться длине дефектного участка плюс с каждой стороны:
1) 1-2 мм; 3)10-20 мм;
2) 5-10 мм; 4) 20-40 мм.
6. Число исправлений одного и того же дефектного участка зависит от категории ответственности конструкции и не должно превышать:
1) двух; 3) четырех;
2) трех; 4) семи.
7.Зачистка шва предполагает удаление:
8.Что должно подвергаться зачистке после сварки?
9.Брызги металла удаляются с поверхности сварного шва и околошовной зоны при помощи:
10.Ширина околошовной зоны, подвергаемой зачистке, составляет не менее:
11.Шлаковую корку со сварного шва можно удалить:
12. Контроль, который предусматривает проверку: квалификации сварщиков, качества сварочных материалов, состояния сварочного оборудования и аппаратуры, сборочно-сварочных приспособлений:
1) предварительный; 3) приемочный;
2) пооперационный; 4) срочный.
13. Контроль, который включает проверку качества подготовки и сборки деталей под сварку, соблюдения режимов сварки, порядка выполнения многослойных швов и т.д.:
1) предварительный; 3) приемочный;
2) пооперационный; 4) срочный.
14. Контроль, производимый после завершения всех предусмотренных технологическим процессом операций, результаты которого фиксируют в сдаточной документации на изделие:
1) предварительный; 3) приемочный;
2) пооперационный; 4) срочный.
15. Приемочный контроль, при котором проверяют все сварные соединения:
1) сплошной; 3) обязательный;
2) выборочный; 4) оперативный.
16. Приемочный контроль, при котором проверяют часть сварных соединений:
1) сплошной; 3) необходимый;
2) выборочный; 4) срочный.
17.Документ, в котором указываются завод-изготовитель основного металла, марка и химический состав металла, номер плавки, профиль и размер материала, масса металла и номер партии, результаты всех испытаний, стандарт на данную марку материала:
1) аттестат; 3) диплом;
2) калькуляция; 4) сертификат
18. Операции, выполняемые для проверки правильности соблюдения технологии данного производства и качества его продукции:
1) контрольные; 3) регистрирующие;
2) технологические; 4) выпускающие.
19.Контроль, при котором выявляют дефекты, обнаруживаемые невооруженным глазом, а также с помощью лупы 10-кратного увеличения:
1) физический; 3) оперативный;
2) визуальный; 4) объективный.
20.Испытания, при которых определяют прочность, твердость, пластичность металла:
1)аналитические; 3)технологические;
2)физические; 4) механические.
Проверка керосином сводится к ряду последовательных операций:
-
Очистка шва с двух сторон от шлака, грязи и ржавчины. -
Покрытие одной из сторон (той, за которой удобнее наблюдать) водной суспензией каолина или мела (350-450 г на 1 л воды). После нанесения суспензии необходимо подождать, пока она высохнет. Для ускорения процесса покрытие можно просушить горячим воздухом. -
Обильное смачивание обратной стороны керосином - 2-3 раза в течение 15-30 минут, в зависимости от толщины металла. Это можно делать струей из краскопульта или паяльной лампы, а также с помощью кисти или кусочка ветоши. -
Наблюдение за стороной, на которую нанесена меловая или каолиновая суспензия, и маркирование проявляющихся дефектов.
Негерметичность швов обнаруживает себя появлением темных полос или точек на меловом или каолиновом покрытии, которые с течением времени расплываются в более обширные пятна. Именно поэтому наблюдать за обратной стороной нужно сразу после нанесения керосина - чтобы зафиксировать первые проявления керосина, точно указывающие на место и форму дефекта. Проявляющиеся точки свидетельствуют о порах и свищах, полоски - о сквозных трещинах. Этот метод, при котором в качестве проникающего вещества используют керосин (керосиновая проба), получил широкое распространение благодаря своей простоте и сравнительно высокой чувствительности. С помощью керосина контролируют открытые изделия – емкости, элементы гидравлических и газовых систем. В ряде случаев этот метод используют и при испытаниях закрытых систем – топливных отсеков, баков, а также сварных соединений различных изделий. Высокая проникающая способность керосина обусловлена тем, что он не является полярно-активной жидкостью, имеет сравнительно низкую вязкость, хорошо растворяет пленки жира и устраняет пробки в неплотностях. В качестве индикатора течи используют меловую обмазку того же состава, что и при гидравлических испытаниях.
Различают четыре способа испытаний:
-
керосиновый; -
керосинопневматический; -
керосиновакуумный; -
керосиновибрационный.
Контроль керосиновым способом выполняют следующим образом.
-
На места контроля, предназначенного для осмотра, наносят меловую обмазку. -
Противоположную сторону изделия несколько раз смачивают керосином либо укладывают на нее ленту или кусок ткани, смоченные керосином. -
После выдержки, определяемой ТУ на изделие, его осматривают, выявляя места течей по пятнам керосина цвета ржавчины на меловой обмазке.
Чувствительность и порядок осмотра изделий при испытаниях керосиновым способом:
Давление керосина, Па | Чувствительность, мм3 · МПа/с | Порядок осмотра при толщине материала изделия, мм | |
до 6 | свыше 6 до 25 | ||
- | 6,6 · 10-2 | 1. Сразу после подачи керосина 2. Через 15...30 мин после подачи керосина | 1. Через 3...5 мин после подачи керосина 2. Через 30...50 мин после подачи керосина |
2,9 · 105 | 6,6 · 10-3 | 1. Через 1...2 мин после подачи давления 2. Через 15...30 мин после подачи давления | 1. Через 1...2 мин после подачи давления 2. Через 30...40 мин после подачи давления |
Иногда для повышения чувствительности контроля керосин окрашивают, растворяя в нем краски ярких цветов. Керосиновым способом могут быть выявлены течи диаметром до 0,1 мм в изделиях толщиной до 25 мм.
При керосинопневматическом способе контроля изделие после смачивания керосином обдувают струей сжатого воздуха под давлением 0,3...0,4 МПа, что повышает чувствительность контроля и ускоряет выявление дефектов.
Керосиновакуумный способ основан на применении переносных вакуумных камер, устанавливаемых на контролируемое изделие со стороны меловой обмазки. При этом так же, как и при керосинопневматическом способе, повышаются чувствительность и производительность контроля.
При керосиновибрационном способе на изделие, смоченное керосином, воздействуют ультразвуковыми колебаниями, что существенно ускоряет процесс проникновения керосина в неплотности и также повышает чувствительность и производительность контроля.
Чувствительность способов испытаний керосином существенно зависит от чистоты последнего. Примеси, растворяемые керосином, повышают его вязкость, что приводит к уменьшению потока через течь, которая при малых размерах может закупориться. Особое влияние на чувствительность
испытаний оказывают компоненты смазок, применяемых при сборке гидро- и газовых систем и вымываемых керосином из объектов в процессе контроля. Использование загрязненной проникающей жидкости может привести к невыявлению скрытых дефектов, которые в дальнейшем, при эксплуатации изделия, могут проявиться в виде значительных течей.
Испытание сжатым воздухом применяется только для закрытых сосудов. Для испытания в сосуд с предварительно заглушенными отверстиями подается сжатый воздух под давлением 1,0—2,0 атм. Снаружи все швы смачиваются мыльной водой, и сжатый воздух, выходя через неплотности, образует мыльные пузыри, по которым определяют пороки в швах и исправляют их.
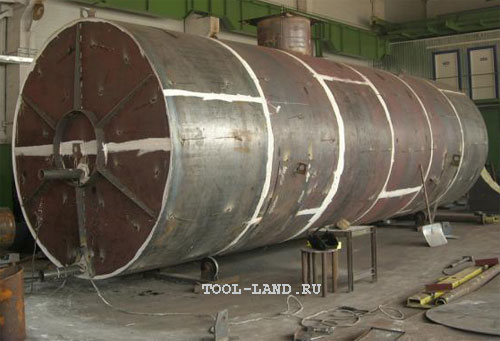
Рис.1. Цистерна, подготовленная для проверки на герметичность с использованием керосина
Испытание воздухом
Необходимо отметить, что испытание воздухом при неправильной подготовке изделий или подаче воздуха без чувствительного манометра и предохранительного клапана представляет значительную опасность. Крышки и заглушки перед испытанием должны быть надежно закреплены.Применять сжатый воздух давлением свыше 2 атм не рекомендуется вследствие опасности разрушения конструкций.
Гидравлическое испытание
При гидравлическом испытании проверяется прочность и плотность различных сосудов, котлов и трубопроводов, работающих под давлением. При этом испытании сосуд с плотно закрытыми отверстиями наполняется водой. Воздух из него выходит через верхнее отверстие, которое после заполнения также заглушается. Затем давление доводится до необходимой величины, и сосуд подвергается тщательному осмотру. Швы, имеющие пороки, дают течь и потение, а слабые места даже разрушаются. После выдержки и осмотра давление в сосуде доводится до рабочего, и металл сосуда на расстоянии 15—20 мм от швов подвергается обстукиванию легкими ударами молотка (весом 0,4—1,5 кг) с круглым бойком для предупреждения образования вмятин. Величина давления при испытании устанавливается соответствующими инструкциями по контролю и правилами освидетельствования. Обычно испытательное давление на 25—100% больше рабочего. Рабочее место, где производится испытание, должно быть оборудовано в соответствии с правилами по технике безопасности.
II.Практическая часть.
1.Технологическая задача: Провести испытания на герметичность швов сварных конструкций. Данные контроля занести в таблицу.
№ п/п | Наименование образца | Наличие бракованных участков | Причины возникновения и способы устранения брака |
| | | |
| | | |
| | | |
2.Технологическая задача: Укажите способы контроля качества сварных швов емкости для хранения нефтепродуктов. Выберите наиболее эффективный. Обоснуйте ответ.
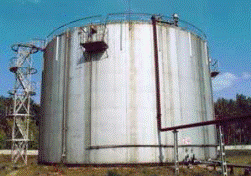
2. Тестовое задание.
1. Ржавчина, окалина, масло, краска, влага являются причиной образования дефектов, которые называют:
1) поры; 3) включения;
2) трещины; 4) несплавления.
2. Трещины, непровары, несплавления относят к группе дефектов, которую называют:
1) объемные; 3) случайные;
2) трещиноподобные; 4) аварийные.
3. Самые опасные дефекты в сварных швах:
1) поры; 3) трещины;
2) включения; 4) наплывы.
4. Самые опасные концентраторы напряжений в сварных швах:
1) поры; 3) наплывы;
2) включения; 4) трещины.
5. При удалении дефектных мест длина удаляемого участка должна равняться длине дефектного участка плюс с каждой стороны:
1) 1-2 мм; 3)10-20 мм;
2) 5-10 мм; 4) 20-40 мм.
6. Число исправлений одного и того же дефектного участка зависит от категории ответственности конструкции и не должно превышать:
1) двух; 3) четырех;
2) трех; 4) семи.
7.Зачистка шва предполагает удаление:
-
неровности; -
шлаковой корки; -
брызг застывшего металла.
8.Что должно подвергаться зачистке после сварки?
-
Только сварной шов. -
Только околошовная зона. -
Сварной шов и околошовная зона.
9.Брызги металла удаляются с поверхности сварного шва и околошовной зоны при помощи:
-
зубила и молотка; -
шлифовального круга, закрепленного в шлифовальной машине; -
круглой шлифовальной металлической щеткой, закрепленной в шлифовальной машине.
10.Ширина околошовной зоны, подвергаемой зачистке, составляет не менее:
-
40 мм; -
20 мм; -
80 мм.
11.Шлаковую корку со сварного шва можно удалить:
-
молотком и зубилом; -
молотком- шлакоотделителем; -
шлифовальным кругом, закрепленным на пневмомашине.
12. Контроль, который предусматривает проверку: квалификации сварщиков, качества сварочных материалов, состояния сварочного оборудования и аппаратуры, сборочно-сварочных приспособлений:
1) предварительный; 3) приемочный;
2) пооперационный; 4) срочный.
13. Контроль, который включает проверку качества подготовки и сборки деталей под сварку, соблюдения режимов сварки, порядка выполнения многослойных швов и т.д.:
1) предварительный; 3) приемочный;
2) пооперационный; 4) срочный.
14. Контроль, производимый после завершения всех предусмотренных технологическим процессом операций, результаты которого фиксируют в сдаточной документации на изделие:
1) предварительный; 3) приемочный;
2) пооперационный; 4) срочный.
15. Приемочный контроль, при котором проверяют все сварные соединения:
1) сплошной; 3) обязательный;
2) выборочный; 4) оперативный.
16. Приемочный контроль, при котором проверяют часть сварных соединений:
1) сплошной; 3) необходимый;
2) выборочный; 4) срочный.
17.Документ, в котором указываются завод-изготовитель основного металла, марка и химический состав металла, номер плавки, профиль и размер материала, масса металла и номер партии, результаты всех испытаний, стандарт на данную марку материала:
1) аттестат; 3) диплом;
2) калькуляция; 4) сертификат
18. Операции, выполняемые для проверки правильности соблюдения технологии данного производства и качества его продукции:
1) контрольные; 3) регистрирующие;
2) технологические; 4) выпускающие.
19.Контроль, при котором выявляют дефекты, обнаруживаемые невооруженным глазом, а также с помощью лупы 10-кратного увеличения:
1) физический; 3) оперативный;
2) визуальный; 4) объективный.
20.Испытания, при которых определяют прочность, твердость, пластичность металла:
1)аналитические; 3)технологические;
2)физические; 4) механические.