Файл: Ремонт с применением сварки монорельса консольнокозлового крана.docx
ВУЗ: Не указан
Категория: Не указан
Дисциплина: Не указана
Добавлен: 05.12.2023
Просмотров: 132
Скачиваний: 1
ВНИМАНИЕ! Если данный файл нарушает Ваши авторские права, то обязательно сообщите нам.
разная ширина и высота шва, что указывает на колебания мощности дуги, частые ее обрывы и неустойчивость горения. Геометрические размеры швов определяют с помощью специальных измерительных приборов: шаблонов, штангенциркулей и линеек.
По форме и размерам швы должны удовлетворять ГОСТ 5264-80, иметь гладкую или равномерно чешуйчатую поверхность (высота или глубина впадин не должна превышать 1 мм), металл шва должен иметь плавное сопряжение с основным металлом, швы не должны иметь недопустимых внешних дефектов.
К недопустимым внешним дефектам относятся: трещины любых видов и размеров, несплавления, наплывы, грубая чешуйчатость, наружные поры и цепочки пор, прожоги и свищи.
По внешним признакам контролируемый сварной шов часто сравнивают со специальными эталонами. Геометрические показатели швов определяют, используя специальные шаблоны и измерительные инструменты.
Рисунок 3.Визуальный измерительный контроль
Ультразвуковой контроль проводят после проведения визуального и измерительного контроля. Ультразвуковой контроль сварных соединений выполняют в соответствии с требованиями ГОСТ 14782-86.
Ультразвуковой контроль сварных швов — это неразрушающий целостности сварных соединений метод контроля и поиска внутренних дефектов недопустимой величины и химических отклонений от заданной нормы. Методом ультразвуковой дефектоскопии (УЗД) проводится диагностика разных сварных соединений. УЗК является действенным при выявлении воздушных пустот (трещин, непроваров, пор и т.д.), химически неоднородного состава (шлаковые включения в металле) и выявления присутствия неметаллических элементов.
Ультразвуковая технология основана на свойстве ультразвуковых волн направленно распространятся в средах и отражаться от их границ или нарушений сплошности (дефектов), обладающих другим акустическим сопротивлением
Способ контроля качества сварных соединений ультразвуком широко распространился благодаря простоте и удобству применения, относительно недорогому оборудованию, безопасности использования по сравнению с радиационным методом.
Минусом способа является трудность расшифровки графического изображения. Контроль качества соединения может сделать только сертифицированный специалист. [11]
2.4 Анализ сварочных дефектов, обнаруживаемых при сварке
Дефектов называется несоответствие параметров и характеристик сварного шва или соединения требованиям нормативно-технической документации.[12]
Различают следующие виды дефектов сварных соединений:
-наружные;
-внутренние;
При выполнении ремонта с применением сварки монорельса консольно-козлового крана могут образоваться следующие дефекты:
1.Трещины(рис.4)- дефект сварного соединения в виде разрыва в сварном шве и (или) прилегающих к нему зонах сварного соединения и основного металла.
Трещины являются недопустимыми дефектами, так как являются концентратором напряжения и очагом разрушения. Это самые опасные дефекты сварного соединения, часто приводящие к его разрушению.
Причинами образования трещин чаще всего является несоблюдение технологии и режимов сварки.
Поверхностные трещины в сварных конструкциях устраняются в следующем порядке: сначала засверливают концы трещины, чтобы она не распространялась дальше по шву, затем трещину удаляют механическим путем или строжкой, после чего место удаления дефекта зачищают и заваривают.
Внутренние трещины (как впрочем, и остальные внутренние дефекты) удаляют механическим способом или строжкой с последующей заваркой данного участка.
Рисунок 4. Трещина в сварном соединении
2. Поры в сварном шве(рис.5) - называют полости, заполненные газами. Возникают в жидком металле шва вследствие интенсивного газообразования, при котором не все газовые пузырьки успевают выйти наружу до затвердевания сварного шва. В сварном шве, помимо одиночных пор, могут возникать и скопления пор, а иногда даже раковины и свищи.
Наличие пористости в сварном соединении снижает механические свойства металла (прочность, ударную вязкость и т.п.), а также герметичность изделия.
Участок сварочного шва, в котором присутствуют поры, подлежит переварке с предварительной механической зачисткой или строжкой с последующей механической обработкой.
Рисунок 5.Поры в сварном соединении
3.Кратер(рис.6) - усадочная раковина в конце валика сварного шва, который образуется в виде углублений в местах резкого отрыва дуги в конце сварки. В углублениях кратера могут появляться усадочные рыхлости, часто переходящие в трещины.
Рисунок 6.Кратер в сварном соединении
Кратеры обычно появляются в результате неправильных действий сварщика. Кратеры уменьшают рабочее сечение сварочного шва, то есть снижают его прочность. Кратеры вырубают до основного металла, зачищают и заваривают.
4.Шлаковое включение(рис.7) - шлак, попавший в металл сварного шва.
Рисунок 7.Шлаковое включение в сварном соединении
Шлак, образующийся при плавлении электродного покрытия, всегда всплывает на поверхность сварочной ванны. Шлак может оставаться внутри металла только при нарушении техники и технологии процесса (большим скорость сварки, неправильный наклон электрода, плохая зачистка ранее выполненного валика).
Шлаковые включения могут иметь размер до нескольких десятков миллиметров и поэтому являются очень опасными. Они уменьшают сечение шва и приводят к концентрации напряжений в нем.
Участок шва, на котором шлаковые включения превышают допустимые нормы, подлежит вырубке и переварке.
5. Непровар(рис.8) - несплавление основного металла по всей длине шва или на участке, возникающее вследствие неспособности расплавленного металла проникнуть в корень соединения.
Рисунок 8.Непровар в сварном соединении
В результате непровара снижается сечение шва и возникает местная концентрация напряжений, что в конечном итоге снижает прочность сварного соединения. При вибрационных нагрузках даже мелкие непровары могут снижать прочность соединения до 40%. Большие непровары корня шва могут снизить прочность до 70%.
Непровар в корне шва происходит при недостаточной силе тока или при повышенной скорости сварки, непровар кромки шва - при смещении электрода с оси стыка. Также причина образования непровара - плохая зачистка металла от окалины, ржавчины и загрязнений, малый зазор при сборке, недостаточный сварочный ток, большая скорость сварки, смещение электрода от центра стыка.
Участки с непроварами приходится вырубать до основного металла, зачищать и вновь заваривать.
Рисунок 9.Подрез в сварном соединении
7.Превышение выпуклости углового шва(рис.10)- избыток наплавленного металла на лицевой стороне углового шва (на всей длине или на участке) сверх установленного значения
Рисунок 10. Превышение выпуклости углового шва
В процессе сварки из-за неправильных режимов сварки, а также по ряду других причин (низкая скорость сварки, неудобное пространственное положение, однопроходная сварка в узкую разделку) при формировании шва избыток металла кристаллизуется в центре сварочной ванны в виде выпуклости, превышающей допустимые значения. Чрезмерную выпуклость другими словами называют превышением усиления шва.
Превышение выпуклости удаляют механическим способом - шлифовальным инструментом.
8. Наплыв(рис.11) - избыток наплавленного металла сварного шва, натекший на поверхность основного металла, но не сплавленный с ним.
Рисунок 11. Наплывв сварном соединении
Причины образования наплывов - большой сварочный ток, слишком длинная дуга, неправильный наклон электрода, большой угол наклона изделия при сварке на спуск, плохая очистка свариваемых кромок. В местах наплывов часто могут выявляться непровары, трещины и др.
Наплывы удаляют механическим способом , проверяя, нет ли в этих местах непровара.
3 БЕЗОПАСНОСТЬ ЖИЗНЕДЕЯТЕЛЬНОСТИ
3.1 Организация рабочих мест
Рабочим местом называется та часть рабочего пространства, где располагается производственное оборудование, с которым взаимодействует человек в рабочей среде.
Организация рабочего места сварщика – это обязательное условие для его правильной и безопасной работы. Данный процесс должен проходить в соответствии с санитарными правилами.
В качестве рабочего места электросварщика рассматривают участок производственной площади, который закрепляется за бригадой/конкретным рабочим и оснащается согласно требованиям технологического процесса инструментом, оборудованием, приспособлениями и принадлежностями.
Планирование рабочего места сварщика должно обеспечивать ему беспрепятственный доступ к заготовкам и безопасные условия труда. Нужно, в частности, позаботиться об отсутствии легковоспламеняющихся и взрывоопасных веществ, а сварочные баллоны должны быть достаточно удалены от открытого пламени. Рабочее место сварщика организуется по ГОСТ 12.3.003-86.
При комплектации рабочего места инструментом учитывается специфика работы. Но можно выделить определенный минимальный перечень инструментов, без которого сварщик не может полноценно работать. Стандартно рабочее место оснащено:
- сварочным аппаратом;
- металлической щеткой;
- столом и стулом сварщика;
- зубилом и молотком;
- электродержателем;
- винтовым зажимом;
- сварочной маской.
При этом не следует излишне загромождать рабочее место ненужными вещами и оборудованием, которые могут помешать работе и представлять опасность.
Сварочные работы на постах выполняются только при работающей вентиляции.
В зависимости от габаритов свариваемых изделий и характера производства рабочее место сварщика может быть расположено либо в специальной кабине(постоянное), либо в цехе или непосредственно на сборочном объекте (временное).
Организация постоянного рабочего места. Размеры кабины должны быть не менее 2x2 м2. Стены кабины делают высотой 1,8-2 м. Для лучшей вентиляции между полом к нижним обрезом стенки оставляют просвет 150-200 мм. В качестве материала для стен кабины можно использовать тонкое железо, а также фанеру, брезент, прочитанные огнестойким составом, или другие огнестойкие материалы. Каркас кабины делают из металлических труб или уголковой стали. Дверной проем кабины обычно закрывают брезентовым занавесом, укрепленным на кольцах. Фанера и брезент должны быть пропитаны огнестойким составом, например раствором алюмокалиевых квасцов.[18]
Пол в кабине должен быть из огнестойкого материала (кирпич, бетон, цемент) несгораемые и нескользкие, обладать малой теплопроводностью.
Стенки окрашивают в светло-серый цвет красками, хорошо поглощающими ультрафиолетовые лучи (цинковые или титановые белила, желтый крон). Окраска сварочных цехов и кабин в темные цвета не рекомендуется, так как при этом ухудшается общая освещенность места сварки.
По форме и размерам швы должны удовлетворять ГОСТ 5264-80, иметь гладкую или равномерно чешуйчатую поверхность (высота или глубина впадин не должна превышать 1 мм), металл шва должен иметь плавное сопряжение с основным металлом, швы не должны иметь недопустимых внешних дефектов.
К недопустимым внешним дефектам относятся: трещины любых видов и размеров, несплавления, наплывы, грубая чешуйчатость, наружные поры и цепочки пор, прожоги и свищи.
По внешним признакам контролируемый сварной шов часто сравнивают со специальными эталонами. Геометрические показатели швов определяют, используя специальные шаблоны и измерительные инструменты.
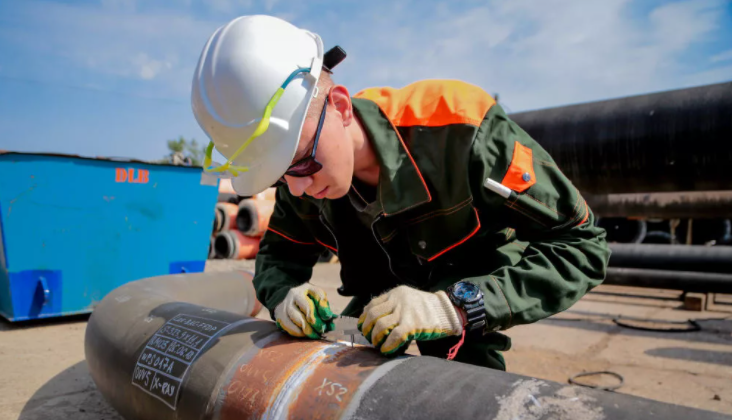
Рисунок 3.Визуальный измерительный контроль
Ультразвуковой контроль проводят после проведения визуального и измерительного контроля. Ультразвуковой контроль сварных соединений выполняют в соответствии с требованиями ГОСТ 14782-86.
Ультразвуковой контроль сварных швов — это неразрушающий целостности сварных соединений метод контроля и поиска внутренних дефектов недопустимой величины и химических отклонений от заданной нормы. Методом ультразвуковой дефектоскопии (УЗД) проводится диагностика разных сварных соединений. УЗК является действенным при выявлении воздушных пустот (трещин, непроваров, пор и т.д.), химически неоднородного состава (шлаковые включения в металле) и выявления присутствия неметаллических элементов.
Ультразвуковая технология основана на свойстве ультразвуковых волн направленно распространятся в средах и отражаться от их границ или нарушений сплошности (дефектов), обладающих другим акустическим сопротивлением
Способ контроля качества сварных соединений ультразвуком широко распространился благодаря простоте и удобству применения, относительно недорогому оборудованию, безопасности использования по сравнению с радиационным методом.
Минусом способа является трудность расшифровки графического изображения. Контроль качества соединения может сделать только сертифицированный специалист. [11]
2.4 Анализ сварочных дефектов, обнаруживаемых при сварке
Дефектов называется несоответствие параметров и характеристик сварного шва или соединения требованиям нормативно-технической документации.[12]
Различают следующие виды дефектов сварных соединений:
-наружные;
-внутренние;
При выполнении ремонта с применением сварки монорельса консольно-козлового крана могут образоваться следующие дефекты:
1.Трещины(рис.4)- дефект сварного соединения в виде разрыва в сварном шве и (или) прилегающих к нему зонах сварного соединения и основного металла.
Трещины являются недопустимыми дефектами, так как являются концентратором напряжения и очагом разрушения. Это самые опасные дефекты сварного соединения, часто приводящие к его разрушению.
Причинами образования трещин чаще всего является несоблюдение технологии и режимов сварки.
Поверхностные трещины в сварных конструкциях устраняются в следующем порядке: сначала засверливают концы трещины, чтобы она не распространялась дальше по шву, затем трещину удаляют механическим путем или строжкой, после чего место удаления дефекта зачищают и заваривают.
Внутренние трещины (как впрочем, и остальные внутренние дефекты) удаляют механическим способом или строжкой с последующей заваркой данного участка.
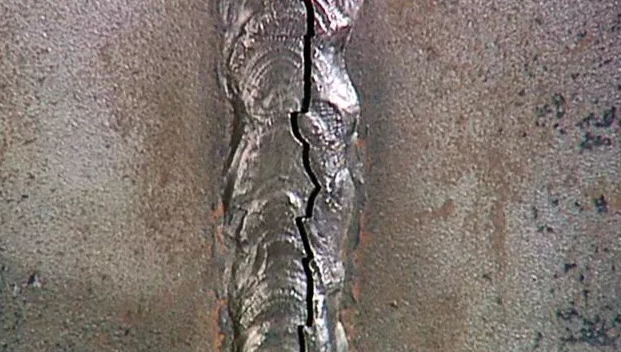
Рисунок 4. Трещина в сварном соединении
2. Поры в сварном шве(рис.5) - называют полости, заполненные газами. Возникают в жидком металле шва вследствие интенсивного газообразования, при котором не все газовые пузырьки успевают выйти наружу до затвердевания сварного шва. В сварном шве, помимо одиночных пор, могут возникать и скопления пор, а иногда даже раковины и свищи.
Наличие пористости в сварном соединении снижает механические свойства металла (прочность, ударную вязкость и т.п.), а также герметичность изделия.
Участок сварочного шва, в котором присутствуют поры, подлежит переварке с предварительной механической зачисткой или строжкой с последующей механической обработкой.
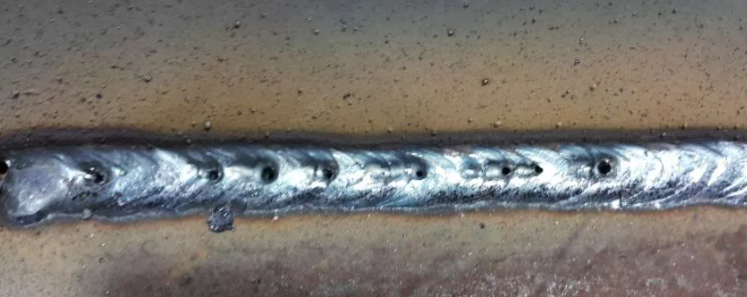
Рисунок 5.Поры в сварном соединении
3.Кратер(рис.6) - усадочная раковина в конце валика сварного шва, который образуется в виде углублений в местах резкого отрыва дуги в конце сварки. В углублениях кратера могут появляться усадочные рыхлости, часто переходящие в трещины.
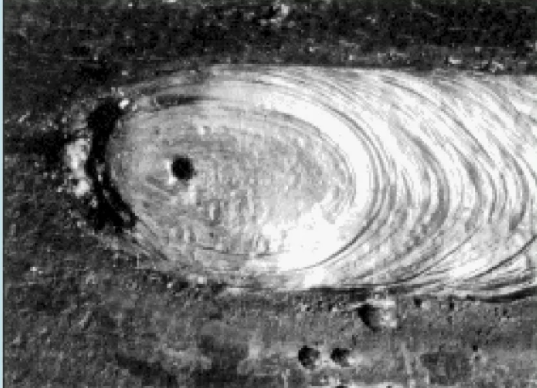
Рисунок 6.Кратер в сварном соединении
Кратеры обычно появляются в результате неправильных действий сварщика. Кратеры уменьшают рабочее сечение сварочного шва, то есть снижают его прочность. Кратеры вырубают до основного металла, зачищают и заваривают.
4.Шлаковое включение(рис.7) - шлак, попавший в металл сварного шва.
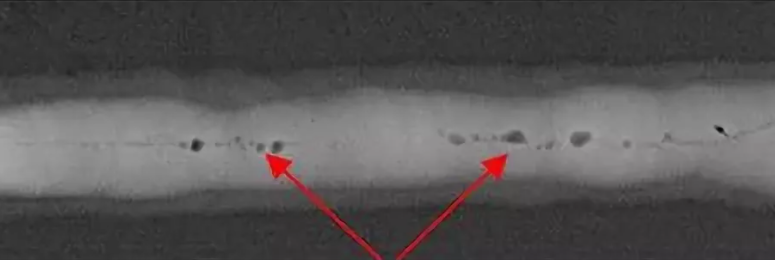
Рисунок 7.Шлаковое включение в сварном соединении
Шлак, образующийся при плавлении электродного покрытия, всегда всплывает на поверхность сварочной ванны. Шлак может оставаться внутри металла только при нарушении техники и технологии процесса (большим скорость сварки, неправильный наклон электрода, плохая зачистка ранее выполненного валика).
Шлаковые включения могут иметь размер до нескольких десятков миллиметров и поэтому являются очень опасными. Они уменьшают сечение шва и приводят к концентрации напряжений в нем.
Участок шва, на котором шлаковые включения превышают допустимые нормы, подлежит вырубке и переварке.
5. Непровар(рис.8) - несплавление основного металла по всей длине шва или на участке, возникающее вследствие неспособности расплавленного металла проникнуть в корень соединения.
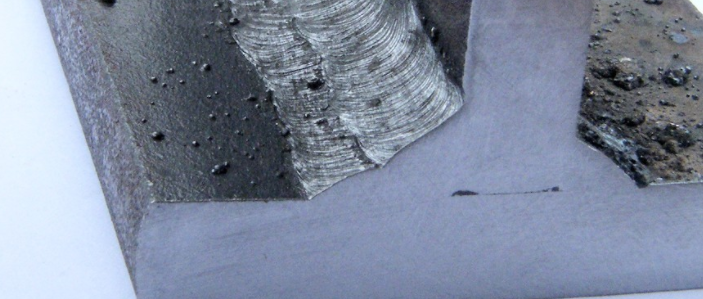
Рисунок 8.Непровар в сварном соединении
В результате непровара снижается сечение шва и возникает местная концентрация напряжений, что в конечном итоге снижает прочность сварного соединения. При вибрационных нагрузках даже мелкие непровары могут снижать прочность соединения до 40%. Большие непровары корня шва могут снизить прочность до 70%.
Непровар в корне шва происходит при недостаточной силе тока или при повышенной скорости сварки, непровар кромки шва - при смещении электрода с оси стыка. Также причина образования непровара - плохая зачистка металла от окалины, ржавчины и загрязнений, малый зазор при сборке, недостаточный сварочный ток, большая скорость сварки, смещение электрода от центра стыка.
Участки с непроварами приходится вырубать до основного металла, зачищать и вновь заваривать.
6. Подрез (рис.9) –углубление продольное на наружной поверхности валика сварного шва. При электродуговой сварке подрезы возникают при повышенном токе и напряжении дуги.
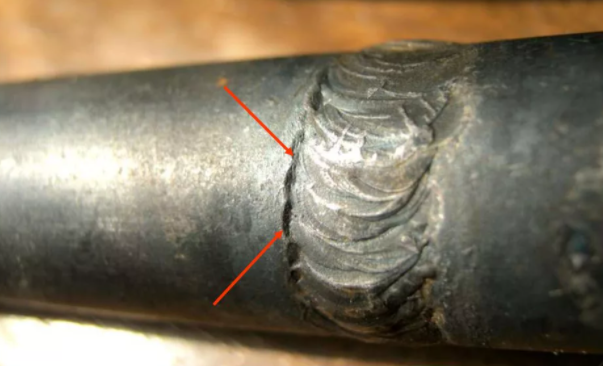
Рисунок 9.Подрез в сварном соединении
7.Превышение выпуклости углового шва(рис.10)- избыток наплавленного металла на лицевой стороне углового шва (на всей длине или на участке) сверх установленного значения
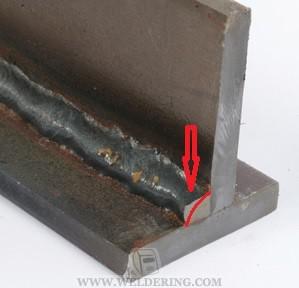
Рисунок 10. Превышение выпуклости углового шва
В процессе сварки из-за неправильных режимов сварки, а также по ряду других причин (низкая скорость сварки, неудобное пространственное положение, однопроходная сварка в узкую разделку) при формировании шва избыток металла кристаллизуется в центре сварочной ванны в виде выпуклости, превышающей допустимые значения. Чрезмерную выпуклость другими словами называют превышением усиления шва.
Превышение выпуклости удаляют механическим способом - шлифовальным инструментом.
8. Наплыв(рис.11) - избыток наплавленного металла сварного шва, натекший на поверхность основного металла, но не сплавленный с ним.
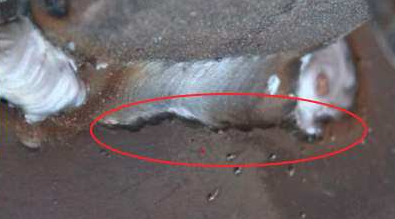
Рисунок 11. Наплывв сварном соединении
Причины образования наплывов - большой сварочный ток, слишком длинная дуга, неправильный наклон электрода, большой угол наклона изделия при сварке на спуск, плохая очистка свариваемых кромок. В местах наплывов часто могут выявляться непровары, трещины и др.
Наплывы удаляют механическим способом , проверяя, нет ли в этих местах непровара.
3 БЕЗОПАСНОСТЬ ЖИЗНЕДЕЯТЕЛЬНОСТИ
3.1 Организация рабочих мест
Рабочим местом называется та часть рабочего пространства, где располагается производственное оборудование, с которым взаимодействует человек в рабочей среде.
Организация рабочего места сварщика – это обязательное условие для его правильной и безопасной работы. Данный процесс должен проходить в соответствии с санитарными правилами.
В качестве рабочего места электросварщика рассматривают участок производственной площади, который закрепляется за бригадой/конкретным рабочим и оснащается согласно требованиям технологического процесса инструментом, оборудованием, приспособлениями и принадлежностями.
Планирование рабочего места сварщика должно обеспечивать ему беспрепятственный доступ к заготовкам и безопасные условия труда. Нужно, в частности, позаботиться об отсутствии легковоспламеняющихся и взрывоопасных веществ, а сварочные баллоны должны быть достаточно удалены от открытого пламени. Рабочее место сварщика организуется по ГОСТ 12.3.003-86.
При комплектации рабочего места инструментом учитывается специфика работы. Но можно выделить определенный минимальный перечень инструментов, без которого сварщик не может полноценно работать. Стандартно рабочее место оснащено:
- сварочным аппаратом;
- металлической щеткой;
- столом и стулом сварщика;
- зубилом и молотком;
- электродержателем;
- винтовым зажимом;
- сварочной маской.
При этом не следует излишне загромождать рабочее место ненужными вещами и оборудованием, которые могут помешать работе и представлять опасность.
Сварочные работы на постах выполняются только при работающей вентиляции.
В зависимости от габаритов свариваемых изделий и характера производства рабочее место сварщика может быть расположено либо в специальной кабине(постоянное), либо в цехе или непосредственно на сборочном объекте (временное).
Организация постоянного рабочего места. Размеры кабины должны быть не менее 2x2 м2. Стены кабины делают высотой 1,8-2 м. Для лучшей вентиляции между полом к нижним обрезом стенки оставляют просвет 150-200 мм. В качестве материала для стен кабины можно использовать тонкое железо, а также фанеру, брезент, прочитанные огнестойким составом, или другие огнестойкие материалы. Каркас кабины делают из металлических труб или уголковой стали. Дверной проем кабины обычно закрывают брезентовым занавесом, укрепленным на кольцах. Фанера и брезент должны быть пропитаны огнестойким составом, например раствором алюмокалиевых квасцов.[18]
Пол в кабине должен быть из огнестойкого материала (кирпич, бетон, цемент) несгораемые и нескользкие, обладать малой теплопроводностью.
Стенки окрашивают в светло-серый цвет красками, хорошо поглощающими ультрафиолетовые лучи (цинковые или титановые белила, желтый крон). Окраска сварочных цехов и кабин в темные цвета не рекомендуется, так как при этом ухудшается общая освещенность места сварки.