Файл: Объем информации, получаемой административноуправленческим аппаратом промышленного предприятия, так велик, что для качественного управления необходимо широкое использование современных средств автоматизации.docx
ВУЗ: Не указан
Категория: Не указан
Дисциплина: Не указана
Добавлен: 06.12.2023
Просмотров: 54
Скачиваний: 1
ВНИМАНИЕ! Если данный файл нарушает Ваши авторские права, то обязательно сообщите нам.
Несконденсированный контактный газ из холодильника поз. Т‑210А направляется на вторую ступень конденсации в конденсатор поз. Т‑211, где охлаждается антифризом температурой минус 12 оС. Конечная температура конденсации составляет 5 оС. Для охлаждения и конденсации контактного газа схемой предусмотрена подача обратного антифриза.
Несконденсированный контактный газ из конденсатора поз. Т‑211 через сепаратор поз. Е‑212 поступает на всас компрессора поз. М‑213. Для исключения возможного залива сепаратора поз. Е‑212 водно‑углеводородным конденсатом схемой предусмотрен постоянный его слив в отстойник поз. Е‑218.
Несконденсированный газ, сжатый компрессором поз. М‑213 до давления 0,12 МПа, поступает на третью ступень конденсации в холодильник поз. Т‑214, где охлаждается оборотной водой и поступает на четвертую ступень конденсации в конденсатор поз. Т‑216.
В конденсаторе поз. Т‑216 несконденсированный контактный газ охлаждается и конденсируется подачей антифриза. Температура антифриза минус 12 оС. Конечная температура конденсации 5 оС. Схемой предусмотрена возможность подачи обратного антифриза для охлаждения и конденсации несконденсированного газа.
Несконденсированный газ после конденсатора поз. Т‑216 поступает в сепаратор поз. Е‑291 предназначенный для отделения из несконденсированного газа воды и углеводородов.
Несконденсированный газ после сепаратора поз. Е-291 поступает в колонну поз. К-290.
Колонна поз. К‑290, работающая под избыточным давлением предназначена для улавливания ароматических углеводородов из несконденсированного газа абсорбентом.
Несконденсированный газ из колонны поз. К‑290 через сепаратор поз. Е‑200С и теплообменник поз. Т‑200D направляется в качестве топлива в пароперегревательную печь поз. П‑201А, В. Схемой предусмотрена возможность сброса несконденсированного газа после сепаратора поз. Е‑200С на факел.
Выделенный конденсат после конденсаторов поз. Т‑210, Т‑211, Т‑216 и холодильников поз. Т‑210А, Т‑214 поступает в отстойник поз. Е‑218, где происходит отстой и разделение водно‑углеводородного конденсата на углеводородный и водный слой.
Углеводородный слой из отстойника поз. Е‑218 непрерывно откачивается насосом поз. Н‑220.1,2 на склад пром. продуктов в резервуар поз. Е‑417 объекта 1808.
Откачка водного конденсата из отстойника поз. Е-218 осуществляется насосом поз. Н‑222.1,2 по уровню раздела фаз.
Для предотвращения полимеризации стирола предусмотрено ингибирование контактного газа и углеводородного конденсата. Раствор ингибитора подается в две точки:
-
в трубопровод контактного газа перед конденсатором поз. Т‑210; -
в трубопровод всаса насоса поз. Н‑220.1,2.
Для опорожнения аппаратов, насосов и трубопроводов отделения дегидрирования предусмотрена подземная емкость поз. Е‑235, из которой углеводороды погружным насосом поз. Н‑235А периодически откачиваются в отстойник поз. Е‑218. Отдувки из отстойника поз. Е‑218 направляются в конденсатор поз. Т‑211 на конденсацию.
Опорожнение конденсаторов поз. Т‑211, Т‑216, теплообменника поз. Т‑298, теплоспутников, насосов, термосифонов от антифриза осуществляется в подземную емкость поз. Е‑391.
Для сбора атмосферных вод предусмотрена подземная емкость поз. Е‑260.1, из которой они погружным насосом поз. Н‑260.1А в зависимости от результата анализа, откачиваются в отстойник поз. Е-218 или в канализацию растворенной органики (Р.О), или в промышленно-ливневую канализацию.
При пуске отделения дегидрирования разогрев катализатора в реакторах осуществляется горячим азотом н.д. Азот н.д. из сети подается для нагрева в пароперегревательную печь поз. П‑201А. Предусмотрена возможность циркуляции азота в системе дегидрирования вакуум‑компрессором поз. М‑213 после разогрева катализатора в реакторах поз. Р‑202.1,2 от теплообменника поз. Т‑200D в линию подачи водяного пара в змеевики печи поз. П‑201А.
Температура в реакторах во время проведения термообработки не должна превышать 600 оС.
Охлаждение катализатора до температуры (250300) оС осуществляется водяным паром, и азотом, со скоростью не более 30 оС/ч до 40 °С.
2.2 Физико-химические процессы в ТОУ
Основным промышленным способом получения стирола является дегидрирование этилбензола. Процесс каталитического дегидрирования этилбензола в стирол осуществляется в адиабатических реакторах, заполненных железоокисным катализатором, в присутствии водяного пара по уравнению реакции:
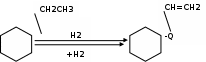


С6Н5С2Н5 → С6Н5С2Н3 + Н2
этилбензол стирол водород
Для протекания реакции необходимо подвести тепло, поскольку реакция эндотермична (тепловой эффект 30 ккал/моль).
Под воздействием высоких температур в некаталитических зонах по свободно‑радикальному механизму возможно образование следующих основных примесей, наличие которых может повлиять на качество товарного стирола:
С6Н5С2Н3 → С6Н5С2Н + Н2
стирол фенилацетиленводород
С6Н5С2Н3 → С6Н5С2Н5 + (С6Н5)2 + С6Н5С2Н2С6Н5
стирол этилбензол дифенил стильбен
С6Н5С2Н3 →С6Н5С2Н5 + С6Н4(С2Н5)2
стирол этилбензол диэтилбензол
С2Н3С6Н4С2Н5 → С6Н5(С2Н3)2 + Н2
этилстирол дивинилбензол водород
С6Н5С2Н3 + Н2О →С6Н5С2Н3О + Н2
стирол вода ацетофенонводород
Вследствие того, что реакция идет с увеличением объема, на показатели процесса благоприятно сказывается понижение парциального давления – при этом повышается равновесная степень превращения этилбензола.
Технологически эти условия выполняются за счет использования в процессе перегретого водяного пара и осуществления процесса дегидрирования под вакуумом. Кроме того, водяной пар непрерывно удаляет с катализатора углерод, образующийся в процессе реакции.
Применение катализатора позволяет увеличить скорость основной реакции и обеспечить высокую избирательность процесса дегидрирования при достаточно глубокой конверсии этилбензола в стирол.
Необходимо учитывать отрицательное влияние хлора и серосодержащих соединений на железоокисный катализатор. Массовое содержание хлора и серы в этилбензольной шихте не должно превышать 0,0002 % соответственно.
При прочих равных условиях (температура, катализатор и т.п.) понижение давления в зоне реакции от избыточного до вакуума позволяет увеличить степень превращения этилбензола в стирол.
Суммарное действие водяного пара, эффективного катализатора, а также снижение избыточного давления в зоне реакции позволяет достигнуть высоких показателей процесса.
Так, снижение давления в зоне реакции на 0,01 МПа дает увеличение селективности процесса до 0,4 %, а конверсии до 0,6 %.
Дегидрирование этилбензола осуществляется под вакуумом в двухступенчатом адиабатическом реакторе с промежуточным подогревом контактного газа. Тип реактора – радиальный с центральной подачей потока. Для выравнивания скорости во входном канале предусмотрено тело вращения заданного профиля. На входе в первую ступень реактора предусмотрен эффективный статический смеситель (типа SMV фирмы «Зульцер», Швейцария), обеспечивающий температурный градиент не более 2
оС.
Условия проведения процесса:
-
температура (580645) оС на входе в слои катализатора; -
объемная скорость подачи этилбензольной шихты в пределах (0,230,45) ч‑1; -
давление (0,045÷0,075) МПа (0,45÷0,75) кгс/см2абс.
Подогрев контактного газа, поступающего во вторую ступень реактора, производится в межступенчатом подогревателе кожухотрубчатого типа, который обогревается перегретым водяным паром, поступающим из печи поз. П‑201А.
Количество водяного пара подаваемого в испаритель поз. Т-204 на смешение с этилбензольной шихтой составляет не менее 10% от массы этилбензольной шихты, поступающей в процесс.
2.3 Анализ параметров, подлежащих контролю, регулированию, сигнализации и защите
Определяющим технологическим параметром установки стирола отделения дегидрирования этилбензола является температура в реакторах Р-202.1,2 во время проведения термообработки, которая не должна превышать 600 оС. Для этого необходимо контролировать температуру внутри колонн с помощью многозонных термопар типа ХА (поз. 1а, 2а, 6а и 11а). А также необходимо регулировать температуру на входе путем подачи перегретого водяного пара в колонны, проходя через подогреватель Т-202А.На входе в реакторы установлены термопары типа ХА(поз. 3а, 5а), сигнал с которых уходит в систему АСУТП, и после, на пневматический регулирующий клапан(поз. 3б, 5б).Аналогичные системы установлены в теплообменнике Т-298, в конденсаторах Т-210, Т-211, Т-216, в холодильниках Т-210А, Т-214
Испарение этилбензольной шихты осуществляется в испарителе Т-204 путем подачи водяного пара. Для этого необходимо контролировать максимальный и минимальный уровень паро-этилбензольн6ой шихты в испарителе Т-204, сигнализировать его и регулировать за счет подачи водяного пара. Поэтому в испарителе установленыультразвуковые уровнемеры (поз. 28а, 28б).А так же, необходимо регулировать подачу этилбензольной шихты и водяного пара в испаритель Т-204. Для этого на линии подачи этилбензольной шихты установлена камерная диафрагма (поз. 26а). Аналогичная система регулирования и сигнализирования уровня установлена в котле-утилизаторе Е -205А/Т -205, в колонне К -290, в конденсаторе Т -216.
Колонна К‑290, работающая под избыточным давлением 0,1 МПа, предназначена для улавливания ароматических углеводородов из несконденсированного газа абсорбентом. В качестве абсорбента используется этилбензольная шихта, которая отбирается из трубопровода этилбензольной шихты к испарителю Т‑204, охлаждается до температуры (2÷16)
оС в теплообменнике Т‑298 и поступает в колонну. Для протекания процесса в колонне К-290 необходимо контролировать перепад давления в колонне, расход несконденсированного газа на выходе и его температуру, и регулировать эти параметры путем подачи этилбензольной шихты. Поэтому в колонне установлены система регулирования перепада давления (поз. 46),система регулирования расхода несконденсированного газа (поз.47), система регулирования температуры несконденсированного газа (поз. 50).
Сепаратор Е-291 предназначен для отделения из несконденсированного газа воды и углеводородов. Водно-углеводородный конденсат из сепаратора выводится в отстойникЕ-218, поэтому необходимо регулировать и сигнализировать уровень в сепараторе. Для этого в сепараторе установлен ультразвуковой уровнемер (поз. 51а).
В конденсаторе Т-216 несконденсированный контактный газ охлаждается и конденсируется. Конечная температура конденсации 5оС. Для конденсации необходима подача антифриза, температуру которого необходимо регулировать. Температура измеряется с помощью термопары (поз. 84а), установленная на линии вывода несконденсированного контактного газа.
Подача сырья, поступающего в насосы Н-224.1,2, Н-222.1,2, Н-220.1,2 сигнализируется для предотвращения аварийных ситуаций, а так же сигнализируется и блокируется температура в подшипниках насосов.
2.4 Описание предлагаемых систем контроля и регулирования
Температура кипения этилбензольной шихты, поступающей с объекта 1808, в испаритель Т-204 может зависеть от её начальных параметров и от количества водяного пара, подаваемого в испаритель Т-204 для смешения с этилбензольной шихтой. Водяной пар подается в испаритель Т-204 пятью потоками. Вторичный водяной пар давления 0,4МПа, вырабатываемый в котле-утилизаторе Е-205А/Т-205, подается четырьмя потоками на смешение с этилбензольной шихтой в нижнюю часть испарителя Т-204, а пятый поток вторичного водяного пара подается до испарителя Т-204. Количество водяного пара подаваемого в испаритель Т-204 должно составлять не менее 10% от массы этилбензольной шихты, поступающей в процесс. За счет подачи водяного пара снижается температура кипения этилбензольной шихты.
Для обеспечения стабильности температуры кипения необходимо поддерживать количество водяного пара, подаваемого в испаритель Т-204.