Файл: Объем информации, получаемой административноуправленческим аппаратом промышленного предприятия, так велик, что для качественного управления необходимо широкое использование современных средств автоматизации.docx
ВУЗ: Не указан
Категория: Не указан
Дисциплина: Не указана
Добавлен: 06.12.2023
Просмотров: 52
Скачиваний: 1
ВНИМАНИЕ! Если данный файл нарушает Ваши авторские права, то обязательно сообщите нам.
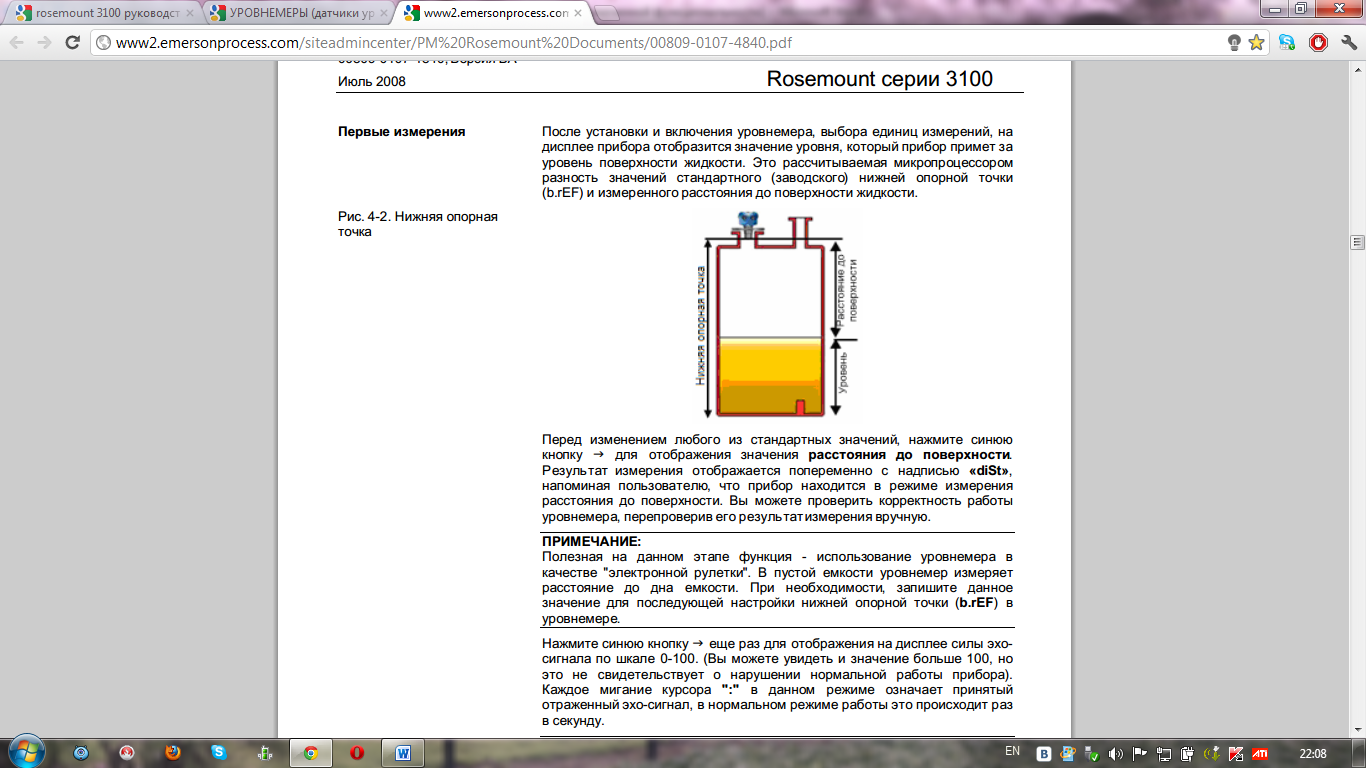
Рисунок 10 –Установка датчика
Перед изменением любого из стандартных значений, нажмите синюю
кнопку g для отображения значения расстояния до поверхности. Результат измерения отображается попеременно с надписью «diSt», напоминая пользователю, что прибор находится в режиме измерениярасстояния до поверхности. Вы можете проверить корректность работы уровнемера, перепроверив его результаты измерения вручную.
Для изменения значения нижней опорной точки выполните следующие
действия:
a) При входе в меню с режима отображения результатов измерений, нажмите зеленую кнопку i для отображения меню настройки «b.rEF» (см. примечание выше).
b) Нажмите синюю кнопку g для входа в меню «b.rEF». На дисплее
отобразится текущее значение параметра «b.rEF».
c) Если значение корректно, нажмите красную кнопку 8 , а затем
зеленую кнопку i для перехода к следующему параметру меню.
d) Для изменения значения нажмите синюю кнопку g. Первая цифра на
дисплее замигает, указывая на возможность ее изменения.
e) Нажимайте зеленую кнопку i до тех пор, пока не установится нужное
значение.
f) Нажмите синюю кнопку g для перехода к следующей цифре. Цифра
на дисплее замигает, указывая на возможность ее изменения.
g) Повторите шаги e) и f) для установки всех требуемых значений.
h) Нажмите синюю кнопку g для подтверждения нового значения
«b.rEF». При этом ни одна из цифр не должна мигать.
i) Если введенное значение верно, нажмите красную кнопку 8 для
сохранения настроек. На дисплее отобразится следующий параметр меню.
j) Если введенное значение неверно, нажмите синюю кнопку g для
выхода из меню. После того, как меню «b.rEF» отобразится снова,
начните с шага или нажмите зеленую кнопку i для отображения следующего параметра меню.
3 Расчетная часть
3.1 Выбор способа прокладки электрических и трубных проводок. Выбор электрических и трубных проводок.
На установке дегидрирования этилбензола используются следующие электрические проводки: ПТГВ 2×2,5 ХА и КВВГЭ 4×1,5.
Контрольные проводки предназначены для подводки питания к приборам, расположенным в операторной. Выбор осуществляется в соответствии с помещением, в котором прокладывается проводка. Исходя из этого, используются проводки марки КВВГЭ с медной жилой,
изоляция из резины, этот кабель прокладывается внутри пожароопасных помещений, в каналах, в туннелях, в условиях средне агрессивной среды при отсутствии механических воздействий на кабель. С сечением жил 1,5 мм2 и наружным диаметром 4 мм которые прокладывают в короб сечением 200 мм. При этом жилы кабелей в зависимости от конструкции выводов и зажимов приборов, аппаратов и сборок зажимов оконцовываются кольцом или штырем; концы многопроволочных жил (кольца, штыри) пропаиваются, штыревые концы могут спрессовываться штифтовыми наконечниками.
В качестве термоэлектрических проводов используют провода марки ПТГВ с сечением жил 2 мм2 и наружным диаметром 2,5 мм2 , которые прокладываются от датчиков в защитных трубах Ц-Р-20×2 до общего короба со всеми проводками и тянется в операторную, где укладывается в короб.
Для измерения давления, расхода применяются бесшовные импульсные трубные проводки из стали 10, наружным диаметром 6 мм и толщиной стенки 1 мм.
Для проводки защитной трубы от датчиков до операторной используют стальную водогазопроводную трубу Ц-Р-20×2.
3.2 Выбор элементов монтажа электрических и трубных проводок
Для закрепления первичных преобразователей температуры и ввода их чувствительных элементов в измеряемую среду являются бобышки (рисунок 11), которые устанавливаются на технологическом оборудовании и трубопроводах.
Для установки уровнемеров применяют кронштейны К-1 – К-3 по ТК4-3459-74 (рисунок 12) и стойки СТ по ТК4-3450-74.
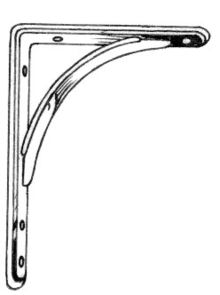
Рисунок 12- Кронштейн
Для укладки проводов используются:
- короба прямые (для прямых участков трассы), масса 14,1 кг. Установка осуществляется по ТМ3-61-78;
- короба угловые (для изменения направления трассы в горизонтальной плоскости), масса 2,4 кг. Устанавливается по ТМ3-65-78;
- полки – для укладки на них проводов, лотков, коробов К1170У3
Для крепления коробов и проводов используются:
- скоба У1059У3 используется для крепления коробов 200х200 мм;
- вводные патрубки У476У3.
- хомутики С437У2 на хомутах или опоре;
- протяжные кабели У272УХП3
3.3 Расчет регулирующего органа и выбор исполнительного механизма
Расчет РО (поз.29а) для регулирования расхода пара
Данные для расчета:
-
среда – пар -
максимальный расход пара Gмакс = 40000 кг/ч=17777,8 м3/ч -
минимальный расход пара Gмин = 3000 кг/ч=1333,3 м3/ч -
давление пара в магистрали Ро= 0,5 МПа -
давление в реакторе Ри = 0,1 МПа -
температура пара Т = 205 0С -
внутренний диаметр трубопровода D = 250 мм
Трубопровод имеет два поворота под углом 900 с радиусом изгиба 0,5 м; на паропроводе установлена запорная задвижка.
Разность высот начального и конечного участков Δh = -10,5 м
Расчет:
а) По таблице пара при Р0 = 0,5 МПа и Т =205 0С находим:
Динамическая вязкость η = 1,65×10-6 кгс/см2
Показатель адиабаты ς = 1,31
Плотность пара ρпара= 2,25 кг/м3
б) Определяем гидростатический напор, соответствующий разности уровней верхней и нижней отметок трубопровода.
ΔРг= Δh∙ρпара , (1)
где Δh – разность высот начального и конечного участка
ρпара – плотность пара
ΔРг =-10,5∙2,25= -23,625 кгс/м2= -0,00023 МПа
ΔРсети= Р0–Рр-ΔРг(3)
где Р0 – давление пара до СУ
Ри – давление после СУ
ΔРг – гидростатический напор
ΔРсети =0,5-0,1+0,00023= 0,4 МПа
Определяем число Рейнольдса при Gмакс:
Red= 36,1∙10-3∙Gмакс/(D∙η), (2)
Где Gmax – максимальный расход пара
D – внутренний диаметр трубопровода
η – динамическая вязкость пара
Red =36,1∙10-3 ∙17777,8/(250∙1,58∙10-6) = 1,6∙106
Определяем условие гидравлической гладкости трубопровода:
Red<27(D/n1)8/7, (3)
где n1 – шероховатость трубопровода, n1 = 0,1 мм
D – внутренний диаметр трубопровода
Red = 27∙(250/0,1)8/7 = 2∙105
Так как трубопровод в данном случае не является гидравлически гладким, то коэффициент трения λ зависит от Red и D/n1, выбираем λ =0,016
Суммарная длина трубопровода
L=10+7+3,5+0,75+2∙(2∙3,14/4)∙0,5 = 22,82 м
Находим среднюю скорость в трубопроводе при максимальном расчетном расходе:
Vмакс = Gмакс∙4/( ρпара ∙π∙D2∙3600), (4)
где, Gmax – максимальный расход пара
ρпара – плотность пара
D – внутренний диаметр трубопровода
Vмакс = 17777,8∙4/(2,25∙3,14∙0,22∙3600) = 69,9 м/с
Находим потерю давления на прямых участках трубопровода:
ΔРпр=λ∙(ρпара∙L∙V2/2∙D), (5)
где λ – коэффициент трения
ρпара – плотность пара
L – длина трубопровода
V – скорость в трубопроводе
ΔРпр = 0,016∙2,25∙22,82∙69,92/(2∙0,25*106) =0,008 МПа
Определяем потери давления в местных сопротивлениях трубопровода:
ΔРм=(ξвх+ξвых+3∙ξ900+ξзд
)∙ρпара ∙V2/2, (6)
По таблицам определяем ξвх=0,5, ξвых=1,0, ξ900=0,66,ξзд=0,08 тогда:
ΔРм=(0,5+1,0+2∙0,66+0,08)(69,92∙2,25)/2*106=0,016МПа
Общие потери давления в линии
ΔРл= ΔРпр+ ΔРм, (7)
где ΔРпр– потеря давления на прямых участках трубопровода
ΔРм – потери давления в местных сопротивлениях трубопровода
ΔРл = 0,008+0,016 = 0,024 МПа
в) Определяем перепад давления в РО при максимальном расчетном расходе пара:
ΔРРО макс = ΔРсети– ΔРл, (8)
Где ΔРсети – давление сети
ΔРл – общие потери давления в линии
ΔРРО макс = 0,4-0,024 = 0,376 МПа
Очевидно, что при очень малых расходах потери давления в линии являются пренебрежимо малой величиной и перепад давления на РО:
ΔРРО мин = Р0– Ри, (9)
где Р0– давление пара до СУ
Рр – давление после СУ
ΔРРО мин =0,5-0,1=0,4 МПа.
Таким образом, перепад на РО практически остался неизменным.
г) Так как ΔРРО/Р0>0,5, то находим максимальную пропускную способность РО:
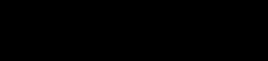
где Gмакс – максимальный расход пара
Р – давление пара до СУ
ρпара – плотность пара
Т – температура
k – коэффициент отклонения

д) Выбираем односедельный РО с условной пропускной способностью Кυ у =320 м3/ч > 1,2Кυ макс = 305,76 м3/ч с Dу = 150 мм
е) Определяем отношение перепада давления в линии к перепаду давления на РО при максимальном расходе:
ΔРл/ ΔРРО=0,024/0,376=0,063≈0 (11)
ж) Так как по условию расходная характеристика должна быть линейной, то при n=0 следует выбрать РО с линейной пропускной характеристикой.
з) Определяем максимальный расход для выбранного РО:
G‘макс= Gмакс * Кυ у / К у макс , (12)
где Gмакс - максимальный расход пара
Кυ у - пропускная способность табличная
К у макс – пропускная способность расчётная
G‘макс = 17777,8 * 320/ 254,8= 22326,9 кг/ч
и) Определяем относительные значения расходов:
μ макс = 17777,8/22326,9 = 0,79;
μ мин = 1333,3/22326,9 = 0,06;
к) Определяем диапазон перемещений затвора РО с линейной характеристикой при n = 0:
ΔS = μ макс – μ мин , (13)
ΔS = 0,79 – 0,06 = 0,73
Вывод: на основе данного расчета выбираем клапан регулирующий пневматический SAMSON типа 3222, Ду= 150 мм.
4 Охрана окружающей среды
На данном предприятии соблюдаются нормы и требования по выбросу вредных веществ в атмосферу. Выявление возможностей возникновения аварий осуществляется на основе:
- действующих норм и правил по безопасности эксплуатации рассматриваемого объекта;
- сведения о производственных авариях и инцидентах;
- анализа деятельности эксплуатируемого и ему подобного объектов на предприятии;
- сведений об авариях на предприятиях родственных отраслей промышленности;
- информационных материалов Госгортехнадзора России, и т.д.
Оценка последствий включает анализ возможных последствий аварий на людей, имущество и окружающую среду. При оценке воздействия последствий аварии на окружающую среду необходимо определить: вероятность выброса вредных веществ в атмосферу и его последствия (пожар, взрыв, загазованность); вероятность попадания вредных веществ в водоем и его последствия; вероятность и последствия разлива продукта.
В нефтехимических производствах аварии сопровождаются взрывами, пожарами и выбросами больших масс токсичных продуктов, что может привести к поражению людей, разрушению зданий и оборудования и нанесению ущерба окружающей среде и блокировки, в результате происходит остановка. Поэтому при возникновении аварийной ситуации происходит срабатывание систем сигнализации блока и сброс продукта в атмосферу по средствам его сжигания. Для предотвращения воздействия продукта и отравления им рабочих, на каждом из участков предусмотрены средства индивидуальной защиты (СИЗ), системы вентиляции помещений, ящики с песком, огнетушители и т.д.
4.1 Анализ отходов и выбросов
На установке при производстве стирола образуются следующие отходы:
-
Твердые и жидкие отходы: отработанный катализатор дегидрирования марки КДЭ и отработанное масло марок Shell clavius, ESSО Teresso, И-40А, И-50А. Отработанный катализатор реализуется через УМТС потребителям и/или на рекультивацию полигона площадки «Д». А масло вывозится на площадку «Г» для компаундирования с мазутом и/или в цех №13 для компаундирования с нефтью или реализуется потребителям. Периодичность образования отходов раз в 3 года, катализаторов раз в 2 года. При утилизации, перед выгрузкой проводится регенерация, затем отправляется на завод втордрагметаллов. -
Сточные воды: атмосферные осадки от насосов направляются в емкость Е‑218 и/или на очистные сооружения и сбрасываются в канализацию растворимой органики, колодец РО-12. Выбросы производятся периодически; паровой конденсат защиты печи П-201 направляется на очистные сооружения и сбрасывается в ливневую канализацию, колодец ЛК-18. Выбросы происходят непрерывно. -
Выбросы в атмосферу: метан, этилен, бензол, толуол, этилбензол, стирол из-за неплотности оборудования; диоксид азота, оксид азота, углерод оксид, сернистый ангидрид из дымовой печи П-201; стирол, этилбензол из воздушки на емкости Е-235; этиленгликоль из воздушки на емкости Е-391. Выбросы производятся непрерывно.