Файл: Учебный курс для студентов очной и заочной форм обучения.doc
ВУЗ: Не указан
Категория: Не указан
Дисциплина: Не указана
Добавлен: 11.12.2023
Просмотров: 902
Скачиваний: 6
ВНИМАНИЕ! Если данный файл нарушает Ваши авторские права, то обязательно сообщите нам.
Технологические процессы различных способов сварки и область их применения рассматриваются в курсе «Технология металлов и конструкци онные материалы».
Сварным соединением называют неразъемное соединение деталей с помощью сварных швов. Если в заклепочном соединении соединяющим эле ментом является заклепка, то в сварных - расплавленный металл, создаю щий при остывании неразъемное соединение, то есть такое, которые не может быть разобрано без повреждения дета лей. Сварные соединения лучше других приближают составные детали к целым и позволяют изготавливать детали неограниченных размеров. Прочность сварных соединений при статических и ударных нагрузках доведена до прочности деталей из целого металла. Освоена сварка всех конструкционных сталей, включая высоколегированные, цветных сплавов и пластмасс.
Масса сварных конструкций при тех же габаритах значительно меньше клепаных (на 15%). Экономия металла достигается за счет использова ния полной площади сечения, а также возможности более рационального конструирования (например, применения стыковых соединений в тех слу чаях, когда при заклепочном соединении приходится применять накладки).
Достоинства и недостатки сварных соединений по сравнению с за клепочными (или литыми деталями).
Достоинства:
- простота конструкции сварного шва и меньшая трудоемкость в изго товлении, обусловленной сравнительной простотой технологического процесса сварки.
- значительное снижение массы конструкции при тех же габаритах. При замене заклепочных соединении сварными экономия в весе получается за счет отказа от применения различных накладок, необходимых в заклепочных соединениях, а также части веса са мих заклепок; при замене литых деталей сварными конструкциями вес их уменьшается за счет более высоких механических свойств прокатного металла.
- возможность соединения деталей любых форм;
- герметичность и плотность соединения;
- бесшумность технологического процесса сварки;
- возможность автоматизации сварочного процесса;
- сварное соединение дешевле заклепочного.
- соединение деталей может выполняться встык без накладок.
- возможность сварки толстых профилей.
Недостатки:
- возникновение остаточных напряжений в свариваемых элементах;
- коробление деталей из-за неравномерного нагрева в процессе сварки;
- зависимость качества шва от исполнителя и труд ность контроля; применение автоматической сварки устраняет этот недостаток.
- склонность к образованию трещин в местах перехо да от шва к цельному металлу вследствие термических напряже ний, возникающих при остывании. Трещины особенно опасны при динамических нагрузках (вибрационных и ударных), поэтому в таких случаях сварные швы стараются не применять, заменяя их заклепочными соединениями. Термические напряжения могут быть частично или полностью устранены термообработкой сварного соединения (низкотемпера турным отжигом). Термическая обработка исключает также последующее коробление сварных конструкций.
Область применения. В настоящее время сварные соединения поч ти полностью вытеснили заклепочные соединения. Сварка применяется для соединения элементов сосудов, испытывающих дав ление (резервуары, котлы); для изготовления турбин, до менных печей, мостов, химической аппаратуры; с помо щью сварки изготовляют станины, рамы и основания машин, корпуса редукторов, зубчатые колеса (рис.2), шкивы, звездочки, маховики, барабаны и т. д. Сварку широко применяют как способ получения заготовок деталей из проката в мелкосерийном и единичном производстве, а также в ремонтном деле.
Рис. 2
Классификация и разновидности сварных соединений (швов)
Классификация.
Сварные швы классифицируют по следующим признакам:
- по назначению — прочные (обеспечивают передачу нагрузки с одно го элемента на другой); прочно-плотные (обеспечивают передачу на грузки герметичность соединения — непроницаемость для жидкостей и газов);
- по расположению сварного шва в пространстве (рис. 3) — нижнее (а); вертикальное (в), горизонтальное (б); потолочное (г). При всех прочих равных условиях нижний шов самый прочный, потолоч ный — наименее прочный (значения прочности указанных выше швов относятся как 1:0,85; 0,9:0,8).
Рис. 3
По взаимному расположению свариваемых элементов различают сле дующие виды соединений
- стыковые (рис.4);
- нахлесточные, ло бовые (рис. 5, а);фланговые (рис. 5, б);
- с накладками (рис. 6);
- тав ровые (рис. 7, а, б). Свариваемые элементы располагаются во взаимно перпендикулярных плоскостях. Соединение может быть выполнено угловыми (рис.7, а) или стыковыми (рис. 7, б) швами.
- угловые (рис. 7 в, г). Применяются для изготовления тары из листовой стали, ограждений и др. Выполняются угловыми швами. Эти соединения передают малые нагрузки и поэтому не рассчитываются на прочность.
Рис.4. Стыковое соединение
Рис. 5. Нахлесточное соединение: а — соединение лобовыми швами;
б — соединение фланговыми швами
Рис. 6. Соединения с накладками
Рис. 7. Соединения тавровые и угловые
Стыковые соединения выполняют так называемыми стыковыми шва ми, а остальные — угловыми.
Конструкции стыковых швов.
Стыковые швы имеют преимущественное распространение вследствие простоты конструкции. В зависимости от толщины свариваемых деталей и обработки кромок стыковые швы делят на следующие типы:
- шов с отбортовкой кромок (рис. 8, а) — рекомендуется для тонко листовых материалов (8 < 2 мм); одна или две кромки деталей отбортовываются;
- односторонний без скоса кромок (рис. 8, б) — шов сваривается без обработки кромок листов при их толщине 8 < 8 мм;
- односторонний со скосом одной кромки (рис. 8, в) — обрабатыва ется только одна кромка деталей толщиной 8 < 12 мм;
- односторонний со скосом двух кромок (рис. 8, г) — применяется при толщине деталей 8 < 25 мм;
- двусторонний с двумя симметричными скосами одной кромки (рис. 8, д) — кромки обрабатываются у одной детали с двух сто рон, толщиной 8 до 40 мм;
- двусторонний с двумя симметричными скосами двух кромок (рис. 8, е) — толщина свариваемых деталей 8 >> 60 мм.
Рис. 8. Соединения стыковые:
а — с отбортовкой;
б — без скоса кромок; в, г, д, е — швы со скосом кромок
Стыковые швы, показанные на рис.9, а, называют прямыми, на рис.9, б — косыми. Косые стыковые швы применяют для увеличения рабочей длины шва.
Рис.9. Стыковые швы: а — прямой; б — косой
Конструкция угловых (валиковых) швов.
Угловые швы применяют в нахлесточных соединениях, в соединениях снакладками, в тавровых и угловых соединениях. По своей прочности они уступают стыковым швам.
По профилю поперечного сечения угловые швы могут быть:
- нормальные (рис.10, а); катет шва принимается равным толщине листа (К= 5);
- вогнутые (рис.10, б) с катетом шва К= 0,85;
- выпуклые (рис.10,в);
- специальные (рис.10, г); их профиль представляет неравнобедренный прямоугольный треугольник (один из катетов K=δ).
Рис.10. Типы угловых швов: а — нормальный;
б — вогнутый; в — выпуклый; г — специальный
Вогнутые швы применяют в особо ответственных конструкциях при переменных нагрузках, так как вогнутость обеспечивает плавный переход шва в основной металл детали, благодаря чему снижается концентрация напряжений. Вогнутый шов повышает стоимость соединения, так как требует глубокого провара и последующей механической обработки для получения вогнутости, выпуклые - вызывают повышен ную концентрацию напряжений. Наиболее приемлем нормальный профиль углового шва. Специальные швы применяют при переменных нагрузках, так как значительно снижает концентрацию напряжений.
По расположению шва относительно действующей нагрузки угловые швы конструктивно разделяют на:
- лобовые, расположенные перпендикулярно к линии действия нагруз ки F (см. рис.5, а); длина лобовых швов не ограничивается;
- фланговые, расположенные параллельно линии действия нагрузки F (см. рис.5, б); максимальная длина флангового шва принимается lш = (50...60)К;
- комбинированные, состоящие из лобовых и фланговых швов.
Нахлесточные соединения и соединения с накладками сваривают уг ловыми швами.
По своей прочности нахлесточные соединения уступают стыковым. Их применяют, когда по конструктивным соображениям стыковые швы применить невозможно. Соединения с накладками применяют, когда сварные швы не обеспечиваютнеобходимой равнопрочности. В конструкциях, под верженных действию вибрационных и знакопеременных нагрузок, нахлесточные соединения и соединения с накладками применять не рекоменду ется (создается значительная концентрация напряжений).
Для обеспечения нормальных условий работы нахлесточных соединений размер перекрытия шва (нахлестку) принимают lп < 48 (см. рис. 5, а). Длину накладок принимают конструктивно.
Расчет сварных соединений
Расчет стыковых соединений.
Швы этих соединений работают на растяжение или сжатие в зависимости от направления действующей нагрузки (рис.11, а и б). Основным критерием работоспособности стыковых швов является их прочность. Соединение разрушается в зоне термического влияния и рассчитывается по размерам сечения детали по напряжениям, возникающим в материале детали.
Рис. 11. К расчету стыковых соединений
Проверочный расчет прочности шва на растяжение.
Условие прочности:
, (1)
где , — расчетноеи допускаемое напряжения на растяжение для шва (табл.1); F — нагрузка, действующая на шов; δ — толщина детали (толщину шва принимают равной толщине детали); lш — длина шва.
Проектировочный расчет. Целью этого расчета является определение длины шва.
Исходя из основного условия прочности (1), длину стыкового шва при действии растягивающей силы определяют по формуле
(2)
Таблица 1. Допускаемые напряжения для сварных соединений деталей из низко- и среднеуглеродистых
сталей при статической нагрузке
Сварным соединением называют неразъемное соединение деталей с помощью сварных швов. Если в заклепочном соединении соединяющим эле ментом является заклепка, то в сварных - расплавленный металл, создаю щий при остывании неразъемное соединение, то есть такое, которые не может быть разобрано без повреждения дета лей. Сварные соединения лучше других приближают составные детали к целым и позволяют изготавливать детали неограниченных размеров. Прочность сварных соединений при статических и ударных нагрузках доведена до прочности деталей из целого металла. Освоена сварка всех конструкционных сталей, включая высоколегированные, цветных сплавов и пластмасс.
Масса сварных конструкций при тех же габаритах значительно меньше клепаных (на 15%). Экономия металла достигается за счет использова ния полной площади сечения, а также возможности более рационального конструирования (например, применения стыковых соединений в тех слу чаях, когда при заклепочном соединении приходится применять накладки).
Достоинства и недостатки сварных соединений по сравнению с за клепочными (или литыми деталями).
Достоинства:
- простота конструкции сварного шва и меньшая трудоемкость в изго товлении, обусловленной сравнительной простотой технологического процесса сварки.
- значительное снижение массы конструкции при тех же габаритах. При замене заклепочных соединении сварными экономия в весе получается за счет отказа от применения различных накладок, необходимых в заклепочных соединениях, а также части веса са мих заклепок; при замене литых деталей сварными конструкциями вес их уменьшается за счет более высоких механических свойств прокатного металла.
- возможность соединения деталей любых форм;
- герметичность и плотность соединения;
- бесшумность технологического процесса сварки;
- возможность автоматизации сварочного процесса;
- сварное соединение дешевле заклепочного.
- соединение деталей может выполняться встык без накладок.
- возможность сварки толстых профилей.
Недостатки:
- возникновение остаточных напряжений в свариваемых элементах;
- коробление деталей из-за неравномерного нагрева в процессе сварки;
- зависимость качества шва от исполнителя и труд ность контроля; применение автоматической сварки устраняет этот недостаток.
- склонность к образованию трещин в местах перехо да от шва к цельному металлу вследствие термических напряже ний, возникающих при остывании. Трещины особенно опасны при динамических нагрузках (вибрационных и ударных), поэтому в таких случаях сварные швы стараются не применять, заменяя их заклепочными соединениями. Термические напряжения могут быть частично или полностью устранены термообработкой сварного соединения (низкотемпера турным отжигом). Термическая обработка исключает также последующее коробление сварных конструкций.
Область применения. В настоящее время сварные соединения поч ти полностью вытеснили заклепочные соединения. Сварка применяется для соединения элементов сосудов, испытывающих дав ление (резервуары, котлы); для изготовления турбин, до менных печей, мостов, химической аппаратуры; с помо щью сварки изготовляют станины, рамы и основания машин, корпуса редукторов, зубчатые колеса (рис.2), шкивы, звездочки, маховики, барабаны и т. д. Сварку широко применяют как способ получения заготовок деталей из проката в мелкосерийном и единичном производстве, а также в ремонтном деле.
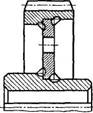
Рис. 2
Классификация и разновидности сварных соединений (швов)
Классификация.
Сварные швы классифицируют по следующим признакам:
- по назначению — прочные (обеспечивают передачу нагрузки с одно го элемента на другой); прочно-плотные (обеспечивают передачу на грузки герметичность соединения — непроницаемость для жидкостей и газов);
- по расположению сварного шва в пространстве (рис. 3) — нижнее (а); вертикальное (в), горизонтальное (б); потолочное (г). При всех прочих равных условиях нижний шов самый прочный, потолоч ный — наименее прочный (значения прочности указанных выше швов относятся как 1:0,85; 0,9:0,8).
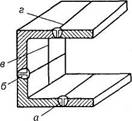
Рис. 3
По взаимному расположению свариваемых элементов различают сле дующие виды соединений
- стыковые (рис.4);
- нахлесточные, ло бовые (рис. 5, а);фланговые (рис. 5, б);
- с накладками (рис. 6);
- тав ровые (рис. 7, а, б). Свариваемые элементы располагаются во взаимно перпендикулярных плоскостях. Соединение может быть выполнено угловыми (рис.7, а) или стыковыми (рис. 7, б) швами.
- угловые (рис. 7 в, г). Применяются для изготовления тары из листовой стали, ограждений и др. Выполняются угловыми швами. Эти соединения передают малые нагрузки и поэтому не рассчитываются на прочность.

Рис.4. Стыковое соединение
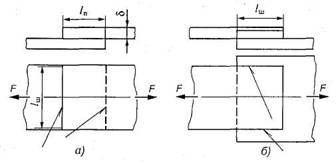
Рис. 5. Нахлесточное соединение: а — соединение лобовыми швами;
б — соединение фланговыми швами
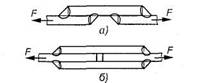
Рис. 6. Соединения с накладками
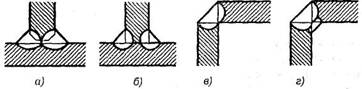
Рис. 7. Соединения тавровые и угловые
Стыковые соединения выполняют так называемыми стыковыми шва ми, а остальные — угловыми.
Конструкции стыковых швов.
Стыковые швы имеют преимущественное распространение вследствие простоты конструкции. В зависимости от толщины свариваемых деталей и обработки кромок стыковые швы делят на следующие типы:
- шов с отбортовкой кромок (рис. 8, а) — рекомендуется для тонко листовых материалов (8 < 2 мм); одна или две кромки деталей отбортовываются;
- односторонний без скоса кромок (рис. 8, б) — шов сваривается без обработки кромок листов при их толщине 8 < 8 мм;
- односторонний со скосом одной кромки (рис. 8, в) — обрабатыва ется только одна кромка деталей толщиной 8 < 12 мм;
- односторонний со скосом двух кромок (рис. 8, г) — применяется при толщине деталей 8 < 25 мм;
- двусторонний с двумя симметричными скосами одной кромки (рис. 8, д) — кромки обрабатываются у одной детали с двух сто рон, толщиной 8 до 40 мм;
- двусторонний с двумя симметричными скосами двух кромок (рис. 8, е) — толщина свариваемых деталей 8 >> 60 мм.
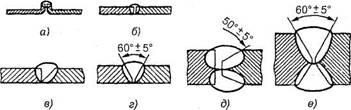
Рис. 8. Соединения стыковые:
а — с отбортовкой;
б — без скоса кромок; в, г, д, е — швы со скосом кромок
Стыковые швы, показанные на рис.9, а, называют прямыми, на рис.9, б — косыми. Косые стыковые швы применяют для увеличения рабочей длины шва.
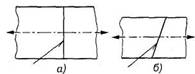
Рис.9. Стыковые швы: а — прямой; б — косой
Конструкция угловых (валиковых) швов.
Угловые швы применяют в нахлесточных соединениях, в соединениях снакладками, в тавровых и угловых соединениях. По своей прочности они уступают стыковым швам.
По профилю поперечного сечения угловые швы могут быть:
- нормальные (рис.10, а); катет шва принимается равным толщине листа (К= 5);
- вогнутые (рис.10, б) с катетом шва К= 0,85;
- выпуклые (рис.10,в);
- специальные (рис.10, г); их профиль представляет неравнобедренный прямоугольный треугольник (один из катетов K=δ).

Рис.10. Типы угловых швов: а — нормальный;
б — вогнутый; в — выпуклый; г — специальный
Вогнутые швы применяют в особо ответственных конструкциях при переменных нагрузках, так как вогнутость обеспечивает плавный переход шва в основной металл детали, благодаря чему снижается концентрация напряжений. Вогнутый шов повышает стоимость соединения, так как требует глубокого провара и последующей механической обработки для получения вогнутости, выпуклые - вызывают повышен ную концентрацию напряжений. Наиболее приемлем нормальный профиль углового шва. Специальные швы применяют при переменных нагрузках, так как значительно снижает концентрацию напряжений.
По расположению шва относительно действующей нагрузки угловые швы конструктивно разделяют на:
- лобовые, расположенные перпендикулярно к линии действия нагруз ки F (см. рис.5, а); длина лобовых швов не ограничивается;
- фланговые, расположенные параллельно линии действия нагрузки F (см. рис.5, б); максимальная длина флангового шва принимается lш = (50...60)К;
- комбинированные, состоящие из лобовых и фланговых швов.
Нахлесточные соединения и соединения с накладками сваривают уг ловыми швами.
По своей прочности нахлесточные соединения уступают стыковым. Их применяют, когда по конструктивным соображениям стыковые швы применить невозможно. Соединения с накладками применяют, когда сварные швы не обеспечиваютнеобходимой равнопрочности. В конструкциях, под верженных действию вибрационных и знакопеременных нагрузок, нахлесточные соединения и соединения с накладками применять не рекоменду ется (создается значительная концентрация напряжений).
Для обеспечения нормальных условий работы нахлесточных соединений размер перекрытия шва (нахлестку) принимают lп < 48 (см. рис. 5, а). Длину накладок принимают конструктивно.
Расчет сварных соединений
Расчет стыковых соединений.
Швы этих соединений работают на растяжение или сжатие в зависимости от направления действующей нагрузки (рис.11, а и б). Основным критерием работоспособности стыковых швов является их прочность. Соединение разрушается в зоне термического влияния и рассчитывается по размерам сечения детали по напряжениям, возникающим в материале детали.
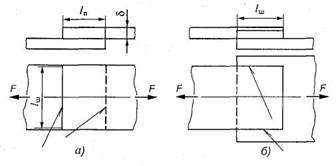
Рис. 11. К расчету стыковых соединений
Проверочный расчет прочности шва на растяжение.
Условие прочности:
, (1)
где , — расчетноеи допускаемое напряжения на растяжение для шва (табл.1); F — нагрузка, действующая на шов; δ — толщина детали (толщину шва принимают равной толщине детали); lш — длина шва.
Проектировочный расчет. Целью этого расчета является определение длины шва.
Исходя из основного условия прочности (1), длину стыкового шва при действии растягивающей силы определяют по формуле
(2)
Таблица 1. Допускаемые напряжения для сварных соединений деталей из низко- и среднеуглеродистых
сталей при статической нагрузке
Вид деформации, напряжение | Автоматическая и полуавтоматическая сварка под флюсом | Ручная дуговая электродами | |
Э50А, Э42А | Э50, Э42 | ||
Растяжение | | | 0,9[σ]р |
Сжатие | | | |
Срез | | | |